Automated tech implemented at iron-ore project
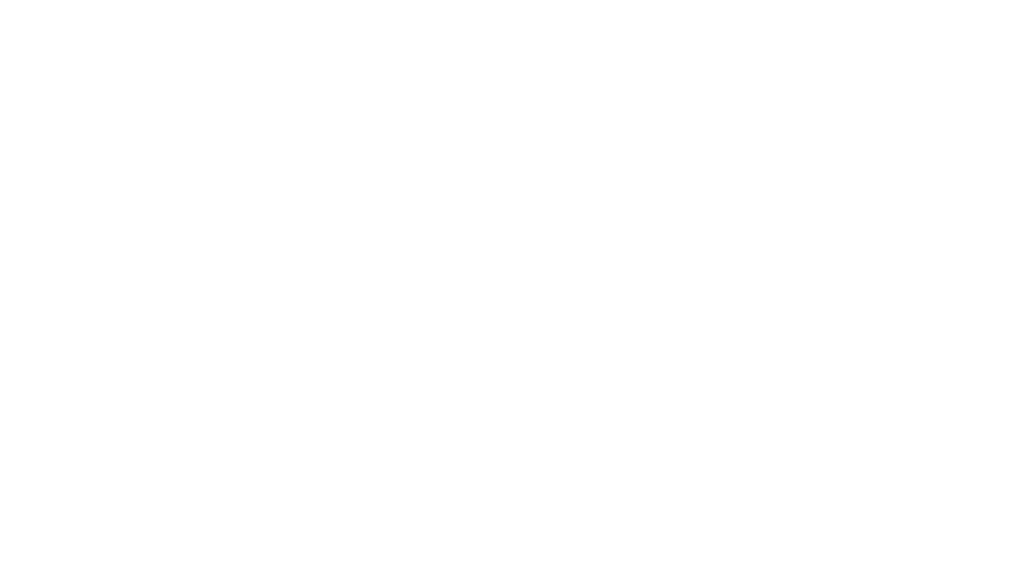
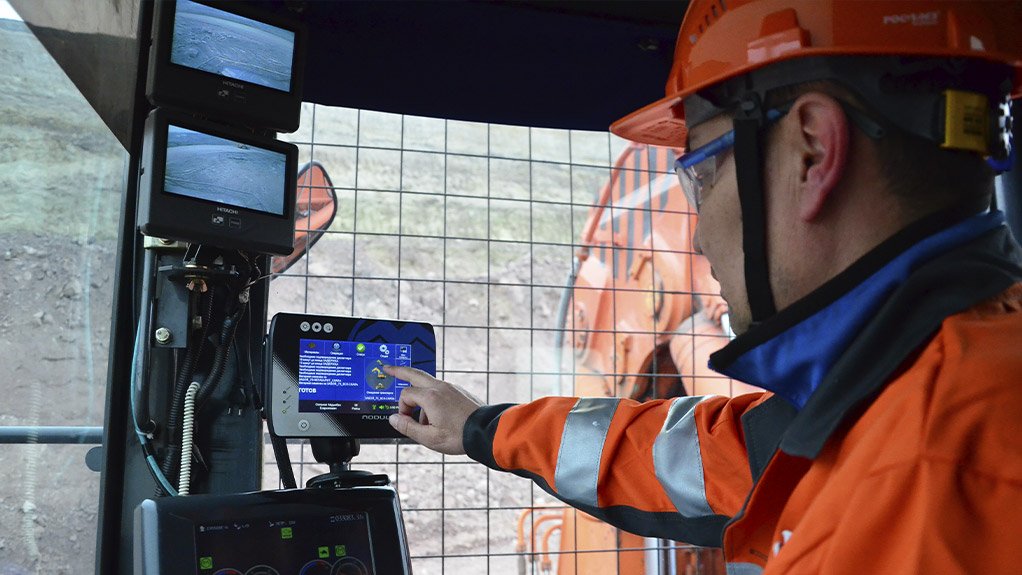

SMART MINE The Kacharsky site is now home to a range of intelligent solutions that help improve efficiency
AIR-SUPPORTED WORKSHOP The new workshop for large dump trucks can be easily relocated if needs be
The trial of the Smart Mine technology project at iron-ore mining company Sokolov-Sarbai Mining Production Association’s (SSGPO’s) Kacharsky opencast site has been successful.
SSGPO, a subsidiary of international metals and mining conglomerate Eurasian Resources Group (ERG), says that it plans to roll out similar systems at several of the other opencast iron-ore mines that it operates, namely, the Kurzhunkulsky, Sokolovsky and Sarbaisky mines.
The introduction of Smart Mine technology is aimed at increasing the productivity of SSGPO’s Kacharsky openpit iron-ore mine by 40%.
In addition, SSGPO says that the technology will enable a reduction in production costs by more than $2.5-million, while significantly improving product quality.
“The ultimate goal of the project is to give SSGPO a competitive edge on the iron-ore market,” the company says.
ERG is one of the first companies in Kazakhstan to develop its own digital modernisation plan and is a major contributor to the country’s economy, having operated in the region for 25 years.
Project Implementation Stages
The Kacharsky site was selected for the testing and pilot implementation of the automated system because the mine accounts for more than half of the total ore production at SSGPO.
The implementation of the Smart Mine initiative at the Kacharsky site comprises several stages, with the first stage, integrated planning, involving the introduction of a module named ‘Mine Designer: Geological and Mine Surveying Platform’.
“This is a software package covering [several] operations, from mine modelling to the preparation of a detailed daily mining plan,” SSGPO explains.
An automated system for the management of moving equipment – a modular dispatching system – is currently being introduced to provide real-time information on the progress of mining operations without the need for manual data input nor human involvement.
Additionally, it also provides data for the analysis of actual performance and the development of appropriate action plans.
The company says the next stage will involve introducing ‘state-of-the-art’ pellet production technologies.
Full Transparency and Control
The Smart Mine implementation is aimed at accomplishing the key operational task of ensuring that all operating conditions at the mine and its performance are fully transparent. This assists in ensuring that the enterprise becomes more cost-effective, SSGPO adds.
To achieve this goal, the iron-ore mining cycle has been fully integrated, using several Industry 4.0 elements, such as a modular automated production management system, a geographic information system (GIS) and an enterprise resource planning (ERP) system.
The integration of these three systems has enabled the modelling of production processes and, moreover, the situation in the mine is monitored by computers, which are able to make necessary adjustments and select the optimal allocation of moving equipment.
The location of vehicles is monitored using a satellite-based vehicle tracking system, and information on the performance and condition of equipment, as well as the quality of ore mined and transported, is transmitted through a reliable wireless data network set up in the mine and at adjacent production sites.
Diagnostic assessments of the operability of dump trucks, excavators and other moving equipment are performed remotely.
Optimal vehicle routes are calculated by a special software programme every time a vehicle arrives to load or unload ore.
The automation of on-site logistics and the use of a machine algorithm for the dispatching of all mining equipment enables SSGPO to use its resources more efficiently. Predictive maintenance and the monitoring of the conditions of systems make it possible to collect data on equipment performance in real time.
“The integration of the modular automated production management system, the GIS and the ERP systems, means that the information on the use of equipment is complete and reliable,” SSGPO claims.
As a result, the company says that its equipment failure rate has been reduced to a minimum, and unscheduled downtime has decreased, while the operating speed of equipment has increased. SSGPO says that this has helped to improve equipment productivity by 10%, while reducing costs and enabling more efficient and informed decisions on further investments in the modernisation of the mine fleet.
Dispatchers play a central role in the newly established system, as their responsibilities include managing the production process, analysing the situation and selecting the workstreams that serve as a basis for planning the operation of equipment.
According to estimates by SSGPO’s economists, the implementation of the Smart Mine initiative will help to achieve significant financial benefits and is based on the expectation that the initiative will translate into reduced equipment downtime, increased ore production, and an overall improvement in operational and technical discipline.
Comments
Announcements
What's On
Subscribe to improve your user experience...
Option 1 (equivalent of R125 a month):
Receive a weekly copy of Creamer Media's Engineering News & Mining Weekly magazine
(print copy for those in South Africa and e-magazine for those outside of South Africa)
Receive daily email newsletters
Access to full search results
Access archive of magazine back copies
Access to Projects in Progress
Access to ONE Research Report of your choice in PDF format
Option 2 (equivalent of R375 a month):
All benefits from Option 1
PLUS
Access to Creamer Media's Research Channel Africa for ALL Research Reports, in PDF format, on various industrial and mining sectors
including Electricity; Water; Energy Transition; Hydrogen; Roads, Rail and Ports; Coal; Gold; Platinum; Battery Metals; etc.
Already a subscriber?
Forgotten your password?
Receive weekly copy of Creamer Media's Engineering News & Mining Weekly magazine (print copy for those in South Africa and e-magazine for those outside of South Africa)
➕
Recieve daily email newsletters
➕
Access to full search results
➕
Access archive of magazine back copies
➕
Access to Projects in Progress
➕
Access to ONE Research Report of your choice in PDF format
RESEARCH CHANNEL AFRICA
R4500 (equivalent of R375 a month)
SUBSCRIBEAll benefits from Option 1
➕
Access to Creamer Media's Research Channel Africa for ALL Research Reports on various industrial and mining sectors, in PDF format, including on:
Electricity
➕
Water
➕
Energy Transition
➕
Hydrogen
➕
Roads, Rail and Ports
➕
Coal
➕
Gold
➕
Platinum
➕
Battery Metals
➕
etc.
Receive all benefits from Option 1 or Option 2 delivered to numerous people at your company
➕
Multiple User names and Passwords for simultaneous log-ins
➕
Intranet integration access to all in your organisation