Case studies prove success of energy efficiency project
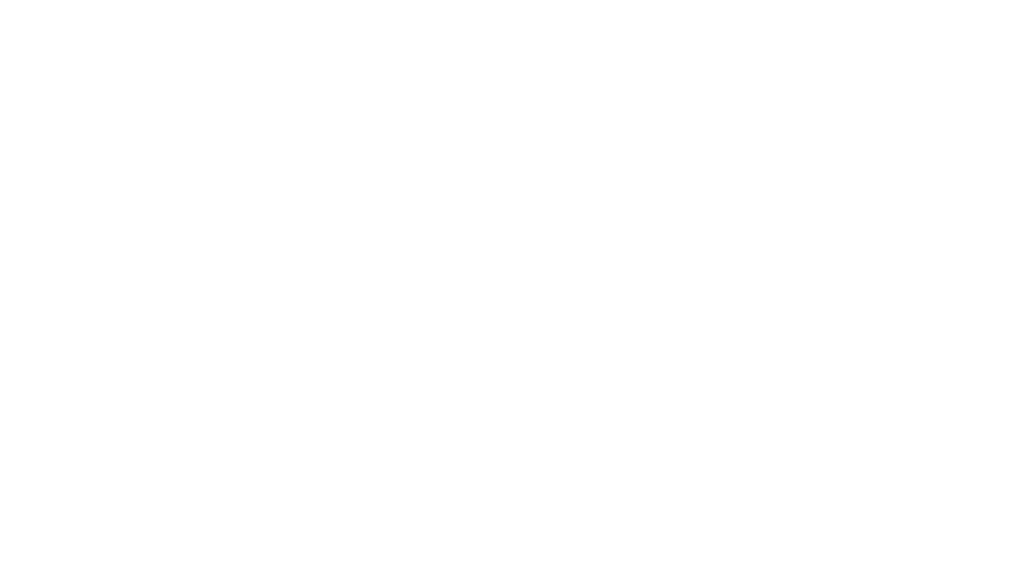
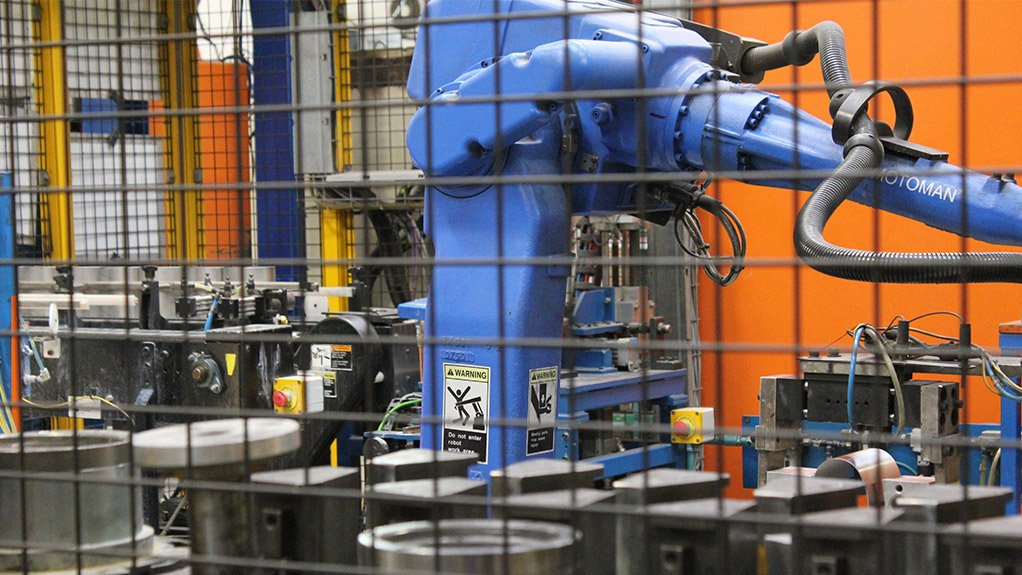
MANUFACTURING EFFICIENCY Tenneco PE implemented an energy management system that allowed for energy savings of R2-million within the first year of implementation
Having been implemented in South Africa in 2010, the Industrial Energy Efficiency (IEE) project, facilitated by the National Cleaner Production Centre South Africa, the Council for Scientific and Industrial Research, the Department of Trade and Industry and the Department of Energy, can now demonstrate its successes and findings through numerous case studies, states IEE national project manager Alfred Hartzenburg.
The IEE project is a flagship programme within the United Nations Industrial Development Organisation and is focused on transforming South Africa’s energy-use patterns.
Its central mandate is to demonstrate the positive impact of energy management on local businesses as a means of reducing carbon dioxide (CO2) emissions, as well as the effectiveness and financial impact of in-plant energy management.
Hartzenburg highlights that different cases have shown different levels of energy savings; however, even the few companies that have not achieved any CO2 emissions savings can serve as case studies to provide future guidance.
He notes that the energy savings that have been reported in the case studies all comply with the International Performance Measurement and Verification Protocol, which allows for studies to be compared.
In many regards, standardisation is integral to the success of the IEE and in the process of improving energy efficiency, standardisation and process management have helped to enhance general operations and the quality thereof, he explains.
The ISO 9001 system used by the programme is based on the plan, do, check, act, or PDCA, method, ensuring the systematic implementation of energy efficiency, says Hartzenburg.
Further, he adds that the IEE project has had positive effects on other aspects of companies, such as product quality, as the project instils a systematic approach to analysing and optimising energy systems and processes in the plant. Subsequently, the operations of some of the biggest sections in a company are standardised and driven to higher levels of general performance, he explains.
Broad Success
Hartzenburg cites the partnership with automotive components manufacturer Tenneco Automotive Holdings as an example of the IEE project’s success in energy-use reduction, which simultaneously provided Tenneco with the resources it needed to improve the quality of its products.
After US holding company Tenneco had instructed Tenneco Port Elizabeth (PE) to improve its energy efficiency, the matter was discussed with the IEE in August 2012.
Tenneco PE subsequently implemented an energy management system that allowed for energy savings of R2-million within the first year of implementation – this enabled Tenneco to buy a new compressor, Hartzenburg enthuses.
Further, Tenneco was the first automotive original-equipment manufacturer in South Africa to obtain an ISO 50001 accreditation, after which another five companies followed suit. In addition, Tenneco PE GM Justin Botha has been selected to champion the task of bringing ISO 50001 standards to Tenneco’s global network.
Hartzenburg elaborates that ISO 50001 certification signals a plant’s commitment to improve its energy management performance and in doing so, its contribution to a sustainable environment. This certification also confers invaluable recognition in international trade.
Other IEE project successes include the project’s involvement with speciality chemicals and sustainable technologies company Johnson Matthey and local steel producer ArcelorMittal South Africa (AMSA).
Hartzenburg highlights that Johnson Matthey is among the small group of nine companies in South Africa that have been ISO 50001-certified and, having embarked on an energy-management programme with the project in 2013, Johnson Matthey saved 7.9-million kilowatt hours in the first year of implementation.
Meanwhile, AMSA’s Saldanha Bay plant was at risk of closure in 2010, with 538 people at risk of losing their jobs. However, the energy savings of 80-million kilowatt hours that amounted to saving R60-million in the first year of implementing an energy-management system rescued the plant from closure.
Hartzenburg enthuses that AMSA’s only significant capital investment was a R500 000 purchase of a voltage optimiser system for the main building.
To date, AMSA’s energy-management system has saved R272-million and is currently a model that the company intends to implement at its Van Der Bijl Park steelworks plant.
Pioneering Energy Efficiency
Hartzenburg avers that the IEE has pioneered the development of an energy-services sector in South Africa, creating a new career option for engineers.
When the IEE project began in 2010, there were about five energy-service experts in the Western Cape and seven dotted elsewhere in South Africa. Currently, there are 35 energy- service experts in the Western Cape, with another 85 employed in the other provinces.
Hartzenburg further enthuses that the IEE has helped promote the growth of other projects including the Private Sector Energy Efficiency project.
He explains that, while discussions about energy efficiency focus on component optimisation, the IEE has also introduced a gradual shift towards optimising operations.
“Therefore, instead of constantly pursuing better technology, we promoted the use of existing technology in a more efficient manner.”
The energy-services sector is one that can sustain its recent success following the IEE programme’s inception, Hartzenburg argues, but adds that energy optimisation will constantly require rethinking because components and operations within a business constantly change.
The IEE has collaborated with only a small fraction of the 14 500 small, medium-sized and large manufacturing facilities in South Africa, therefore there is a long future ahead for the IEE and energy optimisation in South Africa, Hartzenburg says.
Comments
Announcements
What's On
Subscribe to improve your user experience...
Option 1 (equivalent of R125 a month):
Receive a weekly copy of Creamer Media's Engineering News & Mining Weekly magazine
(print copy for those in South Africa and e-magazine for those outside of South Africa)
Receive daily email newsletters
Access to full search results
Access archive of magazine back copies
Access to Projects in Progress
Access to ONE Research Report of your choice in PDF format
Option 2 (equivalent of R375 a month):
All benefits from Option 1
PLUS
Access to Creamer Media's Research Channel Africa for ALL Research Reports, in PDF format, on various industrial and mining sectors
including Electricity; Water; Energy Transition; Hydrogen; Roads, Rail and Ports; Coal; Gold; Platinum; Battery Metals; etc.
Already a subscriber?
Forgotten your password?
Receive weekly copy of Creamer Media's Engineering News & Mining Weekly magazine (print copy for those in South Africa and e-magazine for those outside of South Africa)
➕
Recieve daily email newsletters
➕
Access to full search results
➕
Access archive of magazine back copies
➕
Access to Projects in Progress
➕
Access to ONE Research Report of your choice in PDF format
RESEARCH CHANNEL AFRICA
R4500 (equivalent of R375 a month)
SUBSCRIBEAll benefits from Option 1
➕
Access to Creamer Media's Research Channel Africa for ALL Research Reports on various industrial and mining sectors, in PDF format, including on:
Electricity
➕
Water
➕
Energy Transition
➕
Hydrogen
➕
Roads, Rail and Ports
➕
Coal
➕
Gold
➕
Platinum
➕
Battery Metals
➕
etc.
Receive all benefits from Option 1 or Option 2 delivered to numerous people at your company
➕
Multiple User names and Passwords for simultaneous log-ins
➕
Intranet integration access to all in your organisation