Maintenance vital in efforts to reduce operating costs
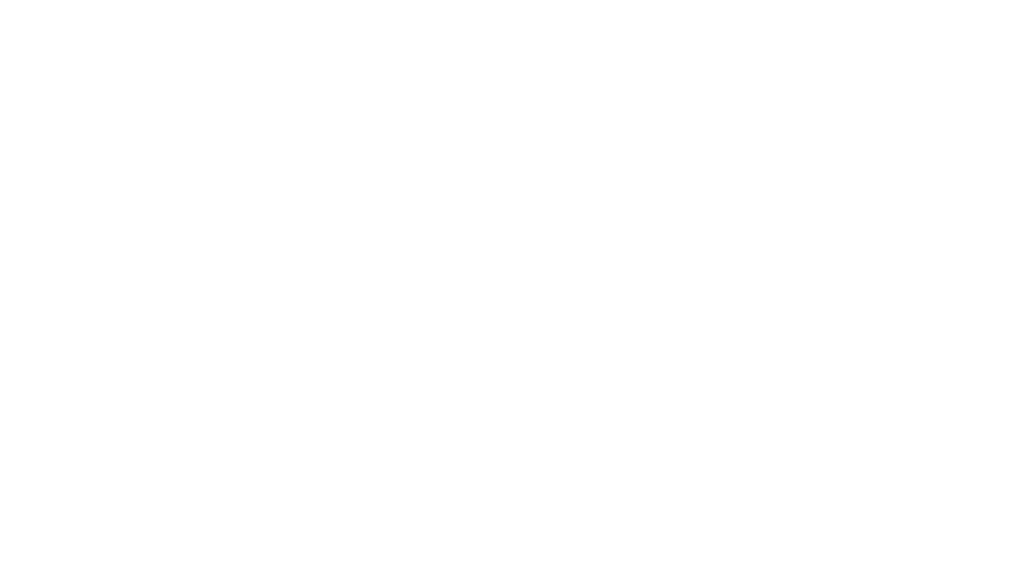
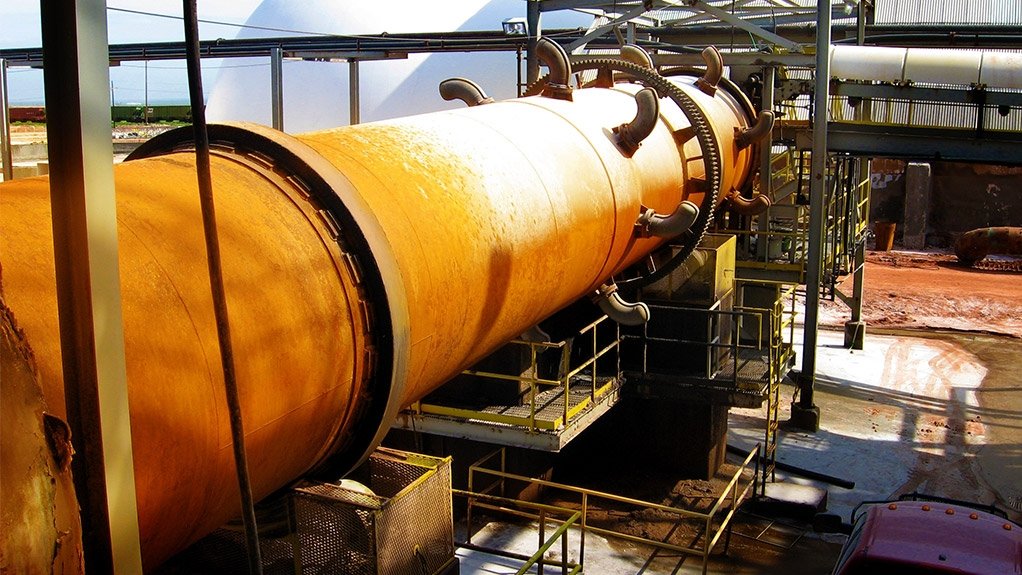
ON-SITE SERVICES The company provides on-site specialist services for rotary kilns for the cement and lime industries in sub-Saharan Africa
The current harsh economic and dynamic business environment that is characterised by recession, stiff competition and globalisation has made it imperative for every organisation to streamline its processes and reduce operating costs to remain competitive, stresses furnaces and industrial services provider Dickinson Group of Companies.
In a May newsletter, the Vereeniging, Gauteng-headquartered company explains that the cement industry has not been spared in this ordeal and, with the rotary kiln at the heart of all cement and clinker production, its maintenance has a huge impact on plant operating costs and profitability. Elaborating, the company states that the objective is to maintain optimum kiln performance and maximum production.
Through its Rotary Kiln Services division, Dickinson is able to provide on-site specialist services for rotary kilns for the cement and lime industries in sub-Saharan Africa. Having a team focused on rotary kilns has enabled the company to offer customers within its area of operation faster response times, lower travel costs and a local contact to call on when required.
The company’s rotary kiln services include troubleshooting, plant analysis, root cause analysis, comprehensive hot kiln alignment, in situ grinding of tyres, the supply of support rollers and thrust rollers, installation, maintenance, repair work, technical guidance and support for all rotary kiln equipment suppliers.
Explaining the four common rotary kiln conditions, the company says the first condition deals with kiln axis geometry. This must be aligned as it determines the distribution of the weight load among the kiln supports and the longitudinal distribution of the bending stresses in the kiln shell.
The second condition involves kiln ovality. The company states that it is vital to ensure that the kiln shell radius of curvature does not change unacceptably during the kiln’s rotation.
The third condition is field crank. Dickinson states that effective proactive kiln inspection must be carried out and that such inspections should include checking for red spots on the kiln shell and ensuring kiln shell sections have not become misaligned.
Finally, the company notes axial kiln balance, stating that trust face temperature measurements must be taken to ensure axial forces are not too great.
The solutions from Dickinson’s rotary kiln services package to avoid these kiln conditions involve maintenance and inspection programmes; survey procedure and hot kiln alignment services; reconditioning, tyre and roller grinding; and installation and repair.
“Our maintenance [and] inspection programme has been designed to help clients adopt a proactive approach to rotary kiln maintenance.”
The programme offers reduced rotary kiln maintenance and operating costs, reduced costly unplanned stoppages, compilation of a comprehensive history of wear rates for mechanical components and the achievement of maximum plant availability, thereby increasing production and reducing operating costs.
Further promised is reduced wear rates achieved by correctly aligning rotary kilns regularly, efficient planning for programmed shutdowns and “confident” budget planning for the replacement of high-cost items such as girth gears, pinions, tyres and trunnion rollers.
In terms of hot kiln alignment, Dickinson says this service ensures that rotary kilns are able to achieve maximum efficiency throughout their service life span and will help to avoid unforeseen breakdowns. “Almost all problems associated with rotary kilns can be attributed to misalignment.”
Alignment adjustment recommendations, together with many other key factors, such as the measurement of roller parameters and kiln thrust and mechanical balance, are included in a comprehensive report, together with a series of drawings. The package also includes a comprehensive mechanical condition report, with recommendations for the repair or improvement of the relevant plant items.
With regard to reconditioning, Dickinson’s rotary kiln division is able to provide an ‘on line’ tyre and trunnion roller surface reconditioning service, which enables worn or damaged running faces of tyres and rollers to be machined flat and parallel while the vessel is in operation.
“When Dickinson conducts in situ grinding of tyres and support rollers, no kiln downtime is needed and the company uses internationally trained grinding engineers to do the work. “The grinding engineers constantly monitor axial thrust of the kiln and bearing temperature throughout the grinding process, carrying out roller adjustments required to stabilise axial movement and temperature.”
In terms of installation and repair, Dickinson states that its personnel are experienced in all aspects of major repairs on any size rotary vessel, with expertise including the replacement of shell sections and the resetting of bedplates.
“From our regional operations, we are capable of performing all types of kiln component replacement, repair and installation, underpinned by the appropriate manpower and technical expertise, with complete project planning capabilities.”
Comments
Press Office
Announcements
What's On
Subscribe to improve your user experience...
Option 1 (equivalent of R125 a month):
Receive a weekly copy of Creamer Media's Engineering News & Mining Weekly magazine
(print copy for those in South Africa and e-magazine for those outside of South Africa)
Receive daily email newsletters
Access to full search results
Access archive of magazine back copies
Access to Projects in Progress
Access to ONE Research Report of your choice in PDF format
Option 2 (equivalent of R375 a month):
All benefits from Option 1
PLUS
Access to Creamer Media's Research Channel Africa for ALL Research Reports, in PDF format, on various industrial and mining sectors
including Electricity; Water; Energy Transition; Hydrogen; Roads, Rail and Ports; Coal; Gold; Platinum; Battery Metals; etc.
Already a subscriber?
Forgotten your password?
Receive weekly copy of Creamer Media's Engineering News & Mining Weekly magazine (print copy for those in South Africa and e-magazine for those outside of South Africa)
➕
Recieve daily email newsletters
➕
Access to full search results
➕
Access archive of magazine back copies
➕
Access to Projects in Progress
➕
Access to ONE Research Report of your choice in PDF format
RESEARCH CHANNEL AFRICA
R4500 (equivalent of R375 a month)
SUBSCRIBEAll benefits from Option 1
➕
Access to Creamer Media's Research Channel Africa for ALL Research Reports on various industrial and mining sectors, in PDF format, including on:
Electricity
➕
Water
➕
Energy Transition
➕
Hydrogen
➕
Roads, Rail and Ports
➕
Coal
➕
Gold
➕
Platinum
➕
Battery Metals
➕
etc.
Receive all benefits from Option 1 or Option 2 delivered to numerous people at your company
➕
Multiple User names and Passwords for simultaneous log-ins
➕
Intranet integration access to all in your organisation