Lubricant range meets evolving die-casting needs
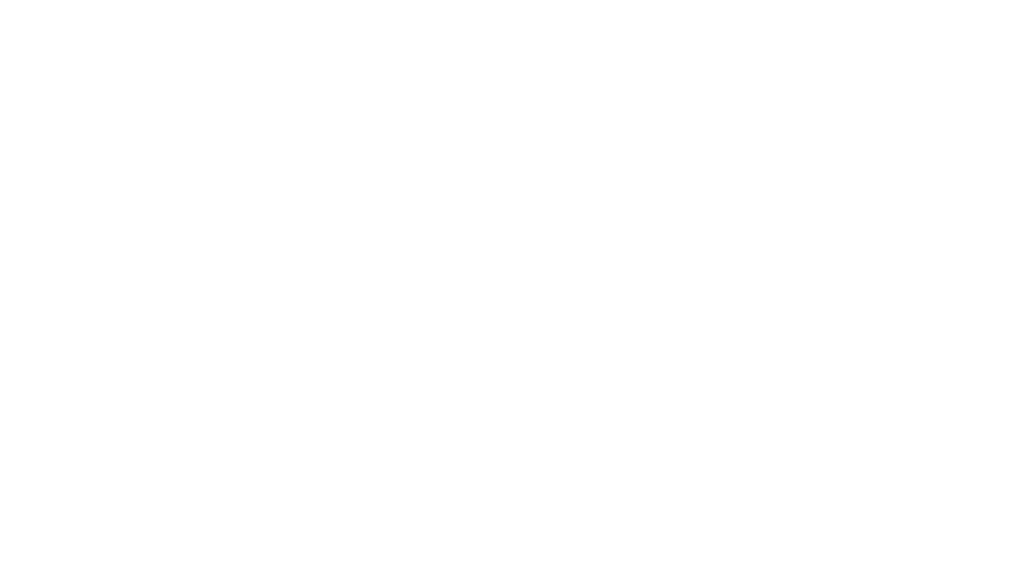
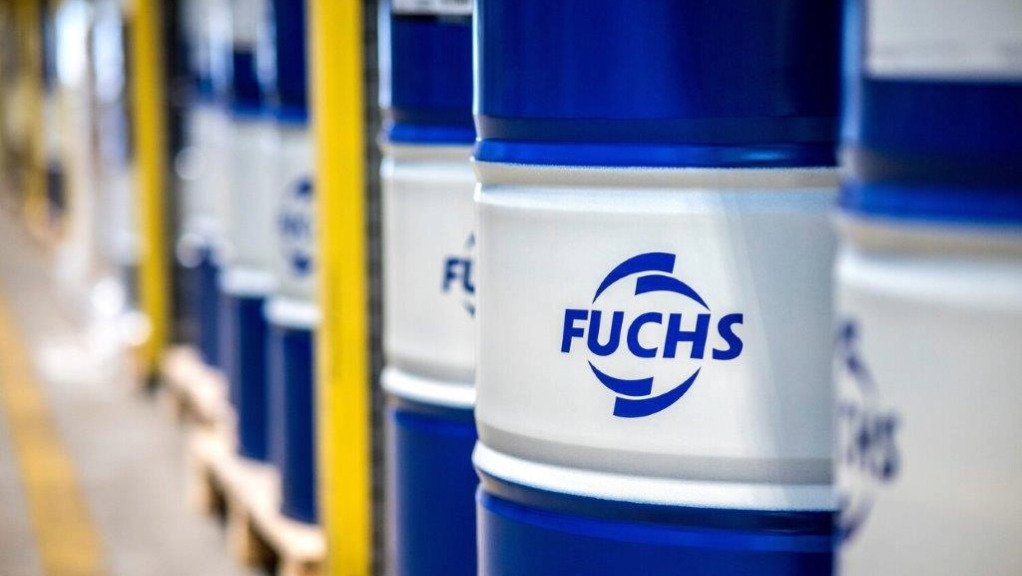
APPROPRIATE PRODUCT FUCHS ensures that their product innovations meet the evolving demands of the die casting sector
The evolving demands of the South African die-casting sector necessitate that lubricants manufacturer FUCHS Lubricants South Africa undertake continuous product innovation and development to support the sector, says FUCHS industrial and speciality manager Ashleigh Pollen.
Die-casting involves injecting molten metal into a mould to produce complex, high-precision components. This technique is essential for creating lightweight and durable parts in the automotive industry, contributing to vehicle efficiency and performance.
Pollen explains that the global die-casting market is projected to grow from about $83-billion in 2024 to about $112-billion by 2029, at a compound annual growth rate (CAGR) of 6.24%. The automotive parts die-casting segment is expected to reach roughly $46-billion in 2024 and grow at a CAGR of over 6.19% to around $62-billion by 2029.
Key drivers include a demand for lightweight vehicles as stringent fuel efficiency standards and emission regulations push automakers to adopt lightweight materials, such as aluminium, to reduce vehicle weight.
Die-casting facilitates the production of these lightweight components.
The rise in electric vehicle manufacturing has also increased the demand for die-cast parts, as these vehicles require complex, high-precision components that can be efficiently produced through die-casting, says Pollen.
Die-Casting Lubrications
Pollen notes that the products available under the FUCH’s LUBRODAL brand cover “every stage” of the die-casting process.
“The LUBRADOL range can withstand the high temperatures and pressures typical in die-casting, ensuring durability and reliability and reducing defects such as porosity and surface imperfections.”
Ladle coatings protect ladles from molten metal, plunger lubricants ensure smooth operation of plungers, and release agents facilitate the easy removal of cast parts from moulds. Additional products include assembly pastes, ejector lubricants and anti-soldering pastes.
Pollen highlights FUCH’s LUBRODAL AL 75, which features high thermal stability, has “excellent” lubricating properties, and is water miscible and easy to mix and apply. Other benefits include consistent performance under high temperatures, “smooth operation” and reduced wear.
LUBRODAL AL 100, mean-while, is a stable emulsion concentrate with high thermal stability, “excellent wetting properties” and no residue build-up. It provides effective lubrication for moulds in pressure die-casting of aluminium, zinc and other non-ferrous metals.
Finally, LUBRODAL AL 125 is water-miscible with solid lubricants and provides high thermal stability for reliable performance in demanding conditions, notes Pollen.
Meeting Die-Casting Needs
“We focus on continuous development of new formulations to meet evolving industry needs,” says Pollen.
FUCHS promotes environ- mentally acceptable lub- ricants and offers biodegradable lubricants designed to meet regulatory requirements for app- lications in sensitive ecological environments.
“These factors make FUCHS a preferred choice in the die-casting industry,” says Pollen.
She notes that the die-casting industry encounters various challenges including dimensional inaccuracies, with thermal expansion and mould wear resulting in faults. Additionally, performance and cost must be balanced while navigating raw material price fluctuations along with increased pressure from global competition and demand for high-quality, low-cost products.
To assist with and/or address the impact of these challenges, FUCHS provides extensive technical support and training programmes to customers to help them optimise the use of their products, including addressing the skilled labour shortage by equipping workers with the necessary expertise.
“Our innovative products are designed to enhance efficiency and reduce downtime,” says Pollen.
By focusing on these areas, FUCHS ensures that its product innovations meet the demands of the die-casting sector, helping manufacturers stay competitive and compliant with industry standards, she concludes.
Comments
Announcements
What's On
Subscribe to improve your user experience...
Option 1 (equivalent of R125 a month):
Receive a weekly copy of Creamer Media's Engineering News & Mining Weekly magazine
(print copy for those in South Africa and e-magazine for those outside of South Africa)
Receive daily email newsletters
Access to full search results
Access archive of magazine back copies
Access to Projects in Progress
Access to ONE Research Report of your choice in PDF format
Option 2 (equivalent of R375 a month):
All benefits from Option 1
PLUS
Access to Creamer Media's Research Channel Africa for ALL Research Reports, in PDF format, on various industrial and mining sectors
including Electricity; Water; Energy Transition; Hydrogen; Roads, Rail and Ports; Coal; Gold; Platinum; Battery Metals; etc.
Already a subscriber?
Forgotten your password?
Receive weekly copy of Creamer Media's Engineering News & Mining Weekly magazine (print copy for those in South Africa and e-magazine for those outside of South Africa)
➕
Recieve daily email newsletters
➕
Access to full search results
➕
Access archive of magazine back copies
➕
Access to Projects in Progress
➕
Access to ONE Research Report of your choice in PDF format
RESEARCH CHANNEL AFRICA
R4500 (equivalent of R375 a month)
SUBSCRIBEAll benefits from Option 1
➕
Access to Creamer Media's Research Channel Africa for ALL Research Reports on various industrial and mining sectors, in PDF format, including on:
Electricity
➕
Water
➕
Energy Transition
➕
Hydrogen
➕
Roads, Rail and Ports
➕
Coal
➕
Gold
➕
Platinum
➕
Battery Metals
➕
etc.
Receive all benefits from Option 1 or Option 2 delivered to numerous people at your company
➕
Multiple User names and Passwords for simultaneous log-ins
➕
Intranet integration access to all in your organisation