Hydrogen-ready furnace aims to cut smelter emissions
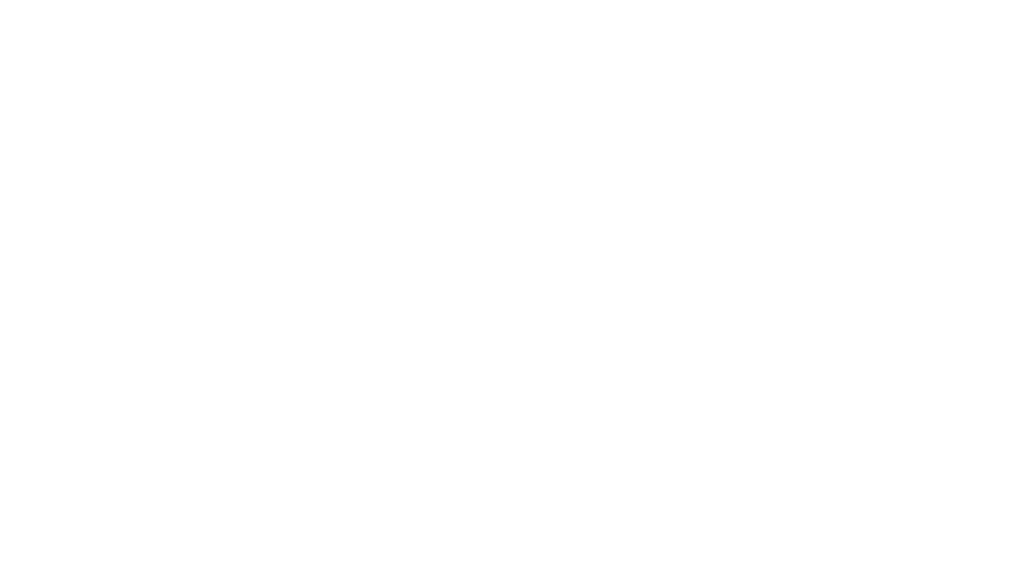
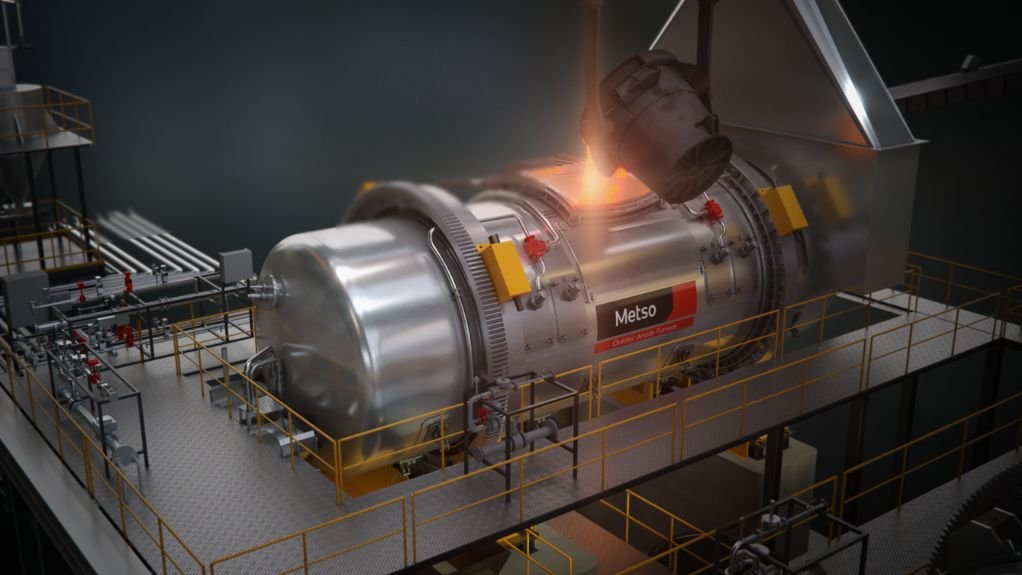
SUSTAINABILITY COMMITMENT Metso initiated the design and development of its own anode furnace as part of its broader commitment to sustainability
A new modernised hydrogen-ready anode furnace was launched to the market in December 2024 by Finnish industrial machinery manufacturer Metso to improve impurity removal and offer innovative reductant options to reduce emissions.
The Outotec Anode Furnace has been designed to reduce CO2 emissions during copper smelting, while also offering increased flexibility in processing various secondary materials.
“Raw materials pose both great challenges and opportunities for copper smelters today. Whether it is bringing in new primary concentrates, utilising existing ones with degrading quality or integrating secondary raw materials into existing processes, the demand for flexibility in the unit processes is growing,” says Metso anode casting and anode furnace technologies senior sales manager Miikka Marjakoski.
At the same time, he says smelters are looking to identify potential reduction sources for greenhouse gas (GHG) emissions, while the evolving raw material base is not making this paramount task easier.
The upgraded anode furnace features the latest design, advances in process safety and ease of maintenance.
It also presents two methods for reducing CO2 emissions through either direct hydrogen reduction in the hydrogen-ready (H2-ready) variant or through a steam-gas reduction system.
“The process is fully prepared to use direct hydrogen reduction in the H2-ready variant. However, if the customer has no opportunity to switch to hydrogen use at present, Metso can also provide the technology to significantly increase the current gaseous hydrocarbon reductant efficiency with a steam-gas reduction system,” says Marjakoski.
When combining this with oxyfuel combustion at the burners, he says, the total reduction in CO2 emissions is demonstrably significant compared with traditional processes, which has also been proved through lifecycle assessment calculations.
The anode furnace delivery scope consists of all key equipment required for operating the furnace, while Metso’s holistic competence in smelter process optimisation and integration of automation systems ensures that the furnace will be seamlessly integrated into the processing chain in both brownfield and greenfield applications.
When combined with services and onsite support, a smooth commissioning and startup is ensured, notes Metso.
Metso’s anode furnaces feature a furnace mouth that is fitted with cooling elements for longer lifetime and easy cleaning of mouth area. The furnaces also include riding rings that are fastened with a patented fastening system to reduce thermal stress, while tuyeres use a sturdy inner/outer pipe design to allow for longer pipe lifetime and easy exchange of pipes. In addition, the company’s anode furnaces also involve a drive unit that features complete redundancy for operational security, an integrated battery-based uninterruptable power supply system and a wide range of operational speed adjustment to serve different process phases. Mechanical stoppers on the rings of the anode furnaces prevent high-consequence leaks to factory floor by stopping freefall movement, while the Outotec Scrap Melting Furnace features additional hatches and burners for higher treatment capacity of high-grade copper.Meanwhile, Metso’s Scrap Melting Furnace variant of the anode furnace presents an opportunity to treat a substantial amount of secondary raw materials by using integrated burners for melting purposes.
The Outotec Scrap Melting Furnace yields great flexibility in treating any mixture of molten copper from upstream processes and high-grade secondary copper feed directly into the anode furnace, explains Marjakoski.
He adds that it can be used as a standalone melting furnace using solely secondary raw materials, making the product a “go-to choice for primary and secondary smelters alike”.
Comments
Press Office
Announcements
What's On
Subscribe to improve your user experience...
Option 1 (equivalent of R125 a month):
Receive a weekly copy of Creamer Media's Engineering News & Mining Weekly magazine
(print copy for those in South Africa and e-magazine for those outside of South Africa)
Receive daily email newsletters
Access to full search results
Access archive of magazine back copies
Access to Projects in Progress
Access to ONE Research Report of your choice in PDF format
Option 2 (equivalent of R375 a month):
All benefits from Option 1
PLUS
Access to Creamer Media's Research Channel Africa for ALL Research Reports, in PDF format, on various industrial and mining sectors
including Electricity; Water; Energy Transition; Hydrogen; Roads, Rail and Ports; Coal; Gold; Platinum; Battery Metals; etc.
Already a subscriber?
Forgotten your password?
Receive weekly copy of Creamer Media's Engineering News & Mining Weekly magazine (print copy for those in South Africa and e-magazine for those outside of South Africa)
➕
Recieve daily email newsletters
➕
Access to full search results
➕
Access archive of magazine back copies
➕
Access to Projects in Progress
➕
Access to ONE Research Report of your choice in PDF format
RESEARCH CHANNEL AFRICA
R4500 (equivalent of R375 a month)
SUBSCRIBEAll benefits from Option 1
➕
Access to Creamer Media's Research Channel Africa for ALL Research Reports on various industrial and mining sectors, in PDF format, including on:
Electricity
➕
Water
➕
Energy Transition
➕
Hydrogen
➕
Roads, Rail and Ports
➕
Coal
➕
Gold
➕
Platinum
➕
Battery Metals
➕
etc.
Receive all benefits from Option 1 or Option 2 delivered to numerous people at your company
➕
Multiple User names and Passwords for simultaneous log-ins
➕
Intranet integration access to all in your organisation