Coatings extend rotating equipment service life
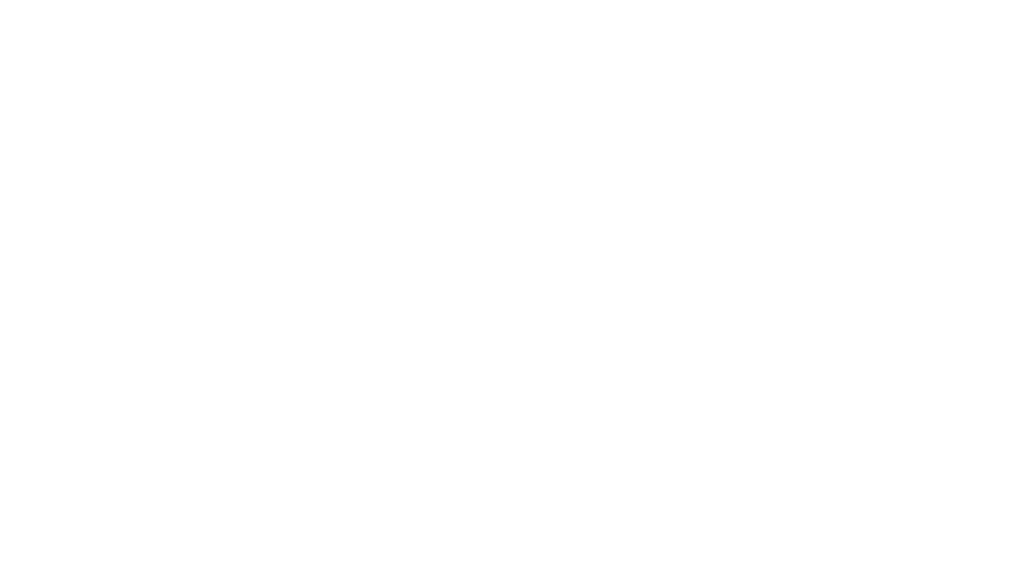
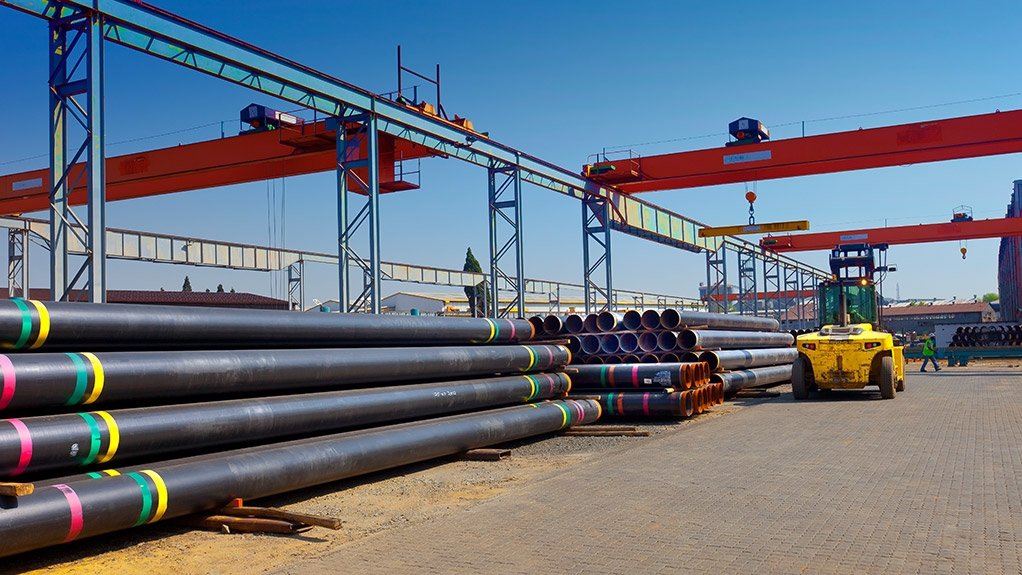
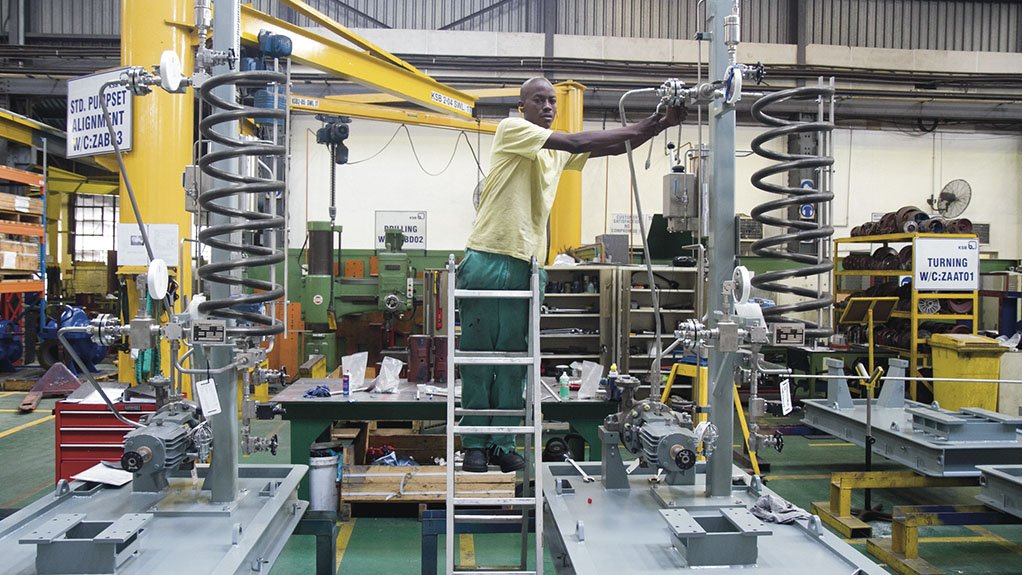
SURFACE COATING TECHNOLOGIES Offer massive improvements to the expected service life of compressors, turbines and pumps that are subject to surface oxidation, corrosion, erosion and heat damage.
Photo by Duane
PLANT OPERATORS They need to determine the various contributory factors and then employ the most appropriate technology available.
Photo by Duane
Rotating equipment manufacturer Sulzer says its latest surface coating technologies offer massive improvements to the expected service life of compressors, turbines and pumps that are subject to surface oxidation, corrosion, erosion and heat damage.
Sulzer's Houston Service Centre components superintendent Travis Cockrell explains that achieving long-term reliability requires a considered approach by plant operators, as they need to determine the various contributory factors and then employ the most appropriate technology available. “Rotating equipment that is in direct contact with the process media presents a major challenge. “However, it is possible to reduce degradation to a minimum by selecting the correct coating system.”
Cockrell states that, generally, turbines, compressors and pumps are subject to several environmental conditions that contribute to corrosion, erosion, fouling and various tempera- ture-related issues.
He notes that, once plant operators understand the machinery’s operating environment, they can then classify the sources of degradation and use specific coating systems to increase efficiencies, lengthen the interval between scheduled maintenance and reduce the occurrence of unscheduled maintenance events.
Pumps and compressors account for more than 20% of the world's electricity demand. Moreover, the energy costs incurred while operating them represent about 95% of a plant’s running costs. “It is, therefore, essential to reduce these costs by improving performance and efficiency, which will also [enhance] reliability and service life.”
Cockrell explains that corrosion occurs as a result of a chemical reaction between the component’s surface and the reacting fluid passing through. “Many metals form oxide layers that adhere to and passivate the surface to prevent further corrosion, but the change in the physical properties of the surface significantly increases the frictional properties.”
He comments that erosion is “generally” caused by solid particles passing through the equipment, affecting aerodynamic efficiencies significantly and leading to premature blade/vane replacement and failure.
Particulate fouling, on the other hand, results from the presence of small particles in the ingested air streams that can cause a distortion to the oncoming laminar flow. “This degrades flow capacity and can reduce the efficiency of the equipment in a short period of time,” Cockrell remarks.
Modern coating technology can be applied to legacy equipment, restoring and upgrading the equipment with greatly improved antifouling and corrosion resistance, he says, adding that implementing a new coating as part of a refurbishment project will significantly improve the performance and reliability of existing equipment.
“Oxidation- and corrosion-resistant coatings are usually aluminides applied using a variety of thermal spray or surface deposition techniques.”
Corrosion-resistant coatings also use an aluminium base coat that is designed to be conductive to allow for cathodic protection. “The aluminium becomes the sacrificial element and, therefore, protects the less active base-metal component. The electrons flow from the aluminium to the base substrate, which becomes negatively polarised and, therefore, protected against corrosion.”
Cockrell explains that the basic thermal spraying and physical or chemical vapour deposition techniques available allow for different coating thicknesses, but also have application restrictions. While spray techniques can be used to apply a thicker layer, they require a relatively flat surface and direct line of sight to accurately apply consistent coating thicknesses. Alternatively, the deposition techniques typically produce a thinner layer, but can coat more complex shapes more easily.
Cockrell notes that applications for these coatings include protection from wear, high tempera- tures or chemical attack, as well as provide a substitute for chromium, which can be hazardous in some states. Coatings can be metallic, ceramic or any combination required to meet a broad range of physical criteria.
For applications that require improved antifouling protection, Cockrell says, coatings can be applied to both stationary and rotating blades as well as diaphragms, guide vanes, rotors and impellers. “Coatings can be tailored to specific applications and include an aluminium base coat for corrosion protection as well as an inorganic sealer and a specialist nonstick final layer.”
These antifouling coatings have a thickness of between 75 µm and 125 µm and use poly- tetrafluoroethylene, which provides excellent chemical resistance in low to medium temperatures with a maximum operating temperature of about 287 °C.
Comments
Press Office
Announcements
What's On
Subscribe to improve your user experience...
Option 1 (equivalent of R125 a month):
Receive a weekly copy of Creamer Media's Engineering News & Mining Weekly magazine
(print copy for those in South Africa and e-magazine for those outside of South Africa)
Receive daily email newsletters
Access to full search results
Access archive of magazine back copies
Access to Projects in Progress
Access to ONE Research Report of your choice in PDF format
Option 2 (equivalent of R375 a month):
All benefits from Option 1
PLUS
Access to Creamer Media's Research Channel Africa for ALL Research Reports, in PDF format, on various industrial and mining sectors
including Electricity; Water; Energy Transition; Hydrogen; Roads, Rail and Ports; Coal; Gold; Platinum; Battery Metals; etc.
Already a subscriber?
Forgotten your password?
Receive weekly copy of Creamer Media's Engineering News & Mining Weekly magazine (print copy for those in South Africa and e-magazine for those outside of South Africa)
➕
Recieve daily email newsletters
➕
Access to full search results
➕
Access archive of magazine back copies
➕
Access to Projects in Progress
➕
Access to ONE Research Report of your choice in PDF format
RESEARCH CHANNEL AFRICA
R4500 (equivalent of R375 a month)
SUBSCRIBEAll benefits from Option 1
➕
Access to Creamer Media's Research Channel Africa for ALL Research Reports on various industrial and mining sectors, in PDF format, including on:
Electricity
➕
Water
➕
Energy Transition
➕
Hydrogen
➕
Roads, Rail and Ports
➕
Coal
➕
Gold
➕
Platinum
➕
Battery Metals
➕
etc.
Receive all benefits from Option 1 or Option 2 delivered to numerous people at your company
➕
Multiple User names and Passwords for simultaneous log-ins
➕
Intranet integration access to all in your organisation