Coal mine on point of turning acid mine drainage into potable water at no cost
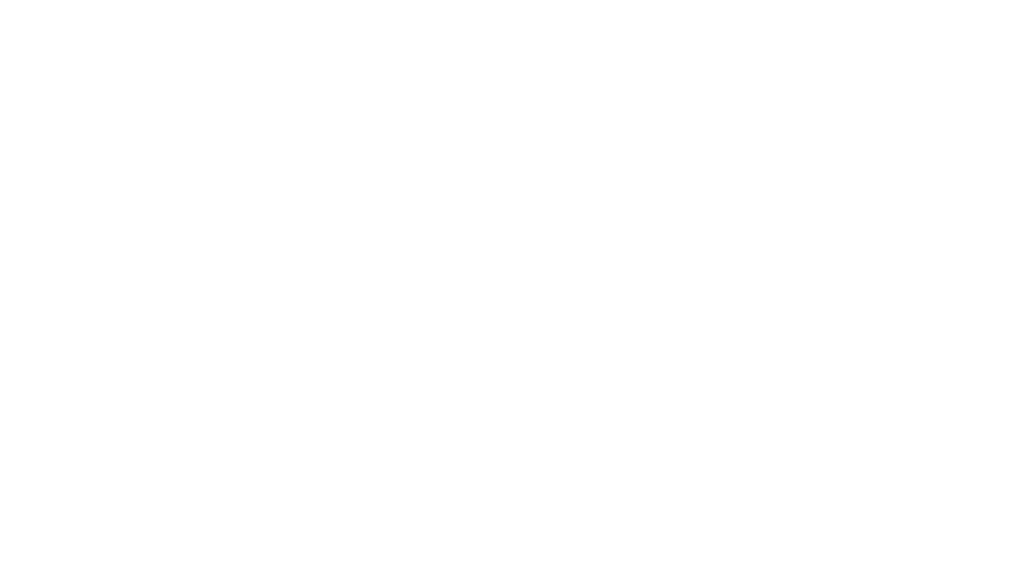
Trailblazer Technologies director John Bewsey interviewed by Mining Weekly’s Martin Creamer. Video: Darlene Creamer.
JOHANNESBURG (miningweekly.com) – An Mpumalanga coal mine is on the point of entering into an agreement before year-end to have its acid mine drainage water curse turned into potable water at no cost, Mining Weekly can today report.
Recovered potassium nitrate, which retails at about R15 000/t and which is marketed at about R11 000/t to R11 500/t, pays for everything – and a return on investment of about 30% is achieved.
The system recovers water at a negative -R2 per cubic metre, said Trailblazer Technologies director John Bewsey in a Zoom interview on Monday, November 23. (Also watch attached Creamer Media video.)
“In other words, each cubic metre of water that we recover brings us in R2,” he reiterated.
Not only mines, but also an organisation in the US and power utility Eskom are also showing interest in the Proudly South African development, which has been assisted by a grant from South Africa’s Technology Innovation Agency.
The grant has enabled Trailblazer to build what Bewsey described as a “world-class” demonstration plant at the company’s premises in Krugersdorp.
As part of the development, acid mine water has been trucked in from various mines and Trailblazer has been able to turn potable waters polluted with as little 3 000 milligrams per litre right up to water with as much as 50 000 milligrams per litre – “that’s 5%, which really is horrendous. We’ve been able to achieve greater than 99% recovery and the water is so pure it’s actually demineralised quality water, and nearly always below 20 milligrams per litre,” Bewsey enthused.
The system is attracting exceptional interest because of its:
- exceptionally high recovery rate of at least 99% of the water, which is a major improvement on any other water recovery process, including reverse osmosis, which generally recovers about 60% of the water and can only remove the salinity;
- absence of a brine to store, which is always hazardous and expensive; and
- ability to turn unwanted salinity into very-much-wanted end products which when sold end up showing a profit.
Because of the expense of storing brines, what many of the mines are doing is to have an electricity intensive process of spraying the brine into the air. In this way, the water evaporates and the solid lands back on the soil “like snow”, spreading the pollution far and wide, and actually achieving nothing, except removing the problem of having to have a dam of brine. But what actually happens is that rain redissolves the pollution, which is put back into the ecosystem.
“It doesn’t achieve anything at all other than waste a whole lot of Eskom’s rather scarce power,” said Bewsey.
Instead, Trailblazer’s system separates the pollution into cations and anions.
“The major pollutants, then, are sodium chloride and sulphate, which is what you get in any saline water, so we can not only treat acid mine water but also saline water, which can be recovered profitably as well.
“On the sodium side, we regenerate using nitric acid. From that we make sodium nitrate, which has got very little use. We then add the fertiliser potassium chloride and that precipitates out the least soluble salt, which is sodium chloride, and leaves us with potassium nitrate, which we separate out, and the sale of that potassium nitrate then pays for the entire process.
“On the anion side, we’ve then got a mixture of chlorides and sulphates and it depends what that mixture is. On quite a lot of the mines, the chlorides are fairly low and the sulphates are very high, so we turn that into ammonium sulphate, which is the fertiliser that we sell, and convert the chlorides into sodium chloride and add that to the stockpile of sodium chloride that we make from the cation side.
“That sodium chloride is a solid material so the cost of trucking it to the coast to put it back into the sea, where it belongs, is a minor cost because we’re trucking solids. We can use a flatbed truck and you’re paying for 100% of its weight in the transport. In the case of trucking a brine to the coast, one has about four tons of water per ton of solids so you end up paying 400% more for the trucking to the coast and it becomes impossible, whereas in our case, it’s economic because the cost of that transport is well covered by the sale of the fertiliser. We still end up with a sizeable net profit, and no brine,” Bewsey told Mining Weekly.
In treating 15 megalitres of acid mine drainage a day, the system yields 49 000 t/y of high-value potassium nitrate and 24 000 t/y of ammonium sulphate.
“The sale of that potassium nitrate pays for the entire process, and we’re left with useable water at no cost,” Bewsey reiterated.
A mixture of chlorides and sulphates is also recovered, and on many of the mines the chlorides are fairly low and the sulphates are very high.
“So, we turn that into ammonium sulphate, which is a fertiliser that we sell and the chlorides are then converted into sodium chloride.
Trailblazer’s model is to build plants in partnership with funders and enter into contracts with mining companies to treat their acid mine water.
It envisages mines having water supply problems solved and farmers being shielded from sodium damage.
The newly developed process can also be used to turn South Africa’s considerable sustainable groundwater areas in arid regions to positive agricultural account – “South Africa could be turned into an agricultural Garden of Eden, quite quickly and quite easily”.
ROBBIE ROBINSON
The late Dr RE (Robbie) Robinson drew up the zero-cost plan for acid mine water as long ago as 1996 for the now stricken Grootvlei gold mine, on the East Rand.
It involved moving away from the process of adding large quantities of lime into the acid water, precipitating it and allowing the overflow to go into the local Blesbokspruit.
Instead, the visionary chemical engineer with distinguished involvement in minerals beneficiation spanning more than 60 years and a passion for linking mining and agriculture, formed an association with a company specialising in the ion-exchange method and engaged previously disadvantaged technikon students to develop a new process that made use of the ion-exchange resin that Trailblazer is now using at its Krugersdorp plant.
In the Grootvlei case, the resin removed the ferric oxide and the acid and was easily regenerated by eluting it with ammonia and producing ammonium sulphate for fertiliser.
The red ferric oxide was very saleable along with nigh nuclear-grade uranium as well as cobalt, copper and nickel oxides.
Moreover, the virtually distilled water was earmarked for agricultural irrigation. Taking all this into account, the Grootvlei gold mine would have been put into a position to treat its acid mine water at zero cost, with Robinson’s innovative new process opening up agricultural pursuits for the people of the nearby informal settlement.
However, the Department of Water and Sanitation of the time broke Robinson’s heart when it opted instead for a far more expensive R10-million alternative that fell flat on its face, had to be discontinued and probably contributed to Grootvlei’s demise, along with the subsequent ignominious Aurora liquidation debacle.
Comments
Press Office
Announcements
What's On
Subscribe to improve your user experience...
Option 1 (equivalent of R125 a month):
Receive a weekly copy of Creamer Media's Engineering News & Mining Weekly magazine
(print copy for those in South Africa and e-magazine for those outside of South Africa)
Receive daily email newsletters
Access to full search results
Access archive of magazine back copies
Access to Projects in Progress
Access to ONE Research Report of your choice in PDF format
Option 2 (equivalent of R375 a month):
All benefits from Option 1
PLUS
Access to Creamer Media's Research Channel Africa for ALL Research Reports, in PDF format, on various industrial and mining sectors
including Electricity; Water; Energy Transition; Hydrogen; Roads, Rail and Ports; Coal; Gold; Platinum; Battery Metals; etc.
Already a subscriber?
Forgotten your password?
Receive weekly copy of Creamer Media's Engineering News & Mining Weekly magazine (print copy for those in South Africa and e-magazine for those outside of South Africa)
➕
Recieve daily email newsletters
➕
Access to full search results
➕
Access archive of magazine back copies
➕
Access to Projects in Progress
➕
Access to ONE Research Report of your choice in PDF format
RESEARCH CHANNEL AFRICA
R4500 (equivalent of R375 a month)
SUBSCRIBEAll benefits from Option 1
➕
Access to Creamer Media's Research Channel Africa for ALL Research Reports on various industrial and mining sectors, in PDF format, including on:
Electricity
➕
Water
➕
Energy Transition
➕
Hydrogen
➕
Roads, Rail and Ports
➕
Coal
➕
Gold
➕
Platinum
➕
Battery Metals
➕
etc.
Receive all benefits from Option 1 or Option 2 delivered to numerous people at your company
➕
Multiple User names and Passwords for simultaneous log-ins
➕
Intranet integration access to all in your organisation