Global shift to Weba Chute Systems represents greater efficiency
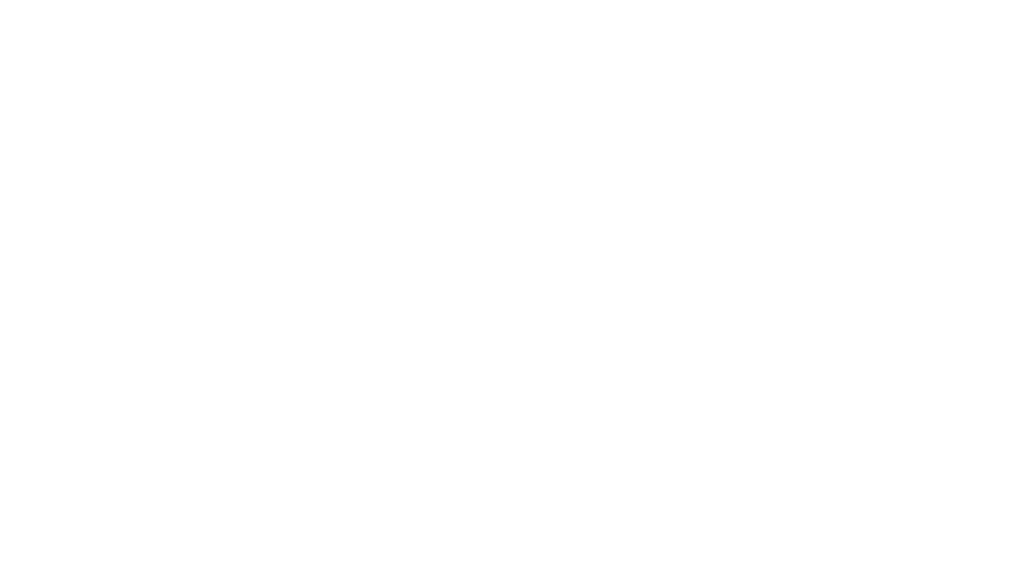
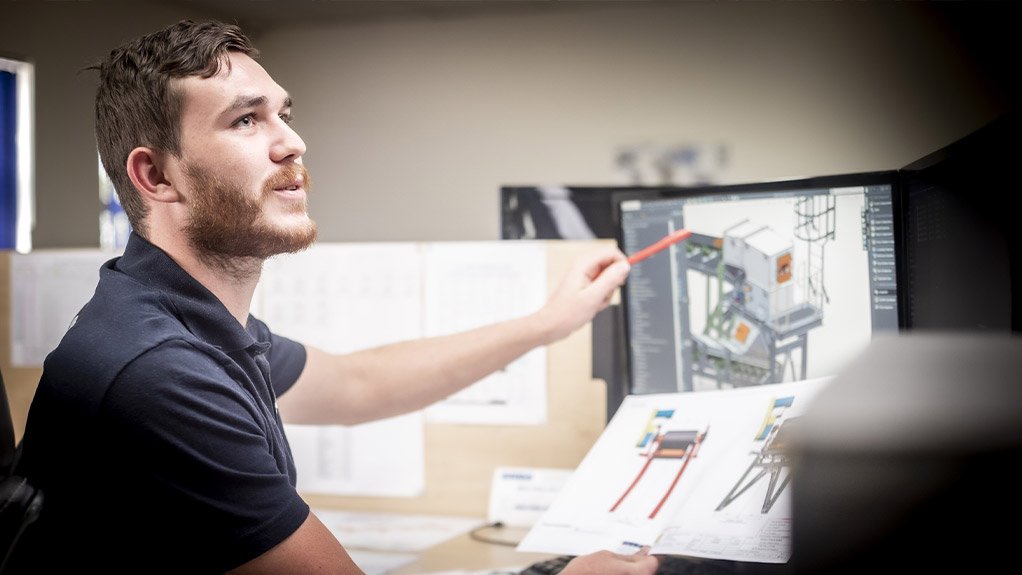
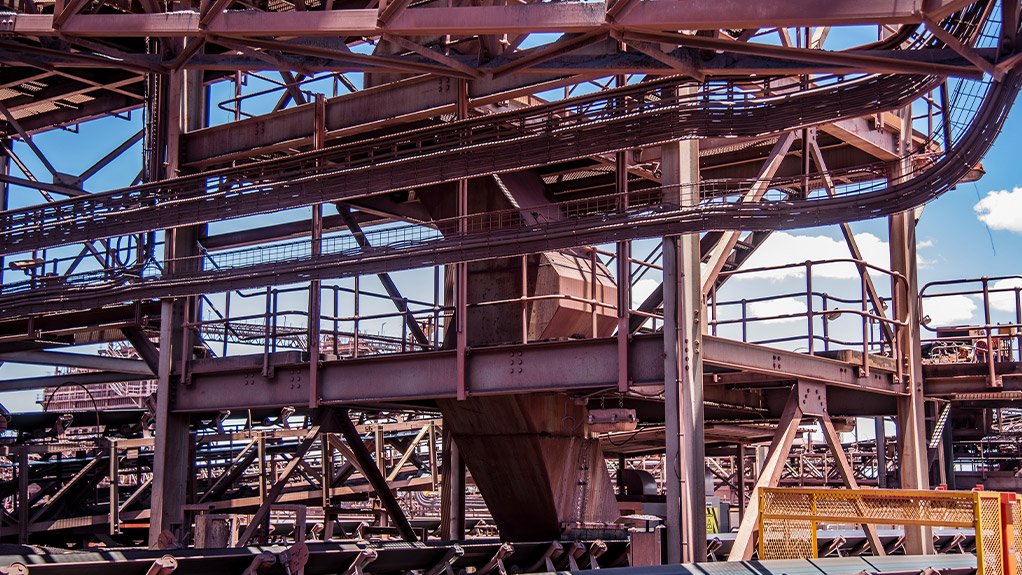
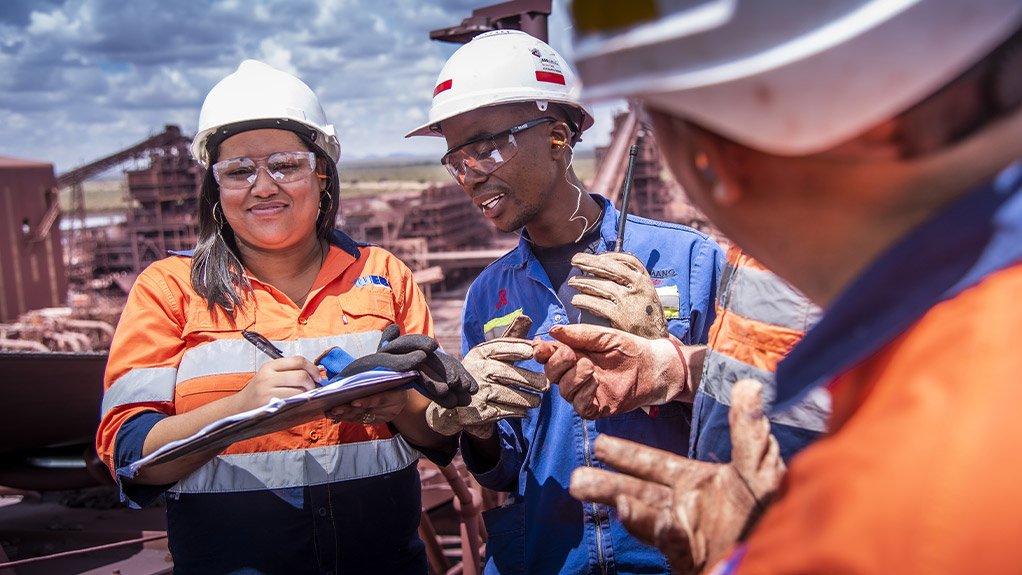
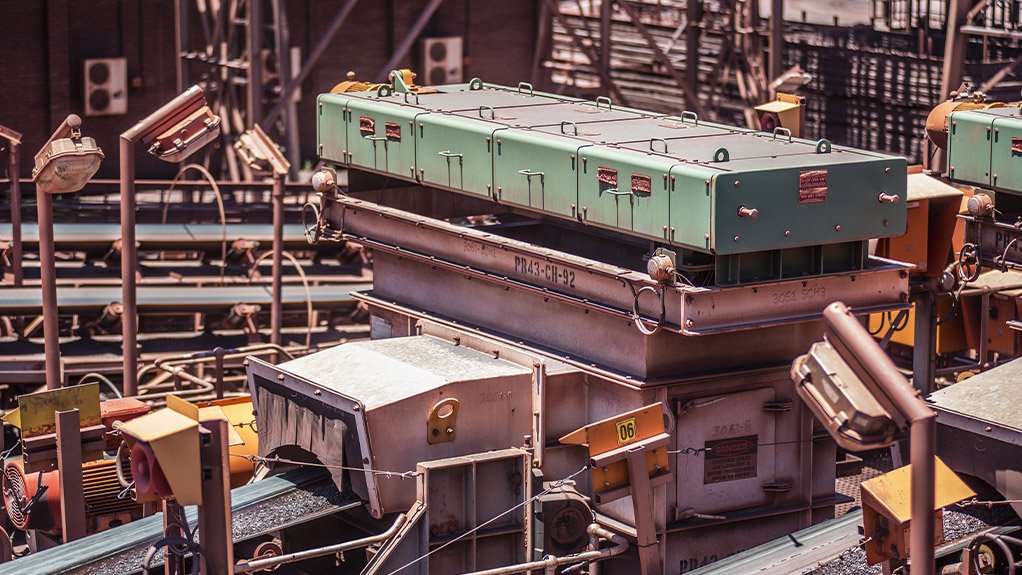

Experienced Weba Chute Systems draughtsman comparing drawings with the 3D model
A Weba conveyor onto conveyor transfer chute at an iron ore mine
Weba Chute Systems site team consulting with the customer at an iron ore mine
A Weba bucket elevator transfer chute at an iron ore mine
Weba conveyor onto conveyor transfer chutes at an iron ore mine
This article has been supplied.
In bulk materials handling applications, the uncontrolled discharge from conventional chutes can lead to increased maintenance and replacement costs, as well as decreased productivity. Recognising these challenges, companies around the world, both large and small, have adopted Weba Chute Systems, a choice which represents a shift towards greater efficiency and less downtime.
Mark Baller, CEO of Weba Chute Systems, explains that there is a growing consensus across the globe that incorporating custom-engineered transfer chutes is paramount. “There are still some that overlook the significance of transfer points that are engineered for specific application requirements, ranking them below screens, crushers or feeders in the process hierarchy."
Baller points out a critical misconception that undermines operational efficiency: the notion that initial savings from inexpensive inferior chutes outweigh long term costs. "This approach is flawed," he argues, "as it inevitably leads to higher operational expenditure due to frequent maintenance, and in some cases unscheduled downtime."
Highlighting the benefits of custom-designed solutions, Baller notes, "Proper initial design significantly lowers maintenance needs, improves material transfer, extends conveyor belt lifespan and boosts throughput. Moreover, our chutes are engineered to minimise environmental impact, reducing airborne dust and enhancing workplace health and safety."
The Weba Chute Systems team, armed with extensive field experience and intellectual resources built up over decades of operation, approaches each project with bespoke solutions aimed at maximising return on investment. "Engaging with our clients during the design phase is crucial for tailoring solutions that not only meet but exceed expectations, and this includes both new transfer points as well as retrofits," he continues.
Baller also sheds light on the pitfalls of retrofitting poorly designed chutes. "Correcting failures post-implementation is far from ideal. Opting for a sound design from the start eliminates such challenges, however we are often called upon to solve issues caused by poor decision making and this is where we are able to tailor make a chute system to deal with whatever challenge the customer is facing, " he says.
Leveraging Discrete Element Modelling (DEM) for validation, Weba Chute Systems prides itself on its engineering acumen. "DEM complements our vast engineering experience, ensuring that our transfer chutes excel in performance and durability," Baller says.
Baller emphasises that Weba Chute Systems stands out from general fabricators, and says that the company's proficiency goes beyond just designing transfer points. “Our team specialises in providing tailor-made solutions that improve materials handling, reduce maintenance needs and lead to considerable financial savings. The company’s dedication to high quality service is reflected in the positive feedback from customers and their achievements in operational efficiency,” he concludes.
Comments
Press Office
Announcements
What's On
Subscribe to improve your user experience...
Option 1 (equivalent of R125 a month):
Receive a weekly copy of Creamer Media's Engineering News & Mining Weekly magazine
(print copy for those in South Africa and e-magazine for those outside of South Africa)
Receive daily email newsletters
Access to full search results
Access archive of magazine back copies
Access to Projects in Progress
Access to ONE Research Report of your choice in PDF format
Option 2 (equivalent of R375 a month):
All benefits from Option 1
PLUS
Access to Creamer Media's Research Channel Africa for ALL Research Reports, in PDF format, on various industrial and mining sectors
including Electricity; Water; Energy Transition; Hydrogen; Roads, Rail and Ports; Coal; Gold; Platinum; Battery Metals; etc.
Already a subscriber?
Forgotten your password?
Receive weekly copy of Creamer Media's Engineering News & Mining Weekly magazine (print copy for those in South Africa and e-magazine for those outside of South Africa)
➕
Recieve daily email newsletters
➕
Access to full search results
➕
Access archive of magazine back copies
➕
Access to Projects in Progress
➕
Access to ONE Research Report of your choice in PDF format
RESEARCH CHANNEL AFRICA
R4500 (equivalent of R375 a month)
SUBSCRIBEAll benefits from Option 1
➕
Access to Creamer Media's Research Channel Africa for ALL Research Reports on various industrial and mining sectors, in PDF format, including on:
Electricity
➕
Water
➕
Energy Transition
➕
Hydrogen
➕
Roads, Rail and Ports
➕
Coal
➕
Gold
➕
Platinum
➕
Battery Metals
➕
etc.
Receive all benefits from Option 1 or Option 2 delivered to numerous people at your company
➕
Multiple User names and Passwords for simultaneous log-ins
➕
Intranet integration access to all in your organisation