Chemicals company unpacks carbon neutrality roadmap
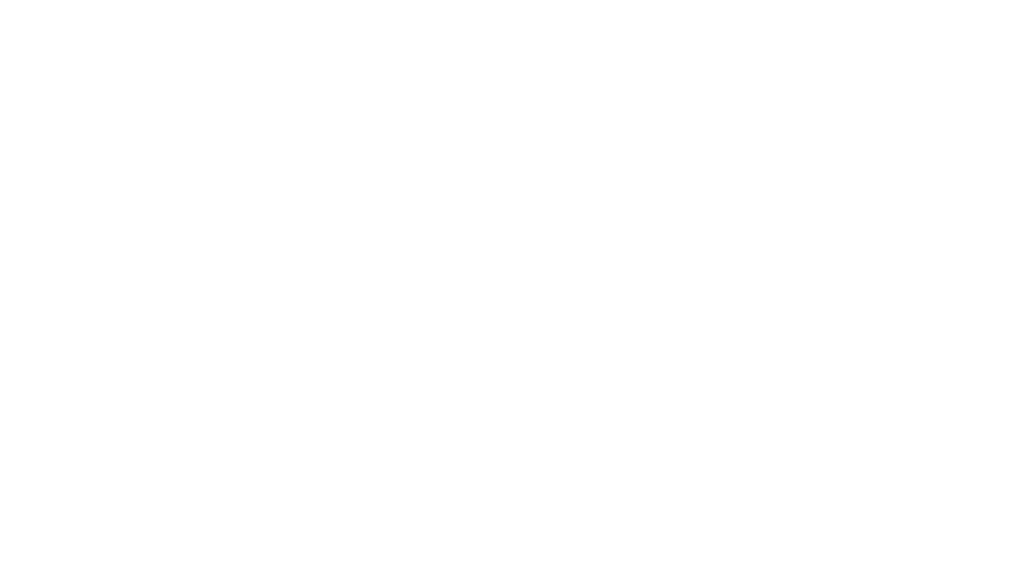
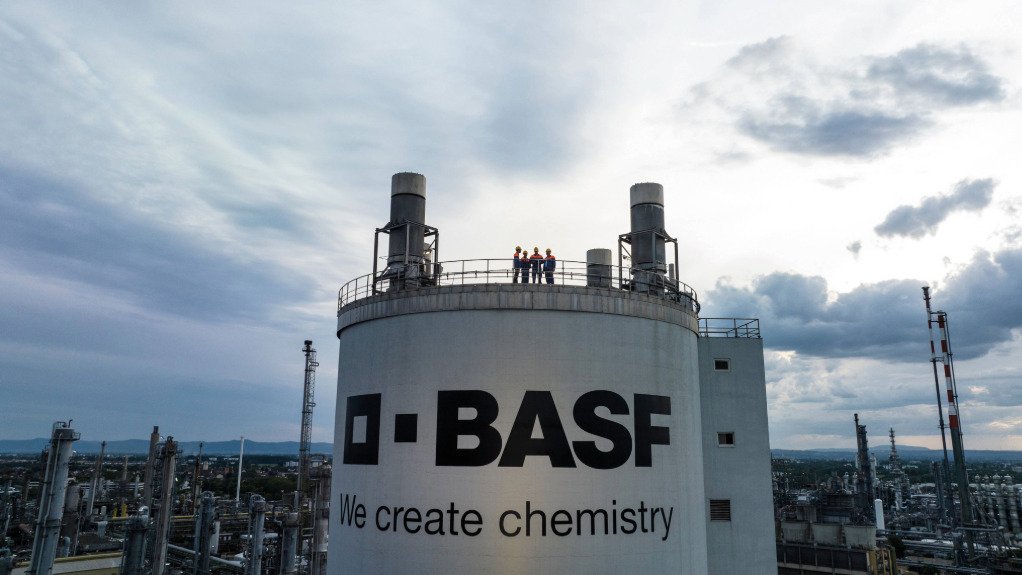
LOFTY AMBITIONS BASF Performance Materials is well on the way to reaching carbon neutrality by 2050
Multinational chemicals company BASF Performance Materials, the largest chemicals producer globally, in August released its strategic roadmap toward achieving carbon neutrality by 2050 and highlighted key milestones on its route toward a circular economy.
With that in mind, the division, which brings together BASF’s entire materials know-how regarding innovative and customised plastics, is positioning itself at the forefront of the “much-needed sustainability transformation” in plastics.
“We want to enable our clients’ transformation by offering a portfolio with lower carbon footprint and diverse circular solutions,” says BASF Performance Materials president Martin Jung.
He adds that the group works through the entire life cycle of plastics to make them more sustainable: from means of producing plastics in a more resource-efficient manner, to improving their use and “giving them a new life”.
“We call this transformation #ourplasticsjourney, and with our roadmap, we are laying an important foundation to make this transformation go faster,” he states.
Accelerating the Journey
BASF has set clear targets to reduce Scope 1 and 2 carbon emissions by 25% by 2030, using 2018 as a baseline, and by 15% for Scope 3.1 emissions, with 2022 as the baseline. The company has the overall goal of achieving carbon neutrality by 2050.
The first and most imperative step of the company’s carbon management strategy is to increase the use of green electricity.
“In 2023 already, more than one-third of our Performance Materials sites worldwide were running on green electricity, and we are making relentless efforts to switch them all completely by 2025”, says Jung.
Green electricity also plays an essential role earlier in BASF’s value chain, particularly in the reduction of Scope 3.1 emissions.
One of BASF’s suppliers, glass fibre solutions developer 3B Fibreglass, supplies the company with glass fibres that are used as reinforcement for thermoplastic and thermoset polymers.
By using solar panels to generate electricity, 3B Fibreglass has significantly reduced its carbon emissions. As a result, the glass fibres’ reduced product carbon footprint is transferred to BASF’s products and, ultimately, to its clients.
This showcases the potential of a circular economy when all stakeholders are committed to sustainability.
Supporting Clients
BASF is actively certifying its manufacturing sites globally with the International Sustainability and Carbon Certification PLUS and REDCert2.
Most performance materials sites are certified in at least one scheme and additional sites will be certified in all regions by the end of 2024.
These schemes certify the amount of renewable raw materials that are attributed to biomass balanced products.
These renewable feedstocks replace a part of the fossil-based raw materials needed for production at the start of the value chain.
The process ensures identical product quality and properties, ensuring clients can use the materials as drop-in solutions.
The same applies to chemically recycled feedstocks like pyrolysis oil from scrap tires or mixed plastic waste.
“Today, a majority of our product portfolio is already available based on renewable feedstocks and with significantly lower or even net-zero product carbon footprints,” says BASF Performance Materials sustainability head Matthias Scheibitz.
He adds that BASF wants to support its clients as early as possible on their journeys to meet their sustainability targets and therefore offers diverse circularity options.
Ambitious Target
To increase the use of circular feedstock in its product portfolio, BASF is looking into the most promising mass balance solutions, thereby meeting clients’ expectations across multiple industries.
On its sustainability journey, BASF Performance Materials commits to reaching at least 20% of circular economy sales by 2030 by making use of products that support the substitution of fossil-based inputs by circular feedstock by at least 20%.
A strong contributor to this target is BASF’s biopolymer portfolio, which is the “optimal solution” for certified compostable packaging and agricultural applications.
Biopolymers contribute to closing the bio- logical loop by reducing food waste, increasing organic recycling of organic waste, returning nutrients to the soil and avoiding the accumulation of microplastics in agricultural soil.
Sustainable Solutions and Co-Creations
BASF Performance Materials views co-creation with clients and partners from all along its diverse value chains as the cornerstone of its sustainability efforts within the plastics industry.
“For us, it is essential to offer our clients commercial and series-ready, sustainable solutions and inspire them with what is possible today,” says Jung, stressing that circularity needs to be deeply embedded into the product design phase.
As an example, BASF Performance Materials has recently developed an innovative polyurethane foam technology that enables simplified and scalable mechanical recycling.
The first steering wheel prototypes to use this new technology have already been presented publicly in Europe and China.
Further, multinational technology conglomerate Siemens’ SIRIUS 3RV2 circuit breaker is the first electrical safety product to include components from biomass-balanced plastics where fossil feedstock at the beginning of the value chain is replaced by biomethane derived from renewable sources such as agricultural waste.
In a similar way, BASF collaborated on international furniture manufacturer Steelcase’s Flex Perch Stool using plastics derived from chemicals recycling to prevent incineration or disposal at a landfill.
In other cases, bio-based and recycled raw materials are used complementarily, such as the door handle and the crash absorber of the Mercedes-Benz S-Class, which was developed in conjunction with German automotive manufacturer Mercedes-Benz AG.
The products combine pyrolysis oil from scrap tires and biomethane from organic waste to replace fossil-based raw materials in plastics manufacturing but retain virgin material properties.
Comments
Press Office
Announcements
What's On
Subscribe to improve your user experience...
Option 1 (equivalent of R125 a month):
Receive a weekly copy of Creamer Media's Engineering News & Mining Weekly magazine
(print copy for those in South Africa and e-magazine for those outside of South Africa)
Receive daily email newsletters
Access to full search results
Access archive of magazine back copies
Access to Projects in Progress
Access to ONE Research Report of your choice in PDF format
Option 2 (equivalent of R375 a month):
All benefits from Option 1
PLUS
Access to Creamer Media's Research Channel Africa for ALL Research Reports, in PDF format, on various industrial and mining sectors
including Electricity; Water; Energy Transition; Hydrogen; Roads, Rail and Ports; Coal; Gold; Platinum; Battery Metals; etc.
Already a subscriber?
Forgotten your password?
Receive weekly copy of Creamer Media's Engineering News & Mining Weekly magazine (print copy for those in South Africa and e-magazine for those outside of South Africa)
➕
Recieve daily email newsletters
➕
Access to full search results
➕
Access archive of magazine back copies
➕
Access to Projects in Progress
➕
Access to ONE Research Report of your choice in PDF format
RESEARCH CHANNEL AFRICA
R4500 (equivalent of R375 a month)
SUBSCRIBEAll benefits from Option 1
➕
Access to Creamer Media's Research Channel Africa for ALL Research Reports on various industrial and mining sectors, in PDF format, including on:
Electricity
➕
Water
➕
Energy Transition
➕
Hydrogen
➕
Roads, Rail and Ports
➕
Coal
➕
Gold
➕
Platinum
➕
Battery Metals
➕
etc.
Receive all benefits from Option 1 or Option 2 delivered to numerous people at your company
➕
Multiple User names and Passwords for simultaneous log-ins
➕
Intranet integration access to all in your organisation