Ensuring pump reliability in abrasive service
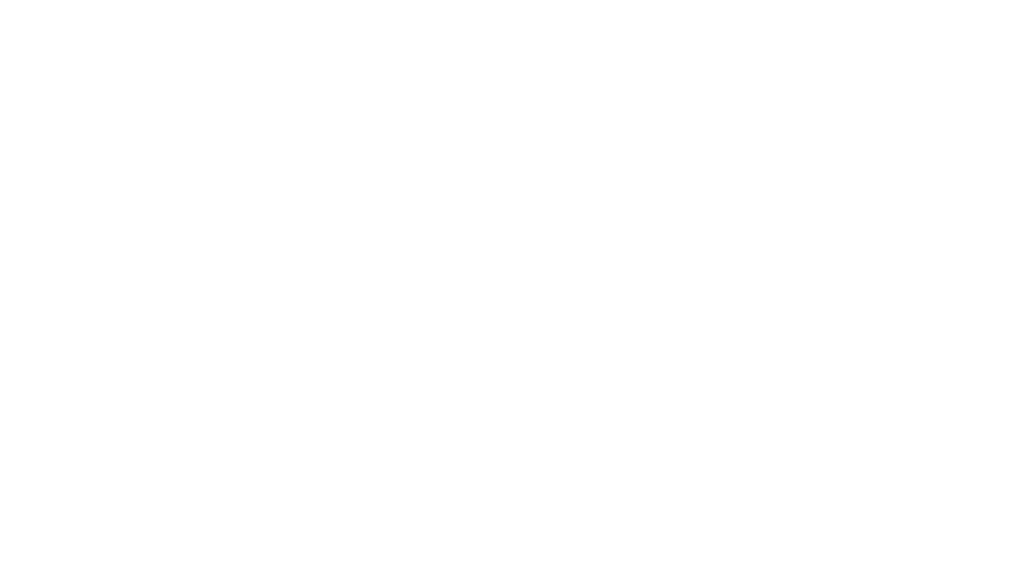
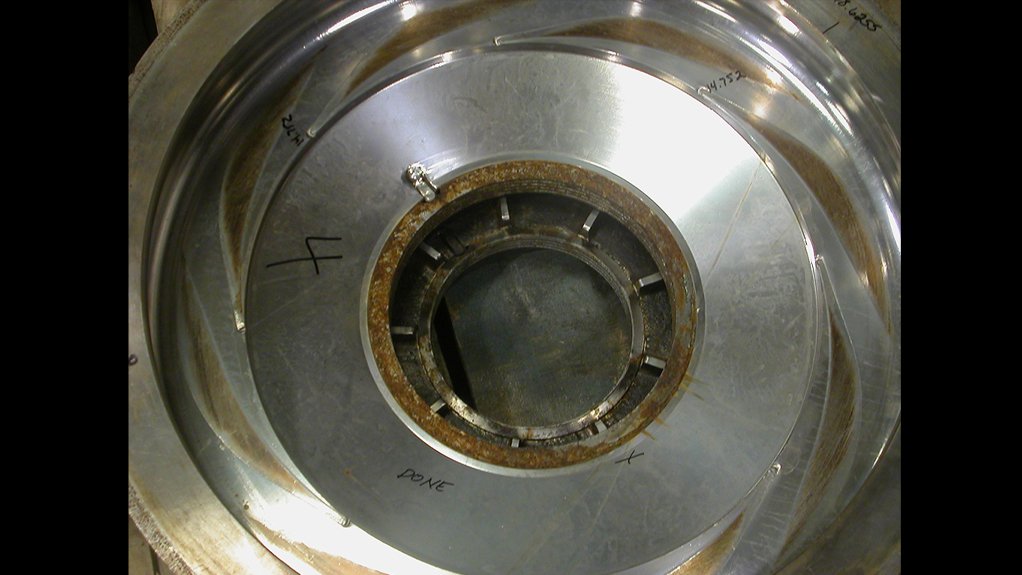
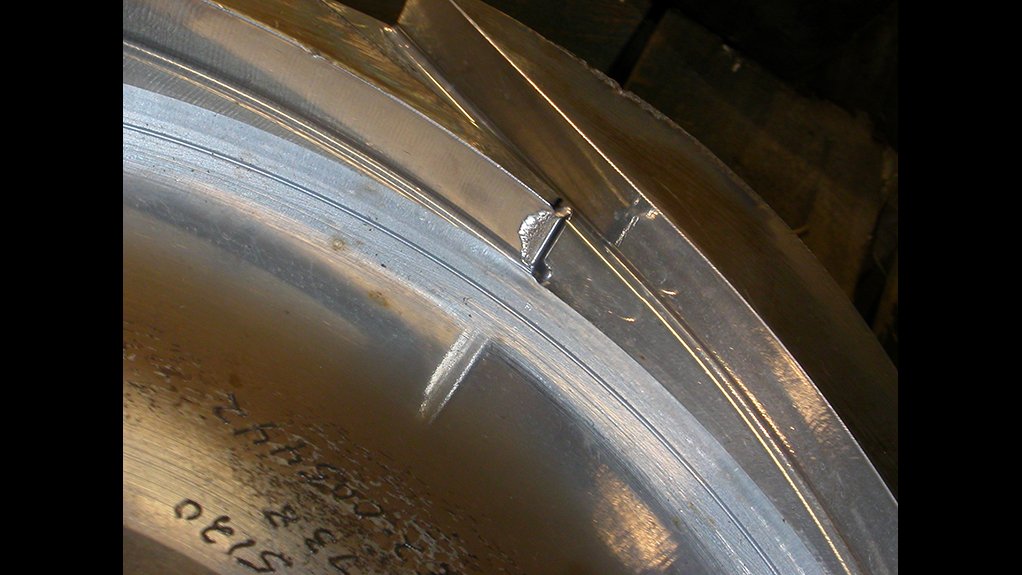
DESIGN CAPABILITIES The pumps responsible for delivering these materials are constantly under attack and their design directly affects their durability and efficiency
AS GOOD AS NEW To refurbish the pump shaft to original dimensions, it was rebuilt using the HVOF coating process
Maintaining and improving reliability of pumps used to transport abrasive media can be challenging in high-energy applications with players in the oil and gas industry aiming to optimise performance and minimise downtime.
Fluid engineering company Sulzer says these objectives can be met through planning maintenance and introducing modern materials technology to existing assets.
The company explains that refineries and oil and gas installations, both on and offshore, use high-energy pumps for various applications to deliver products at high flow rates and heads.
“Each application has its own challenges, especially those involving materials that cause erosion, corrosion or abrasion, whereby the pumps responsible for delivering these materials are under constant attack and their design directly affects their durability and efficiency.”
High-energy pumps use large electric motors that contribute significantly to an operation’s energy costs.
Improving energy efficiency can enable cost savings, but the company explains that more revenue is lost if production halts, owing to unplanned pump downtime.
While pump redundance is built into the design of production facilities, allowing assets to be maintained without affecting output, the frequency of these maintenance windows needs to be kept to a minimum to optimise running costs.
The company explains that adverse operating conditions can lead to excessive wear and erosion which needs frequent remediation – sometimes every few months – which can encourage lead operators to review the pumps’ design and compare costs of maintenance against a new asset that could offer improved reliability and efficiency.
Additionally, capital expenditure and downtime incurred during installation of new pump assets, that may have differing foundation and piping requirements, can halt efforts to improve equipment availability.
“There is a middle ground to consider where existing designs are assessed and upgraded to improve durability while also reducing maintenance costs. Better still, this option will be considerably cheaper than investing in a new asset which may not be as appropriately designed.”
Long-Term Solutions
The company says that understanding the cause of problems in pumps can allow for the delivering of a long-term solution.
For example, greater durability can be achieved through adding specialist coatings which can improve performance and reliability should they be applied by specialists.
For applications designed to improve wear and corrosion resistance, high velocity oxygen fuel (HVOF) coatings are commonly used.
Sulzer explains that different coatings have varied bonding properties with different substrates, making it essential to understand the conditions required to achieve a perfect bond.
A coatings bond is one of the most critical aspects of success and it should be in focus during all processes associated with coating.
“In every refurbishment project, establishing the process specifications is essential to the long-term success and durability of the coating. “This involves detailing the approved equipment and process parameters as well as the properties required for the coating acceptance, such as its tensile strength, microstructure characteristics, hardness and surface roughness values.”
By inspecting the microstructure and mechanical properties of the coating, it is possible to verify that it was applied to required specifications, and that it will provide all the expected benefits in operation.
There are many pumping applications in the oil and gas sector involving fluids that contain abrasive media.
Sulzer explains that unless the pumps are designed and constructed to handle these challenging conditions, the reliability of this equipment can be substantially affected.
Further, changes in process parameters and applications can cause legacy equipment to be adversely affected and without specialist intervention or complete replacement the maintenance costs can increase dramatically.
High energy pumps represent a considerable investment and they are expected to deliver efficient and reliable service, even in challenging environments.
By working with a partner that has the expertise and facilities of an original-equipment manufacturer, operators can benefit from a vast reserve of knowledge.
Experienced assessment coupled with expert design analysis enable improvements in durability and reliability to be applied to high-energy pumps. These cost-effective solutions represent an ideal opportunity to extend service life and minimise operating costs
.
“Our customers benefit from our commitment to innovation, performance and quality and from our responsive network of 180 world-class production facilities and service centres across the globe,” concludes Sulzer.
Comments
Press Office
Announcements
What's On
Subscribe to improve your user experience...
Option 1 (equivalent of R125 a month):
Receive a weekly copy of Creamer Media's Engineering News & Mining Weekly magazine
(print copy for those in South Africa and e-magazine for those outside of South Africa)
Receive daily email newsletters
Access to full search results
Access archive of magazine back copies
Access to Projects in Progress
Access to ONE Research Report of your choice in PDF format
Option 2 (equivalent of R375 a month):
All benefits from Option 1
PLUS
Access to Creamer Media's Research Channel Africa for ALL Research Reports, in PDF format, on various industrial and mining sectors
including Electricity; Water; Energy Transition; Hydrogen; Roads, Rail and Ports; Coal; Gold; Platinum; Battery Metals; etc.
Already a subscriber?
Forgotten your password?
Receive weekly copy of Creamer Media's Engineering News & Mining Weekly magazine (print copy for those in South Africa and e-magazine for those outside of South Africa)
➕
Recieve daily email newsletters
➕
Access to full search results
➕
Access archive of magazine back copies
➕
Access to Projects in Progress
➕
Access to ONE Research Report of your choice in PDF format
RESEARCH CHANNEL AFRICA
R4500 (equivalent of R375 a month)
SUBSCRIBEAll benefits from Option 1
➕
Access to Creamer Media's Research Channel Africa for ALL Research Reports on various industrial and mining sectors, in PDF format, including on:
Electricity
➕
Water
➕
Energy Transition
➕
Hydrogen
➕
Roads, Rail and Ports
➕
Coal
➕
Gold
➕
Platinum
➕
Battery Metals
➕
etc.
Receive all benefits from Option 1 or Option 2 delivered to numerous people at your company
➕
Multiple User names and Passwords for simultaneous log-ins
➕
Intranet integration access to all in your organisation