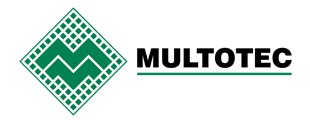
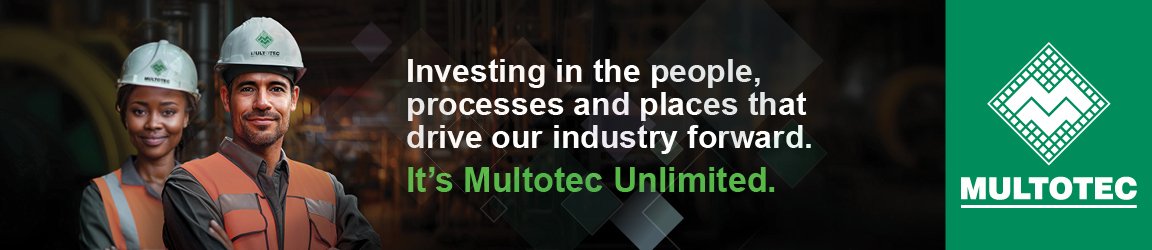
Degritting spiral reduces carbon costs for gold miners
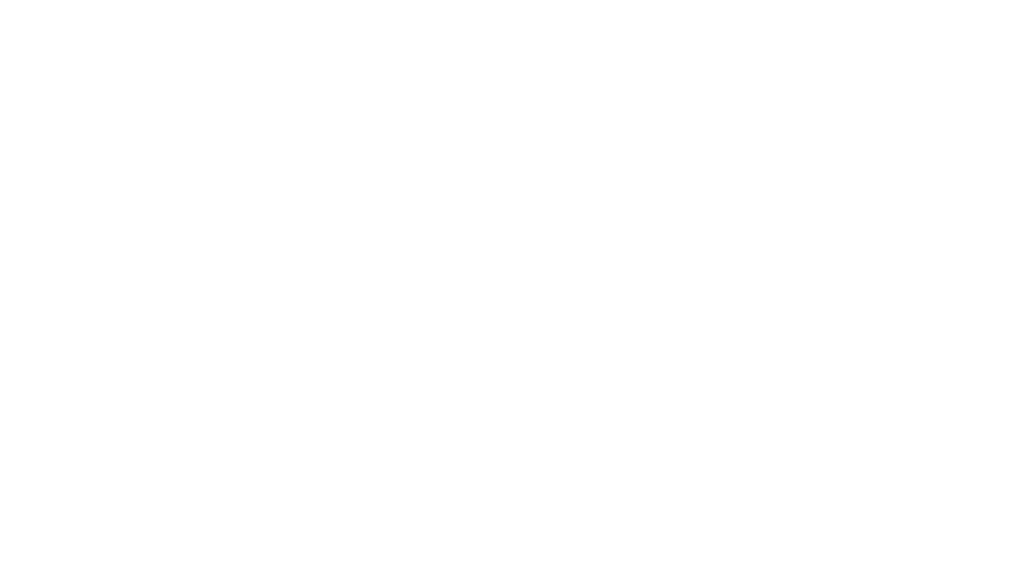
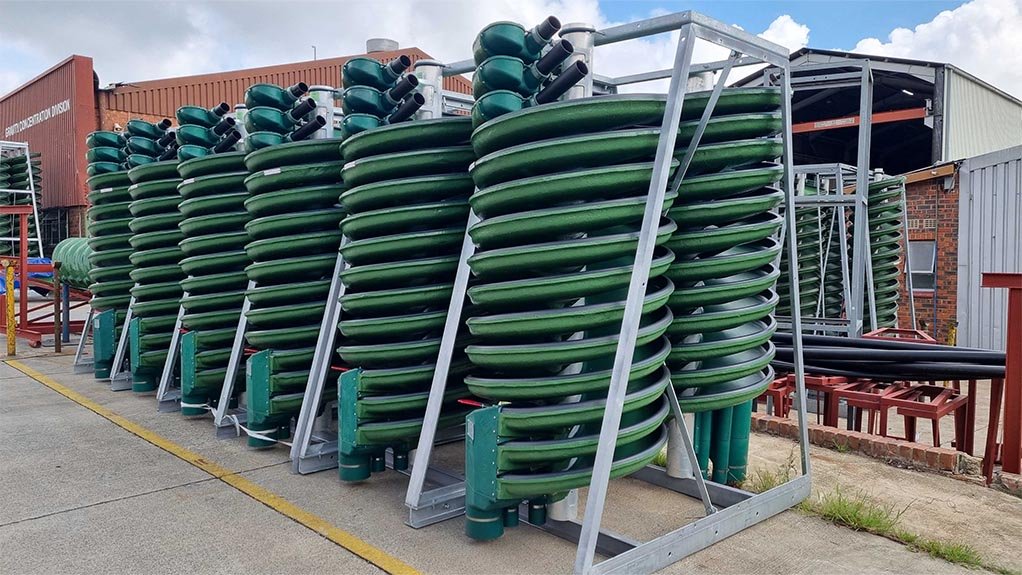
PRODUCT ADAPTATION To help reduce gold processing costs, Multotec adapted its SX4 spiral separator, which is commonly used in coal processing, and developed it to be used for the processing of gold ores
Amid tough economic conditions, metallurgy and process engineering solutions developer Multotec has responded to the challenge of the high costs associated with using activated carbon in gold processing faced by gold operations in West Africa.
To help reduce gold processing costs, Multotec adapted its SX4 spiral separator, which is commonly used in coal processing, and developed it to be used for the processing of gold ores.
The use of the SX4 spiral achieved up to 95% removal of contaminants from carbon and proved to be an efficient and cost-effective solution, according to Multotec.
Several mining operations in West Africa exploit low-grade gold reserves and thus push more volumes of mined ore through their mill circuits to increase their yield, explains Multotec West Africa GM Godwin Dzwairo. He notes that this compromises milling efficiency as a result.
“This means that they run up costs in terms of activated carbon usage during the carbon-in-leach process, which is an integral part of gold extraction. The carbon subsequently becomes contaminated with non-gold-bearing material such as silica, sand and woodchips, and these need to be removed,” says Dzwairo.
He explains that Multotec’s SX4 can remove between 85% and 95% of waste material from the carbon, which also improves the efficiency of downstream processes and reduces the amount of reagents needed during the final elution and gold recovery process, thus saving further costs.
Multotec Group process engineer Refentse Molehe says the SX4 spiral is a cost-effective solution because it relies solely on water and gravity for the separation process and does not require any energy source or chemicals.
“This isn’t a new technology, as it has previously been used in coal mining, but we saw an opportunity and adapted it for a new purpose,” she says.
Molehe adds that while the high cost of carbon is not a new problem facing the gold mining sector, it has, in recent times, been exacerbated by the increased economic pressures on gold production.
Accounting Requirements
Dzwairo says metallurgical accounting requirements are becoming increasingly stringent, meaning that gold extracted from ore must be accurately accounted for using analysis of the rock, slurry, carbon and final product.
“When the carbon is associated with material that is not gold bearing, this material can be carried over to the elution processing phase and the weight can distort gold accounting,” he says.
Therefore, by taking the waste material out of the carbon before the next step in the processing process, Dzwairo says gold miners can account more accurately for gold, leading to downstream processes being more efficient as a result of the contaminants having already been removed.
“Typically, waste material makes up about 10% to 20% of the product weight, so removing it allows you to better estimate the weight of the gold yield,” he says.
The SX4 spiral is constructed with materials that ensure a high-quality product with a longer life that has a low maintenance requirement and low investment cost.
Implementation of the SX4 spirals in gold operations is done with ease through the option of retrofitting the spiral into existing operations; alternatively, there is flexibility to use a compact modular design.
To date, Multotec has completed SX4 degritting spiral installations at three gold mining operations in Ghana, and at a gold mine in Guinea, and has also engaged with a potential customer in Burkina Faso that is seeking to improve efficiencies.
Multotec’s spirals development team completed the design drawings for the SX4, whereafter the company’s field service team and contractors managed and assisted with the installations at the customers’ plants in West Africa.