Commissioning of tin concentrate dryer finalised
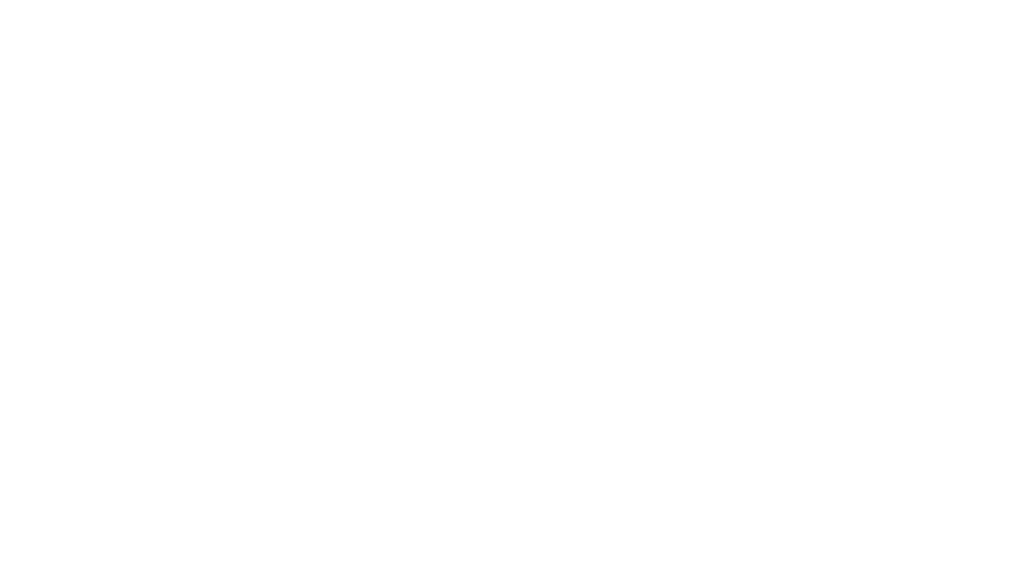
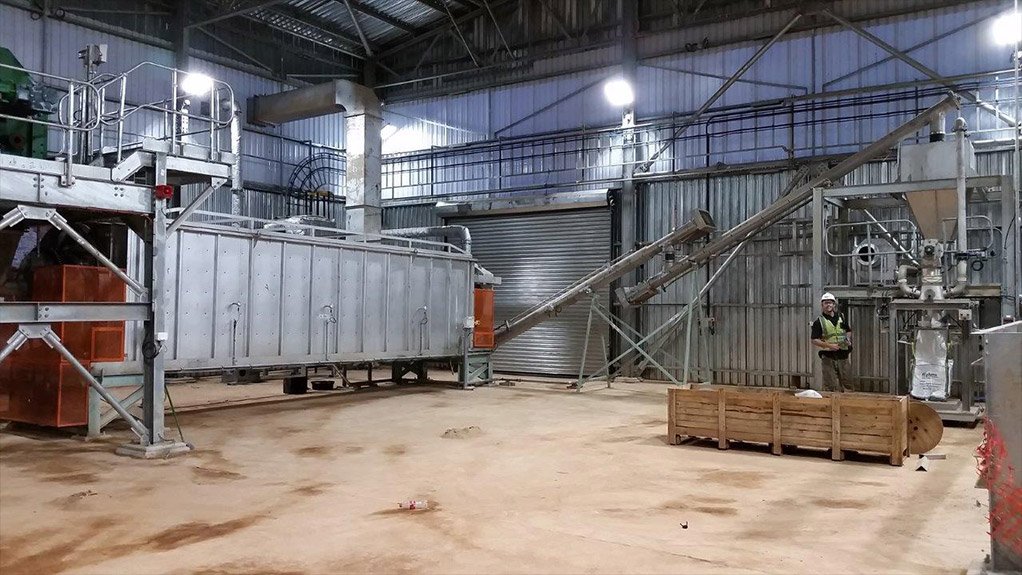
TESTING Thermopower has manufactured the rotary dryer for the Bisie tin mine and a laboratory unit for national mineral research organisation Mintek to carry out iron-ore reducibility testing
South Africa-based furnace and kiln manufacturer Thermopower Furnaces commissioned a tin concentrate dryer at tin mine developer Alphamin Resources’ Bisie tin mine, in the Democratic Republic of Congo, in March.
Thermopower director William Oldnall tells Mining Weekly that the rotary dryer is diesel-fired and has an insulated baghouse filter, as well as a feed screw, discharge screw and cooling screw. The dryer is about 10 m long, 2.4 m wide and 2.4 m high and can dry 3 t/h of concentrate.
“This unit was designed to be modular and easily containerised to facilitate transport to its extremely remote location.”
He adds that time was critical on the project, and “we managed to design, build, put it through a factory acceptance test and prepare the dryer for shipping within seven weeks of receiving the order”.
Being able to dry the ore concentrate on site is one of the benefits of having the dryer at the mine, says Oldnall. The dryer ensures that the concentrate does not have unnecessary moisture content that could increase transportation costs.
Meanwhile, Thermopower is working on other projects for the engineering and mining industries across South Africa, which will be commissioned this month and the next. One of the projects is for the recovery of platinum-group metals (PGMs) at a precious metals refinery in Rustenburg, in the North West.
The thermal beneficiation plant comprises an electrically fired controlled air rotary incinerator with hydraulic ram feed system and discharge screw. He explains that this unit addresses the client’s need to safely recover valuable PGMs that are entrained in its solvent plant waste streams. “The focus of the design was to ensure no operator contact with the feed materials,” says Oldnall.
This equipment will enable the client to process its solvent waste streams directly on site, greatly reducing the administration and security cost of transporting the material to an external contractor, he adds.
“The technology was developed over an 18-month research and development (R&D) period at our premises, and is a novel approach to incineration. The plant was ordered on the merits of the R&D campaign, which demonstrated excellent results.”
He notes that this project is one of the most notable projects Thermopower has done for the year because it is a combination of the company’s innovative technologies, designed to extract value from waste streams.
However, Oldnall points out that the recent amendments to environmental legislation are hampering R&D efforts, as the law makes no provision for R&D on listed activities.
“Whether you are producing a few kilograms of material over a number of months or establishing a commercial operation producing several hundred tons, you are subjected to the same requirements and permitting costs, which generally makes R&D prohibitively expensive and drawn out.”
Oldnall adds that the development of the country’s resources will, nonetheless, inevitably create opportunities for local thermal equipment manufacturers in established technologies and R&D. “We are productively engaged with the relevant authorities and remain positive that working together, we will arrive at a solution for R&D enterprises to operate with the new legal framework.
“South Africa still has an abundance of mineral wealth, which should underpin the economic growth the country is in such dire need of, provided government can establish the appropriate business and political environment.”
He notes that several local kiln, furnace and dryer manufacturers are “world class” in terms of their technology and supply innovative solutions worldwide.
“There is plenty of opportunity to be seized in the global arena in the minerals processing space, and I hope that South African suppliers continue to fly the flag and extend their reach into these markets,” Oldnall concludes.
Comments
Press Office
Announcements
What's On
Subscribe to improve your user experience...
Option 1 (equivalent of R125 a month):
Receive a weekly copy of Creamer Media's Engineering News & Mining Weekly magazine
(print copy for those in South Africa and e-magazine for those outside of South Africa)
Receive daily email newsletters
Access to full search results
Access archive of magazine back copies
Access to Projects in Progress
Access to ONE Research Report of your choice in PDF format
Option 2 (equivalent of R375 a month):
All benefits from Option 1
PLUS
Access to Creamer Media's Research Channel Africa for ALL Research Reports, in PDF format, on various industrial and mining sectors
including Electricity; Water; Energy Transition; Hydrogen; Roads, Rail and Ports; Coal; Gold; Platinum; Battery Metals; etc.
Already a subscriber?
Forgotten your password?
Receive weekly copy of Creamer Media's Engineering News & Mining Weekly magazine (print copy for those in South Africa and e-magazine for those outside of South Africa)
➕
Recieve daily email newsletters
➕
Access to full search results
➕
Access archive of magazine back copies
➕
Access to Projects in Progress
➕
Access to ONE Research Report of your choice in PDF format
RESEARCH CHANNEL AFRICA
R4500 (equivalent of R375 a month)
SUBSCRIBEAll benefits from Option 1
➕
Access to Creamer Media's Research Channel Africa for ALL Research Reports on various industrial and mining sectors, in PDF format, including on:
Electricity
➕
Water
➕
Energy Transition
➕
Hydrogen
➕
Roads, Rail and Ports
➕
Coal
➕
Gold
➕
Platinum
➕
Battery Metals
➕
etc.
Receive all benefits from Option 1 or Option 2 delivered to numerous people at your company
➕
Multiple User names and Passwords for simultaneous log-ins
➕
Intranet integration access to all in your organisation