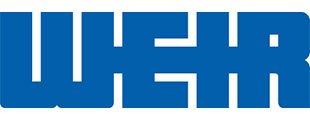
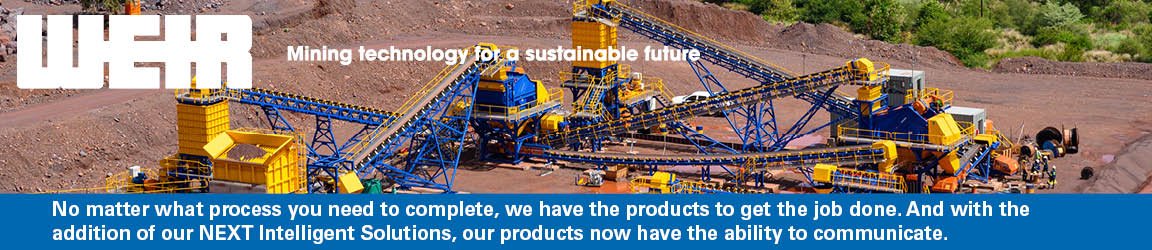
Not Just Any Pump Will Do For A Filter Press
The role of a filter press in recovering valuable saleable product makes it an important consideration for a mine operator, and just as important is the selection of the most appropriate pump for this application. Weir Minerals Africa has the expertise to advise on the best selection and offers a wide range of suitable pumps.
As a mission-critical system in the mineral concentration process, the filter press demands a carefully selected pump to ensure optimal performance and uptime.
According to Marnus Koorts, product manager for slurry pumps at Weir Minerals Africa, the role of a filter press in recovering valuable saleable product is an important consideration for a mine operator. The high pressures associated with operating a filter press, however, often lead the pump to underperform.
“The operation of a filter press involves a wide spectrum of pressure and flow conditions within each cycle,” Koorts says. “This ranges from high-flow, low-pressure conditions when slurry is initially being pumped into the press, to low-flow and high-pressure when full.”
He emphasises that it is not enough to simply specify a pump for the average of this range of conditions. Rather, it is vital to establish the minimum and maximum values on the spectrum, and to specify accordingly.
“Filter presses in the market can demand pressures of up to 45 bar,” he says. “In many cases, therefore, the application requires high-pressure pumps such as the Warman AHPP high pressure range. Where lower pressure requirements are present, the newer technology of the Warman WBH could be used as it is generally a more efficient pump with longer wear life of spare parts.”
Failure of the pump to deliver enough pressure to the filter results in the solid-liquid separation process being inefficient. The selection of the right size of pump is therefore an important starting point in ensuring optimal operation.
With decades of experience in this field, Weir Minerals Africa has developed the expertise to advise on the best selection. It also offers a wide range of pumps suitable for application with filter presses.
The next key aspect of the customer’s selection, Koorts says, is the choice of sealing arrangement. This aspect of the pump can often lead to issues in the plant, when valuable product is lost through leakage.
“An expeller seal is not usually recommended, as the pressure it generates to seal the pump is generally not sufficient in a filter press application,” he says.
The stuffing box option can be used under certain conditions. However, the pressure of the surface water needs to be higher than the pressure inside the pump. This means that it would usually be suitable on a low-pressure pump for a low-pressure filter press.
“When the filter press requires a higher pressure, then the plant will have to provide a water line with a higher pressure to feed the gland, or it will not seal properly,” he says.
The preferred sealing option is a mechanical seal. While more costly, the mechanical seal can offer the customer substantial savings by preventing product being lost and downtime being incurred.
“While the benefits of a mechanical seal far outweigh its cost, it must be properly installed by a specialist,” he warns. “It is a unique piece of equipment and we see plenty that fail due to incorrect installation.”
A further consideration is the level of corrosive aspects of trace elements in the slurry. This can lead to rapid corrosion of mild steel pumps, and many applications require stainless steel options.
Comprehensive technical backup needs to underpin each step in this process, emphasises Koorts. For Weir Minerals Africa, this begins with its high quality local manufacturing process. This integrated process includes foundries for casting components, through to local componentry manufacture and assembly capability.
“This quality control and capacity feeds into our spares availability and service exchanges for refurbished pumps,” he says. “The result is quick supply through our strategically located branch network with 12 offices in South Africa and eight through the rest of Africa.”