Pilot projects start at mines
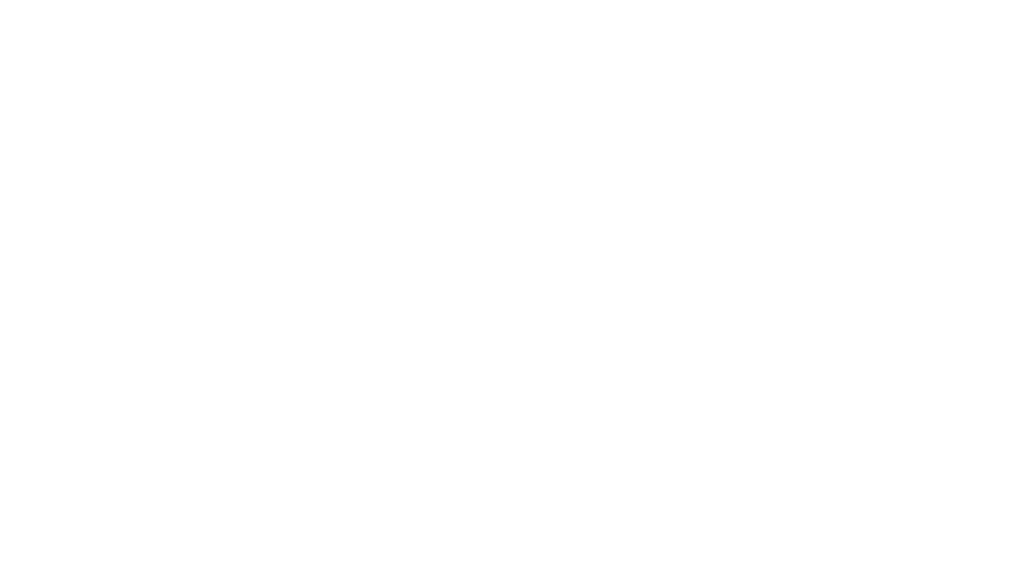

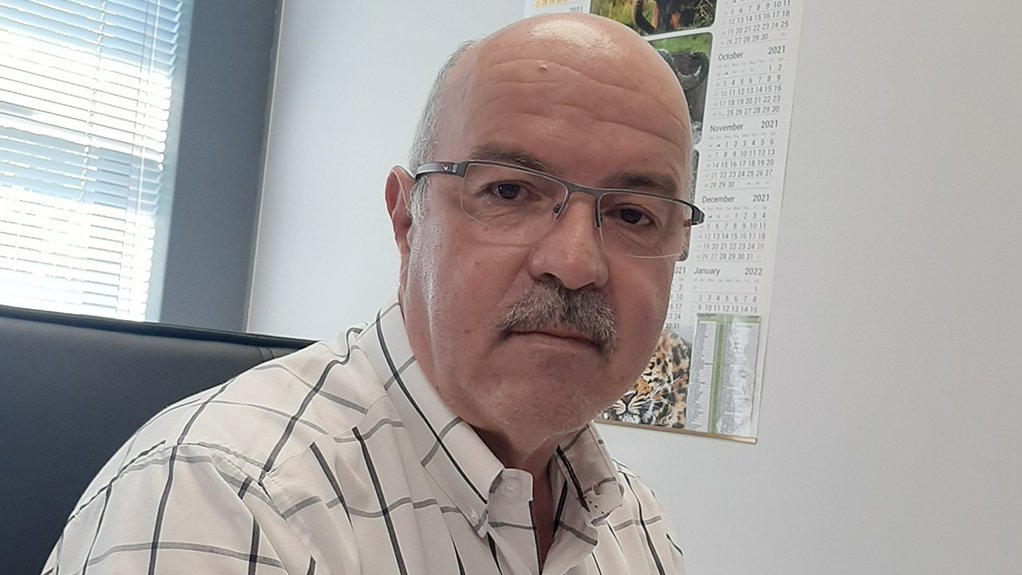
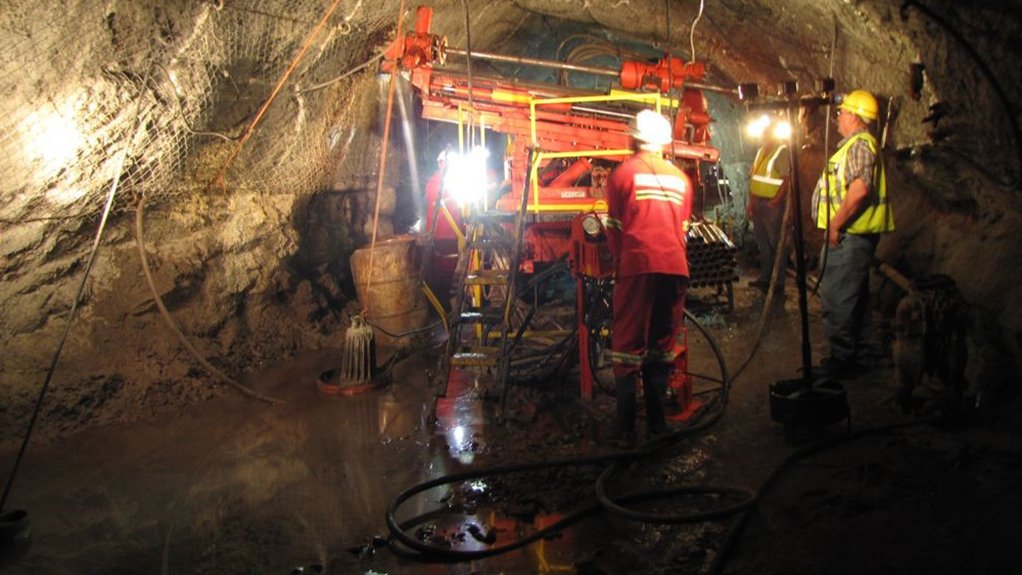
GROUNDBREAKING DRILLING The company’s Rocor machines are standardised and fully interchangeable drills. They can be used above and below ground, and can be truck-, skid- or crawler-mounted
CAROLS DA SILVA Rosond has been involved in all local mining sectors, including iron-ore, diamonds, gold, coal and others, where we have done extensive underground drilling
VERSATILE RANGE Rosond has a 22 kW mini-Rocor, a 45 kW Rocor for exploration and LIB drilling, and a 75 kW for drilling in excess of 1 000 m
Drilling technology and services provider Rosond is involved in the development of new drilling solutions and methodologies for pilot projects at local underground mines.
These projects involve using innovations, such as drilling using flushed air or foam instead of water, as well as using smaller machines for pothole drilling, says Rosond director Carlos Da Silva.
The first project is at gold miner Gold Fields’ South Deep underground mine, in Gauteng.
The company began a pilot project in February to use Rosond’s 22 kW mini-Rocor machine to do cover, prospect drilling and backfill testing for the mine.
“The mine is using backfill as a support mechanism, and we are trying to see if we can use dry drilling, without water. The pilot project is focused on drilling through the backfill so that the mine can establish how strong the support mechanism is currently.”
This comes in addition to six 75 kW Rocor drilling machines which were also being used for drilling of long inclined boreholes (LIB) exploration drilling in high distressed areas for the mine.
The Rocor machines are standardised and fully interchangeable drills. They can be used above and below ground, and can be truck-, skid- or crawler-mounted.
The mini-Rocor was introduced to the local market in 2010 as a prototype 22 kW to replace the older, noisier pneumatic drill rigs to comply with the new environmental noise level and safety requirements, and Rosond has subsequently improved aspects of the machine.
The company is conducting a feasibility study for this drilling methodology. Da Silva says Rosond hopes that this methodology can create a new market in dry drilling, adding that using water is generally the preferred method for drilling.
He stresses that this methodology will provide the mine with a clear ore sample that is not contaminated by any water or chemicals. Receiving a dry ore sample will also help the miner to determine the quality of its backfill support mechanism.
Backfill material provides support to surrounding rock mass, and allows for a safe working area for production activities in an underground mine.
“With rock mechanics, that’s the end-game – ensuring that the backfill support is sufficient for the mine. Dry drilling will go a long way towards providing the mine with an accurate sample on what they’re looking for.”
Since the beginning of the pilot project, Rosond has used a combination of methods, firstly, changing the diameter of the borehole drilled and then using a combination of air and foam.
While the company is still waiting for the results of the feasibility study, Da Silva states that, to date, dry drilling using air and foam has proved more successful and is the preferred method.
Platinum Project
The second project that Da Silva highlights is concerned with potholes that occur during mining operations in the platinum-rich Bushveld Igneous Complex in South Africa.
Potholes can result in fracturing and fragmentation of the mined material. This can lead to ground instabilities, particularly in the hanging wall, and other safety concerns.
To address this, Rosond has been involved with a pothole drilling pilot project since January at platinum miner Impala Platinum’s mining operation in the area.
Rosond is using smaller, easily transportable machines to move into mining stopes, and drill 10 m to 15 m holes, to determine the size of the potholes that occur underground. “This lack of heavy equipment enables Rosond to use “the smallest size core that we can drill.”
Rosond, to date, has completed a pilot project at platinum miner Impala. Da Silva emphasises that if this project is successful, two to three machines can be used on any given shaft at the mine to determine the size of a pothole.
This means that Rosond can easily access the working area in a shaft, drill a 10 m to 15 m hole with a smaller machine, determine where the pothole is located and how large it is, and then carry on drilling safely.
Da Silva enthuses that this can save miners money in blasting and developing in mine areas where there is no reef, and can save money and time in developing areas that are not payable.
“We’ve now started a pilot project at Impala. It is new for the industry as far as pothole drilling is concerned, whereby mines can save significantly by eliminating unnecessary drilling. We do the drilling the mine needs, and help them safeguard and explore the ore.”
If successful, this pothole drilling methodology could be implemented throughout the mine which could see Rosond mobilising additional machines.
Comments
Press Office
Announcements
What's On
Subscribe to improve your user experience...
Option 1 (equivalent of R125 a month):
Receive a weekly copy of Creamer Media's Engineering News & Mining Weekly magazine
(print copy for those in South Africa and e-magazine for those outside of South Africa)
Receive daily email newsletters
Access to full search results
Access archive of magazine back copies
Access to Projects in Progress
Access to ONE Research Report of your choice in PDF format
Option 2 (equivalent of R375 a month):
All benefits from Option 1
PLUS
Access to Creamer Media's Research Channel Africa for ALL Research Reports, in PDF format, on various industrial and mining sectors
including Electricity; Water; Energy Transition; Hydrogen; Roads, Rail and Ports; Coal; Gold; Platinum; Battery Metals; etc.
Already a subscriber?
Forgotten your password?
Receive weekly copy of Creamer Media's Engineering News & Mining Weekly magazine (print copy for those in South Africa and e-magazine for those outside of South Africa)
➕
Recieve daily email newsletters
➕
Access to full search results
➕
Access archive of magazine back copies
➕
Access to Projects in Progress
➕
Access to ONE Research Report of your choice in PDF format
RESEARCH CHANNEL AFRICA
R4500 (equivalent of R375 a month)
SUBSCRIBEAll benefits from Option 1
➕
Access to Creamer Media's Research Channel Africa for ALL Research Reports on various industrial and mining sectors, in PDF format, including on:
Electricity
➕
Water
➕
Energy Transition
➕
Hydrogen
➕
Roads, Rail and Ports
➕
Coal
➕
Gold
➕
Platinum
➕
Battery Metals
➕
etc.
Receive all benefits from Option 1 or Option 2 delivered to numerous people at your company
➕
Multiple User names and Passwords for simultaneous log-ins
➕
Intranet integration access to all in your organisation