Expansion secures company’s position in growing market
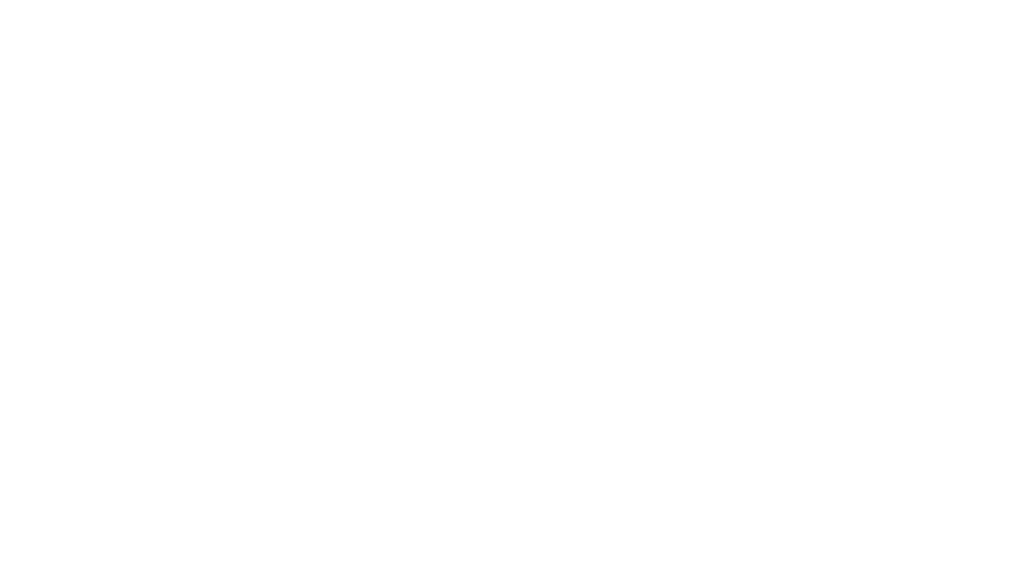
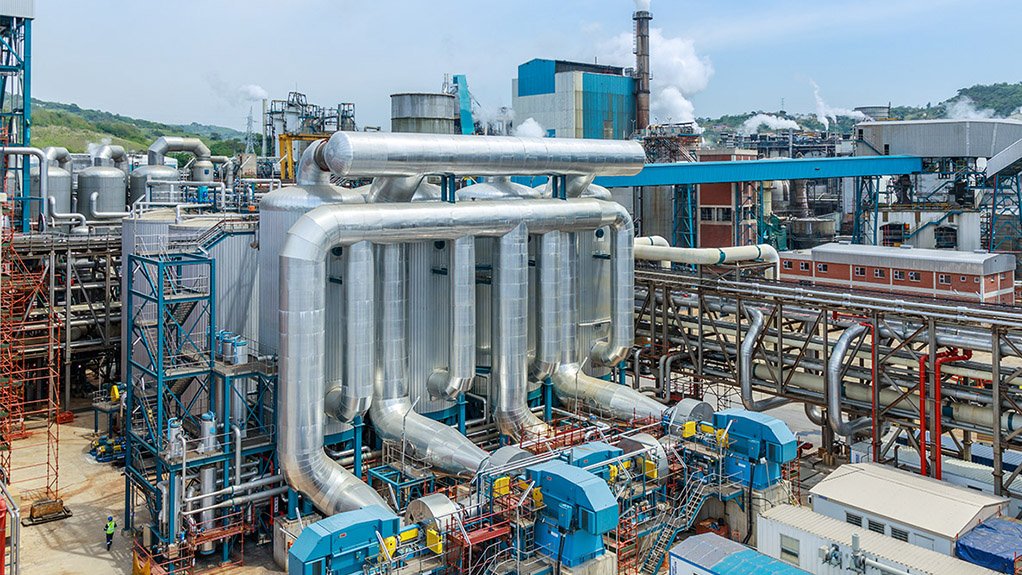
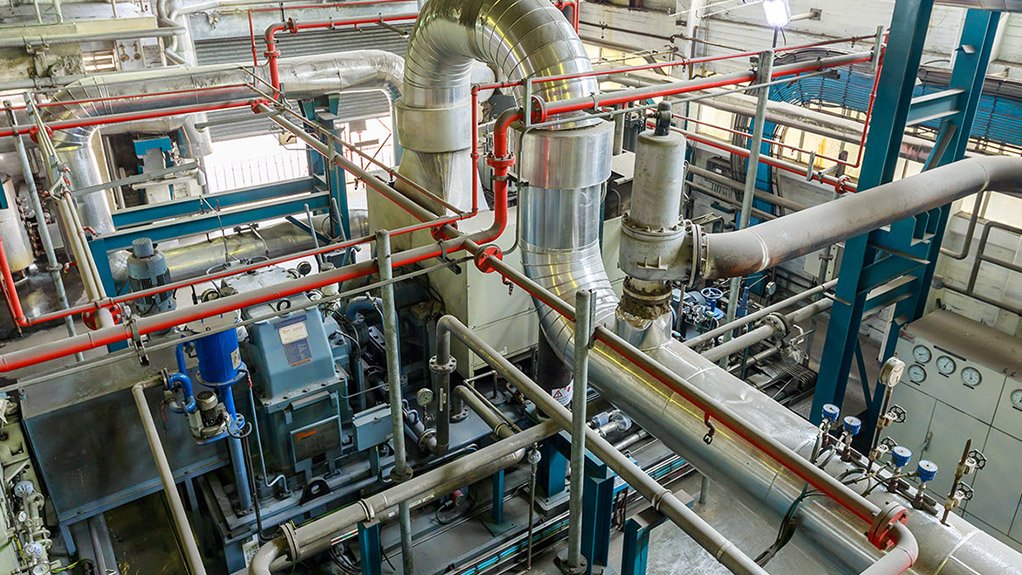
PROJECT VULINDLELA The R7.7-billion project is aimed at increasing the capacity and global competitiveness of the Saiccor mill
ENHANCING MACHINE EFFICIENCIES Currently, the project is in a ramp-up and optimisation phase, as cost savings and environmental benefits will be realised as the project continues to ramp up
With the global increase in the demand for dissolving pulp, paper and pulp company Sappi’s current business strategy for local growth is focused on the R7.7-billion expansion project at its Saiccor mill in KwaZulu-Natal called Project Vulindela, which is now responsible for more than 60% of its yearly global production capacity for dissolving pulp.
This R7.7-billion investment secures Sappi’s leading position in this growing market, states Sappi South Africa manufacturing, research and development and engineering VP Dr Beverley Sukhdeo.
“Project Vulindlela is aimed at increasing the capacity and global competitiveness of the mill. Not only will the investment increase the mill’s production from 780 000 t/y to 890 000 t/y, but it will also reduce the environmental footprint of the operation through equipment and process upgrades which will employ the best available technology,” she enthuses.
She adds that the expansion includes a new evaporator, recovery boiler, and screening and washing plant, as well as upgrades to the bleach plant and pulp machines, improved recovery circuits and additional magnesium digesters.
In addition to increasing the mills’ production capacity, improving its environmental performance and creating additional future permanent employment for about 120 people, the project has the potential to save the company at least R300-million a year through improved processes.
KwaZulu-Natal will also earn an additional R1-billion a year, directly benefiting the province’s economy.
She adds that Sappi has focussed on enhancing machine efficiencies, digitising its processes, and reducing variable costs through new practices in logistics and procurement.
“This comes in addition to implementing go-to-market strategies, lowering the cost of serving our customers and increases customer satisfaction. We are embracing emerging technologies so that every solution we create through our value streams supports our goal of making our products and processes more sustainable.”
Some of the new technology includes improved washing technology to optimise water and energy efficiency; optimised cooking technology for improved pulp quality control; the application of robotics to facilitate debottlenecking; and shop-floor digitisation for improved commissioning, control and operational efficiency.
Sukhdeo emphasises that the conversion of the calcium cooking line at the Saiccor mill to the more sustainable magnesium bisulphite line reduces the need for coal-based power generation at the mill. “This lowers the carbon footprint, and will additionally facilitate considerable variable cost savings.”
These improvements will cut fossil fuel carbon emissions in half, will reduce sulphur dioxide emissions, and specific water use efficiency will improve by 17%, while water consumption will be reduced by 5%.
Waste-to-landfill from coal ash will also be reduced by 48%.
“All this increases our renewable energy use in line with our commitment to Sustainable Development Goal (SDG) 7: Affordable and Clean Energy, and SDG13: Climate Action. Project Vulindlela is a critical element for Sappi to reach its global commitment of reducing its greenhouse-gas emissions by 18% by 2025.”
Delays and Milestones
The project first commenced in 2018. In 2020, Sappi was forced to declare force majeure on the project owing to Covid-19 stopping construction.
Last year, construction was further delayed by the social unrest in South Africa, as well as ongoing Covid-19 travel restrictions meaning certain essential service providers could not enter the country.
Hot commissioning was completed in the middle of December last year.
Currently, the project is in a ramp-up and optimisation phase, which will take a number of months, as Sukhdeo describes progress to date as “positive”. “Cost savings and environmental benefits of the project will be realised as the project continues to ramp up”.
She highlights one milestone as the installation of the largest sulphite recovery boiler globally. This boiler stands at about 86 m high and has the capacity to process up to 1 500 t/d of dry solids.
Owing to the confined space on site, the pipe bridges were fabricated off site with the pipes installed in the lay down area as modules. These modules were then transported to site, positioned and the pipes welded together successfully.
Tanks were also fabricated off site and brought onto site by specialised motorised transport. Sukhdeo points this out as a significant feat considering the large size of this equipment.
A system was developed to complete the distributed control system factory acceptance tests of certain plant areas remotely owing to the Covid-19 travel restrictions.
Skills Centre
Sappi has demonstrated commitment to improving the skills levels of local communities around their major operations, specifically in engineering maintenance disciplines. The Saiccor Skills Centre was established in 2018 and contains a state-of-the art artisan training facility as well as a basic hand skills option. The Skills Centre identifies local youth for basic vocational training, mathematics and engineering science bridging programmes, as well as phase training for artisans.
“Providing engineering skills to local unemployed youth increases their employability and income generation opportunities, whether with Sappi, local contractors or other businesses that require such services. We hope that through building real capacity in electrical work, welding, civil maintenance and related trades, we can reduce unemployment and provide people with opportunities to succeed,” she concludes.
Comments
Press Office
Announcements
What's On
Subscribe to improve your user experience...
Option 1 (equivalent of R125 a month):
Receive a weekly copy of Creamer Media's Engineering News & Mining Weekly magazine
(print copy for those in South Africa and e-magazine for those outside of South Africa)
Receive daily email newsletters
Access to full search results
Access archive of magazine back copies
Access to Projects in Progress
Access to ONE Research Report of your choice in PDF format
Option 2 (equivalent of R375 a month):
All benefits from Option 1
PLUS
Access to Creamer Media's Research Channel Africa for ALL Research Reports, in PDF format, on various industrial and mining sectors
including Electricity; Water; Energy Transition; Hydrogen; Roads, Rail and Ports; Coal; Gold; Platinum; Battery Metals; etc.
Already a subscriber?
Forgotten your password?
Receive weekly copy of Creamer Media's Engineering News & Mining Weekly magazine (print copy for those in South Africa and e-magazine for those outside of South Africa)
➕
Recieve daily email newsletters
➕
Access to full search results
➕
Access archive of magazine back copies
➕
Access to Projects in Progress
➕
Access to ONE Research Report of your choice in PDF format
RESEARCH CHANNEL AFRICA
R4500 (equivalent of R375 a month)
SUBSCRIBEAll benefits from Option 1
➕
Access to Creamer Media's Research Channel Africa for ALL Research Reports on various industrial and mining sectors, in PDF format, including on:
Electricity
➕
Water
➕
Energy Transition
➕
Hydrogen
➕
Roads, Rail and Ports
➕
Coal
➕
Gold
➕
Platinum
➕
Battery Metals
➕
etc.
Receive all benefits from Option 1 or Option 2 delivered to numerous people at your company
➕
Multiple User names and Passwords for simultaneous log-ins
➕
Intranet integration access to all in your organisation