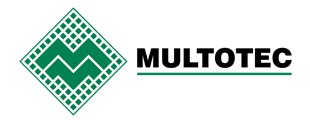
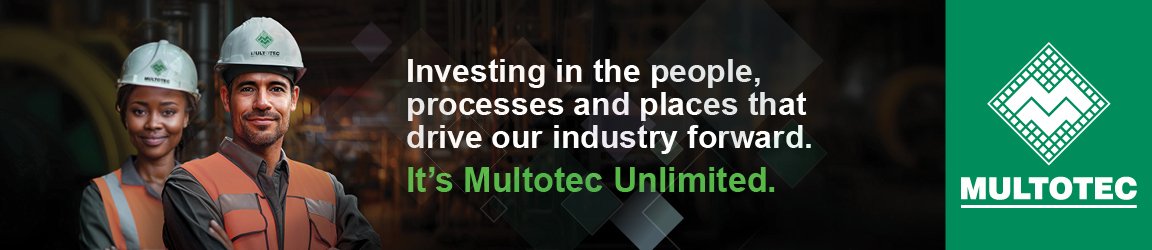
New presses give Multotec the edge in mill linings
Responding to the rising demand, Multotec has added to its facilities two new rubber vulcanisation presses at its extensive local manufacturing facility in Spartan, Gauteng – raising quality levels while reducing lead times for customers.
The new additions have improved both the production capacity of the facility as well as the dimensional capability in the production of lifter bars, shell plates, head plates and grate plates for mill linings.
According to Thando Makhoba, managing director of Multotec Rubber, the new hydraulic presses have larger daylight openings to accommodate higher throughput and larger dimensions of products.
One of the new presses, the largest yet installed by Multotec, is among the largest in South Africa’s wear lining industry. With a 2.7 m long platen size, it is 1.9 m wide and boasts a 1.1 m daylight and the press has a 3,600 tons pressing capacity.
“This enables us to produce lifter bars up to 400 mm wide, with advanced human-machine interface (HMI) software and a locally developed PLC control system,” says Makhoba. “It also means we can improve our production rates, so that we reduce the lead time on these items for customers.”
He also highlights the safety benefits of the new units, with the HMI hardware and software allowing operators to have less physical engagement with the machines during production. Adding to efficiency on one of the presses are two stripping tables – one directly in front of the press to pull the mould out of the daylight – and a side stripping table to pull out the first mould to make space for the second. This allows semi-automated loading and unloading, further accelerating the process.
Technical manager at Multotec Rubber, Waldo Verster, says the new presses allow Multotec to press more units per cycle, with one press capable of pressing between seven and 14 lifter bars at a time.
“These presses also improve our ability to service the demand for integrated liners, allowing us to integrate up to two lifter bars and two shell plates – or two lifter bars and two head plates – into a single liner,” says Verster.
“For the customer, these integrated liners are quicker to install, so they reduce mill re-lining time. And they are also safer, as they can be installed by a mill liner handler operated from outside the mill.”
A further opportunity for the new equipment is the market demand for larger lifter bars, as few companies can produce lifter bars measuring 400 mm in wide and 350 mm high. Makhoba notes that the installations demonstrate Multotec’s commitment to taking a technological lead in its sector, to optimise the operations of customers.
“This allows us to deliver high local content in our products, in line with the aims of the Mining Charter,” he says. “To the best of our knowledge, we are the only mill lining supplier in the country with a local content certification from the South African Bureau of Standards.”
Hashtags
#mineralsprocessing
#rubberliners