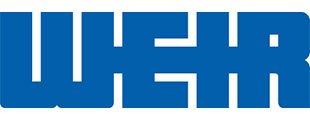
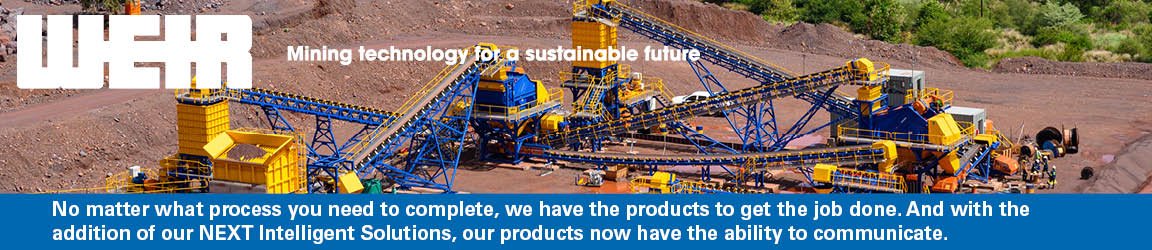
Automatic lubrication reduces labour, costs
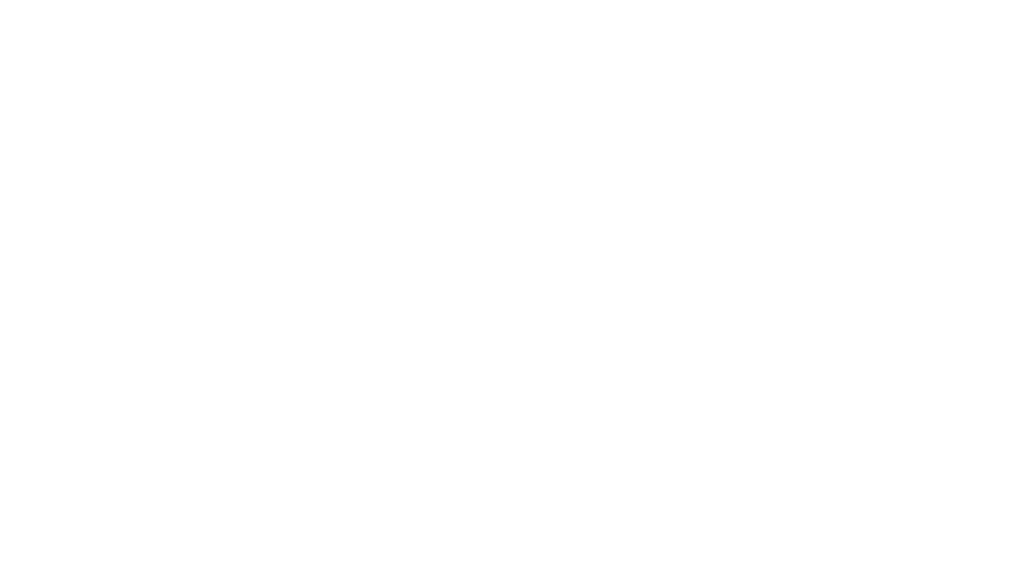
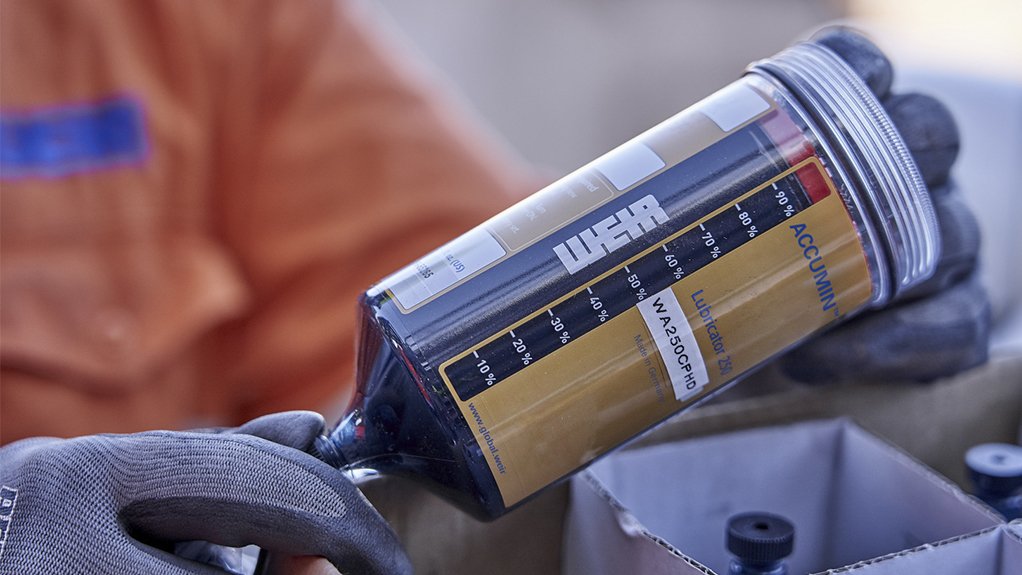
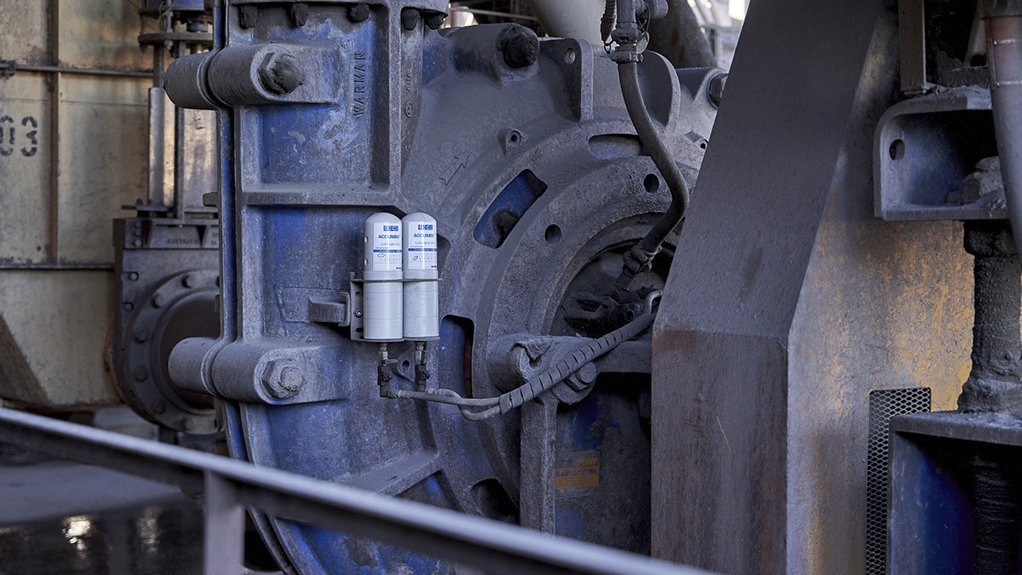
CONSISTENCY IS KEY Accumin lubricators are driven electro-mechanically, dispensing consistent dosages of lubricant regardless of ambient temperature
DOSING FROM A DISTANCE Accumin canisters can be deployed up to five metres from the lubrication point for ease of access
Since adding the Accumin range of lubrication systems to its portfolio of products and solutions in 2020, pumps original-equipment manufacturer Weir Minerals Africa says the system has generated significant value for pump installations at mine sites.
Regular maintenance of slurry pumps extends the wear life, helps avoid unplanned downtime and lowers the total ownership cost for end-users. However, in the rigorous mining environment, slurry pumps are often run to breaking point before intervention.
Weir Minerals Africa pumps product manager Marnus Koorts tells Mining Weekly that manual lubrication of bearings is labour-intensive and, consequently, exacerbates challenges inherent to pump system maintenance.
Typically, the bearings on pump systems have to be lubricated once a week, but it is debatable whether operators follow this schedule.
“Some sites have hundreds of pumps, and with every pump requiring weekly lubrication, it demands all hands on deck and, naturally, this introduces the element of human error.
“Mine sites often do not have dedicated resources for bearing maintenance and therefore assign various employees to the task. There is an inherent amount of risk to this, particularly as people tend to skip pump installations that are remotely located some distance from the main operation areas on a site,” he explains.
Koorts adds that pump systems often get under-lubricated, or over-lubricated, both of which can damage the pump in different ways.
Under-lubrication tends to cause overheating, and ultimately, pump failure, if the problem escalates undetected. This then requires operators to open the system up, repair the damage to the inside of the pump and replace the bearings, which, coupled with the downtime in production, costs the mining company much more than an effective automatic lubrication system would have.
In the case of tailings pump failures, Koorts notes that the whole processing plant needs to be stopped, which is even more costly than a system that has partly been stopped.
Over-lubrication typically occurs when employees apply a double dose of grease to avoid greasing again the next week, but while the grease enables the pump to run more efficiently, too much grease increases friction and also leads to premature failure.
Additionally, pumps must essentially work to overcome the flow resistance caused by friction, which means increased power consumption and, therefore, higher electricity costs, which already comprise a substantial portion of mines’ operational expenditure.
Koorts points out that pumps are among the largest consumers of power at a mine site and, consequently, any additional cost in this regard is unnecessary.
Therefore, Weir Minerals offers its Accumin range of lubricators as a solution. They can be retrofitted to pump systems already on site or come fitted with new Warman slurry pumps.
“Accumin is an automatic lubrication system that protects the pump more effectively, owing to consistent greasing according to the pump’s requirements, compared with manual greasing that mostly happens at varying levels. It is also less labour intensive,” Koorts highlights.
With its Accumin lubrication system, Weir Minerals offers three sizes and two drive configurations, facilitating varying volumes of lubricant, catering for all pumps ranges in its portfolio or that a site may require.
Accumin lubricators can also be used on conveyors, fans, electric motors, filter belts, vacuum pumps, mechanical seals and gearbox seals.
The operator can configure the system to dispense grease on a continuous basis, using either an analogue or digital setting, depending on the model of lubricant system. Koorts says that most mines normally need two different sizes of Accumin lubrication systems.
The cannisters are changed every three to four months, depending on usage, which is a “clean and simple process”. Weir Minerals offers its Accumin cannisters with a range of mineral based and synthetic grease or a lubricant specified by a customer.
As an added feature, some of the Accumin lubrication systems are equipped with a gauge that measures the contents of the cannister and will start flashing when it nears empty. This enhances the ease of maintenance and overall cost-effectiveness.
Koorts concludes that Weir Minerals Africa’s strong stockholding ensures its Accumin lubrication system availability across the country and in Africa, as well as throughout varying levels of Covid-19-linked lockdown, while its extensive branch network is accessible for customers requiring cannister exchanges or on-site assistance.