3D printing enhances components industry’s capabilities
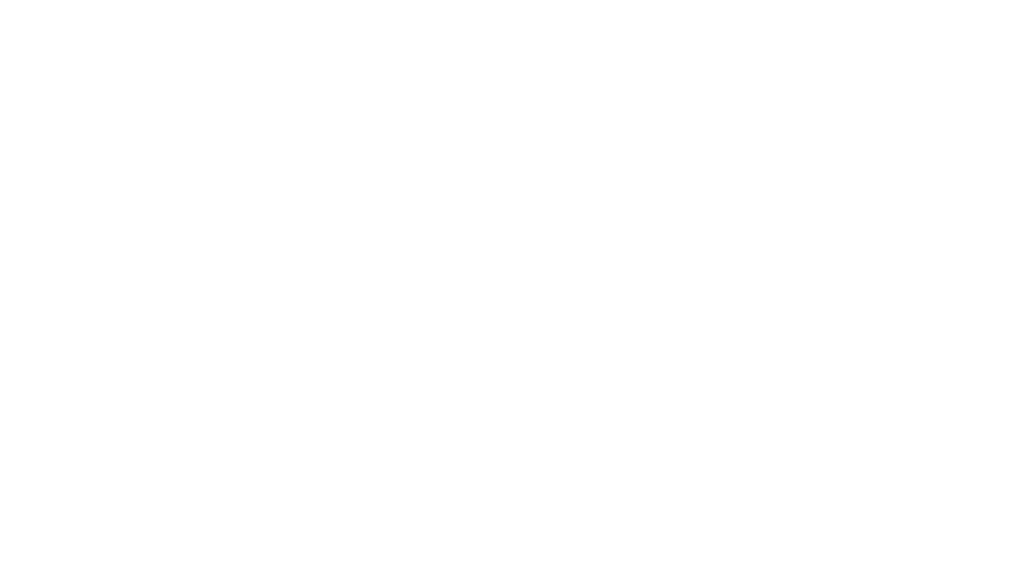
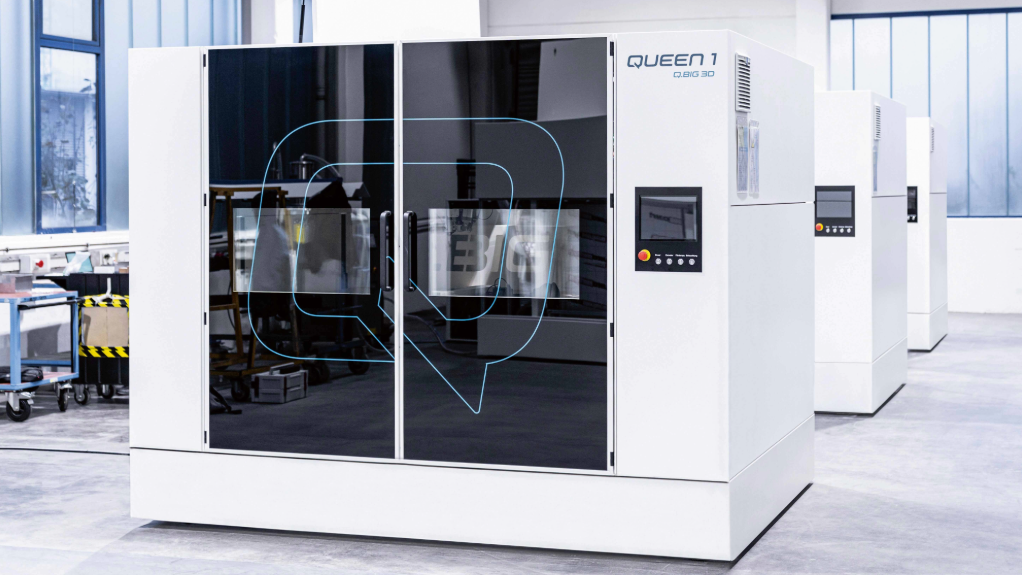
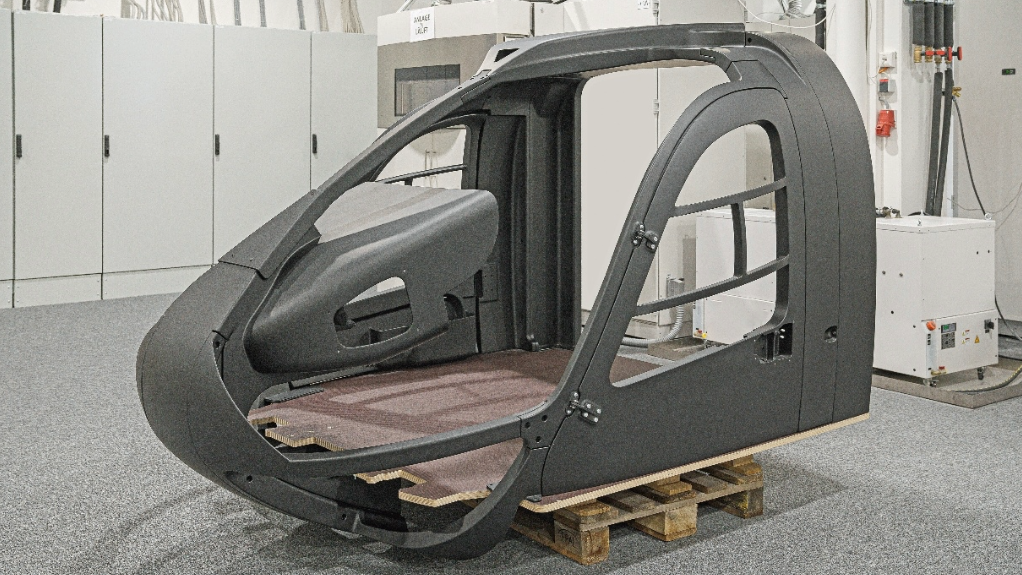
QUEEN1 3D PRINTER The QUEEN1 3D Printing system has the ability to manufacture various large-format automotive components in detail mode and turbo mode
3D HELICOPTER COCKPIT The QUEEN1 3D printer is able to print components, such as a cockpit for a helicopter
Additive manufacturing and three-dimensional (3D) printing solutions company Q.BIG 3D is transforming the way in which large-volume automotive components are manufactured using its QUEEN1 3D extrusion printing system, making it economically viable and beneficial for automotive industry players.
The company uses a variable fused granulate fabrication (VFGF) process, which includes the use of a variable nozzle that enables fast printing with a processing speed of about 500 mm/s, and high material throughputs guaranteed for geometric form and in-fill area jobs – referred to as ‘turbo mode’ – as well as low material throughputs for high-precision in the ‘detail mode’.
The detail mode of the variable nozzle is mainly used for fine structures or textures and fastening elements. In contrast, the turbo mode allows for enhanced speed for rapid build times during the manufacturing of large-volume automotive components.
Additionally, the QUEEN1 3D system, in tandem with the variable nozzle and VFGF process, applies the material layer by layer – much like primitive additive manufacturing or 3D printing – maintaining a combination of 1.5 mm in detail mode and 3 mm in turbo mode.
The benefits that accompany Q.BIG 3D’s product and service offerings are ample for automotive industry players and original-equipment manufacturers. Firstly, unlike traditional mould-based manufacturing processes, 3D extrusion printing of automotive parts does not come with high tool costs. This, in turn, makes it highly cost-effective, as manufacturers will not have to spend money on tools for single large-volume components.
“In a tool-based moulding process, the tool costs massively limit profitability. In 3D printing, we overcome these limits by combining a variable nozzle with a large build space,” says Q.BIG 3D founder Dennis Herman.
He adds that material cost procurement is the main benefit of 3D granulate printers, as this process does not require filaments, which are usually necessities in mould-based parts construction.
Some of the projects completed using the QUEEN1 3D printing system include model components for caravan construction; assembly and measuring jigs for automotive application; and a full-size helicopter cockpit.
These are indicative of the futuristic nature of 3D printing of fully functional automotive components for an array of transportation modes.
“We are producing the future. 3D material extrusion using the VFGF process is pushing the boundaries of what is possible and is making a whole new level of cost-effectiveness and amortisation possible.
“I see enormous potential for product development in large-format 3D printing. This also applies to lightweight construction, bionics and saving resources. Above all, however, the VFGF process is an accelerator for the Industry 4.0 approach,” enthuses Herman.
Comments
Press Office
Announcements
What's On
Subscribe to improve your user experience...
Option 1 (equivalent of R125 a month):
Receive a weekly copy of Creamer Media's Engineering News & Mining Weekly magazine
(print copy for those in South Africa and e-magazine for those outside of South Africa)
Receive daily email newsletters
Access to full search results
Access archive of magazine back copies
Access to Projects in Progress
Access to ONE Research Report of your choice in PDF format
Option 2 (equivalent of R375 a month):
All benefits from Option 1
PLUS
Access to Creamer Media's Research Channel Africa for ALL Research Reports, in PDF format, on various industrial and mining sectors
including Electricity; Water; Energy Transition; Hydrogen; Roads, Rail and Ports; Coal; Gold; Platinum; Battery Metals; etc.
Already a subscriber?
Forgotten your password?
Receive weekly copy of Creamer Media's Engineering News & Mining Weekly magazine (print copy for those in South Africa and e-magazine for those outside of South Africa)
➕
Recieve daily email newsletters
➕
Access to full search results
➕
Access archive of magazine back copies
➕
Access to Projects in Progress
➕
Access to ONE Research Report of your choice in PDF format
RESEARCH CHANNEL AFRICA
R4500 (equivalent of R375 a month)
SUBSCRIBEAll benefits from Option 1
➕
Access to Creamer Media's Research Channel Africa for ALL Research Reports on various industrial and mining sectors, in PDF format, including on:
Electricity
➕
Water
➕
Energy Transition
➕
Hydrogen
➕
Roads, Rail and Ports
➕
Coal
➕
Gold
➕
Platinum
➕
Battery Metals
➕
etc.
Receive all benefits from Option 1 or Option 2 delivered to numerous people at your company
➕
Multiple User names and Passwords for simultaneous log-ins
➕
Intranet integration access to all in your organisation