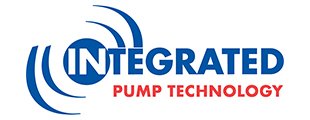
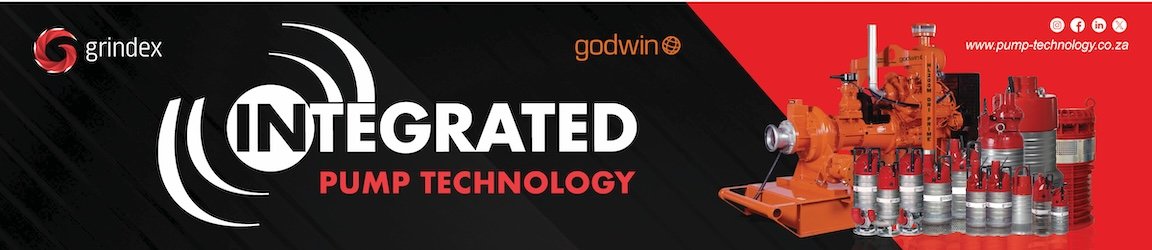
Integrated Pump Technology delivers Godwin HL150 to Senegal mine for open pit dewatering
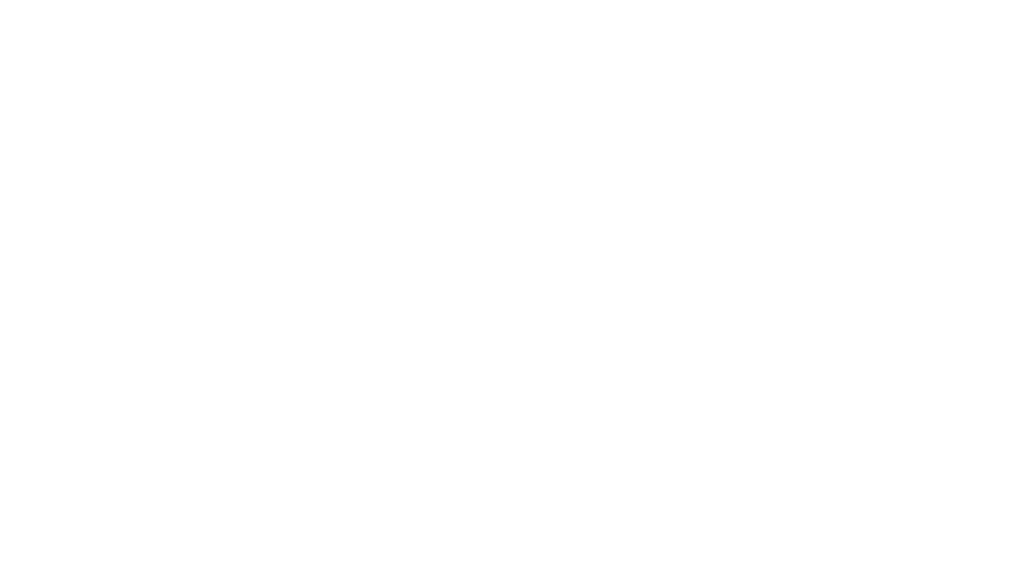
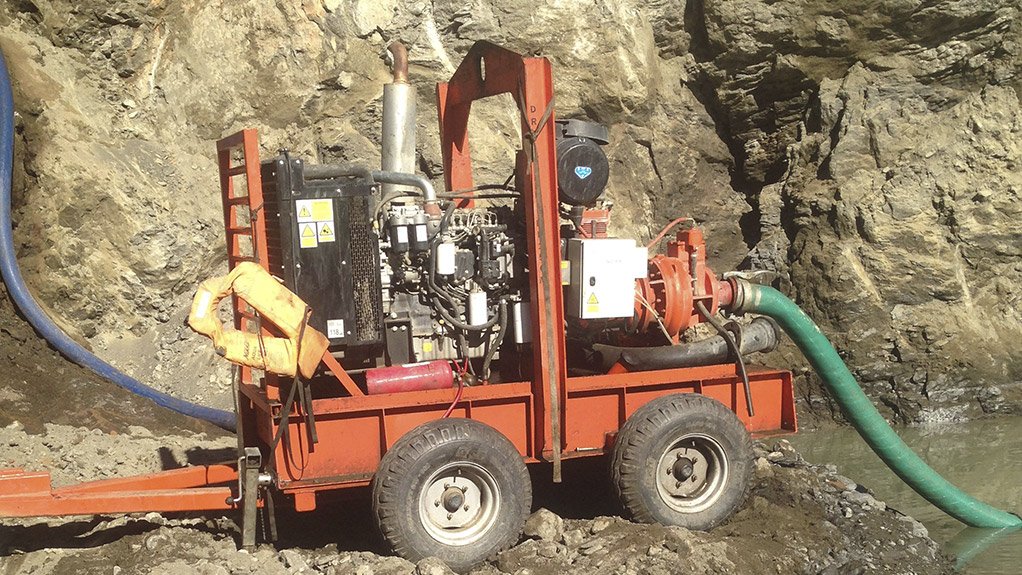
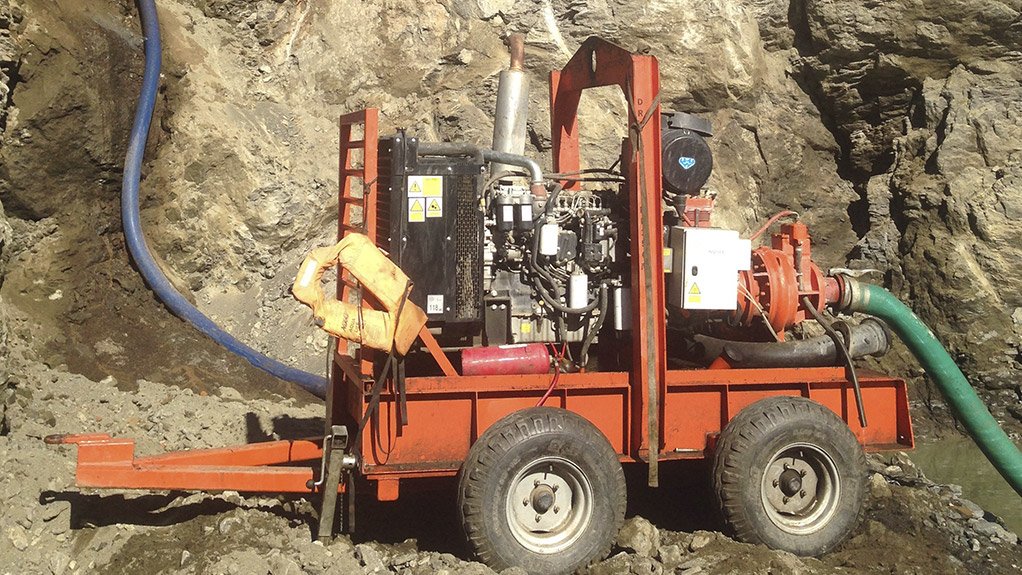
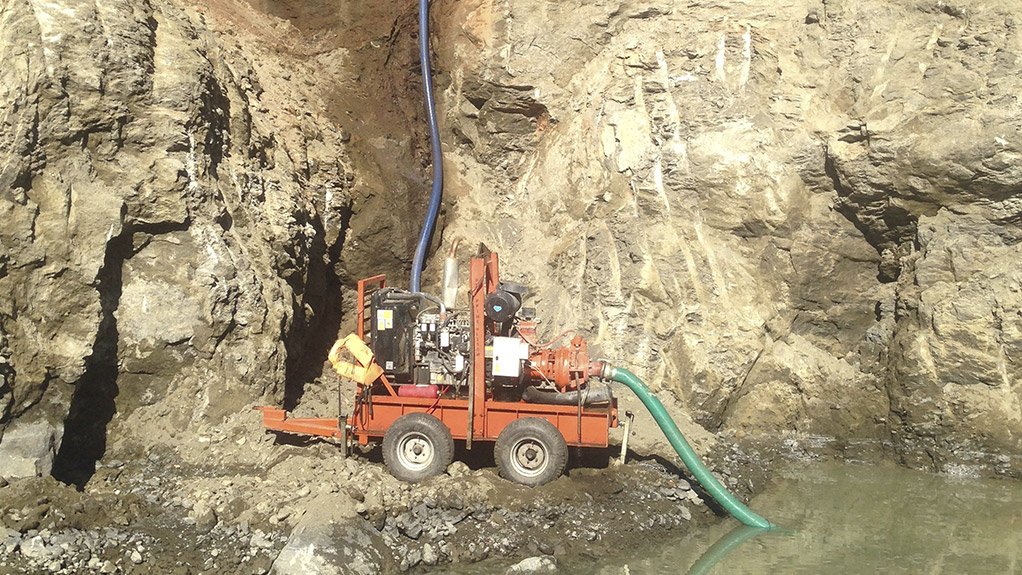
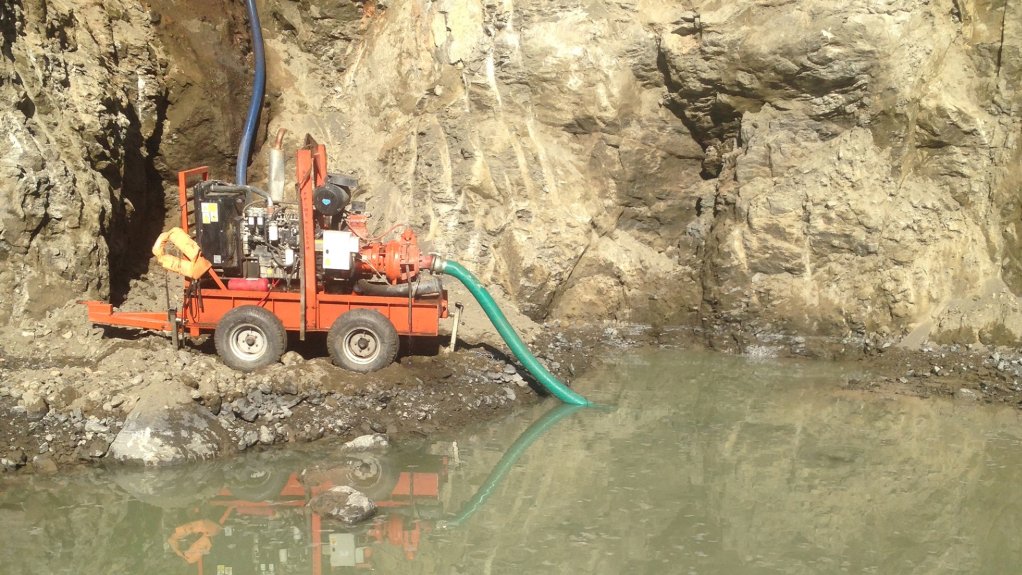
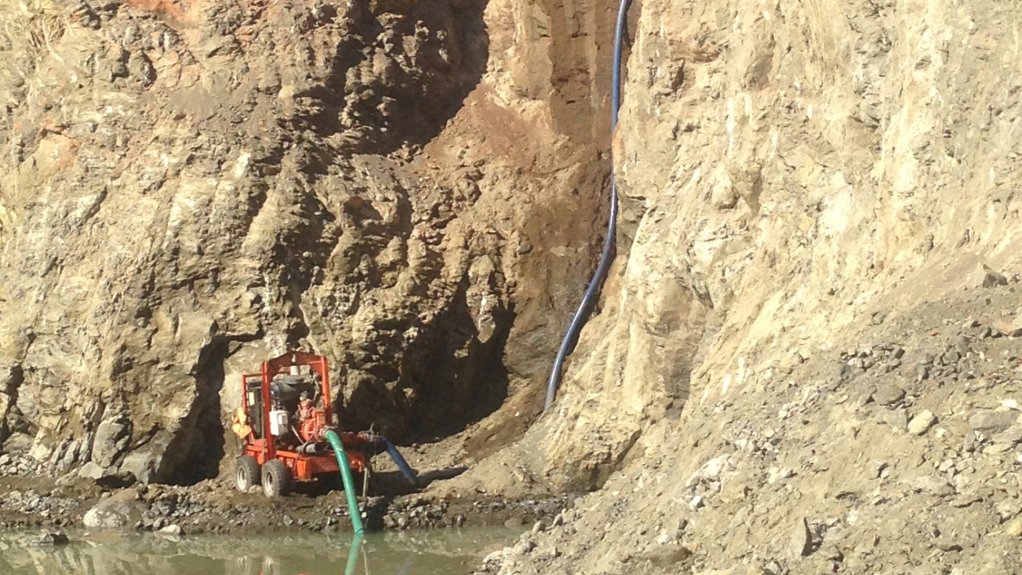
Integrated Pump Technology has secured an order for its first Godwin HL150 pump to a mining operation in Senegal, marking a significant step in the company's ongoing support for mining operations across West Africa
Dewatering applications in open pit operations call for a robust pump and the Godwin HL150M can handle solids up to 35 mm in diameter
Combined with its fully automatic priming system, the Godwin HL150M offers reliable performance, making it a valuable asset for mining operations in challenging environments
One of the key features of the Godwin HL150M is its ability to run dry for extended periods thanks to its high pressure oil bath mechanical seal
For the Senegalese mine, the Godwin HL150M pump will provide a robust solution that can be quickly mobilised to where it's needed most
Integrated Pump Technology has secured an order for its first Godwin HL150 pump to a mining operation in Senegal, marking a significant step in the company's ongoing support for mining operations across West Africa. The trailer-mounted diesel-driven self-priming pump has been selected to provide vital dewatering services for an open pit mine, where fluctuating groundwater levels, particularly during the rainy season, pose a challenge to efficient operations.
Mining operations, especially open pit mines, are often situated in remote areas where power availability is limited. This makes diesel-driven pumps the preferred option, offering the flexibility to be deployed without reliance on external power sources. For the Senegalese mine, the Godwin HL150M pump will provide a robust solution that can be quickly mobilised to where it's needed most, keeping operations running smoothly even during periods of intense rainfall when groundwater levels rise rapidly.
JD Nel, Godwin Product Manager at Integrated Pump Technology, says the Godwin HL150M Pump was considered the ideal choice due to its exceptional capabilities. “Compact yet powerful, this pump is capable of delivering flow rates of up to 374 m³/h and can discharge water at heights of up to 148 metres. This level of performance makes it perfectly suited for high-demand dewatering applications like those found at this open pit mine,” he explains.
One of the key features of the Godwin HL150M is its ability to run dry for extended periods thanks to its high pressure oil bath mechanical seal. Nel says that this innovative design ensures continuous operation in tough conditions such as those found in the Africa mining regions and it allows the pump to automatically prime and reprime as needed, without manual intervention.
“Dewatering applications in open pit operations call for a robust pump and this model can handle solids up to 35 mm in diameter, allowing it to deal with both slurry and clean water, adding versatility to its application,” he says.
Another critical benefit is the pump's ability to achieve a suction lift of up to 8.5 metres. Combined with its fully automatic priming system, the Godwin HL150M offers reliable performance, making it a valuable asset for mining operations in challenging environments.
“This recent delivery to Senegal underscores Integrated Pump Technology’s growing presence and support for mining projects across Africa. We have built a strong reputation for supplying high quality dewatering solutions tailored to the needs of the mining sector in Africa, where the ability to maintain uninterrupted operations during the rainy season is crucial,” Nel says.
Alongside its range of Godwin diesel driven pumps and Grindex electric submersible pumps, Integrated Pump Technology offers end-users in the region not only reliable equipment but also comprehensive support. This includes expert consultation to ensure the correct specification for each dewatering challenge, as well as maintenance and service options to keep the pumps operating at peak efficiency throughout their lifespan.
“With advanced solutions like the Godwin HL150M pump, Integrated Pump Technology enables African mining operations to tackle environmental challenges head-on, enhancing operational efficiency and reducing downtime to ensure optimal productivity,” Nel concludes.