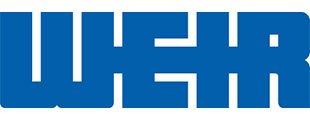
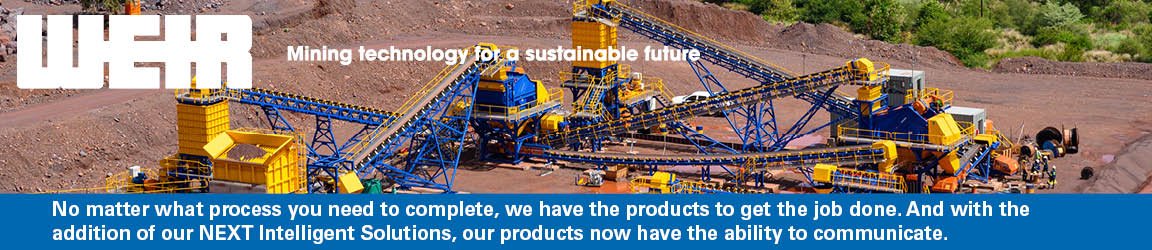
Weir Minerals integrates key brands in Mudflo™ pump
Integrated solutions are what separates equipment suppliers from solution providers, argues Marnus Koorts, general manager pump products at Weir Minerals Africa – and the recently launched Multiflo® Mudflo™ pump shows how this is done.
This dredge/excavator-mounted, mud-pumping innovation was launched last year, after being developed in response to a challenge which a customer faced, says Koorts. It is a heavy duty hydraulic submersible slurry pump designed for abrasive applications and large particle handling. Its application is primarily in reprocessing and relocating tailings ponds, maintaining water retention dams and managing slimes and sludge ponds.
“The Multiflo Mudflo pump successfully combines elements of the Warman MGS submersible slurry pump-end, and a custom Multiflo designed bearing assembly coupled to a hydraulic motor,” he says. “Another key ingredient is the pairing of twin Multiflo CB33 hydraulic cutters with Weir ESCO excavation teeth.”
The cutters mechanically agitate the settled solids, allowing abrasive and highly charged slurries and mud to be efficiently pumped. He emphasises that the components making up the Multiflo® Mudflo™ pump are drawn from Weir Minerals proven brands, and are carefully combined to produce an integrated solution that saves customers time and money. It also reduces environmental impact, by avoiding the costly and energy-intensive process excavating and trucking the material off site.
“The pump design includes Weir Minerals' Ultrachrome A05 chrome alloy casting for high wear resistance,” he says. “There is also a suction strainer to prevent excessively large particles clogging the pump.”
This ensures that the unit delivers optimal uptime alongside high performance levels: the Mudflo™ 200 pump is capable of pumping between 150 m3/h and 1,200 m3/h, up to a head of 82 metres. The pump can handle a maximum particle size of 80 mm, and a maximum liquid temperature of 35°C.
“While our integration of products has grown organically over the years, it has become more systematic and deliberate as our product range has grown and become more diverse,” says Koorts. “The way we have developed this solution shows the progress in recent years toward integrating our product lines to add value to our offerings.”
He notes that the process of ETO ensures that solutions developed by Weir Minerals’ engineering teams deliver more value than the sum of their component parts. In this case, the company’s dewatering experts were able to draw on the best technology from Weir Minerals’ Multiflo®, Warman® and Weir ESCO® brands – combining them with advanced hydraulics to create an innovative result.
“Our extensive footprint in the field and our close collaboration with customers on a daily basis gives us a detailed understanding of their specific requirements,” he says. “We can therefore ensure that our innovations are fit for purpose, being based on our considerable ETO capability and technical excellence.”