High efficiency key to production facility’s expansion
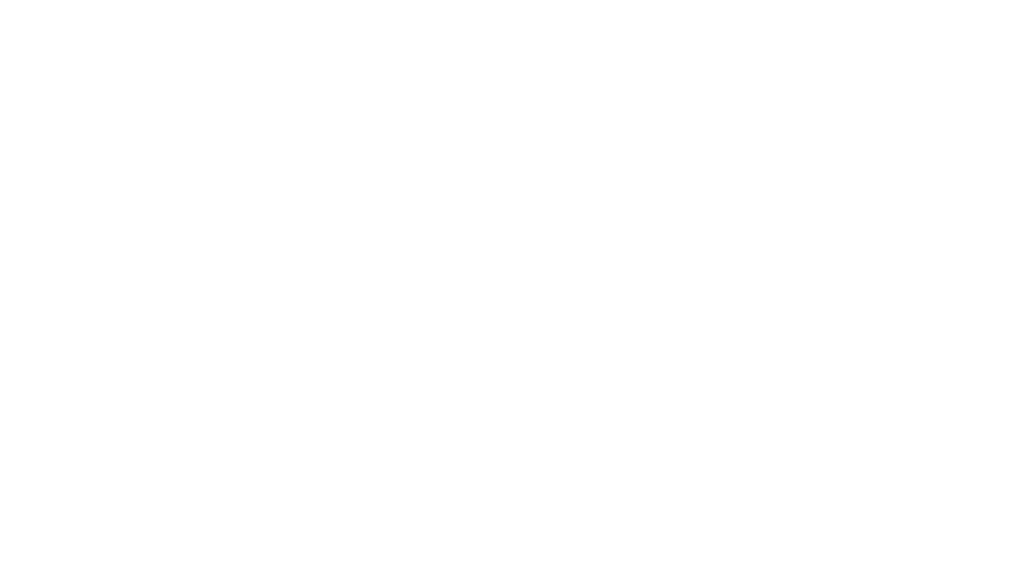
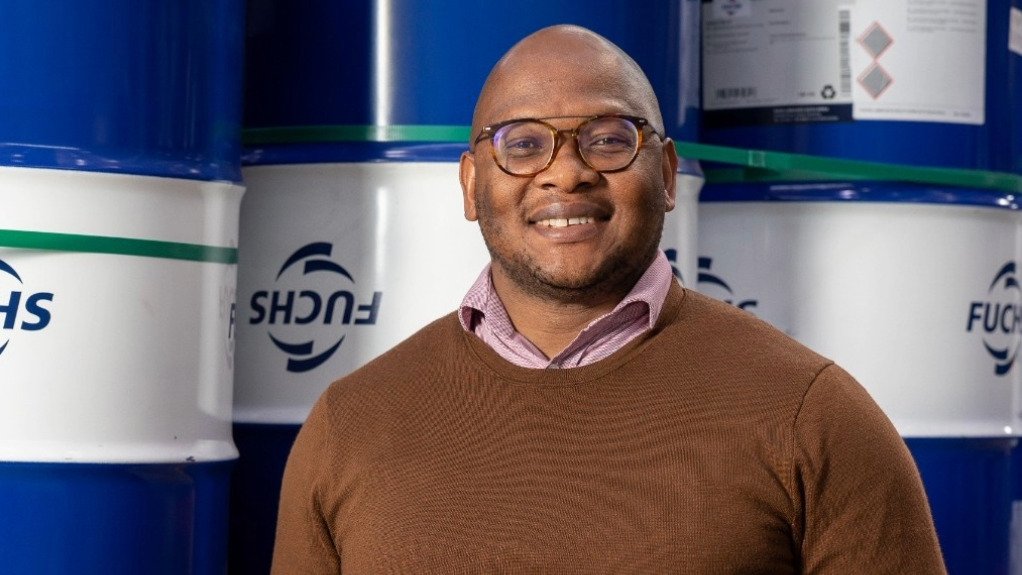
THAMI MZOLO On top of these new developments, FUCHS is working to ensure that the existing plant continues to deliver high-quality products to customers when they need them
Leading lubricants manufacturer and supplier FUCHS LUBRICANTS South Africa introduced customers to its new expanded Isando, Ekurhuleni facility during a customer day in February.
FUCHS LUBRICANTS South Africa manufacturing executive Thami Mzolo, who has been involved with the project since joining the company in early 2024, comments that it is the most efficient plant build and upgrade in which he has been involved.
“We contracted out the engineering, procurement and construction management project to [multidisciplinary engineering firm] DRA Global and [it] did a fantastic job in terms of attention to detail on the design and execution, to the extent that we commissioned the plant a full month ahead of schedule. Since commissioning, we have achieved a 100% right-first-time manufacturing result in the new plant.”
FUCHS embarked on the second round of its investment strategy, ‘Creating Capacity’, in mid-2020, explains FUCHS LUBRICANTS South Africa MD Paul Deppe.
“We purchased neighbouring land and, as [part of] Phase 1 of the project, we built a new warehouse and head office in Isando, both completed at the end of 2022. The new warehouse is 4.5 times larger than the old one, significantly reducing congestion and improving storage for raw materials, packaging, and finished goods,” says Deppe.
“The aim of the customer day was to showcase our new facilities and increased capacity. As the leading independent lubricants manufacturer, this will unlock significant opportunities and markets for us,” comments Deppe. “It was not just the actual technology we showcased, but also the level of control, automation, and integration with our new SAP enterprise resource planning (ERP) system.”
Now that the expanded facility is up and running, Mzolo’s mission is to maintain flexibility while taking advantage of the new plant’s high efficiencies and ensure FUCHS meets its commitment to provide quick turnarounds. “The focus now is to look at further operational efficiencies in our processes to unlock more capacity and enhance our flexibility by removing inefficiency and waste,” says Mzolo.
The aim of the project was to move the high-volume, fast-moving, large-batch products out of the existing plant. “State-of-the-art technology” has been incorporated into the new tank farm, blending plant and filling lines, while the existing plant remains operational.
Mzolo highlights the new plant boasts a 40% increase in available manufacturing capacity. “This means that we are geared to capture future business seamlessly and are prepared to grow with our customers.” The new plant comprises three blending vessels, five base oil tanks and two additive vessels, adding an extra 300 000 ℓ of blending capacity.
In addition to the blending capacity, the plant boasts a massive 1.3-million litres of base oil storage and 120 000 ℓ of additive storage. The blending process is fully automated, with a control system seamlessly integrated into the SAP ERP system. “This ensures precise dosing and consistent processing of materials, maintaining the high-quality standards FUCHS’s customers have come to expect.”
Three new “state-of-the-art” filling lines have also been introduced which significantly increases the capacity for filling of intermediate bulk containers (IBCs), drums, pails and small packs – typically 1 ℓ and 5 ℓ pack sizes. Bulk line filling is fully automated using loadcells to ensure the correct quantity is filled every time, and both drums and IBCs can be packed interchangeably. The new 20 ℓ pail line, also using loadcells for the filling, has a vision system to ensure correct labelling and a cap sensor that ensures good quality product at the end of the line.
The small pack line features ten modular stations, eight of which are fully automated. This line runs both 1 ℓ and 5 ℓ products interchangeably, depending on the product configuration. The latest quality assurance technology includes sensors to prevent leaking bottles and a checkweigher to ensure there are no missing packs in the cases.
“On top of these new developments, we are working hard to ensure that the existing plant continues to deliver high-quality products to customers when they need them,” says Mzolo. The lubes filling plant comprises ten filling lines, namely three drum lines, three 20 ℓ lines, one IBC line, and two small pack lines, including the new small pack line.
On the other side of the facility is the grease plant that was commissioned in 2018. It has been instrumental in supplying high-performance grease products to customers across diverse industries. Mzolo says that its “robust systems and well-trained staff” ensure consistent production and quality. Further, “grease plant capacity can be increased by 25% by introducing an additional shift, which demonstrates its ability to meet future demand”.
He comments that demand for specialty greases is growing significantly, which means that FUCHS’s expanded grease plant is ideally positioned to supply customers with products that meet stringent quality and performance standards. “It is a testament to our commitment to innovation and production excellence that we are able to comfortably meet this increased demand,” says Mzolo. “The overall expansion ensures we continue to lead in the industry, delivering quality and value in an efficient and sustainable way at every level.”
Comments
Press Office
Announcements
What's On
Subscribe to improve your user experience...
Option 1 (equivalent of R125 a month):
Receive a weekly copy of Creamer Media's Engineering News & Mining Weekly magazine
(print copy for those in South Africa and e-magazine for those outside of South Africa)
Receive daily email newsletters
Access to full search results
Access archive of magazine back copies
Access to Projects in Progress
Access to ONE Research Report of your choice in PDF format
Option 2 (equivalent of R375 a month):
All benefits from Option 1
PLUS
Access to Creamer Media's Research Channel Africa for ALL Research Reports, in PDF format, on various industrial and mining sectors
including Electricity; Water; Energy Transition; Hydrogen; Roads, Rail and Ports; Coal; Gold; Platinum; Battery Metals; etc.
Already a subscriber?
Forgotten your password?
Receive weekly copy of Creamer Media's Engineering News & Mining Weekly magazine (print copy for those in South Africa and e-magazine for those outside of South Africa)
➕
Recieve daily email newsletters
➕
Access to full search results
➕
Access archive of magazine back copies
➕
Access to Projects in Progress
➕
Access to ONE Research Report of your choice in PDF format
RESEARCH CHANNEL AFRICA
R4500 (equivalent of R375 a month)
SUBSCRIBEAll benefits from Option 1
➕
Access to Creamer Media's Research Channel Africa for ALL Research Reports on various industrial and mining sectors, in PDF format, including on:
Electricity
➕
Water
➕
Energy Transition
➕
Hydrogen
➕
Roads, Rail and Ports
➕
Coal
➕
Gold
➕
Platinum
➕
Battery Metals
➕
etc.
Receive all benefits from Option 1 or Option 2 delivered to numerous people at your company
➕
Multiple User names and Passwords for simultaneous log-ins
➕
Intranet integration access to all in your organisation