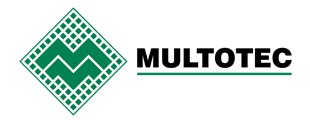
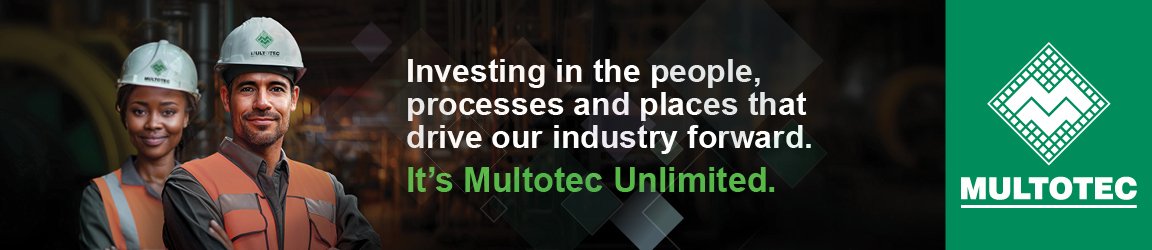
Multotec drives process efficiency, solutions with in-house test work
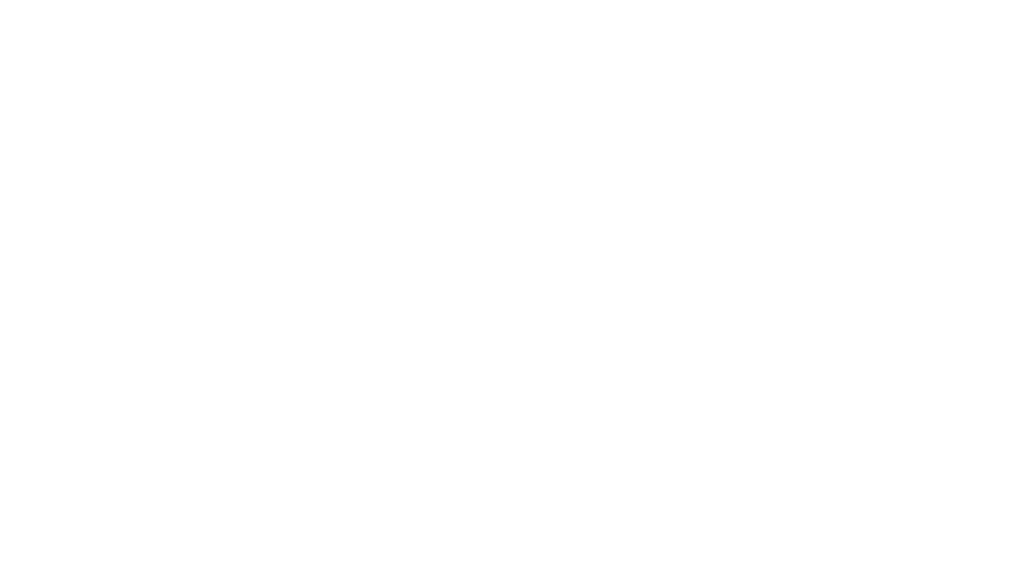
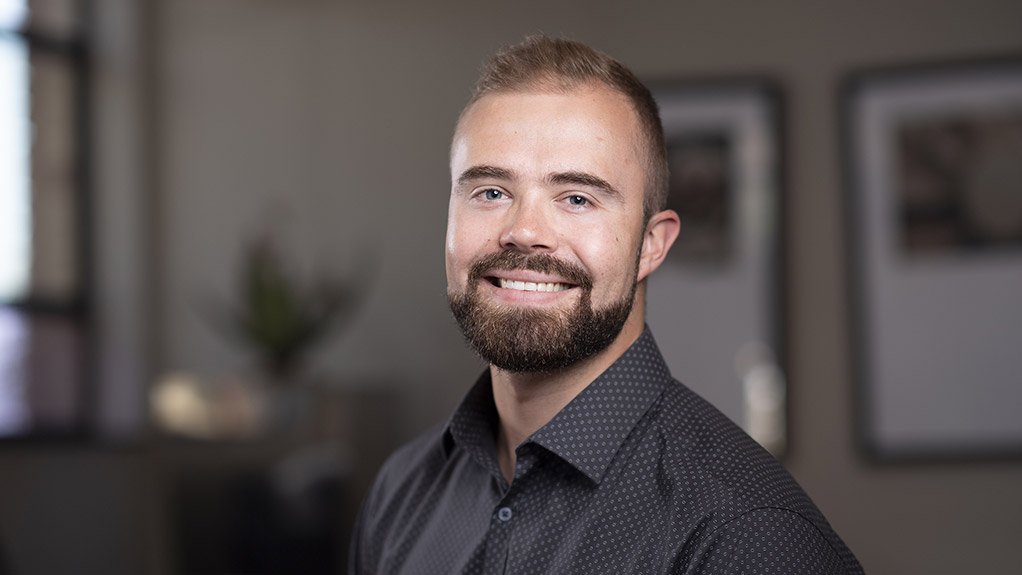
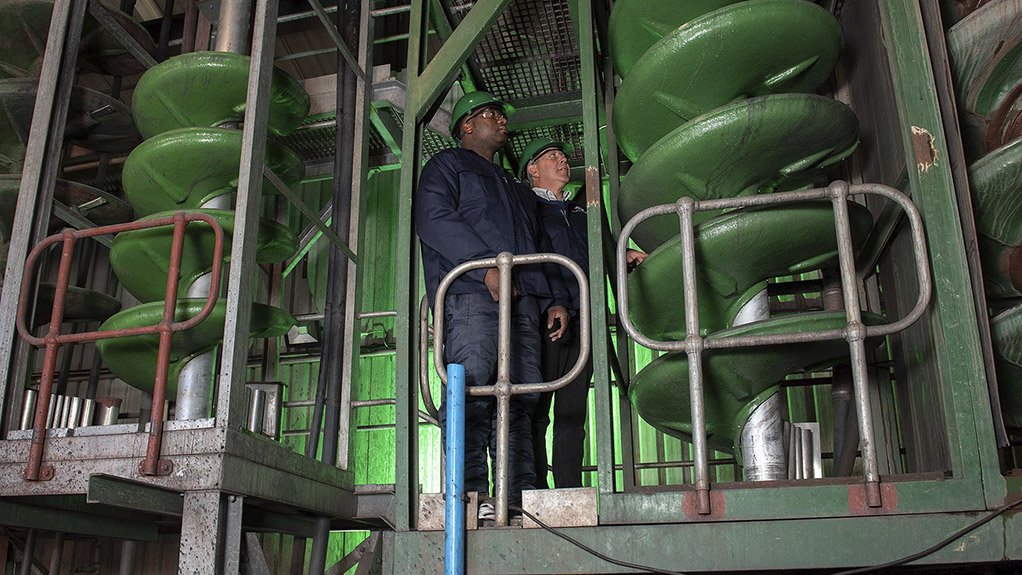
PJ Pieters, Process Engineer at Multotec
Multotec’s test work capabilities include gravity concentration using spirals as well as cyclones, magnetic separation, solid-liquid separation and water treatment related to metals recovery
New mines or expansions rely on accurate test work to know how best to recover the minerals in an ore body; mineral processing specialist Multotec not only provides the processing solutions, but can also test material to inform clients’ financial and operational planning.
In a recent presentation to the South African Institute of Mining and Metallurgy (SAIMM), Multotec process engineer PJ Pieters and R&D engineer Jeantelle Rust outlined how the company’s extensive test work capability was put to use by industry.
“The process starts with accurate sampling – a field in which Multotec has developed a depth of expertise and a dedicated product range,” says Rust. “We prepare samples from clients with techniques such as filtration, drying, particle size distribution analysis and laboratory-scale float and sink analysis. We can also conduct sample splitting and packaging before the analysis takes place.”
Serving an international client base, Multotec has done test work on minerals including but not limited to gold, coal, lithium, mineral sands, copper, iron ore and tin. The work is carried out and supported by experienced metallurgists and product specialists.
“Our expertise in physical separation allows us to test the samples using selected products from our portfolio, and ensures that the client gets the most effective solution,” she says.
Test capabilities include gravity concentration using spirals as well as cyclones, magnetic separation, solid-liquid separation and water treatment related to metals recovery.
“Accurate screening is also important, so our test facilities include Vibramech and LuCoTec vibrating screens to identify the best solutions to increase plant capacity, reduce wear and energy consumption, and optimise reagents,” says Pieters.
There is also a trommel screen testing facility to provide insight into sizing or the removal of oversize material. Screening deck optimisation using deck maps helps clients find the best combination of open area and durability. The breadth of capability has led to many interesting tests being run, he says.
While most test work is conducted at Multotec’s dedicated research and testing facilities, the company is also able to take certain equipment to a client’s operation for on-site testing to be done.
“This is a convenient way to conduct testing under normal plant operating conditions,” he says. “This kind of test work adds confidence to the client’s decision to invest in a specific solution.”
“These tests range from liners for bauxite and magnetic separation for wollastonite, to using cyclones to separate cow manure from grass and grit for use as a biofuel,” Rust says. “Testing with spirals has also helped clients find the best separation methods for material as varied as tantalite, wolframite and crushed computer components.”
Multotec’s test work feeds valuably into product development, continuously and cost effectively improving the company’s offerings based on its own R&D combined with client requests. The solutions can often be turned around much quicker than expected, using rapid prototyping with 3D printing and CNC machining powered by specialised modern software.
“Our test work has allowed us to modify cyclones, for instance, for innovative applications like removing plastic from sand or to vary cyclone inlet head geometries and ratios,” she says . “It has recently led to solid-liquid separation developing a South African-manufactured filter press.”