Company investing in new tech despite challenging market
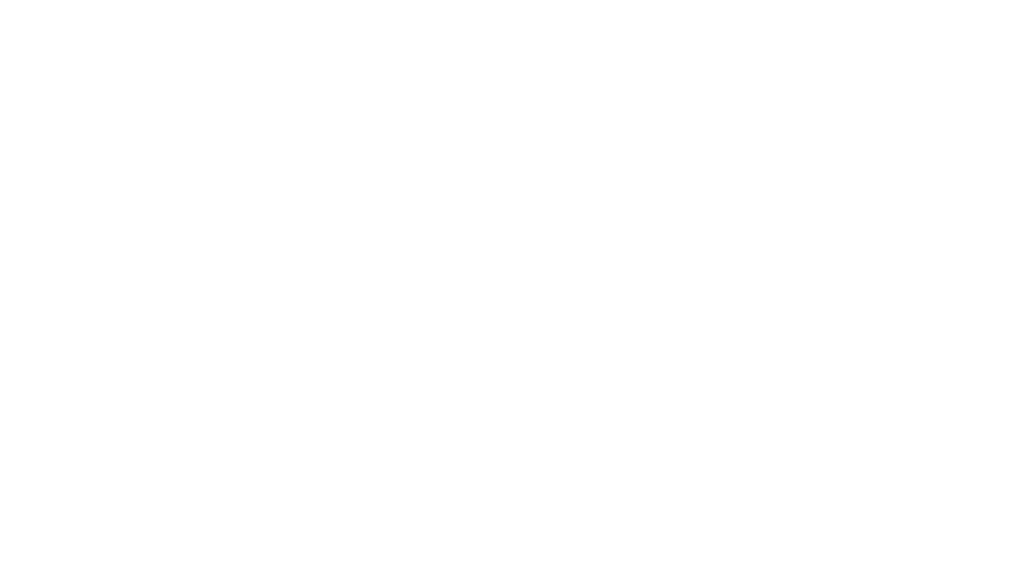
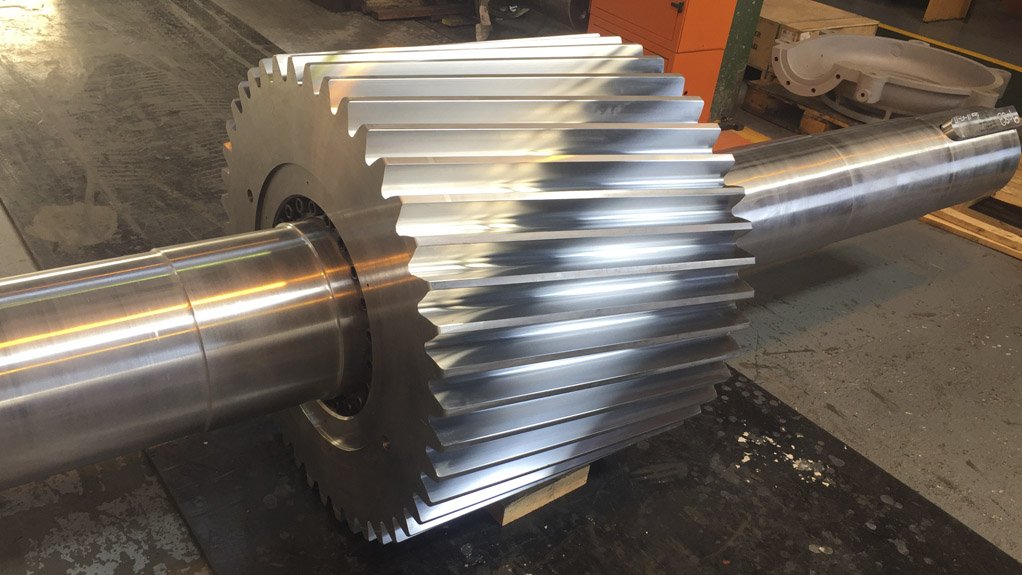
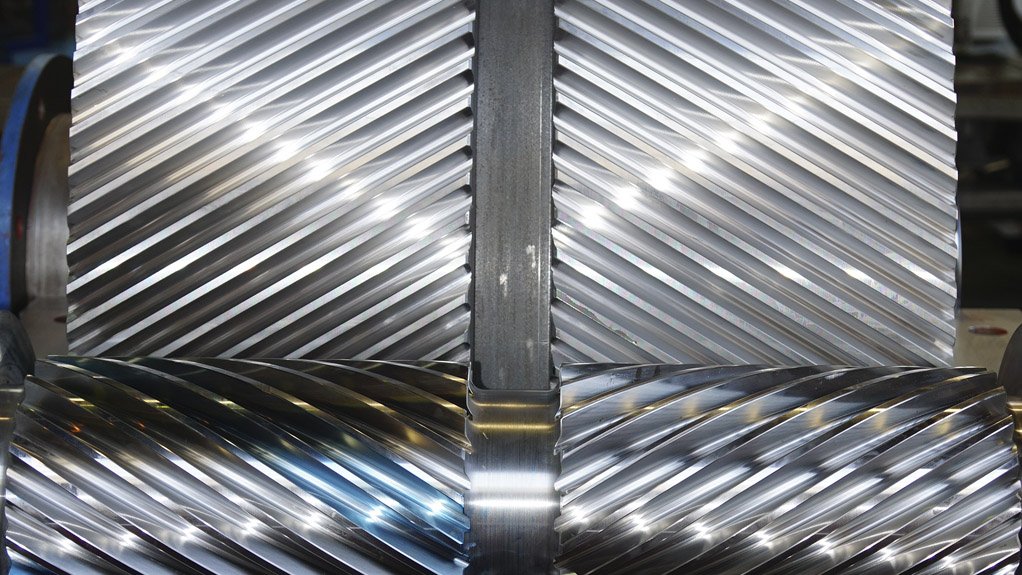
ON THE GRIND The Hӧfler Rapid 2000 cylindrical gear grinding machine manufactures high-accuracy pinions for mill and kiln open gearing applications
IN GEAR The Hӧfler Rapid 2000 cylindrical gear grinding machine will increase the company’s capacity to manufacture and supply the highest-quality gears
Mining solutions provider Harcliff Mining Services has installed a German-made Höfler Rapid 2000 cylindrical gear grinding machine at its manufacturing facility in Gauteng, South Africa.
The machine, bought from Switzerland-headquartered Swiss-German gear technology company Klingelnberg Group, was successfully commissioned by Harcliff in mid-June.
Harcliff technical director Graeme Kneale tells Mining Weekly that, in the mining industry, this machine will be used to manufacture high-accuracy gearbox internals used in mill main drives, barring drives, open-gearing mill pinions and industrial gearboxes.
He points out that Harcliff invested in the new technology despite the mining sector experiencing the challenges of the South African economy’s poor performance and a lack of international investment. The lack of investment has resulted in fewer greenfield projects getting off the ground: “With many of our local mines nearing the end of their life span, this is, of course, a big concern because they are essentially the lifeblood of our economy and feed work to many industries such as ours.”
Nonetheless, Harcliff has survived in these tough economic times, owing to the company’s ability to repair and refurbish equipment. This service ensures much-reduced capital outlay for mines, which, in turn, enables those considered as marginal to continue operating, he says.
Harcliff’s investment in the Höfler Rapid 2000 is expected to boost the company’s sustainability by increasing its capacity to manufacture and supply the highest-quality gears to customers throughout Africa and to service new markets.
“Harcliff has [grown] year-on-year since its establishment and will strive to continue this growth,” avers Kneale.
He says the Höfler Rapid 2000 boasts the latest technology in manufacturing high- precision gears, producing gears of extremely high quality in terms of profile, form, pitch, lead and surface finish.
It also boasts on-board testing heads that can measure and certify gear tooth geometry to high DIN – Deutsches Institut für Normung (German institute for standardisation) – and American Gear Manufacturers Association accuracy classes. “We are quite proud of being able to produce high-standard gearing, as this will optimise gear unit and mill pinion operational efficiency and reliability.”
Subsequently, the manufactured gearing will have increased performance and reliability. Further, the installation of such gears is far quicker and their operation produces reduced harmonics, thereby extending the life span of gears and bearings.
Kneale indicates that, in addition to these operational benefits, companies that use grinding mills can further benefit from the machine’s high cutting speed, which enables Harcliff to offer its clients better-quality products with much shorter delivery lead times. In some circumstances, product cost may be reduced owing to this shorter production time.
Before acquiring the Höfler Rapid 2000, Harcliff used gear hobbers and gear shapers, which, despite being conventional and accurate, were extremely labour intensive and slow.
Harcliff is actively educating the market on the Höfler Rapid 2000, informing companies that this technology is now available to them at the company’s Johannesburg workshop.
Crushing, Milling and Screening
Harcliff offers a turnkey package, from design to installation, for new and previously owned mills and has successfully completed projects in gold, platinum, copper, vanadium and diamond mining operations, notes Kneale.
Moreover, the company has its own field service technicians who are available 24/7 to assist clients.
Kneale highlights that the company completed a total mill rebuild for a chrome producer in August. The project required extensive redesign and repairs to ensure that the mill adhered to its original design specifications. The mill was previously being used in a completely different process, but the company’s design team effected the required speed and liner changes to ensure a “flawless” operation in its new application.
Moreover, Harcliff also secured an order to supply a new mill to a large vanadium producer in South Africa, in August, highlights Kneale. For this project, design work is at an advanced stage and the manufacturing stage is imminent. The mill is scheduled to be installed and commissioned in April 2018.
In the crushing sector, Harcliff is the appointed agent for Brazil-based cone and jaw crushers supplier Furlan Crushers.
The company is also the local agent for crusher parts supplier Excel Foundry & Machine. Kneale avers that Excel is arguably the biggest stockholder of crusher spares in the world and carries parts for all the well-known brands of cone and gyratory crushers, as well as parts for hydraulic and electric shovels.
In February, Harcliff supplied a shaft – forged from 40 t of steel and weighing, after final machining, a hefty 27 t – for a very large gyratory crusher, Kneale says.
The company is also supplied a scrubber (roller mill) to a diamond operation in Angola, in June. Within a month of operation, the mine discovered its second-largest stone, weighing in at more than 200 ct, he enthuses.
For milling, Harcliff offers new components manufacture and the repair of any part of a mill, including trunnions, shells, girth gears, pinions, gearboxes, motors, liners and lubrication units. The company also has three field-service crews – each with its own set of advanced tooling equipment, such as laser alignment, vibration monitoring and thermal cameras – which enables Harcliff to immediately mobilise a team to site to deal with breakdowns.
Harcliff has strategic global alliances with manufacturing facilities in Asia and locally represents European original-equipment manufacturers (OEMs). The company is also the local agent and service centre for UK OEM Radicon Gear Drives.
Comments
Announcements
What's On
Subscribe to improve your user experience...
Option 1 (equivalent of R125 a month):
Receive a weekly copy of Creamer Media's Engineering News & Mining Weekly magazine
(print copy for those in South Africa and e-magazine for those outside of South Africa)
Receive daily email newsletters
Access to full search results
Access archive of magazine back copies
Access to Projects in Progress
Access to ONE Research Report of your choice in PDF format
Option 2 (equivalent of R375 a month):
All benefits from Option 1
PLUS
Access to Creamer Media's Research Channel Africa for ALL Research Reports, in PDF format, on various industrial and mining sectors
including Electricity; Water; Energy Transition; Hydrogen; Roads, Rail and Ports; Coal; Gold; Platinum; Battery Metals; etc.
Already a subscriber?
Forgotten your password?
Receive weekly copy of Creamer Media's Engineering News & Mining Weekly magazine (print copy for those in South Africa and e-magazine for those outside of South Africa)
➕
Recieve daily email newsletters
➕
Access to full search results
➕
Access archive of magazine back copies
➕
Access to Projects in Progress
➕
Access to ONE Research Report of your choice in PDF format
RESEARCH CHANNEL AFRICA
R4500 (equivalent of R375 a month)
SUBSCRIBEAll benefits from Option 1
➕
Access to Creamer Media's Research Channel Africa for ALL Research Reports on various industrial and mining sectors, in PDF format, including on:
Electricity
➕
Water
➕
Energy Transition
➕
Hydrogen
➕
Roads, Rail and Ports
➕
Coal
➕
Gold
➕
Platinum
➕
Battery Metals
➕
etc.
Receive all benefits from Option 1 or Option 2 delivered to numerous people at your company
➕
Multiple User names and Passwords for simultaneous log-ins
➕
Intranet integration access to all in your organisation