Safety a major driver for innovation in crushing
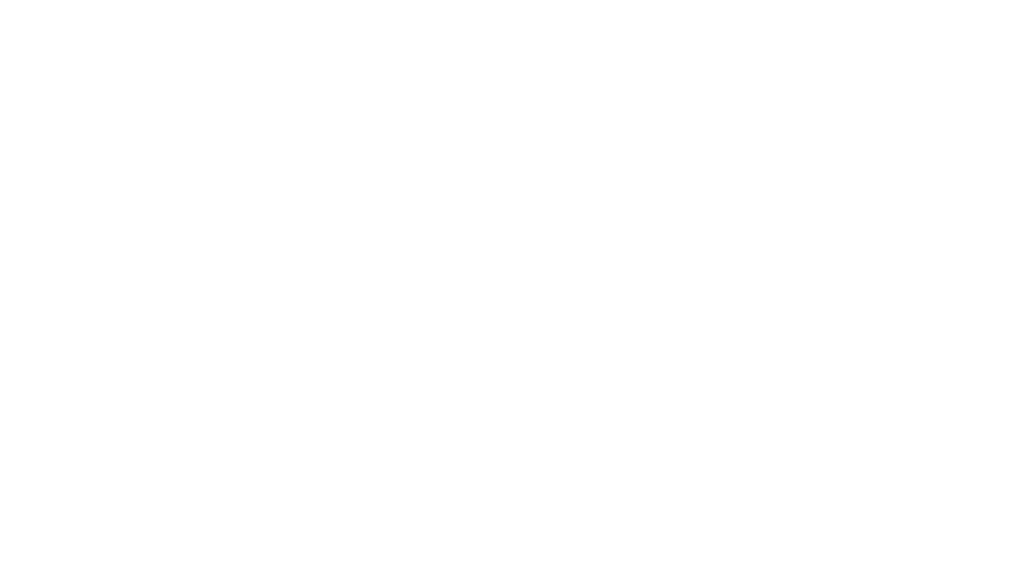
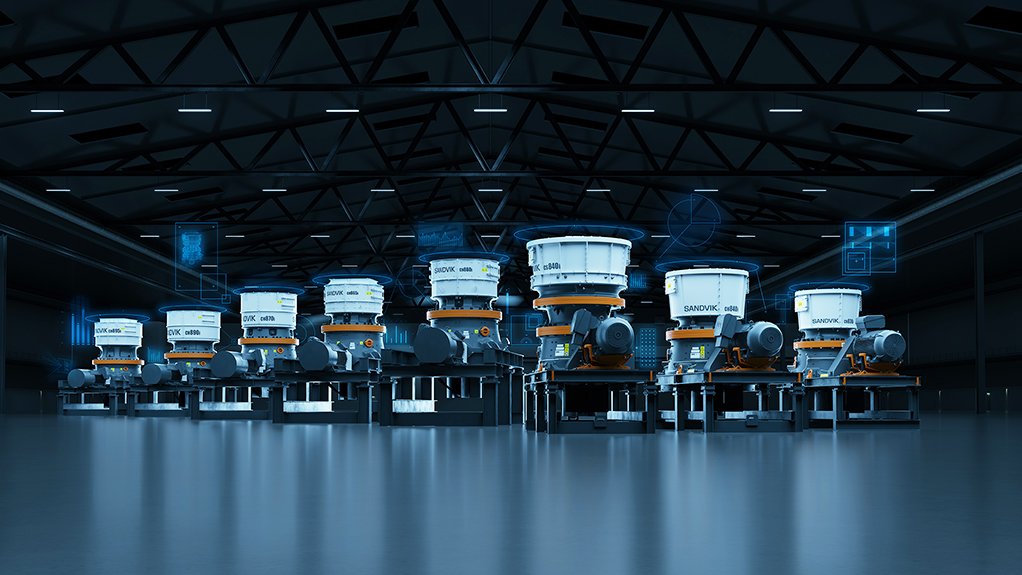
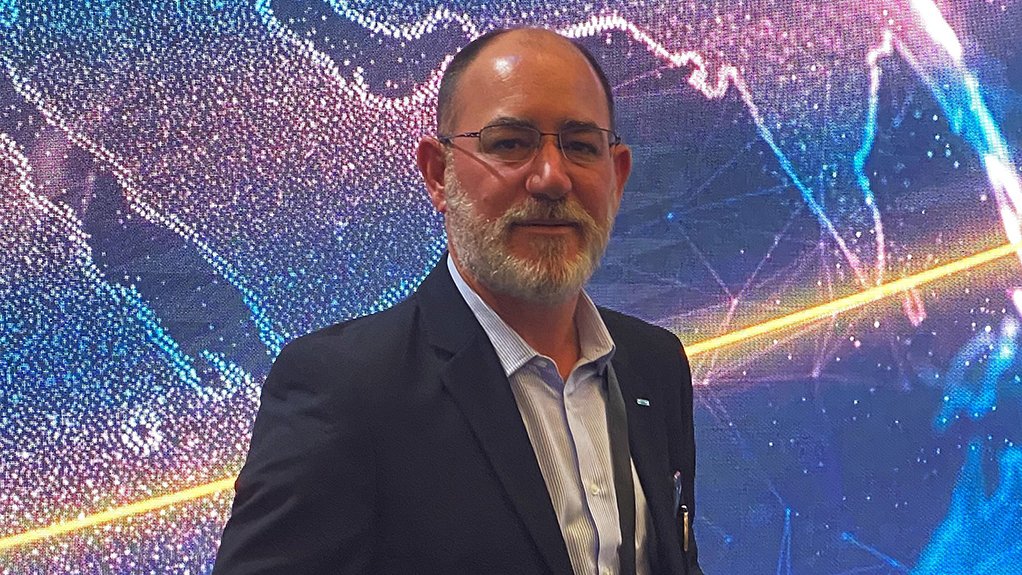
CRUSHING IT The Sandvik 800i series cone crushers come with the new generation automation and connectivity system as standard
GLENN SCHOEMAN The pursuit of zero harm is powerful driving force behind innovation
An increased focus on safety is one of the key driving factors behind innovation and development in original-equipment manufacturer (OEM) Sandvik Mining and Rock Technology’s crushing and screening product ranges.
“We’ve seen an evolution around the safety aspect of technology developments in our crushing equipment. This has been led by strategic dialogue between key stakeholders, mining business drivers and Sandvik executives,” says Sandvik Mining and Rock Technology business line manager for crushing and screening in sub-Saharan Africa Glenn Schoeman.
He says that, increasingly, OEMs are being asked to help provide equipment for mines that can help them maintain zero-harm working environments.
“Zero harm is also a fundamental focus for Sandvik Mining and Rock Technology, whether at a customer’s site, at one of our own facilities or on the road,” Schoeman says.
The company’s latest range of cone crushers – the 800i series – was launched in September last year and features a number of technological advancements that increase not only safety but also operating efficiencies and running costs.
The 800i series comes with the new-generation automation and connectivity system (ACS) as standard, which continually monitors, analyses and optimises the crusher’s performance. It also controls the complete lubrication system to increase uptime and reliability.
The ACS can automatically adjust crusher settings to compensate for crushing chamber wear, thereby ensuring consistent product size. The automation system automatically adapts the crusher’s settings in real time to match feed curve variations, as well as variations in the hardness of the feed material.
The automatic calibration also ensures as much as 4% more uptime, compared with that of manual calibration.
Data from the ACS can be accessed through the MySandvik customer portal.
“The MySandvik platform helps engineers and maintenance staff to know when the machine is due for a service or a liner change; how the machine is performing in terms of temperatures, telemetries and pressures; and what the optimal closed-side-setting is to get the best product yield,” Schoeman explains.
It also provides a means of ordering spares online.
Sandvik Mining and Rock Technology has also been making headway in terms of increasing the availability of spare parts throughout Africa through improved distribution channels and making spares easier to replace.
“There has been a radical shift in how we change out parts, compared with how they were changed out in the past,” Schoeman says.
For example, replacing the main shaft sleeve on a large crusher historically meant that it had to be removed using cutting torches and disc grinders, which could take up to about five hours and required potentially dangerous “hot works”.
By contrast, Sandvik Mining and Rock Technology can now replace a main shaft sleeve on a large crusher using cold hydraulics, where no heating or cutting is required, and it can be achieved in 2.5 hours.
Another safety-related improvement to the company’s crusher technology involves limitations on noise emissions.
“Noise pollution is a concern that customers often raise and, for many of them, reducing noise pollution is a critical requirement for their specific operation, with some looking for as much as a 25% reduction in noise levels.”
Schoeman explains that the company has developed rubber media to line feed hoppers, for example, to reduce the noise from the traditional steel-on-steel designs of the past.
In parallel to increased safety, technological advancements in Sandvik Mining and Rock Technology’s crushing range also translates to improved efficiencies, as well as lowered maintenance requirements and operating costs.
For example, the company has moved towards using spherical helical gears to ensure smoother and more efficient power generation, thereby limiting power wastage from mechanical losses.
Moreover, improved alloys developed by Sandvik Mining and Rock Technology’s special materials division enhance wear times on liners and other replaceable components.
The premium alloy mixes M2, M7, M8 and M9 offer higher resistance to abrasive rock while providing lower resistance to shock and impact. These manganese-based alloys can improve the life of components by as much as 10%.
Schoeman reveals that Sandvik Mining and Rock Technology assisted in extending the replacement period for crusher components at a South African mine from once every three weeks to once every six weeks – a 100% increase in uptime – using the M9 alloy in conjunction with other enhancements.
The M9 alloy has been rolled out to other projects in South Africa, as well as Lesotho.
Despite technological enhancements, Schoeman notes that one of the most effective ways of reducing operating costs is through effective customer operator training, which Sandvik Mining and Rock Technology offers to all customers throughout Africa.
“We’ve invested in various levels of training, depending on customer needs, and can offer it online as well,” he explains, adding that having well-trained operators results in better plant management and minimised hidden costs because of less-than-ideal maintenance.
“We’ve seen efficiencies improve directly as a result of ensuring that the human element is well trained,” Schoeman concludes.
Comments
Press Office
Announcements
What's On
Subscribe to improve your user experience...
Option 1 (equivalent of R125 a month):
Receive a weekly copy of Creamer Media's Engineering News & Mining Weekly magazine
(print copy for those in South Africa and e-magazine for those outside of South Africa)
Receive daily email newsletters
Access to full search results
Access archive of magazine back copies
Access to Projects in Progress
Access to ONE Research Report of your choice in PDF format
Option 2 (equivalent of R375 a month):
All benefits from Option 1
PLUS
Access to Creamer Media's Research Channel Africa for ALL Research Reports, in PDF format, on various industrial and mining sectors
including Electricity; Water; Energy Transition; Hydrogen; Roads, Rail and Ports; Coal; Gold; Platinum; Battery Metals; etc.
Already a subscriber?
Forgotten your password?
Receive weekly copy of Creamer Media's Engineering News & Mining Weekly magazine (print copy for those in South Africa and e-magazine for those outside of South Africa)
➕
Recieve daily email newsletters
➕
Access to full search results
➕
Access archive of magazine back copies
➕
Access to Projects in Progress
➕
Access to ONE Research Report of your choice in PDF format
RESEARCH CHANNEL AFRICA
R4500 (equivalent of R375 a month)
SUBSCRIBEAll benefits from Option 1
➕
Access to Creamer Media's Research Channel Africa for ALL Research Reports on various industrial and mining sectors, in PDF format, including on:
Electricity
➕
Water
➕
Energy Transition
➕
Hydrogen
➕
Roads, Rail and Ports
➕
Coal
➕
Gold
➕
Platinum
➕
Battery Metals
➕
etc.
Receive all benefits from Option 1 or Option 2 delivered to numerous people at your company
➕
Multiple User names and Passwords for simultaneous log-ins
➕
Intranet integration access to all in your organisation