Wheel alignment crucial to ensuring end-carriages last longer
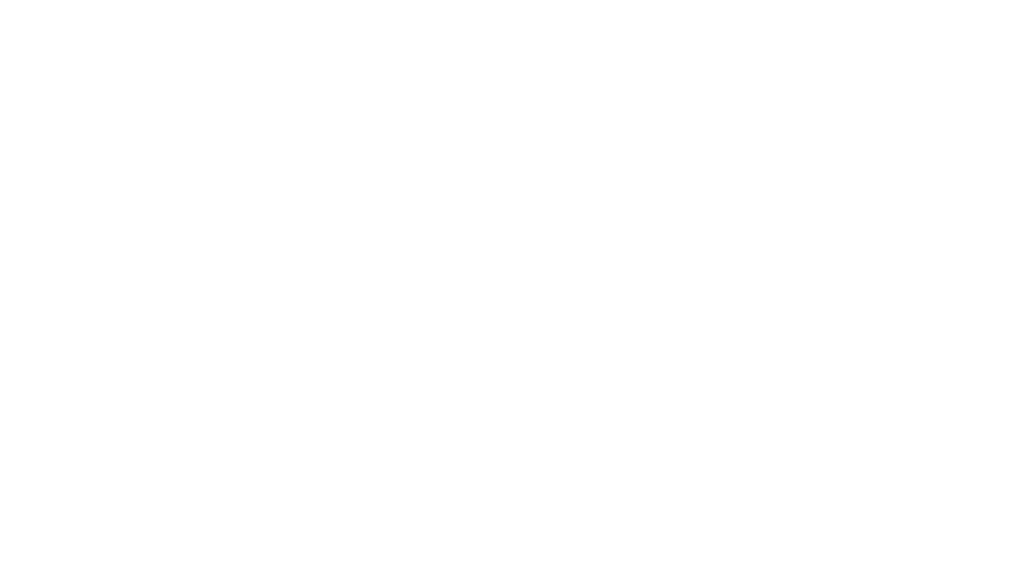
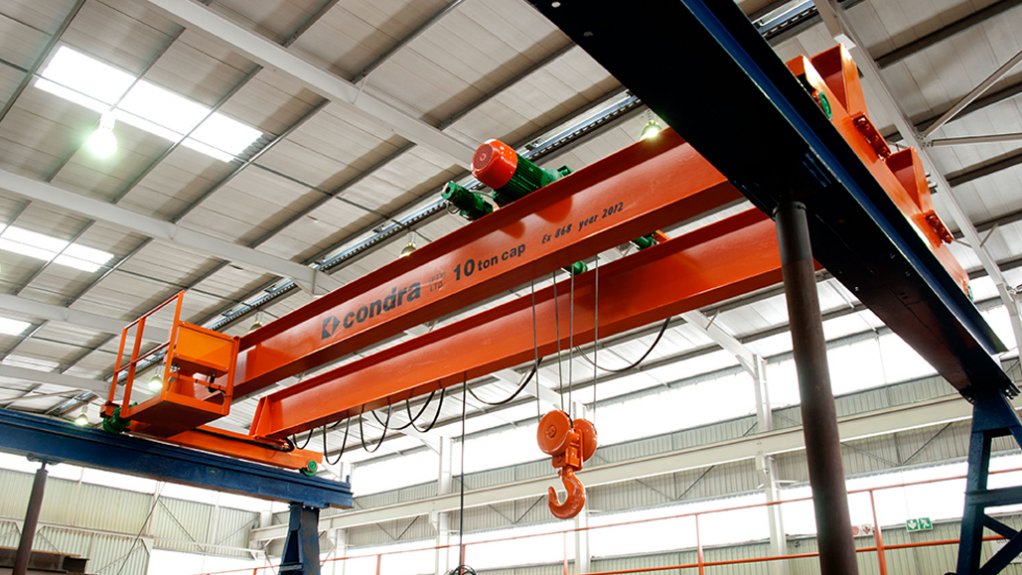
DOUBLE-GIRDER OVERHEAD CRANE UNDER TEST The twin girders are fixed to end-carriages at each end, and alignment of these wheels is critical to prevent wear
End-carriages are key subassemblies in overhead cranes, and customers are advised not to attempt their own end-carriage assembly using individually sourced wheel blocks, as wheel alignment is critical to ensuring the longevity of these ‘feet’ of overhead cranes, says crane and hoists specialist company Condra MD Marc Kleiner.
End-carriages support girders and hoists, and move them along the rails. Wheel wear as a result of misalignment of the wheels at each end of the end-carriage and/or distortion of the rails caused by heat can result in excessive end-carriage maintenance costs.
Wheel alignment within the end-carriage should not be confused with the alignment of the end-carriages at either end of the girder, which is a much simpler process that most manufacturers would be able to carry out.
To avoid misalignment within the end-carriage wheels, Condra recommends sourcing the end-carriage as a completed subassembly from a single company, he states.
“Wheel alignment is a very specialised and delicate process. Get it wrong, and the steel-on-steel wheeled movement of the crane will result in rapid wheel wear and increased maintenance costs.”
The second cause of wheel wear, rail distortion, is more difficult to counter, because it is caused by the very high temperatures that accumulate in the upper levels of all factories, where the rails are located.
Although periodic wheel replacement is inevitable, owing to rail distortion, Condra has minimised costs through careful design of the wheel block, which allows for the quick and easy removal of the wheels in position using a simplified bolt arrangement, explains Kleiner.
Stocks of service exchange units are held either on site or by Condra, according to customer preference, he adds.
Meanwhile, the Condra design office needs to know only the load and how fast this load has to move to supply a recommended configuration of the wheels, the motor, the gearbox and the brake for the wheel blocks, as well as recommendations for a fully designed end-carriage and a rail. Should the rail not be available, Condra will adjust the wheel diameter and, if necessary, the motor and gearbox.
“Tell us what you want to move and how fast you want to move it, and Condra will come up with the solution,” says Kleiner, explaining that the design process, simplified for the customer, nevertheless involves end-carriage design and component selection. About 20 000 design combinations are possible.
“Wheels, for example, are available in ten off-the-shelf diameters, from 63 mm to 630 mm, with each one offered with the flange on either side, or flangeless, and in widths from 30 mm to 125 mm to suit the rail. There are also different motor powers and mounting arrangements for the wheel blocks, and the overall end-carriage varies in length, depending on the girder arrangement."
Condra generally uses larger-diameter wheels than its competitors to reduce loading and decrease rolling resistance. The result is a longer component life span and lower overall lifetime costs.
“With our design, it is not necessary to change the end-carriage wheels every two years,” highlights Kleiner.
Condra’s end-carriages are among several component assemblies offered to crane manufacturers worldwide. Hoists, crabs, bottom blocks, cable-loop systems and enclosed conductor systems are also available. Hoists are supplied with capacities of up to 500 t.
All end-carriages are manufactured to customer specification for final assembly, eliminating the need to transact with multiple suppliers, and a 12-month guarantee is standard, Kleiner concludes.
Comments
Press Office
Announcements
What's On
Subscribe to improve your user experience...
Option 1 (equivalent of R125 a month):
Receive a weekly copy of Creamer Media's Engineering News & Mining Weekly magazine
(print copy for those in South Africa and e-magazine for those outside of South Africa)
Receive daily email newsletters
Access to full search results
Access archive of magazine back copies
Access to Projects in Progress
Access to ONE Research Report of your choice in PDF format
Option 2 (equivalent of R375 a month):
All benefits from Option 1
PLUS
Access to Creamer Media's Research Channel Africa for ALL Research Reports, in PDF format, on various industrial and mining sectors
including Electricity; Water; Energy Transition; Hydrogen; Roads, Rail and Ports; Coal; Gold; Platinum; Battery Metals; etc.
Already a subscriber?
Forgotten your password?
Receive weekly copy of Creamer Media's Engineering News & Mining Weekly magazine (print copy for those in South Africa and e-magazine for those outside of South Africa)
➕
Recieve daily email newsletters
➕
Access to full search results
➕
Access archive of magazine back copies
➕
Access to Projects in Progress
➕
Access to ONE Research Report of your choice in PDF format
RESEARCH CHANNEL AFRICA
R4500 (equivalent of R375 a month)
SUBSCRIBEAll benefits from Option 1
➕
Access to Creamer Media's Research Channel Africa for ALL Research Reports on various industrial and mining sectors, in PDF format, including on:
Electricity
➕
Water
➕
Energy Transition
➕
Hydrogen
➕
Roads, Rail and Ports
➕
Coal
➕
Gold
➕
Platinum
➕
Battery Metals
➕
etc.
Receive all benefits from Option 1 or Option 2 delivered to numerous people at your company
➕
Multiple User names and Passwords for simultaneous log-ins
➕
Intranet integration access to all in your organisation