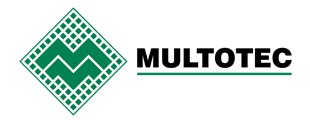
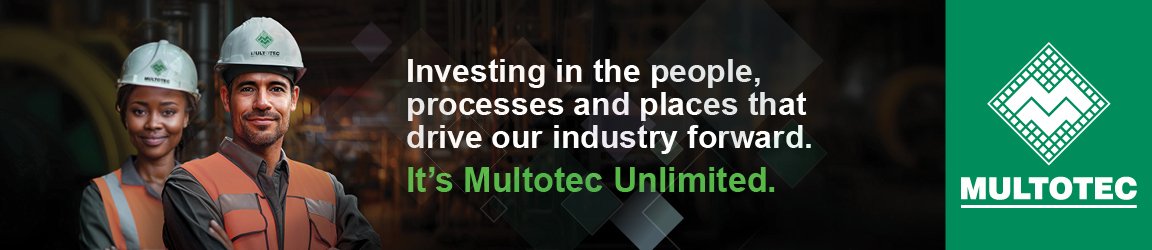
Company Announcement: Multotec Appoints Dedicated Sampling Specialist
Multotec has appointed sampling specialist, Rolf Steinhaus, to offer a dedicated sampling consulting service to mining and engineering companies. “There has been a definite gap in the marketplace for a sampling advisory service capable of providing application-specific advice in terms of specifying “correct” sampling equipment designs and assisting in the provision of a fit-for-purpose custom engineered system that will meet the sampling requirement on each individual process plant,” says Steinhaus, who has been with Multotec for more than 18 years in the sampling sphere and has extensive experience in sampling equipment across a broad range of minerals sectors, both locally and internationally.
Multotec originally entered the sampling equipment arena in 1987, when it signed the first licencing agreement with Siebtechnik GmbH of Germany. Today, all sampling solutions are provided through this South African-based company, with manufacturing through its ISO 9001:2000 TUV certified accredited facilities in Johannesburg.
“When a company decides to build a new processing plant, it’s essential for a sampling specialist to be involved from the earliest design stages to ensure that appropriate attention is given to the sampling requirements of the various process streams,” he says. “In the case of Multotec, companies are dealing with an OEM able to advise on a sampling solution that will achieve what is expected in each unique application and hopefully accommodate plant layouts and project budgets.
“Retrofitting of samplers is high risk, as often, no provisions are made for headroom, resulting in compromises in equipment design. This not only impacts on mechanical equipment reliability, but also calls into question the sampling integrity of the final results.”
Steinhaus recommends that even before design work commences on plant layouts, a sampling specialist should be on board to advise on the necessary sampling protocols, including what material has to be sampled, where it should be sampled and the sampling frequency as well as the equipment selection and design relevant to a particular application.
“Sampling largely involves a custom design solution that takes into account a client’s process parameters,” he continues. “Often it is these parameters that can vary significantly from one application to the next and from one plant to another in terms of material densities, particle size distribution and pulp viscosities. All these factors, amongst others, impact on the materials handling outcome.
“Sample taking and collection with associated trickle feeds of small quantities of material requires a very different approach to bulk material flows. Additionally headroom is invariably a critical requirement, as it impacts on the cost of a plant, (with a now possibly taller building) and limits the number of options to prevent small quantities of the sampled material remaining behind within the sampling system. This is particularly the case with sampled material with associated moisture content.
“On the dry sampling side, there are techniques that can assist in keeping headroom down to a minimum, for example, the use of horizontal or inclined mini feeder conveyors. However, these techniques call for a larger overall sampling plant footprint.” Steinhaus believes samplers are not always regarded as critical to the process by certain plant operators, as they are not a production unit. For this reason, budget is often insufficient or not even allocated for this equipment in capital projects. If budget is allocated and there are project cost overruns, the samplers are frequently the first items to be discarded to save costs.
“When samplers are not seen as a critical component of a process plant, they also tend to be ordered as one of the last items as they are not always given the needed focus,” he continues. “This puts the sampling equipment suppliers under pressure to deliver and, when it is one of the last items ordered, plant layout designs are already far advanced when the equipment is procured, without due attention given to the space requirements and certified equipment interface needs. Samplers need to be seen as having more than nuisance value.”
“Optimum sampling solutions are obviously in the best interest of the customer and the ability to maximise product yields or recoveries via process control, so there is a real need to bring this message across to the industry. I find myself constantly engaging with the engineering companies that we partner with on these issues to ensure there is a better understanding of the requirements for sampling and better appreciate the need for correct sampling practice and protocols.
“Mining houses derive huge benefit when they have appointed in-house champions responsible for product quality and metallurgical accounting, particularly with regard to and emphasis on sampling equipment selection and performance, because these personnel have the opportunity to make a critical input into projects before suppliers are even approached. This is an advantage because the customer can ensure that standards are consistently implemented and maintained, even on new ventures within their organisations. “When there are clearly defined requirements based on sound internationally accepted sampling standards and designs, which are understood by all concerned, it also helps the supplier to recommend the most suitable technology,” Steinhaus concludes.