Firm develops new process to recover cyanide
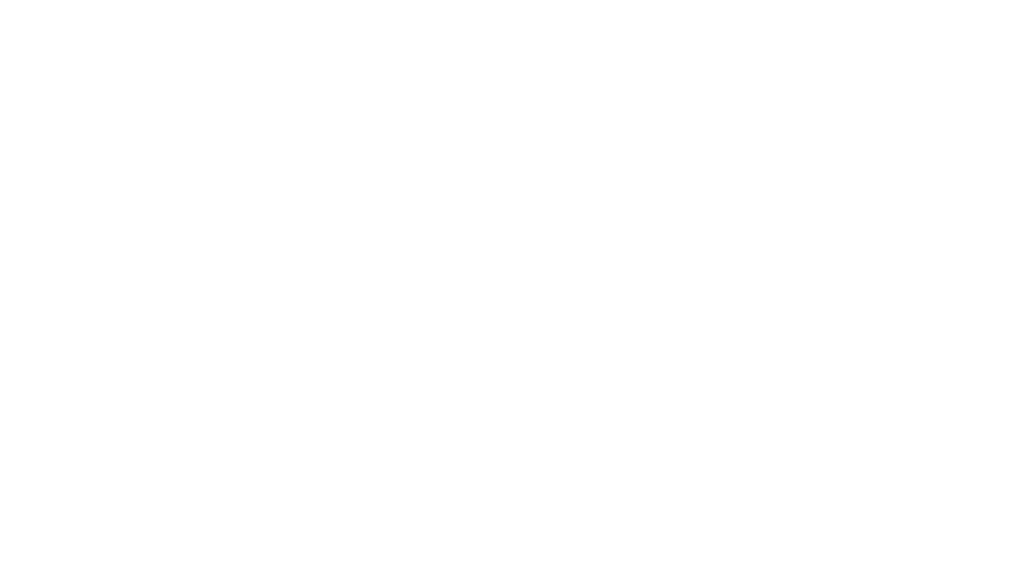
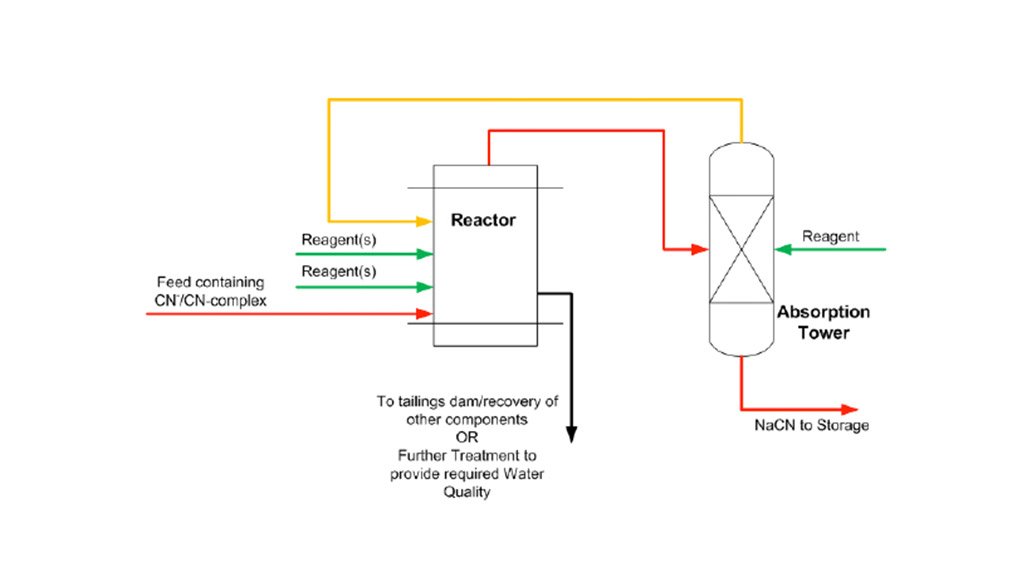
RECOVERY PROCESS Submerged Industrial’s cyanide recovery process produces an instantaneous reaction in the reactor, with zero emissions, owing to its closed-circuit recovery process
Separation technology provider Submerged Industrial has developed a unique process to recover cyanide, a substance most commonly used as a reagent in the gold recovery process and, in some cases, produced as an unwanted by-product in the process industry.
Submerged Industrial MD Samuel de Klerk tells Mining Weekly that the process can be applied in mining and large-scale process industries.
He further explains that while the technology was first introduced in 2003 to assist in minerals processing and also in solids separation in industrial wastewater, the reagents used in the recovery process have been changed to allow for cyanide recovery for reuse.
Submerged Industrial provides a unique solution for cyanide recovery in the form of solid sodium cyanide. The chemistry during the conventional recovery process is maintained, but with technology and processes that differ from the conventional stripping and recovery practice – the acidification-volitilisation- reneutralisation, or cyanisorb, process, which removes cyanide from the solution to produce gaseous hydrogen cyanide.
Submerged Industrial’s process has only two main process units – a specialised reactor and an absorption tower – as opposed to the conventional method that uses an acidification reaction vessel, a stripping tower and an absorption tower, as well as a significant network of reticulation streams.
The conventional process also requires the use of large, open cyanide-leaching stir tanks in which the reaction takes place. The hazards involved in this process include a long retention time in the acidification vessel, which causes increased risk of exposure to hydrogen cyanide (HCN) and the risk of releasing toxic gases into the environment.
However, Submerged Industrial’s approach produces an instantaneous reaction in the reactor, with zero emissions, owing to its closed- circuit recovery process, which results in minimum risk of exposure to HCN.
Further, during the conventional cyanide recovery process, cyanide is stripped and recovered from mill tailings, with recoveries of up to 90%, while Submerged Industrial’s process enables recovery and reuse of between 98% and 99% of cyanide, with up to 100% of possible cyanide, depending on the ore composition, as contaminants in the ore effect the recovery rate.
Submerged Industrial’s process produces sodium cyanide and a virtually cyanide-free slurry that can either be treated further to produce the requisite water quality or dewatered rapidly using one of Submerged Industrial’s dewatering technologies, which entails using an altered version of the recovery reactor with a different chemistry.
The most significant difference between the two processes is that the Submerged Industrial process uses a closed-loop system and functions with negative pressure to ensure that all gaseous streams are recycled back into the system. “A leak would simply add air to our system,” explains De Klerk.
Additional benefits of the Submerged Industrial process is that the equipment used has a much smaller footprint – 20 m × 20 m – than the 50 m × 60 m equipment used in a conventional recovery process. In terms of overall price, the Submerged Industrial process is as much as 30% more cost effective than the conventional process, owing to the instantaneous reaction time and its smaller footprint.
De Klerk says the process can even be 40% more cost effective when compared with the price of destructing the cyanide.
There is also an added benefit in the reduction in electricity and chemicals consumption when opting to use Submerged Industrial’s process, he concludes.
Comments
Press Office
Announcements
What's On
Subscribe to improve your user experience...
Option 1 (equivalent of R125 a month):
Receive a weekly copy of Creamer Media's Engineering News & Mining Weekly magazine
(print copy for those in South Africa and e-magazine for those outside of South Africa)
Receive daily email newsletters
Access to full search results
Access archive of magazine back copies
Access to Projects in Progress
Access to ONE Research Report of your choice in PDF format
Option 2 (equivalent of R375 a month):
All benefits from Option 1
PLUS
Access to Creamer Media's Research Channel Africa for ALL Research Reports, in PDF format, on various industrial and mining sectors
including Electricity; Water; Energy Transition; Hydrogen; Roads, Rail and Ports; Coal; Gold; Platinum; Battery Metals; etc.
Already a subscriber?
Forgotten your password?
Receive weekly copy of Creamer Media's Engineering News & Mining Weekly magazine (print copy for those in South Africa and e-magazine for those outside of South Africa)
➕
Recieve daily email newsletters
➕
Access to full search results
➕
Access archive of magazine back copies
➕
Access to Projects in Progress
➕
Access to ONE Research Report of your choice in PDF format
RESEARCH CHANNEL AFRICA
R4500 (equivalent of R375 a month)
SUBSCRIBEAll benefits from Option 1
➕
Access to Creamer Media's Research Channel Africa for ALL Research Reports on various industrial and mining sectors, in PDF format, including on:
Electricity
➕
Water
➕
Energy Transition
➕
Hydrogen
➕
Roads, Rail and Ports
➕
Coal
➕
Gold
➕
Platinum
➕
Battery Metals
➕
etc.
Receive all benefits from Option 1 or Option 2 delivered to numerous people at your company
➕
Multiple User names and Passwords for simultaneous log-ins
➕
Intranet integration access to all in your organisation