Crushing plant fabrication completed
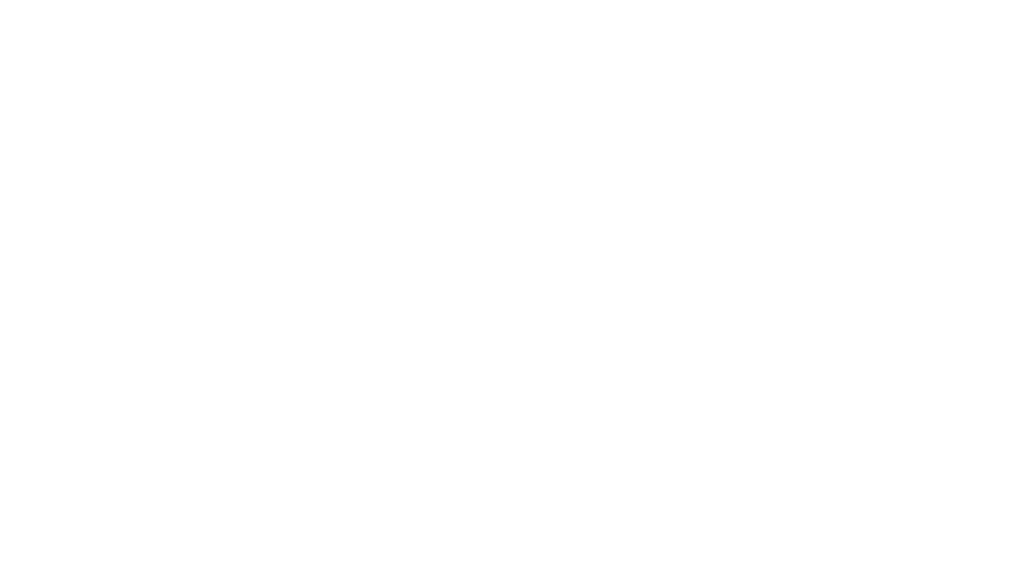
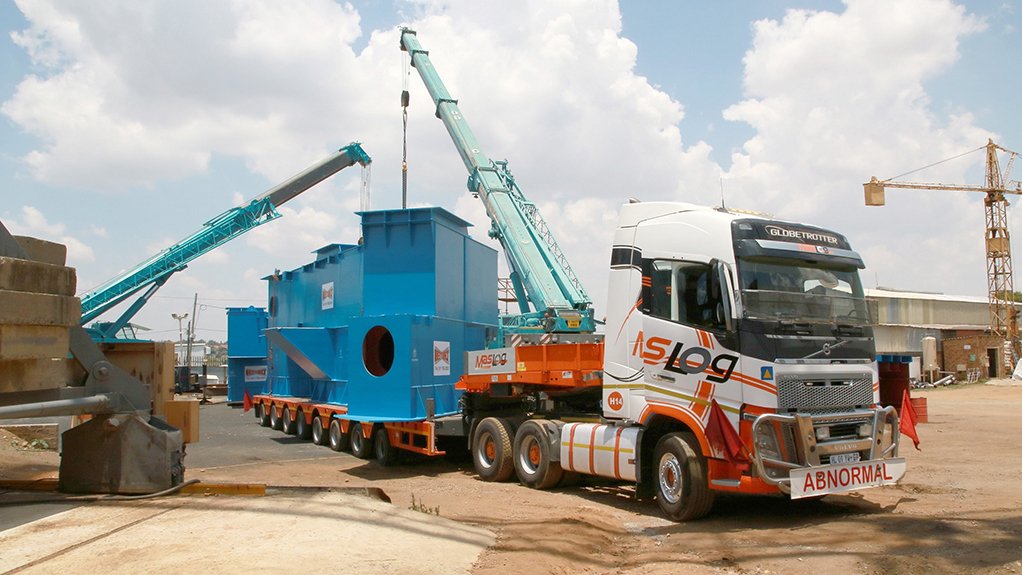
A MOVING PROJECT The semi-mobile crusher plant is a pan-African infrastructure project that required collaboration between African industrial suppliers
Steel fabrication and structure erection company Betterect has successfully completed the fabrication of a semimobile crushing plant (SMCP) for a coal mine in Mozambique. The SMCP project was required to meet the mine’s goal to increase production.
The mining business unit of diversified industrial company ThyssenKrupp commissioned Betterect to undertake the project, which was awarded at the end of July 2019, with fabrication completed in February this year. Project delivery was well within the specified timeline and budget.
While ThyssenKrupp designed the SMCP, Betterect was awarded the fabrication and preassembly was responsible for SMCP equipment in South Africa.
“This was not only because we are recognised for our focus on quality and our extensive experience and expertise, but also because we are ideally located to carry out fabrication and erection projects throughout Southern and Central Africa,” says Betterect MD Nicolette Skjoldhammer.
The SMCP project was accordingly undertaken in Betterect’s workshop in Chamdor, Krugersdorp, as the client required preassembly and full fabrication in one off-site location. This also reduced the safety risks associated with hot work on-site.
All fabrication and preassembly work was carried out under strict quality assurance and project management protocols, in accordance with South African Bureau of Standards 0157 and International Organisation for Standardisation 9001:2000 standards.
“Moreover, all safety, health environment and quality requirements were met. From an environmental perspective, and with environmental concerns top-of-mind, all steel off-cuts were collected and recycled,” Skjoldhammer points out.
About the Fabrication
Comprising over 1 000 component parts, once completed, the SMCP totalled 950 t overall – including items such as grating and hand-railing. Some 750 t comprised Betterect’s structural steel and platework, while VRN – hard-wearing steel plate – linings accounted for about 60 t thereof.
To handle the massive operational loads placed on the SMCP during the day-to-day operations at the mine, steelwork and platework was selected as the construction material of choice.
“The SMCP needed to be robust enough to cope with this very demanding working environment,” Skjoldhammer explains.
Throughout the project, Betterect ensured the most stringent quality standards of fabrication. Consequently, the fabricator used its expertise in full penetration welding technology.
“Over the past five years we have made a significant investment into the latest pulse arc welding technology, which not only provides excellent weld quality but significantly reduces welding time and duration.”
Skjoldhammer adds that this technology is highly effective in ensuring high-quality welds and reducing weld defects such as porosity, cavities or cracks, lack of fusion or lack of penetration.
Notwithstanding this process, each weld also underwent the required 100% nondestructive testing, having to pass either radiographic or ultrasonic testing. Radiographic testing checks for defects inside the weld, while ultrasonic testing allows for a full volumetric examination of the components.
“This labour-intensive process ensured that every weld and join would withstand the tough and rigorous environment in which the SMCP would be deployed,” she explains.
In addition, to withstand the exposure to the elements and harsh operational requirements, the steelwork was corrosion-protected and several coats of paint applied, to an industrial specification.
Africa Perspective
“Our successful collaboration with our client ThyssenKrupp, and supply to the end-client in Mozambique, demonstrates the Team Africa concept in action, whereby companies are able to form a cooperative and synergistic partnership. This includes supplying and processing steel, then fabricating and installing the finished structures,” Skjoldhammer says.
She notes that the Team Africa approach is an effective mechanism for the delivery of high-calibre pan-African infrastructure projects across a variety of industries.
Skjoldhammer adds that the seamless supply by Betterect’s Team Africa partner on this project, steel supplier Allied Steelrode, also contributed to the overall success of the project.
“This underlines that Betterect and its partners have a competitive advantage in undertaking projects in Africa for both local and international clients.”
ThyssenKrupp South Africa mining business project manager Jens Dombrowsky commends Betterect and its Team Africa collaboration for its high-quality work on this milestone project and for completing it within the allocated timeframe.
She says that the SMCP project is another pan-African infrastructure project that demonstrates the fact that when industrial suppliers truly collaborate, they can collectively drive economic growth.
The SMCP project was also nominated for the SAISC Steel Awards 2020, which will take place on October 15, 2020.
Comments
Press Office
Announcements
What's On
Subscribe to improve your user experience...
Option 1 (equivalent of R125 a month):
Receive a weekly copy of Creamer Media's Engineering News & Mining Weekly magazine
(print copy for those in South Africa and e-magazine for those outside of South Africa)
Receive daily email newsletters
Access to full search results
Access archive of magazine back copies
Access to Projects in Progress
Access to ONE Research Report of your choice in PDF format
Option 2 (equivalent of R375 a month):
All benefits from Option 1
PLUS
Access to Creamer Media's Research Channel Africa for ALL Research Reports, in PDF format, on various industrial and mining sectors
including Electricity; Water; Energy Transition; Hydrogen; Roads, Rail and Ports; Coal; Gold; Platinum; Battery Metals; etc.
Already a subscriber?
Forgotten your password?
Receive weekly copy of Creamer Media's Engineering News & Mining Weekly magazine (print copy for those in South Africa and e-magazine for those outside of South Africa)
➕
Recieve daily email newsletters
➕
Access to full search results
➕
Access archive of magazine back copies
➕
Access to Projects in Progress
➕
Access to ONE Research Report of your choice in PDF format
RESEARCH CHANNEL AFRICA
R4500 (equivalent of R375 a month)
SUBSCRIBEAll benefits from Option 1
➕
Access to Creamer Media's Research Channel Africa for ALL Research Reports on various industrial and mining sectors, in PDF format, including on:
Electricity
➕
Water
➕
Energy Transition
➕
Hydrogen
➕
Roads, Rail and Ports
➕
Coal
➕
Gold
➕
Platinum
➕
Battery Metals
➕
etc.
Receive all benefits from Option 1 or Option 2 delivered to numerous people at your company
➕
Multiple User names and Passwords for simultaneous log-ins
➕
Intranet integration access to all in your organisation