African Rainbow Minerals crowns grade as king, declares war on reef waste on PGMs front
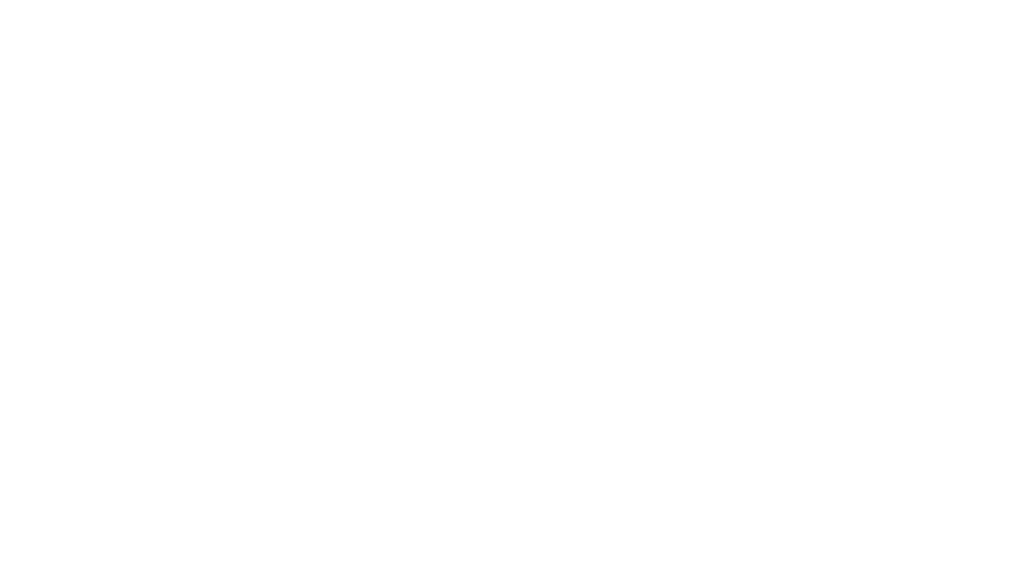
Master Drilling CEO Danie Pretorius interviewed by Mining Weekly's Martin Creamer. Video: Darlene Creamer.
JOHANNESBURG (miningweekly.com) – Two acronyms were drummed into new mining entrants in the days of yore – GIK and WAR.
GIK is short for ‘grade is king’ and at the opposite end of the scale, everyone was urged to declare war on WAR, which is short for ‘waste as reef’.
Putting ‘grade is king’ on the highest of pedestals can elevate mining operations to the highest of performance levels – and if war is not declared on WAR, waste as reef can kill a mine stone dead, particularly in the current low-priced environment.
Interestingly, one major company that is spotlighting GIK with the brightest of bright lights on its platinum group metals (PGMs) firmament is the Johannesburg Stock Exchange-listed diversified mining company African Rainbow Minerals (ARM), headed by executive chairperson Dr Patrice Motsepe.
To drive GIK with all the force at its disposal and significantly flatten WAR in the process, ARM is implementing innovative reef boring technology developed with its two partners, Herrenknecht, a German company known for its excellence in designing and manufacturing tunnel boring machines worldwide, and Master Drilling, the Johannesburg Stock Exchange-listed South African company that specialises in reef boring solutions.
Three overlapping cutter heads in one frame innovated by Herrenknecht provide three times the volume of rock per metre plus consistent fragmentation, which simplifies and reduces downstream materials handling infrastructure requirements.
Moreover, the rectangular cut profile provided by Master Drilling maximises upper group two (UG2) extraction, minimises dilution and helps to achieve the highest grade possible.
Both of the inventive concepts crown grade as king and knock dilution into a cocked hat, with ARM's Bokoni PGMs mine seen as the ideal location for implementation. High PGM grades of 9 g/t are contained within Bokoni’s 70 cm-wide UG2 reef.
“We’re implementing it as we stand here today, and hopefully in six months, we can give you an update on that,” was the comment of an upbeat Mike Schmidt, ARM executive of growth and strategic development in the executive chairperson’s office, in response to Mining Weekly during the company’s latest results presentation.
ARM explored various mining methods and ultimately chose reef boring as the best solution in that it not only optimises GIK and declares war on WAR, but shows convincing promise of achieving the same productivity, safety and cost performance as a mechanised, low profile board-and-pillar operation in a narrow tabular orebody.
Bokoni PGM mine’s UG2 is being grasped as the opportunity to roll out what is perceived to be a paradigm shifter that will take people out of the stopes, open the way for explosion-free mining, lift grade sky high and even shrink tailings requirements.
Complete remote operation will mean that there will be no need for employees to be at the rockface, which offers major safety advantages.
The reef boring method has the potential to deliver PGM grades of up to 60% better than with a conventional mine by maximising the UG2 reef extraction while minimising the inclusion of the low PGM content waste from the hanging wall and footwall.
But beyond just improving grades, this technology is also well suited for mechanisation and then ultimately to automation, which can lead to further improvements in productivity and lower mining cost per ton.
When the higher PGM grades are combined with the lower cost per ton, a major improvement in cost per PGM ounce comes forth.
The key challenge, however, is obtaining necessary monthly production volumes, and ARM will be verifying achieving of essential production targets as it deploys this game-changer at Bokoni.
In addition, the high grade of the reef mining justifies the cost of placing backfill underground into previously mined stopes, which increases the extraction percentage of the orebody to greater than 90%, extends the life-of-mine, improves the stoping to development ratio, which then enhances the run-of-mine grades, and reduces the amount of mining development required.
In turn, the ability to place tailings underground, combined with more selective mining and minimised waste dilution, shrinks the size of the tailings storage facility (TSF) required on surface.
This not only positively impacts the environment, but also reduces both the operating and capital costs associated with running the TSF.
Numerous full-scale cutting tests for both concepts using actual production cutter heads have been carried out.
“It’s not ARM alone, albeit our preferred technology. We've learned from the industry and from failures, and one of the areas is that you can't try and put machines into a conventional layout. That doesn’t work.
“You have to change your mining layout to suit your equipment and we've done it.
“We've also taken the equipment from the preferred suppliers and manufactured the first set of equipment, and that is, as we talk, going underground on trials, to see where it goes.
“So, we’re still taking a conservative approach, and to see if we can yield the results we want.
“With WAR in this environment, companies die, not people, because you can't get it out. It's vitally important for us to get our industry changed at a time when technology has changed, automation process has changed, the learnings and certainly IT and software have arrived where we can do predictive maintenance.
“So, all these benefits of software, combined with a layout, combined with new mining technology, gives us what we're looking for.
“But the most important thing is that this technology allows you to do explosiveless mining,” Schmidt emphasised.
“I grew up in the industry in gold and platinum mining, and we know that the platinum and narrow tabular gold seams in South Africa are, in general, 60 cm and less, and the containment within them varies between 6 g/t and 12 g/t.
“As a conventional industry, we've been mining at 120 cm to 150 cm, which is 100% to 120% dilution, and the industry yields between 3 g/t and 4 g/t.
“For decades, the industry, including Comro, researched how to get people out of the face, improve grade, productivity, efficiencies, and to achieve that in a way that’s cost-effective. But the many attempts over the last 20 years have not really been successful from a commercial point of view.
“Now, the intention is to achieve all that and to mine under a metre, which immediately gives all those benefits,” said Schmidt.
During its presentation of results earlier this year, Master Drilling displayed the cutter head it is developing for ARM and stated: ”Initiatives like this could significantly impact operations, doubling grade, halving the material that you move…and it allows you to work continuously and remotely.”
Master Drilling uses a novel cutter head layout where the cutter wheels are perpendicular to the direction of drilling. There are two counter rotating cutting wheels, with a central vacuum suction to remove cuttings to the reef drive.
When Mining Weekly asked Master Drilling CEO Danie Pretorius to provide more insight, this was his response: “This is actually a joint venture between ourselves and ARM and I think the challenge goes back way back when the miners realised the need to get people out of the stoping area.
“It's a highly dangerous area for people to operate in and I think there were a number of tests also done in the platinum industry, way back at Lonmin, to do mechanical cutting, which was never really successful.
“I think the key performance indicator was always to try and cut at least close to 15 000 t per month to 20 000 t per month, but I think the maximum that the mechanical cutting companies achieved was around about 2 000 t per month, which is way below the set target, and we've embarked on this project with ARM and together, designed the machine and we’re probably now in a position where we can probably roll it out in the next year, obviously subject to a site.” (Also watch response to second question on attached Creamer Media video.)
HAND-HELD JACKHAMMERS
Narrow tabular orebodies in South Africa have traditionally been mined using hand-held jackhammers and scraper winches to clean stope panels and gullies.
Few platinum and gold mines have been able to make the narrow stoping width viable by moving to mechanisation. As machinery for narrow tabular orebodies had to be scaled down to fit into the narrow confines of a metre and less stoping widths, the equipment had to be specially manufactured, which elevated cost to excessive levels.
Herrenknecht has proposed quite an innovative solution to address the cross sectional challenge by using three overlapping cut heads in one frame, while Master Drilling focused on attaining a rectangular cut profile instead of a circular cut profile, which maximises reef extraction and minimises the waste dilution.
Both approaches are aimed at increasing the production and reducing waste, in close associated with ARM, which not only mines and beneficiates PGMs, but does the same with iron-ore, manganese ore, chrome ore, nickel and coal and also has a strategic investment in gold through the Johannesburg Stock Exchange-listed Harmony Gold.
Comments
Announcements
What's On
Subscribe to improve your user experience...
Option 1 (equivalent of R125 a month):
Receive a weekly copy of Creamer Media's Engineering News & Mining Weekly magazine
(print copy for those in South Africa and e-magazine for those outside of South Africa)
Receive daily email newsletters
Access to full search results
Access archive of magazine back copies
Access to Projects in Progress
Access to ONE Research Report of your choice in PDF format
Option 2 (equivalent of R375 a month):
All benefits from Option 1
PLUS
Access to Creamer Media's Research Channel Africa for ALL Research Reports, in PDF format, on various industrial and mining sectors
including Electricity; Water; Energy Transition; Hydrogen; Roads, Rail and Ports; Coal; Gold; Platinum; Battery Metals; etc.
Already a subscriber?
Forgotten your password?
Receive weekly copy of Creamer Media's Engineering News & Mining Weekly magazine (print copy for those in South Africa and e-magazine for those outside of South Africa)
➕
Recieve daily email newsletters
➕
Access to full search results
➕
Access archive of magazine back copies
➕
Access to Projects in Progress
➕
Access to ONE Research Report of your choice in PDF format
RESEARCH CHANNEL AFRICA
R4500 (equivalent of R375 a month)
SUBSCRIBEAll benefits from Option 1
➕
Access to Creamer Media's Research Channel Africa for ALL Research Reports on various industrial and mining sectors, in PDF format, including on:
Electricity
➕
Water
➕
Energy Transition
➕
Hydrogen
➕
Roads, Rail and Ports
➕
Coal
➕
Gold
➕
Platinum
➕
Battery Metals
➕
etc.
Receive all benefits from Option 1 or Option 2 delivered to numerous people at your company
➕
Multiple User names and Passwords for simultaneous log-ins
➕
Intranet integration access to all in your organisation