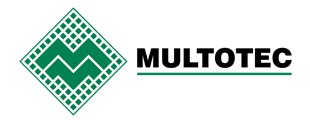
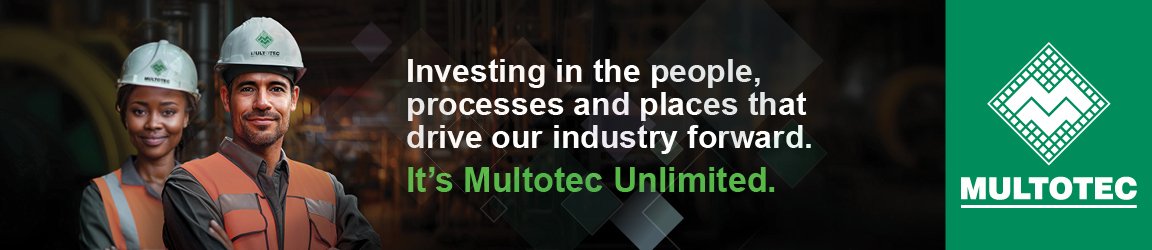
Mining-focused manufacturers see innovation as key to survival and future growth
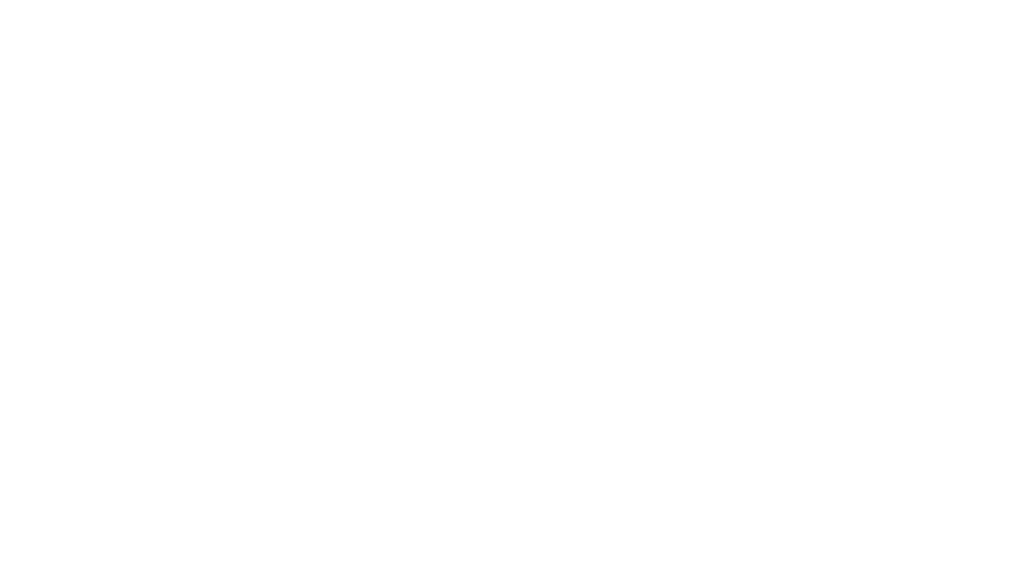
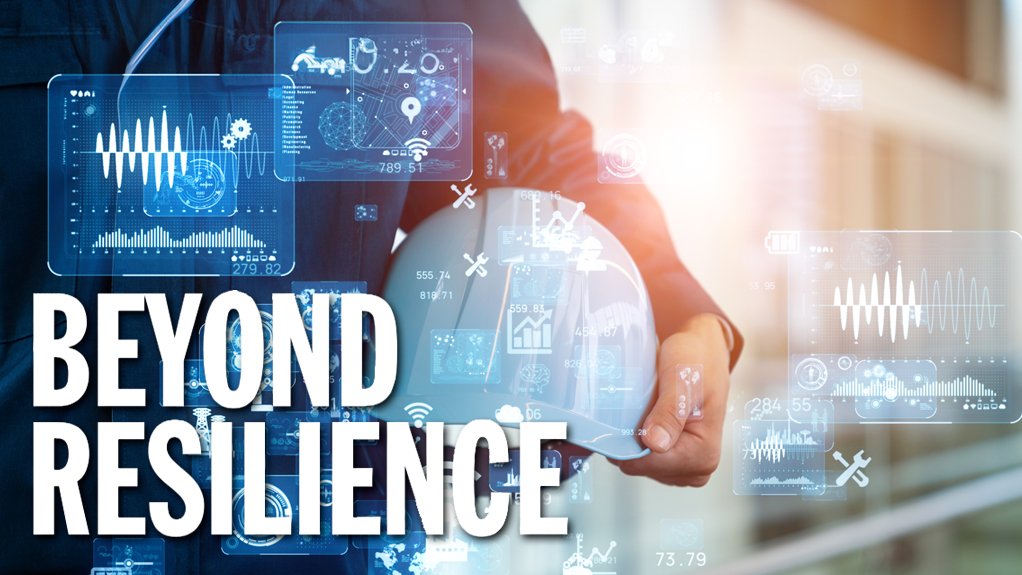
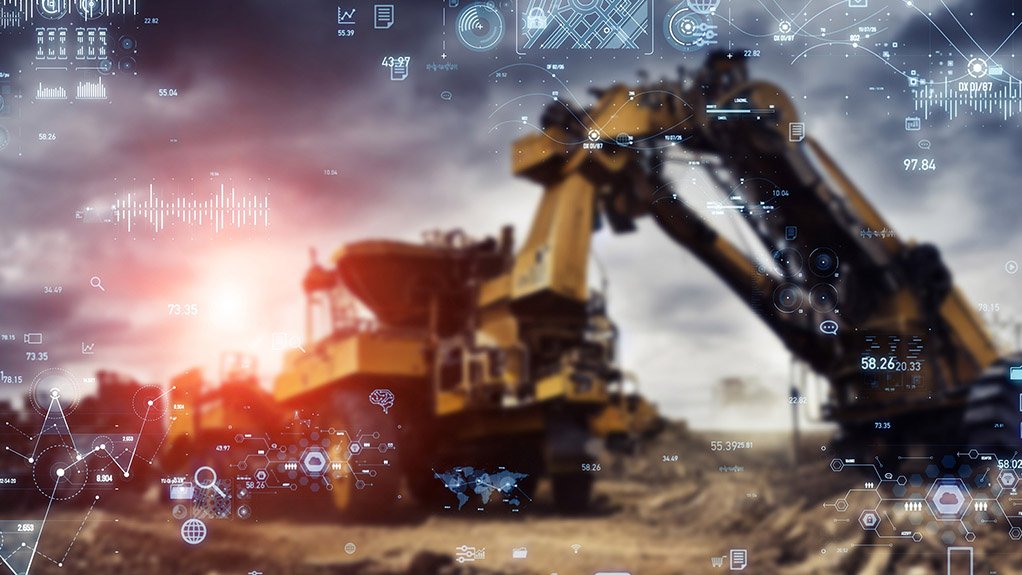
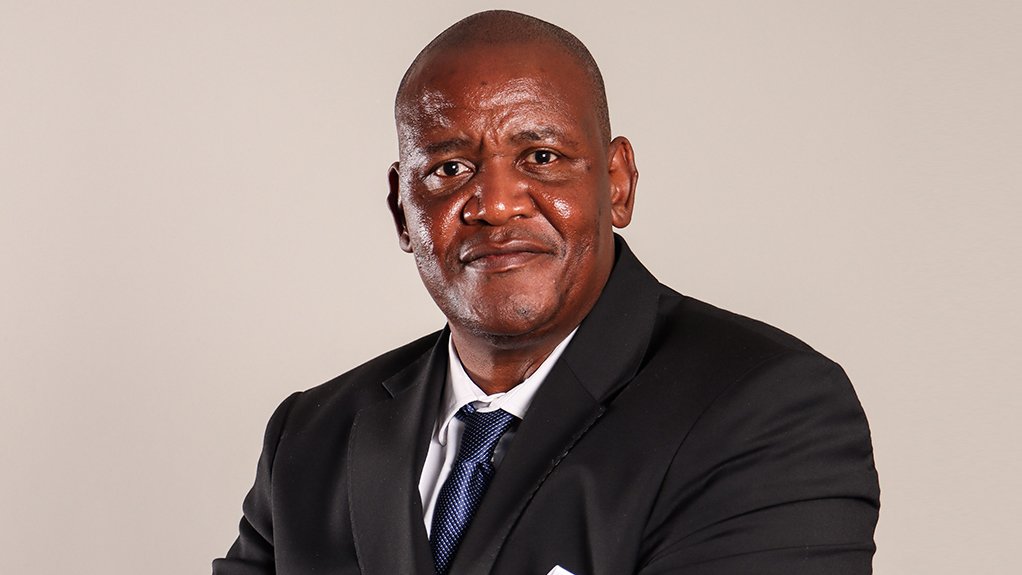
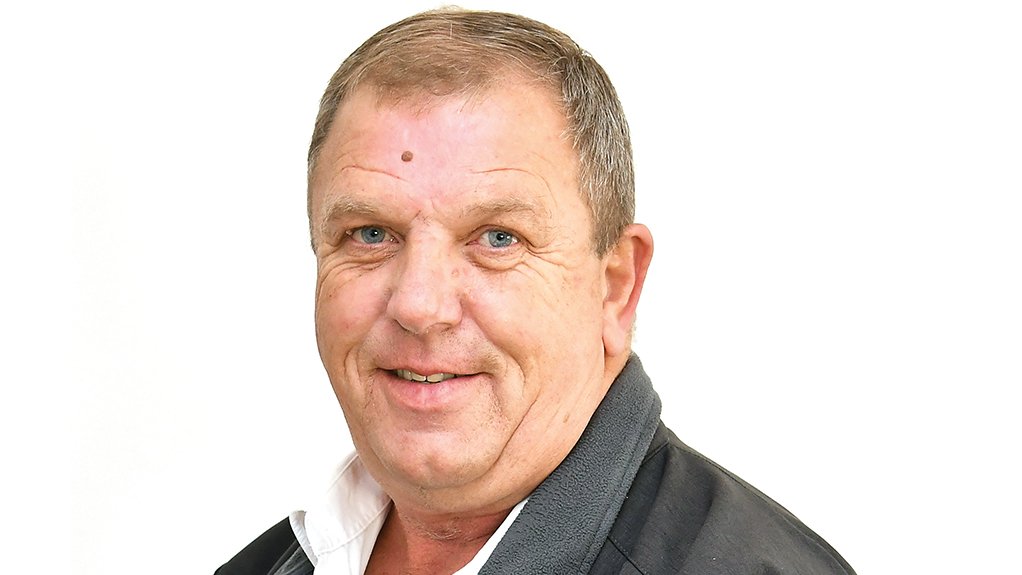
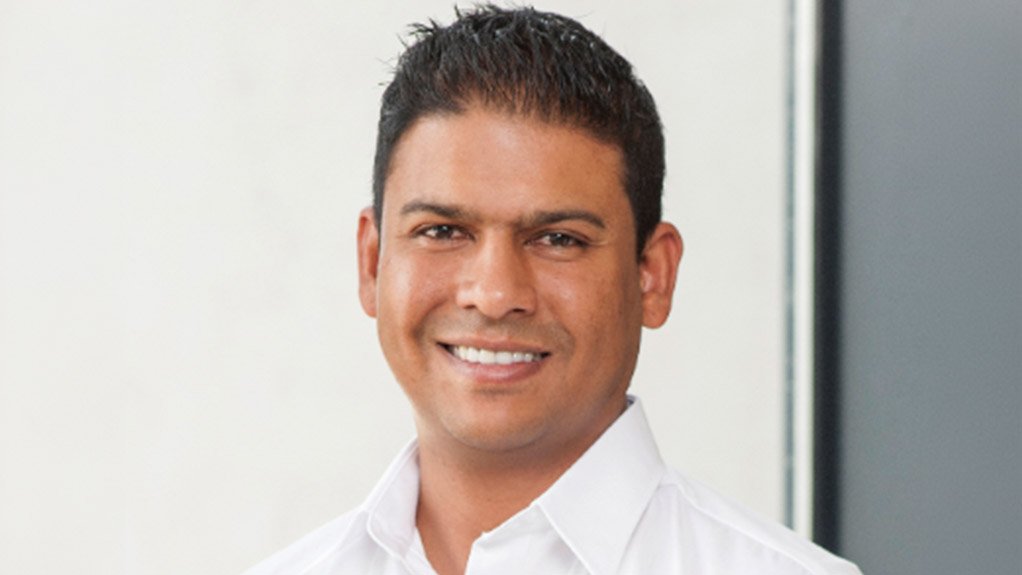
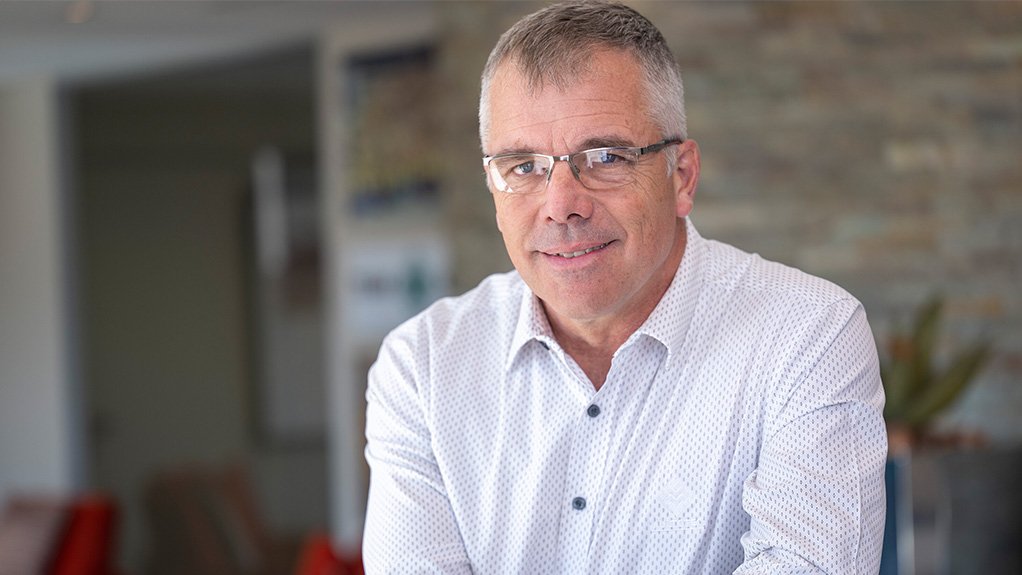
AGAINST THE ODDS While the local mining sector continues to face challenges, such as loadshedding, industry players remain resilient
Memsa CEO Lehlohonolo Molloyi
Saceec CEO Eric Bruggeman
Epiroc business line manager for digital solutions Vikesh Chiba
Multotec Group CEO Thomas Holtz
Amid the challenges of loadshedding, logistical constraints and volatile commodity prices, South Africa’s mining-focused manufacturers and equipment suppliers view ongoing innovation, including embracing digitalisation and artificial intelligence (AI), as increasingly central to their survival and future growth.
Mining Equipment Manufacturers of South Africa (Memsa) CEO Lehlohonolo Molloyi describes local manufacturers in the sector as “resilient” and responsive to the needs of the sector, highlighting in particular how innovation has played a central role in improving the domestic mining sector’s once-dismal safety record.
“The stats speak for themselves, if one looks at how the numbers have declined in terms of fatalities in the mining industry,” Molloyi said during a recent Creamer Media webinar hosted to showcase innovation in mining and mining services. He was referring to the significant improvement in mine safety over the past number of years.
Despite a regression in the number of mining-related fatalities in 2023, Minerals Council South Africa noted in a media statement released in February that the industry – led by the Minerals Council, and in collaboration with the Department of Mineral Resources and Energy (DMRE) and organised labour, and through company- specific programmes to directly engage employees – has made significant progress on the journey towards zero harm in the past decade, with a 42% decline to a record low of 49 fatalities in 2022 from 84 in 2014.
Collaboration among all key stakeholders – including the Mine Health and Safety Council, the DMRE, the Minerals Council, and manufacturers in the mining sector – has played an important role in supporting these positive trends, including through the introduction of technologies and innovations.
Through concerted initiatives, the Minerals Council reported that fatalities arising from falls-of-ground and transportation-and- mining, the two historically leading causes of deaths and injuries, fell by 83% and 43% respectively between 2014 and 2022. Injuries declined by 19%.
The trajectory for both innovation and mine-focused manufacturing has not been a smooth one, however.
Nevertheless, the sector has proved resilient, despite some difficult periods when commodity prices and investment have been unsupportive. To illustrate this, Molloyi pointed to the fact that Memsa’s membership has increased over the years, as has the sector’s exports.
He noted that the Africa Continental Free Trade Area has also opened up opportunities across Africa for local manufacturers, where collaboration is proving important to both business sustainability and growth.
South African Capital Equipment Export Council (Saceec) CEO Eric Bruggeman agreed that collaboration is necessary to tackle challenges, adding that showcasing local initiatives is important.
“That is quite a task and I believe that we, in South Africa, are very successful at this,” he said.
While Multotec Group CEO Thomas Holtz concurred with both Molloyi and Bruggeman, he argued that the local manufacturing sector is still struggling to reach its full potential domestically and abroad.
“South Africans are getting a bit tired of being resilient.
“It’s a challenge, because deindustrialisation is a factor . . . [and] you have to have a mindset of taking on the challenges: putting in the power required and being capable of dealing with the loadshedding, or load curtailment, and many other hurdles,” said Holtz.
“At Multotec, we’ve taken the bull by the horns . . . I think we’ve taken on the challenge,” he added, pointing to a number of the company’s innovations in the mining sector.
These include the company’s UX7 spiral, which focuses on recovering material with a particle size of 75 microns or smaller, in addition to it also having developed a composite rubber steel integrated liner that has partly replaced the steel liners used in mill mining applications.
Enter Artificial Intelligence
Digitalisation and AI have also started to impact on the local mining industry, with original-equipment manufacturer Epiroc business line manager for digital solutions Vikesh Chiba arguing that, by failing to embrace digitalisation, mines put themselves at a disadvantage.
While traditional paper-based methods are prone to human error, loss of information and slow processes in consolidating data, Chiba argued that digitalisation allows for faster, more accurate data collection.
Epiroc, which offers a broad range of autonomous solutions for drilling, loading and haulage in underground and surface mining operations, says such solutions enable machines to be operated and controlled through complex AI algorithms. This also enables the machines to communicate and coordinate with each other in an orchestrated way to get the maximum possible usage from the machines.
“From an AI perspective, I feel we are really only scratching the surface of what is possible in South Africa, and there’s this huge opportunity for us to leverage AI to have a greater impact.”
While there are sites in South Africa already running autonomous surface drills, Chiba noted that there are limited applications in the surface haulage space and the underground mining space.
“I think that is because there’s still some work to do in terms of the operational maturity that’s required before we can take that next step to fully autonomous systems.”
However, there are areas where AI is being used quite routinely in the industry, such as in design planning and scheduling platforms, which employ algorithms to simulate mining operations and predict outcomes based on different scenarios and operational constraints.
“So, there’s a lot happening in the software space, but if I think about what’s happening in terms of AI-related hardware, such as AI cameras, for example, there is still scope for such systems to increase significantly in mining,” said Chiba.
New Applications
Epiroc has made several strategic acquisitions in the mining technology space in the past few years, thereby bolstering its technology capabilities and broadening its digital and automation portfolio with products such as autonomous controlled machines and real-time situational awareness tools.
Some of the company’s latest developments include a real-time location tracking system for surface mining applications, called Blast Support, which allows for a three-dimensional visualisation of people’s location at the mine site to ensure that no one is in the danger zone during blasting.
The system can also track fixed or moving assets. This surface platform has been built on a real-time location system, which has been used in underground applications in South Africa.
In the collision prevention systems (CPS) or collision avoidance systems (CAS) space, Chiba also mentioned that Epiroc has launched its Titan CxD system.
While CPS and CAS are not new concepts in South Africa, Chiba described this product as “quite exciting”, as it combines various sensor technologies, such as global positioning systems, low frequency, radio frequency, time of flight and AI cameras – depending on the specific underground or surface operating conditions.
“That combination significantly increases the likelihood of the CPS system detecting a person or vehicle. We [are] also working closely with the University of Pretoria around that, so there’s a lot happening in the space, and I think that the developments will continue,” said Chiba.
“With the technology we have . . . these sorts of information, if you think about planning and scheduling, can be sent to machines and operators in near real time. So, digitisation has become very streamlined, and it’s something that . . . we even use . . . within Epiroc, quite effectively,” he added.
There is also a focus on integrating various platforms, whereby a single solution could be offered with different technology plug-ins, depending on what customers need in terms of productivity efficiency, or safety improvements.
Solutions are also emerging that ensure there is visibility across various silos, with engineering simulation and data management systems company Simera Trace technical director Kevin O’Neill noting that the company is offering ore tracing software that can integrate throughout different mining phases.
“We had to develop a software platform that could integrate to each one of these and make it our own real-time platform so that you can track it right through . . . without having to go to each silo and get the information.
“So, we have the digital non-erasable ID on the ore tracer that travels with the orebody the whole time. We’re totally in control of it,” he said.
There was also general consensus across webinar participants that, for the mining industry in South Africa to advance, there is a need for greater collaboration, through which creative solutions can be developed to improve safety and sustainability.