Company offers alternative to conventional splicing
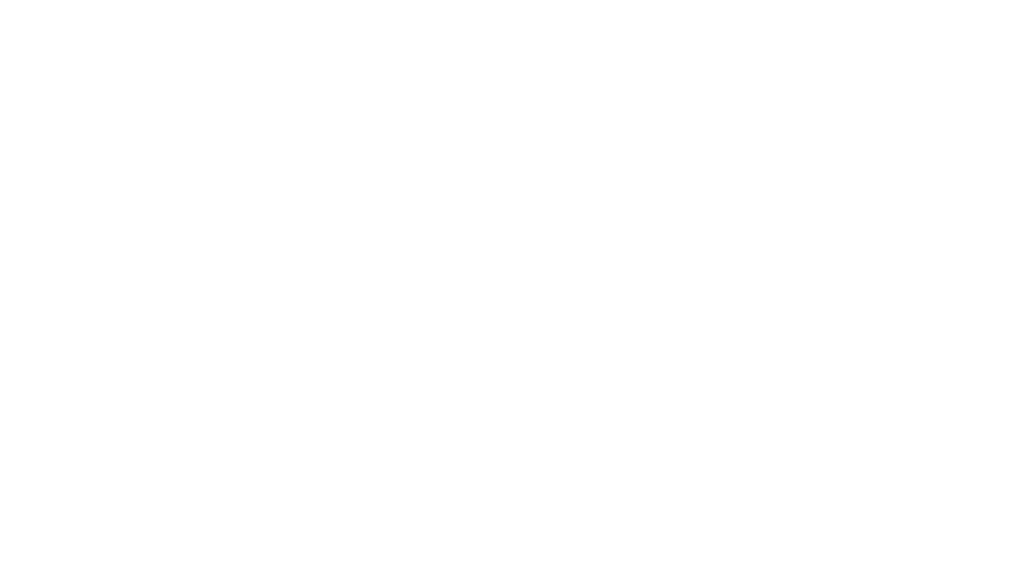
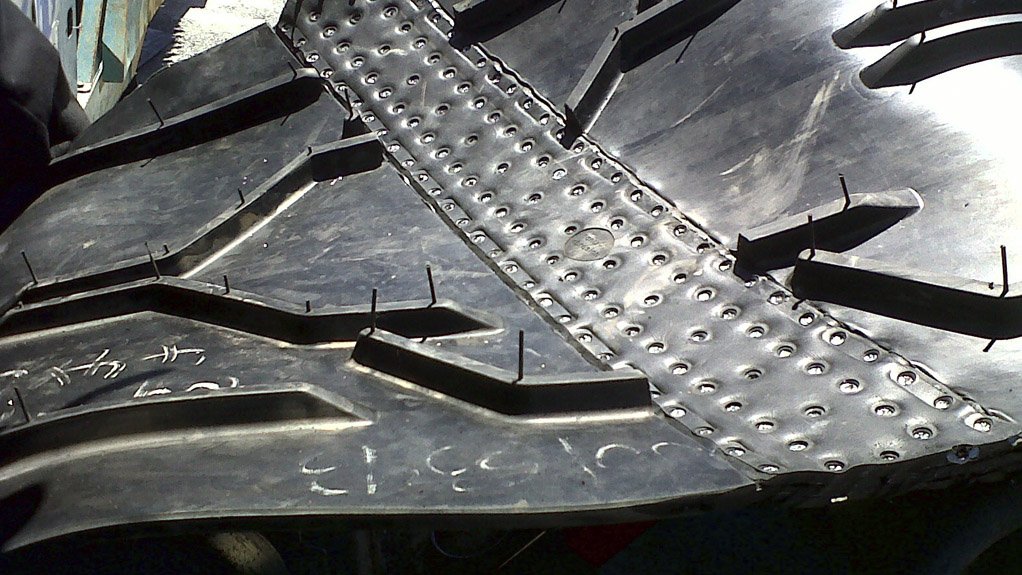
SUPER SPLICING The Super-Screw surface of the splice is level with the two ends of the original belt, making the splice surface as even and as thick as the belt itself
A current trend in the conveyors industry with regard to splicing procedures is to avoid the use of hazardous substances wherever possible, says technical solutions provider BMG.
These solvents have an anaesthetic effect and must be used with face shields and gloves, owing to health and safety concerns. Exposure to hazardous solvents such as trichloroethylene in the workplace may cause scleroderma, which is a systematic autoimmune disease.
Trichloroethylene is often used in conventional hot and cold splicing procedures; however, it can be replaced with BMG’s Super-Screw system as a safe splicing alternative.
Field test results indicate that this is the quickest method to repair a conveyor belt in any emergency situation, reducing downtime. “The mechanical joining technique is easy to complete, [not requiring] a skilled operator and heavy, costly equipment,” states BMG.
This Super-Screw system, which offers high tensile strength, has proved to be a suitable alternative to conventional splicing methods and, in some cases, has exceeded the tensile rating of hot and cold splice samples of the same class rating.
The tests, using a belt with a 600 mm width, demonstrated that a conventional hot splice takes seven hours and a cold splice including curing takes over eight hours, while the Super-Screw takes less than one hour.
The system is leakproof and can be used for belt joining, repairing a longitudinal rip or a puncture in the belt, as well as inserting new belting into old conveyor belt systems. It is also compatible with small pulley diameters, suitable for pipe conveyors and is conveyor scraper and V-plough (a cleaning measure on belts) friendly.
The screws within the system are self-drilling and self-tapping, spreading the carcass threads without cutting them. The system requires no predrilling, can withstand service tensions of up to 2 000 kN/m and is available in various rubber grades to suit requirements.
The rubber material, containing tensile fabric used for the splices, is manufactured in rolls up to 25 m long and in various strength ratings, from Class 315 to Class 2 000 conveyor belting. The material is abrasion, heat, fire and oil resistant, as well as heat retardant up to 200 ºC.
“The Super-Screw system is also available in a ready-to- install option, with maximum precut lengths of 3 m and preinstalled assembly spacers. This nonmagnetic system has metallic inserts made of stainless steel with stainless steel screws,” reports BMG.
Steel screws are screwed into an embedded nut inside the material, sandwiching the belt carcass between the top and bottom covers.
The surface of the splice is level with the two ends of the original belt, making the splice surface as even and as thick as the belt itself. It is fitted at the bias like regular splices to ensure optimal strength and flexibility around the pulleys.
In selecting the correct Super-Screw fastener for each application, factors to consider include the belt tension and strength of the belt, as well as the required final belt thickness.
Additionally, ambient conditions have to be considered before a cold splice can take place – if the humidity levels are too high, the adhesive may not be effective. However, the Super-Screw is effective in all weather conditions.
“With training from BMG, an in-house maintenance team can quickly and efficiently install the Super-Screw system, using a simple tool such as an electrical or battery-powered screwdriver,” notes BMG.
Commitment to Conveyors
BMG ensures operational efficiency of light and bulk materials handling systems in the mining industry through the supply of a range of high-quality branded components, supported by technical resources, fabrication and field service capabilities.
“Because conveying and materials handling form a critical part of production and mining processes, BMG focuses on limiting interruptions and downtime,” says BMG materials handling GM Ryan Forsyth.
He adds that specialist regional service centres, with fabrication operations that include belt conversion and joining, are enhanced by an on-site splicing and maintenance service offered by BMG.
The company also works closely with the South African Bureau of Standards (SABS) to ensure certification of various belt types, specifying that products are manufactured independently to strict standards, which ensure high-quality product manufacturing.
“BMG has forged partnerships with a select group of belt manufacturers around the world and is, therefore, able to select the most suitable manufacturer for the product scope requirement. “These plants have been SABS-audited and are approved manufacturers, in accordance with SABS standards,” notes Forsyth.
Other Components
BMG supplies a range of screening media with various surfaces to suit performance requirements. Selection of the correct product is based on the specific application, material size, desired throughput and required efficiency of the screen.
Included in BMG’s range are polyurethane (PU) and rubber screen panels, side liners, spray nozzles, screen mounts, springs and rubber buffers.
Standard PU screen panels, of 85 Shore hardness, have a dynamic load capacity and are designed for efficient operation in wet and dry applications. Special PU screen panels, such as PolyTuff, of 60 Shore hardness, have the properties of standard PU and rubber, and improved flexibility from specially engineered plastics.
These screens do not perish in elevated temperature environments and offer extended service life, states BMG.
Woven wire mesh screens, which are designed for corrosion and abrasion resistance, are manufactured from high carbon, mild steel, stainless steel and spring steel and are available in square, slotted, standard harp and tri-harp weave types, with an aperture range of 2 mm to 120 mm. The wire diameter ranges from 0.9 mm to 12.5 mm.
Comments
Press Office
Announcements
What's On
Subscribe to improve your user experience...
Option 1 (equivalent of R125 a month):
Receive a weekly copy of Creamer Media's Engineering News & Mining Weekly magazine
(print copy for those in South Africa and e-magazine for those outside of South Africa)
Receive daily email newsletters
Access to full search results
Access archive of magazine back copies
Access to Projects in Progress
Access to ONE Research Report of your choice in PDF format
Option 2 (equivalent of R375 a month):
All benefits from Option 1
PLUS
Access to Creamer Media's Research Channel Africa for ALL Research Reports, in PDF format, on various industrial and mining sectors
including Electricity; Water; Energy Transition; Hydrogen; Roads, Rail and Ports; Coal; Gold; Platinum; Battery Metals; etc.
Already a subscriber?
Forgotten your password?
Receive weekly copy of Creamer Media's Engineering News & Mining Weekly magazine (print copy for those in South Africa and e-magazine for those outside of South Africa)
➕
Recieve daily email newsletters
➕
Access to full search results
➕
Access archive of magazine back copies
➕
Access to Projects in Progress
➕
Access to ONE Research Report of your choice in PDF format
RESEARCH CHANNEL AFRICA
R4500 (equivalent of R375 a month)
SUBSCRIBEAll benefits from Option 1
➕
Access to Creamer Media's Research Channel Africa for ALL Research Reports on various industrial and mining sectors, in PDF format, including on:
Electricity
➕
Water
➕
Energy Transition
➕
Hydrogen
➕
Roads, Rail and Ports
➕
Coal
➕
Gold
➕
Platinum
➕
Battery Metals
➕
etc.
Receive all benefits from Option 1 or Option 2 delivered to numerous people at your company
➕
Multiple User names and Passwords for simultaneous log-ins
➕
Intranet integration access to all in your organisation