Blasting and drilling increasingly automated
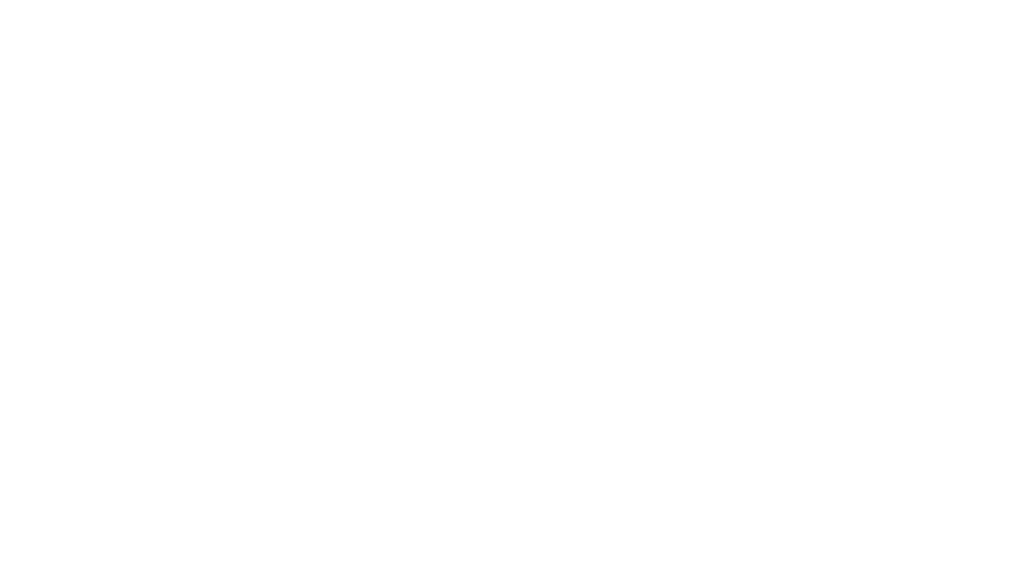
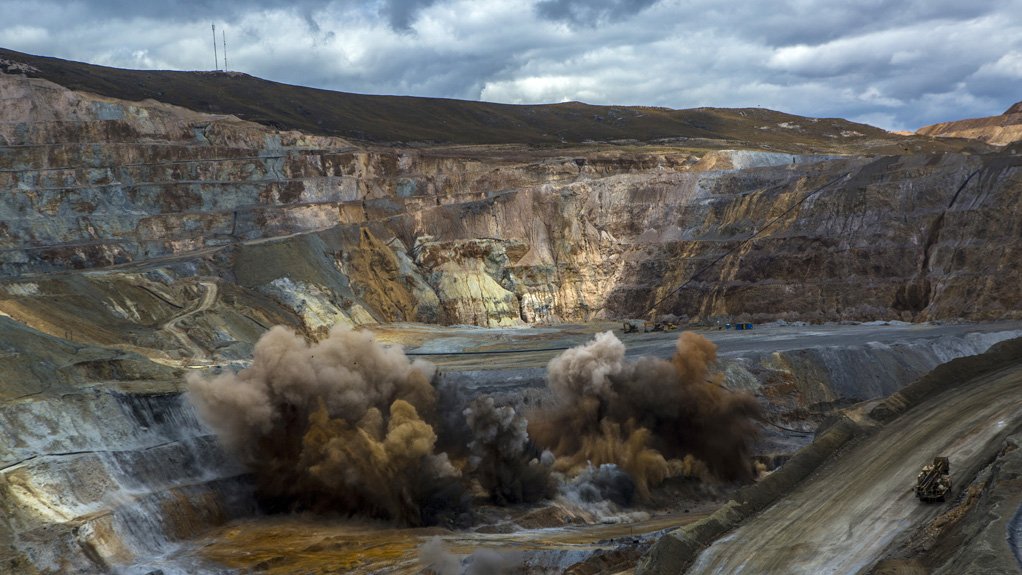
NEW ERA iRing aims to demystify blasting and drilling operations through its software solutions, making them safer and more efficient
Photo by Bloomberg
Ongoing developments to underground mining solutions provider iRing’s mine planning software suite are increasingly automating blasting and drilling operations, providing increased accuracy and safety in hazardous mining environments.
iRing software development manager Christopher Preston notes that, in the past, drilling and blasting have been treated as something of a misunderstood “black art”. Drawing on a vast range of knowledge that includes detonation physics, rock mechanics and stress analysis, mechanisms of failure, particle-size analysis, operations research and materials handling, as well as a strong knowledge of economics in relation to material extraction, iRing is, however, determined to demystify these operations through its software solutions.
The Canadian company’s Aegis Designer and Aegis Analyzer have been available globally since 2014 and are being used by seven mines in South Africa, as well as five mines in other parts of Africa. Preston highlights that ongoing developments to the software suite aim to streamline mine blast design and eliminate human error, allowing for an accurate one-off event that is not preceded by a costly – and potentially dangerous – experimental phase. As blasting introduces seismic waves into the host rock, understanding wave motion dynamics has also been integral to preclude the effects of environmental hazards and human response.
“Mine blasting operation costs can now be managed through detailed analysis that aims to expose bad practices and substitute these with best practices. Drilling accuracy is key to this effort – gone are the days when explosives are seen as an acceptable solution to rectify a badly drilled hole,” explains Preston.
Future Focused
iRing envisions that, in the near future, orebodies will extend deeper into the earth’s crust and that in-ground stresses will be of such magnitude that blasting operations will become precision operations.
Preston outlines that orebodies will be delineated not only by diamond drill core systems but also satellite-based systems, which can distinguish between high-stress ore zones at depth and those just below the surface. Drill holes through the ore will provide access for neutron activation analysis methods that quantify grade without assaying.
“iRing is moving towards the development of an advanced product that could take the wireframe of the orebody and, with one click of a button, define the stope size and volume, considering in-ground stresses in laying out the drills that access the ore.”
Ring sections will be designed automatically, based on drilling equipment and the most suitable explosive, as well as the timing and sequencing required to reduce blasting stresses that will add to the ever-present in-ground stresses. The complete pattern design will be downloaded to drills that are allocated to drilling blast holes – a feature already provided with both Aegis products.
“Recovery will be improved and dilution eliminated. The complete blasting operation itself will function as a well-tuned primary crusher that will finally eliminate the need for an expensive underground crushing level. Ore may be hydraulically pumped to the surface instead of being skipped and safety would remain paramount, with many autonomous equipment components replacing labour in hazardous environments,” says Preston.
Developmental Steps
Preston highlights that the quest for this “state-of-the-art mine design solution” involves the evolution of a multiplicity of software programs to constantly improve processes on various fronts, such as ore delineation, stope design, development access design, drilling explosives loading, timing and sequencing, blasting and mucking, results analysis and the development of new baselines.
“The objective is to provide many of these tasks in one complete software package to reduce the overall number of packages required from other manufacturers – especially from the aspect of underground blasting design.”
Providing a stepping stone for this solution is iRing’s Aegis software, which has been specifically designed to allow for many “what-if” scenarios to be tested and applied to complex orebodies, in seconds, to find the most suitable ring layouts that are optimised for the highest recovery at the lowest cost.
Preston explains that Aegis Designer is used in mines that are content with existing procedures that have enabled them to mine safely and economically, even during extreme downturns in global supply and demand. Aegis Analyzer, however, is used on the premise that current blasting operations can be improved through careful control of the application of explosive energy distributed throughout an orebody to provide maximum recovery with absolute minimum dilution. The software’s primary objective is to recover all the ore and leave behind only the support rock.
The latest addition to the Aegis Analyzer – available since April – is a scenario-based costing module that enables mine planning engineers to accurately cost an entire blast. This facilitates cost comparisons between different products, patterns and methods.
iRing provides consulting services for its distributors and mining corporations, not only in support of its products but also for additional advanced knowledge in blast design, explosives end-use and application, rock mechanics and the physics of the detonation process. The company has also assisted in customising the iRing Aegis interface for a variety of mining operations.
Comments
Announcements
What's On
Subscribe to improve your user experience...
Option 1 (equivalent of R125 a month):
Receive a weekly copy of Creamer Media's Engineering News & Mining Weekly magazine
(print copy for those in South Africa and e-magazine for those outside of South Africa)
Receive daily email newsletters
Access to full search results
Access archive of magazine back copies
Access to Projects in Progress
Access to ONE Research Report of your choice in PDF format
Option 2 (equivalent of R375 a month):
All benefits from Option 1
PLUS
Access to Creamer Media's Research Channel Africa for ALL Research Reports, in PDF format, on various industrial and mining sectors
including Electricity; Water; Energy Transition; Hydrogen; Roads, Rail and Ports; Coal; Gold; Platinum; Battery Metals; etc.
Already a subscriber?
Forgotten your password?
Receive weekly copy of Creamer Media's Engineering News & Mining Weekly magazine (print copy for those in South Africa and e-magazine for those outside of South Africa)
➕
Recieve daily email newsletters
➕
Access to full search results
➕
Access archive of magazine back copies
➕
Access to Projects in Progress
➕
Access to ONE Research Report of your choice in PDF format
RESEARCH CHANNEL AFRICA
R4500 (equivalent of R375 a month)
SUBSCRIBEAll benefits from Option 1
➕
Access to Creamer Media's Research Channel Africa for ALL Research Reports on various industrial and mining sectors, in PDF format, including on:
Electricity
➕
Water
➕
Energy Transition
➕
Hydrogen
➕
Roads, Rail and Ports
➕
Coal
➕
Gold
➕
Platinum
➕
Battery Metals
➕
etc.
Receive all benefits from Option 1 or Option 2 delivered to numerous people at your company
➕
Multiple User names and Passwords for simultaneous log-ins
➕
Intranet integration access to all in your organisation