Custom chutes show their mettle with abrasive ore
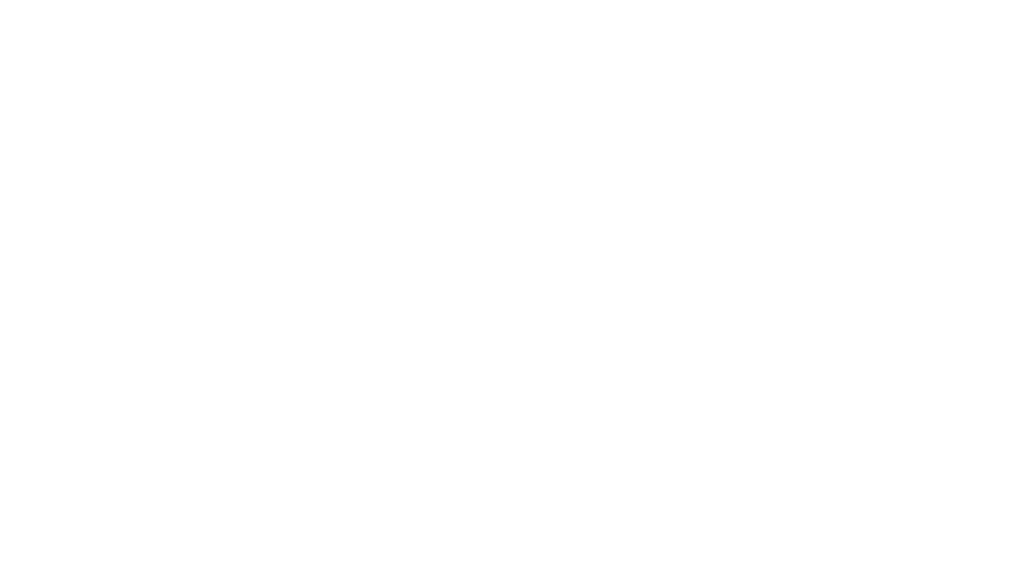
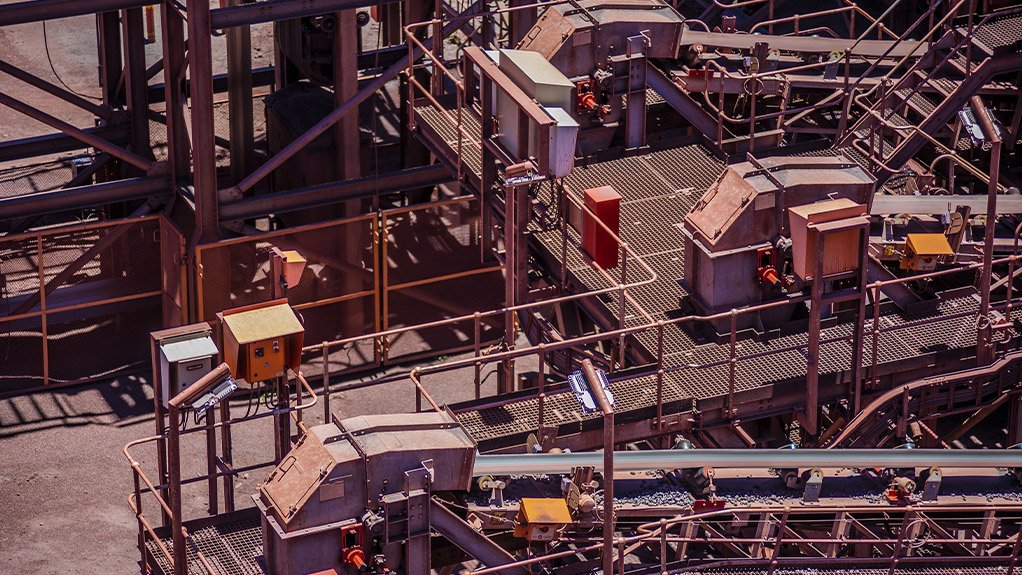
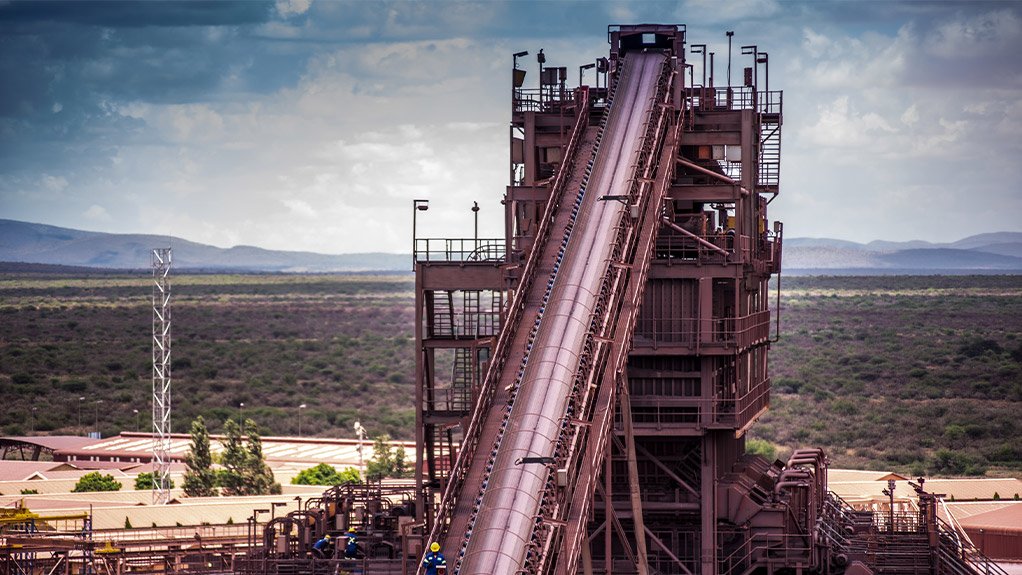
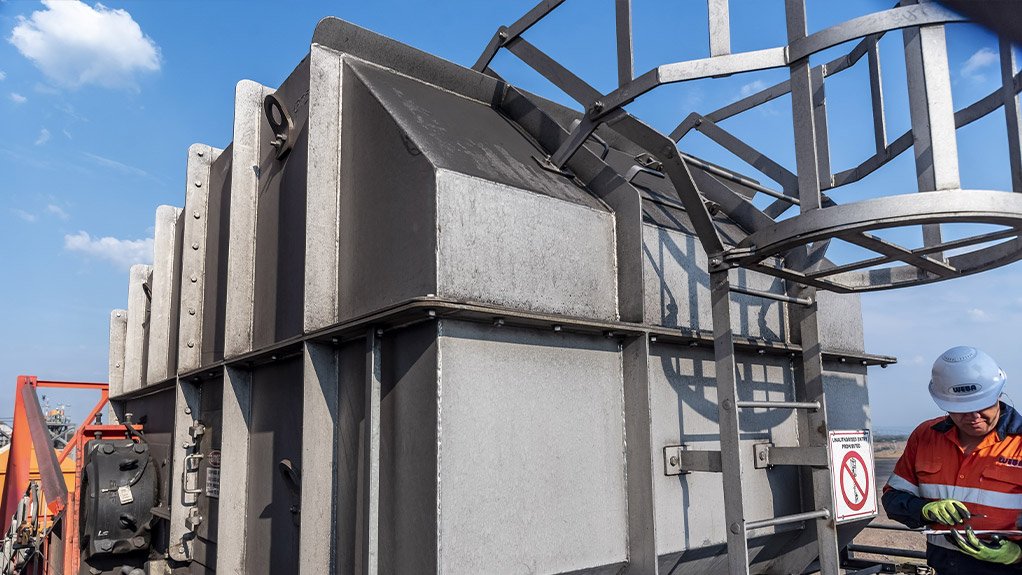
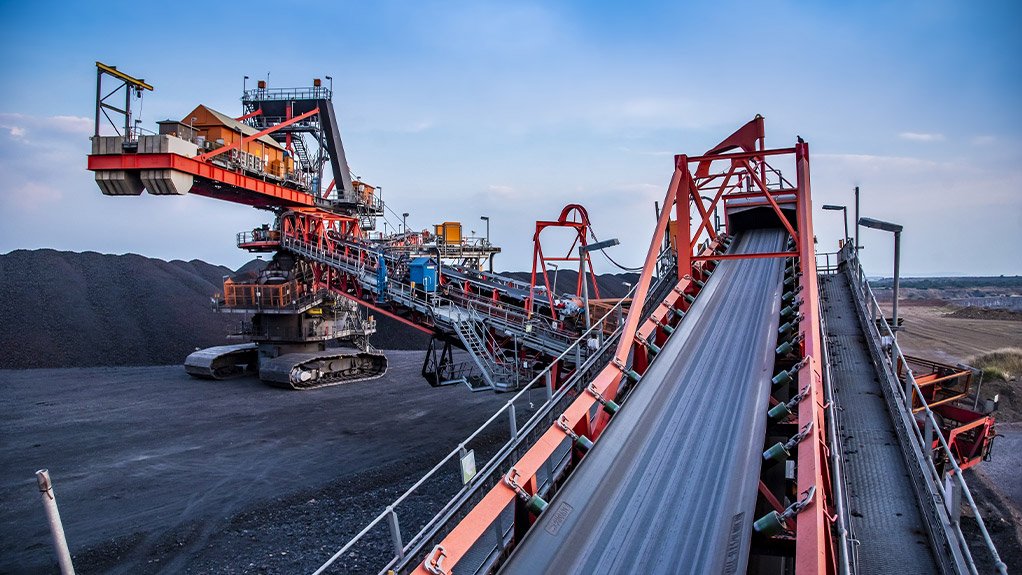
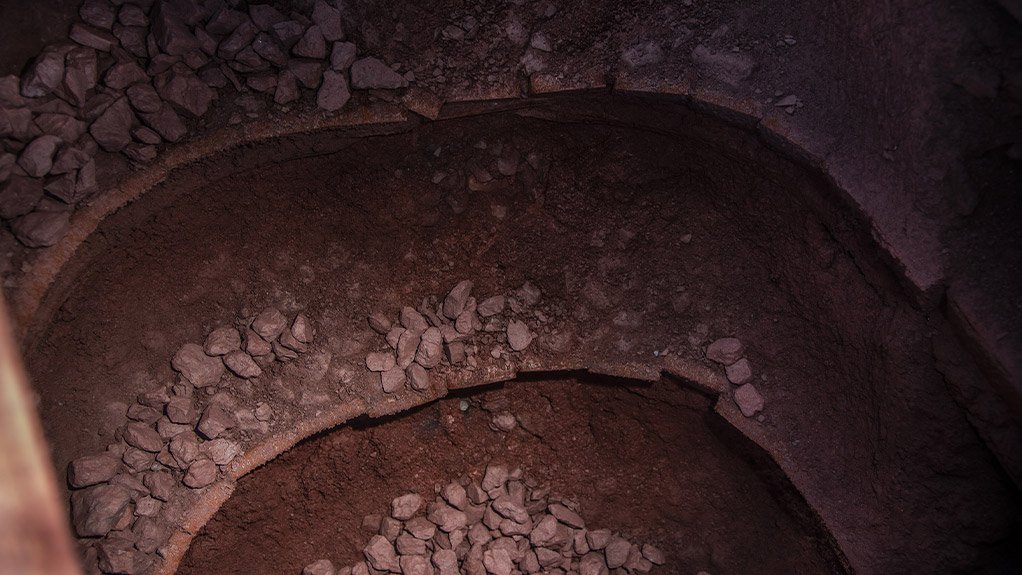
A Weba Chute Systems head chute, engineered to handle abrasive materials, reduce maintenance and extend service intervals with controlled material flow, in operation
Designed for demanding environments, Weba Chute Systems' conveyor belt setup feeds directly into a high performance transfer chute, enhancing throughput and protecting equipment from costly downtime
An expertly engineered Weba head chute designed to ensure optimal material through put while reducing wear and tear
Conveyor belts channel ore smoothly into a custom-designed Weba Chute ensuring controlled flow and minimal wear in abrasive conditions typical of Southern Africa's mining operations
Weba’s innovative chute design with dead boxes and lips traps material to create a protective buffer, significantly lowering wear on the chute's surface and extending equipment life in the mining sector
This article has been supplied.
With most of its 5,000-strong global footprint of transfer chutes being installed in Southern Africa, Johannesburg-based Weba Chute Systems has built a reputation in demanding mining conditions.
The region is a leading producer of platinum and manganese, for instance, which are both highly abrasive ores, points out Dewald Tintinger, Technical Manager at Weba Chute Systems. The company’s innovative approach and customised designs control material flow and resist wear, matching specific site conditions.
“First and foremost, a chute must facilitate optimal throughput so that mining production is not hampered by frequent blockages or repairs,” says Tintinger. “It is well known that the cost of a quality chute is a fraction of the cost of lost production through downtime.”
He highlights that Weba Chute Systems takes a systematic approach to assessing each customer’s requirements, starting with the general arrangement of the area around transfer points. The depth of experience accumulated over 40 years in business allows the company’s experts to suggest improvements to the layout – where these are possible and where they affect the chute performance.
“Then we consider a range of key factors like the material characteristics, the throughput tonnages and speed of travel, when we plan the design,” he says. “These considerations guide the application of our controlled flow philosophy.”
The design is built on scientific calculations using the anticipated trajectories, impacts and pressures on the structure. The main conceptual options are Weba’s Cascade Chute with dead boxes, the Weba Superflow chute with liners or a combination of both.
“A key element of our popular Cascade Chute is the use of dead boxes and lips on the inside of the structure, which traps material and allows other material to flow over it,” says Tintinger. “This ensures that up to 70% of the wear surface is protected by stationery material, which substantially reduces wear and maintenance costs while extending service intervals.”
As material enters the chute and flows through, it lands mainly on other material which absorbs the impact more effectively, protecting the underlying wear plates and structure from undue damage. This also reduces dust creation, he notes, which is an ongoing health and safety concern on mines.
“Controlling material flow through the right chute design also protects costly equipment like conveyor belts,” he says. In one example, Weba Chute Systems installed a cascade chute at a Southern African copper mine to better control the flow of material onto conveyor belts. This saved immediately on belt costs – while boosting productivity through improved uptime.
Comments
Press Office
Announcements
What's On
Subscribe to improve your user experience...
Option 1 (equivalent of R125 a month):
Receive a weekly copy of Creamer Media's Engineering News & Mining Weekly magazine
(print copy for those in South Africa and e-magazine for those outside of South Africa)
Receive daily email newsletters
Access to full search results
Access archive of magazine back copies
Access to Projects in Progress
Access to ONE Research Report of your choice in PDF format
Option 2 (equivalent of R375 a month):
All benefits from Option 1
PLUS
Access to Creamer Media's Research Channel Africa for ALL Research Reports, in PDF format, on various industrial and mining sectors
including Electricity; Water; Energy Transition; Hydrogen; Roads, Rail and Ports; Coal; Gold; Platinum; Battery Metals; etc.
Already a subscriber?
Forgotten your password?
Receive weekly copy of Creamer Media's Engineering News & Mining Weekly magazine (print copy for those in South Africa and e-magazine for those outside of South Africa)
➕
Recieve daily email newsletters
➕
Access to full search results
➕
Access archive of magazine back copies
➕
Access to Projects in Progress
➕
Access to ONE Research Report of your choice in PDF format
RESEARCH CHANNEL AFRICA
R4500 (equivalent of R375 a month)
SUBSCRIBEAll benefits from Option 1
➕
Access to Creamer Media's Research Channel Africa for ALL Research Reports on various industrial and mining sectors, in PDF format, including on:
Electricity
➕
Water
➕
Energy Transition
➕
Hydrogen
➕
Roads, Rail and Ports
➕
Coal
➕
Gold
➕
Platinum
➕
Battery Metals
➕
etc.
Receive all benefits from Option 1 or Option 2 delivered to numerous people at your company
➕
Multiple User names and Passwords for simultaneous log-ins
➕
Intranet integration access to all in your organisation