Vibrating screens in copper production process vitally important
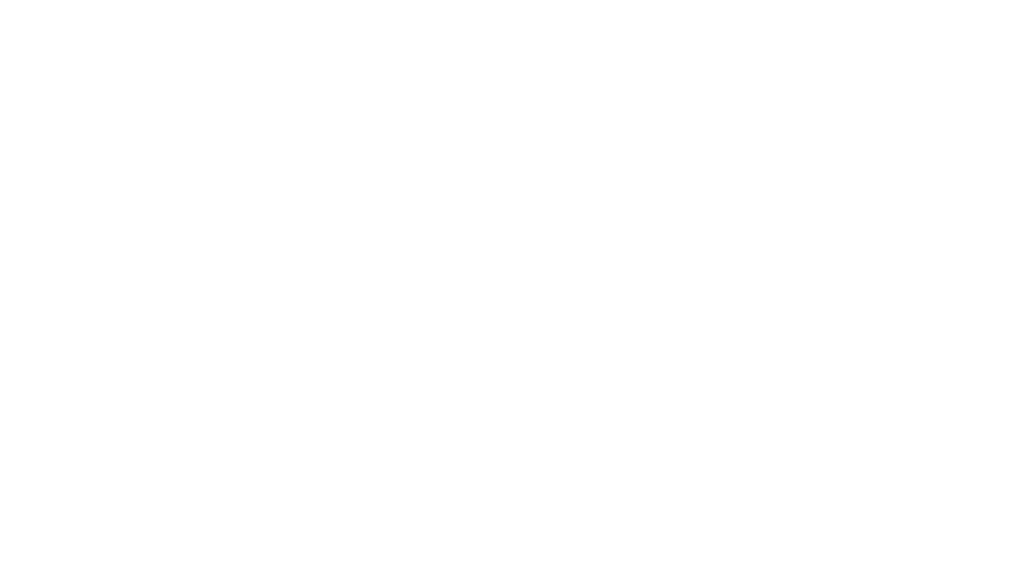
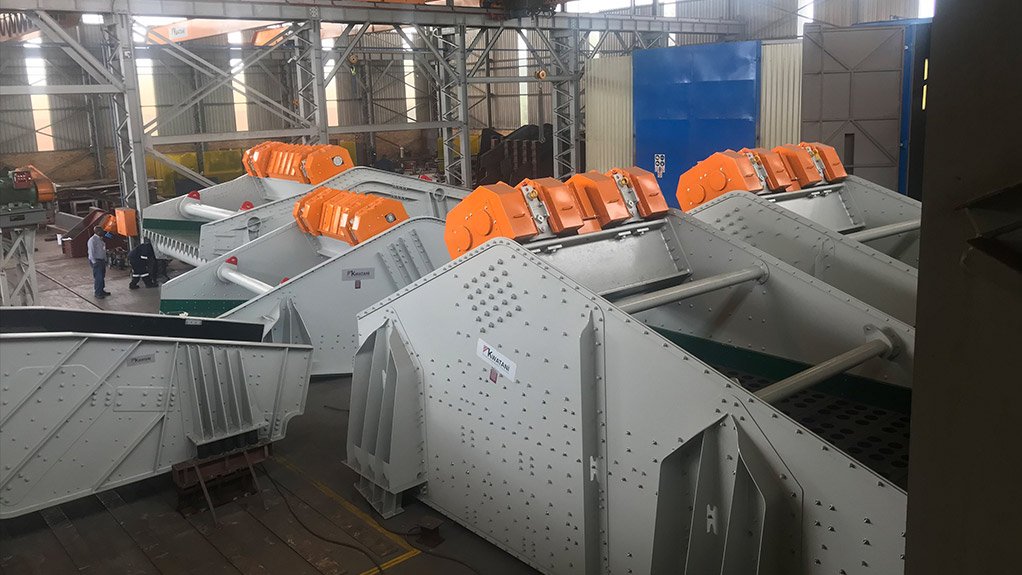
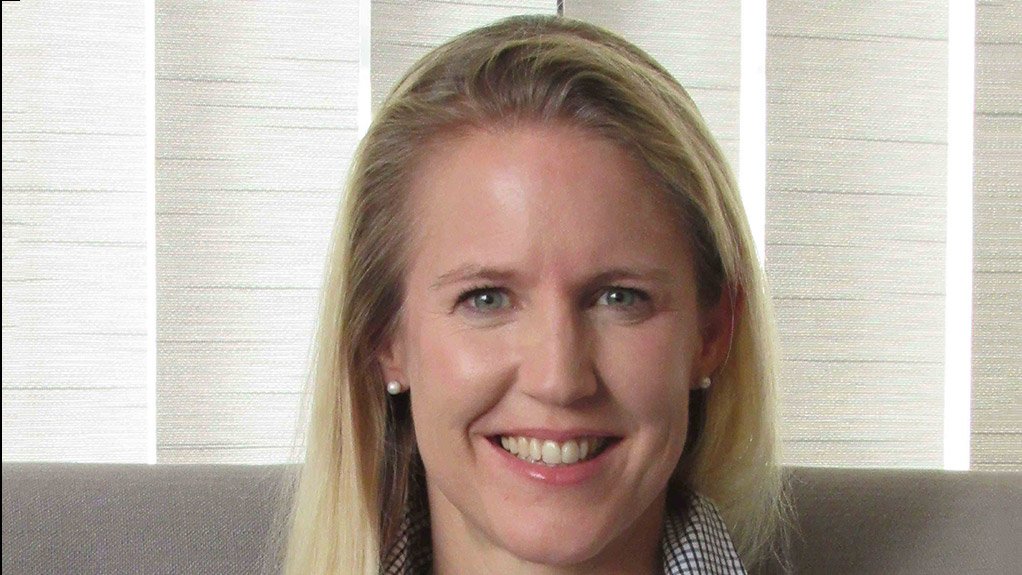
RUGGED AND ROBUST Vibrating screens must be able to handle large tonnages from the crushing or milling process – and efficiently size the material for the downstream process
KIM SCHOEPFLIN Kwatani offers customised vibrating screens and feeders to the mining industry operating in terms of a reference base rather than a standard catalogue
Copper plays an important role in technological advancements, and vibrating- and original-equipment manufacturer and supplier Kwatani is well positioned to take advantage of the growing copper demand.
“Kwatani offers customised vibrating screens and feeders to the mining industry; we don’t have a standard catalogue. Every screen or feeder we develop is customised for mechanical, as well as metallurgical applications,” says Kwatani CEO Kim Schoepflin.
The company also supplies this equipment to copper processing plants, with Schoepflin emphasising that vibrating screens play an important role in the copper production process.
The vibrating screen must be robust – to handle the large tonnages from the crushing or milling process – and efficiently size the material for the downstream process, Schoepflin explains, adding that inefficient screening will result in unnecessary recirculation back to the mill.
Further, modern copper production plants are using large semi-autogenous grinding mills, which, in turn, require large vibrating screens to screen oversized material from the mill discharge thereby protecting pumps, cyclones and pipelines from excessive wear.
The company is building a 4-m-wide vibrating screen for a copper mine in Zambia, which is one of the largest built to date by Kwatani.
The company has established a strong reference base of vibrating screens and feeders used in the copper processing industry. The acquisition of equipment manufacturer Lockers Engineering in 2012 has resulted in both companies having more than 100 vibrating screens and feeders operating across the Copperbelt region.
Trending
“Kwatani always keeps clients’ needs in mind and is committed to assisting them in achieving their objectives by delivering solutions that guarantee a sustainable cost of ownership,” Schoepflin states.
She notes that an evident trend in copper production is “the bigger, the better” – with equipment becoming larger. This is being driven by clients opting to increase tonnage throughput and plant availability.
This trend impacts on the entire supply chain, resulting in a drive for larger vibrating screens. “This means that the technical specifications, robustness and durability requirements of the machine change,” Schoepflin points out.
Further, she explains that copper mines are driving tonnages and that it is absolutely critical that Kwatani’s equipment is reliable and runs continuously, as any stoppages will affect mines’ output.
“The company’s mantra is ‘engineered for tonnage’ and it relates back to our ability to design, manufacture, test, commission and maintain screens of this capacity and ruggedness to ensure consistent tonnage at the lowest cost of ownership.”
She emphasises that it is crucial to fully understand a specific mine’s requirements, including feed types and parameters, as well as any restrictions on the processing plant.
“Our depth of expertise and experience in the field, combined with our substantial facilities and quality standards equip us to custom-design and engineer fit-for purpose machines that handle high tonnages reliably while efficiently meeting clients’ demands.”
Moreover, the company endeavours to develop strong, collaborative working relationships with clients, partnering with them to find feasible solutions for their processing plants. The company also provides tailor-made after-sales services to clients.
“There are some challenges, as most of the copper mines in Africa are remote, but we have qualified teams that can solve and deal with problems,” Schoepflin highlights.
Design
During the development and design phase of its equipment, Kwatani focuses on critical issues such as life span and structural integrity.
“With vibrating equipment, throughout the design process, it is crucial to ensure that the forces are directed through sections of the structure and components that can handle those forces,” Schoepflin stresses.
She further explains that the centrifugal forces generated are directed equally along the designed drive angle to ensure that the vibrating screen runs symmetrically along the longitudinal axis and that the material is carried across the feed deck of the vibrating screen in a steady and even motion, providing effective screening.
“Kwatani designs ensure that the mass of the screen is distributed correctly. The major benefit for clients is that downtime is reduced dramatically and added benefits of the company’s approach are that the screen can be designed for specific applications, as well as accommodate any existing footprint,” she adds.
Plant Upgrades
Existing process plants continue to optimise their performance and, in this regard, Kwatani assists with plant audits by analysing the existing requirements.
“New greenfield copper mines in Africa are rare – most of the existing large-scale mines have been operating for a long time and these mines demand technology to effectively enhance their overall process plant’s efficiencies without incurring massive costs upfront.”
She explains that, when the company retrofits old vibrating equipment, it first analyses the condition of the existing equipment and infrastructure, together with its processing requirements, through consultative processes, as the company must also accommodate the restrictions and parameters of the equipment that needs to be replaced. “The equipment must fit into a client’s existing infrastructure.
“Having successfully retrofitted hundreds of existing vibrating screens across Africa, Kwatani has proven it understands this market requirement,” Schoepflin concludes.
Comments
Press Office
Announcements
What's On
Subscribe to improve your user experience...
Option 1 (equivalent of R125 a month):
Receive a weekly copy of Creamer Media's Engineering News & Mining Weekly magazine
(print copy for those in South Africa and e-magazine for those outside of South Africa)
Receive daily email newsletters
Access to full search results
Access archive of magazine back copies
Access to Projects in Progress
Access to ONE Research Report of your choice in PDF format
Option 2 (equivalent of R375 a month):
All benefits from Option 1
PLUS
Access to Creamer Media's Research Channel Africa for ALL Research Reports, in PDF format, on various industrial and mining sectors
including Electricity; Water; Energy Transition; Hydrogen; Roads, Rail and Ports; Coal; Gold; Platinum; Battery Metals; etc.
Already a subscriber?
Forgotten your password?
Receive weekly copy of Creamer Media's Engineering News & Mining Weekly magazine (print copy for those in South Africa and e-magazine for those outside of South Africa)
➕
Recieve daily email newsletters
➕
Access to full search results
➕
Access archive of magazine back copies
➕
Access to Projects in Progress
➕
Access to ONE Research Report of your choice in PDF format
RESEARCH CHANNEL AFRICA
R4500 (equivalent of R375 a month)
SUBSCRIBEAll benefits from Option 1
➕
Access to Creamer Media's Research Channel Africa for ALL Research Reports on various industrial and mining sectors, in PDF format, including on:
Electricity
➕
Water
➕
Energy Transition
➕
Hydrogen
➕
Roads, Rail and Ports
➕
Coal
➕
Gold
➕
Platinum
➕
Battery Metals
➕
etc.
Receive all benefits from Option 1 or Option 2 delivered to numerous people at your company
➕
Multiple User names and Passwords for simultaneous log-ins
➕
Intranet integration access to all in your organisation