Coatings, cladding enhance pump performance
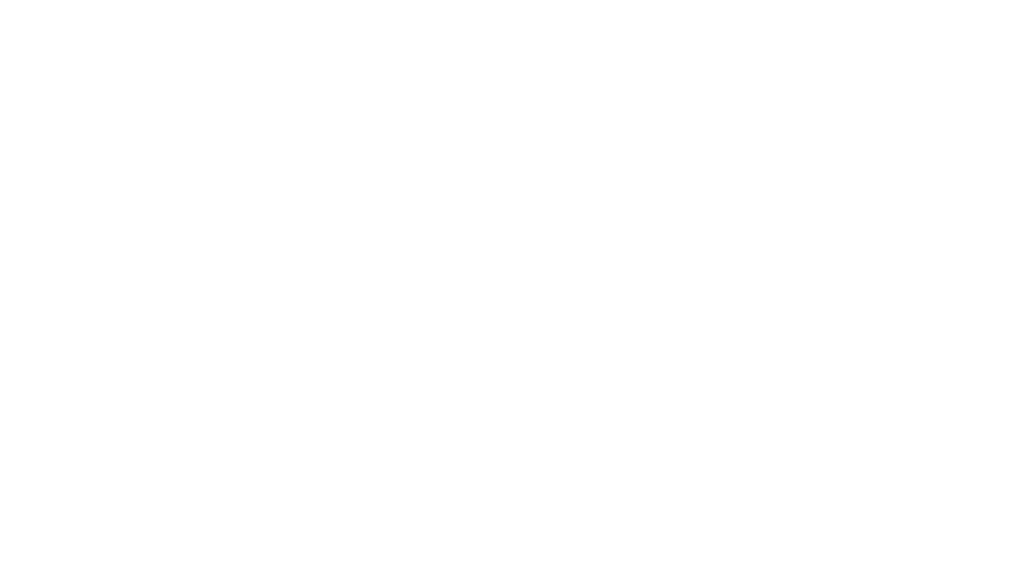
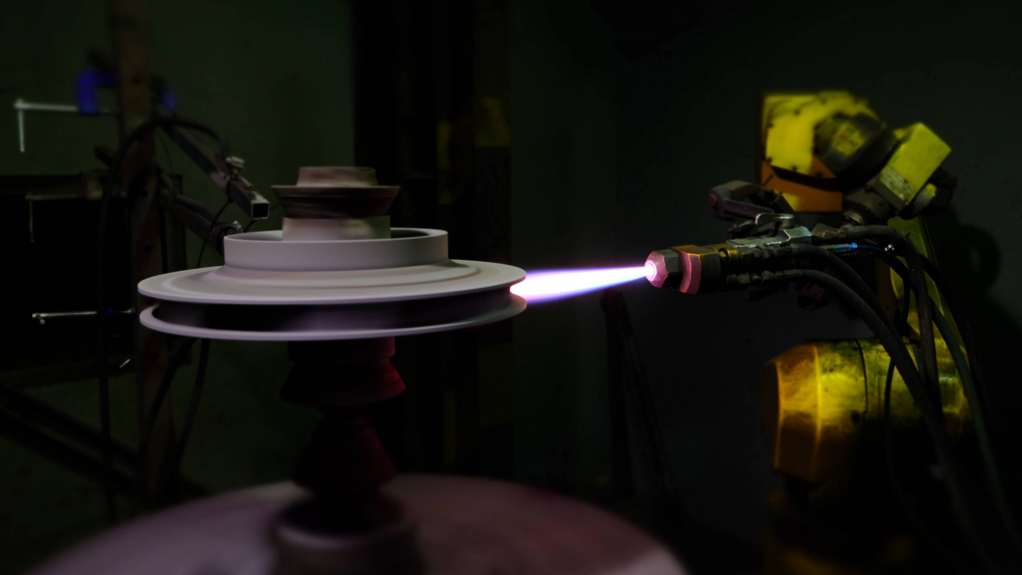
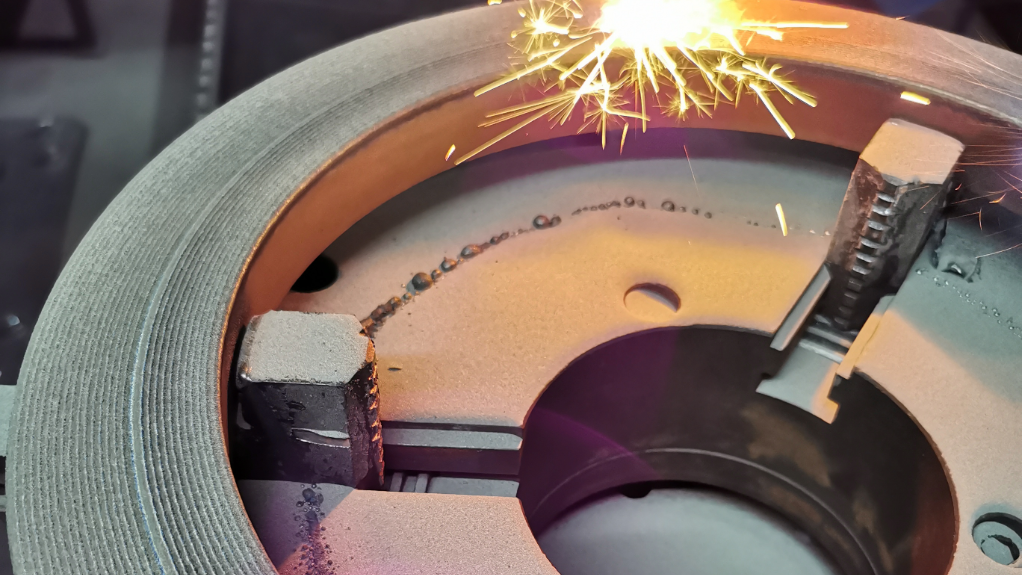
ESSENTIAL MAINTENANCE Coatings protect high-wear areas, such as impeller lands and casing rings, which are essential for maintaining the pump’s efficiency and prolonging its operational life
PROTECTIVE LAYER A protective layer is applied to critical components such as impellers, rings and casing surfaces, shielding them from the damaging effects of wear and tear
Surface engineering company Thermaspray’s thermal spray coatings and laser cladding technologies are delivering significant benefits to the pumps industry, particularly for components subjected to harsh operating conditions.
With a focus on extending the life of high-wear components and reducing maintenance costs, these technologies are “becoming indispensable” for industries, such as mining, where pumps must withstand the abrasive effects of solid particulates, says production manager Paul Young.
Thermal spray coatings are primarily used to extend the life of pump components, as abrasion in pumps often occurs when solid particles are present in the liquid being pumped from mine shafts, dams or other industrial sites.
They create a protective layer on critical components, such as impellers, rings and casing surfaces, shielding them from the damaging effects of wear and tear, he explains.
“In some cases, our coatings can be used to repair or refurbish components, like damaged pump shafts,” Young adds, highlighting the example of pump shafts that are manufactured from specialised materials, where the lead times for manufacturing replacements can take several months.
By applying Thermaspray’s coating technology to repair the damaged areas, the time to restore functionality is reduced from months to days, in addition to improving the overall characteristics of the repaired component.
Young adds that the application of thermal spray coatings can be highly beneficial for industries that rely on pumps to operate in harsh environments, as the coatings help maintain the clearances critical for efficient pump operation.
Thermaspray’s thermal spray coatings are also specifically designed to protect the internal hydraulics of pumps, which are most vulnerable to wear caused by solid particulates in the water.
“The internal hydraulics, including impellers, rings and diffusers, have shown the most improvement when coated. These components experience reduced wear, allowing for longer operational life spans and more consistent pump performance,” he says.
A 2007 study conducted by the company further demonstrates the economic and operational benefits of its coating solutions. The study indicates that coated pumps required about 11% less energy to pump the same volume of water, while pumping time was reduced by as much as 20%.
“This leads to significant cost savings through not only reduced energy consumption but also lower overall operational costs associated with maintaining pump systems,” Young adds.
By reducing wear, the frequency of pump replacements is lowered, contributing to reduced maintenance costs and increased uptime, he adds.
Meanwhile, Thermaspray’s laser cladding technology offers a high-performance solution for repairing worn pump components.
One of the key advantages of laser cladding is the formation of a metallurgical bond between the coating material and the substrate. This bond, combined with the ability to apply thicker coatings, results in a more durable repair that can withstand the demanding conditions to which pump components are exposed.
“Laser cladding is a low-heat input process, which allows us to apply the cladding on components that would typically distort under conventional welding techniques,” Young explains.
This is particularly important for parts, such as impeller lands and volute casings, where distortion could severely impact on the repair procedure, timelines and costing.
The selective nature of laser cladding results in only the damaged areas being repaired, as the integrity of the surrounding components that remain unaffected by wear are preserved.
Another significant advantage of laser cladding is that many materials do not require post-weld heat treatment, further reducing the risk of distortion and shortening the overall repair time.
This is especially useful in environments where downtime must be kept to a minimum, as pump components can be quickly repaired and returned to service without compromising performance or safety.
Thermaspray continues to explore new ways of enhancing its thermal spray coatings and laser cladding technologies.
Young says the company has a close working relationship with powder manufacturers, such as Oerlikon and Praxair, to evaluate and implement new coating materials that offer even greater durability and wear resistance.
“We are always looking at ways to improve the application process, including the use of robotics to adapt coatings for different wear patterns,” he concludes.
Comments
Press Office
Announcements
What's On
Subscribe to improve your user experience...
Option 1 (equivalent of R125 a month):
Receive a weekly copy of Creamer Media's Engineering News & Mining Weekly magazine
(print copy for those in South Africa and e-magazine for those outside of South Africa)
Receive daily email newsletters
Access to full search results
Access archive of magazine back copies
Access to Projects in Progress
Access to ONE Research Report of your choice in PDF format
Option 2 (equivalent of R375 a month):
All benefits from Option 1
PLUS
Access to Creamer Media's Research Channel Africa for ALL Research Reports, in PDF format, on various industrial and mining sectors
including Electricity; Water; Energy Transition; Hydrogen; Roads, Rail and Ports; Coal; Gold; Platinum; Battery Metals; etc.
Already a subscriber?
Forgotten your password?
Receive weekly copy of Creamer Media's Engineering News & Mining Weekly magazine (print copy for those in South Africa and e-magazine for those outside of South Africa)
➕
Recieve daily email newsletters
➕
Access to full search results
➕
Access archive of magazine back copies
➕
Access to Projects in Progress
➕
Access to ONE Research Report of your choice in PDF format
RESEARCH CHANNEL AFRICA
R4500 (equivalent of R375 a month)
SUBSCRIBEAll benefits from Option 1
➕
Access to Creamer Media's Research Channel Africa for ALL Research Reports on various industrial and mining sectors, in PDF format, including on:
Electricity
➕
Water
➕
Energy Transition
➕
Hydrogen
➕
Roads, Rail and Ports
➕
Coal
➕
Gold
➕
Platinum
➕
Battery Metals
➕
etc.
Receive all benefits from Option 1 or Option 2 delivered to numerous people at your company
➕
Multiple User names and Passwords for simultaneous log-ins
➕
Intranet integration access to all in your organisation