Mine haul roads can reduce emissions, costs
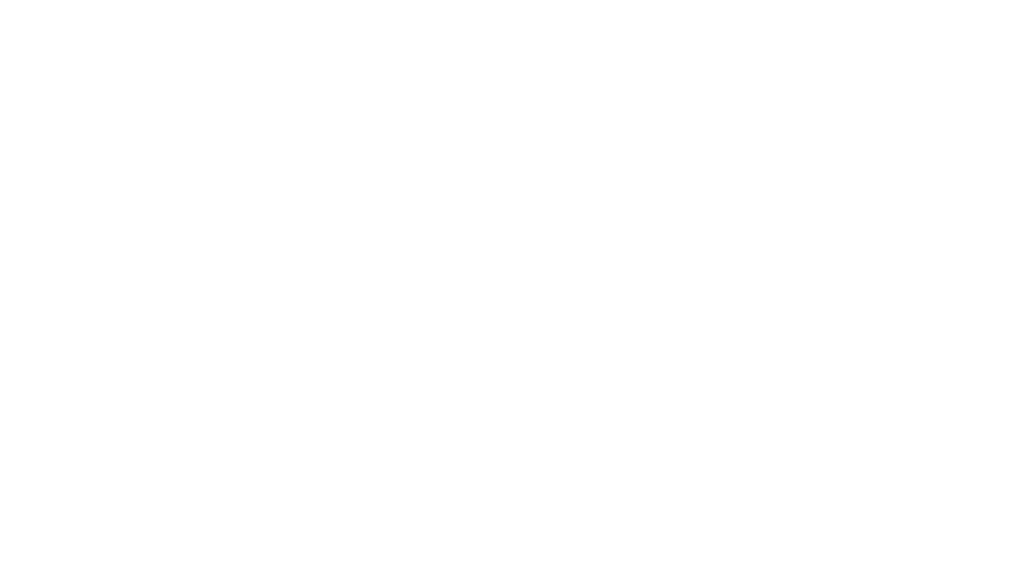
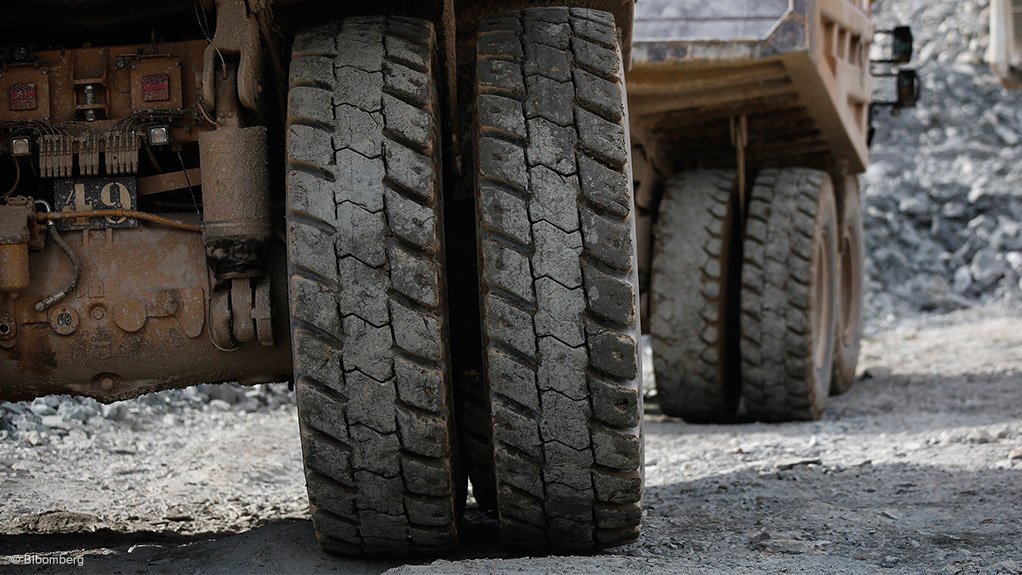
PAVING THE WAY If roads are not constructed properly, undulations can form, increasing rolling resistance. This can cause increased diesel fumes from trucks and health and safety risks
Photo by Bloomberg
Having researched the design and management of opencast mine haul roads locally and globally for the past 30 years, retired University of Pretoria civil engineering professor Alex Visser highlights a specific road construction system for mine haul roads which can reduce fuel emissions and save money.
He maintains that this road construction system has been taught in many courses locally, as well as in countries such as Brazil and Chile.
This system comprises a methodology for the construction of roads on opencast mines, which allows for haul trucks to transport mined materials on site more effectively.
Said methodology enables the construction of semi-permanent roads with a low rolling resistance – the amount of resistance to motion of the truck from the road. This means that trucks can move on these roads with less difficulty, reducing their diesel consumption and increasing productivity.
Smoother Mine Haul Roads
Based on previous work experience on local public road systems, Visser and his research partners calibrated a computer programme to calculate the stresses and strains on a road. This provides data and information that allows for decisions on the appropriate amount of protection a road needs to support large-haul mine trucks.
If these roads are not constructed properly, undulations can form, affecting the riding quality of trucks, which, in turn, can increase the rolling resistance of the road.
In addition to increased diesel fumes that can present environmental risks, as well as increased costs for operations, increased rolling resistance can also present health and safety risks for truck operators. This can include the development of musculoskeletal disorders from prolonged exposure to high magnitude vibration while driving these trucks.
Visser also points to the significant size of the trucks that operate on openpit mine sites, noting that some of these are as heavy as 600 t, with wheel loads of 100 t.
Building these haul roads in a specific manner to reduce the aforementioned risks involves the appropriate selection of material and shape of the riding surface, as well as the appropriate level of maintenance to counteract wear and tear.
“The geometry of the roads has to be appropriate for all stages of the life-of-mine. The first step is based on knowing where the road will go, while the second involves providing a road structure that can support large trucks,” he comments.
Visser stresses that much of the road structure strength relies on the construction of the dump rock base layer which is covered by a vehicle friendly wearing course – a relatively thin layer (100 to 200 mm) which provides a dust and mud free surface and gives a good ride.
Historically, openpit mines would generally use unpaved roads to prevent damage to haul roads in the event of a spillage of mined material. Motor graders would also be needed to remove the spillage, which, in turn, would increase the level of diesel fuel emissions and dust.
“We have guidelines for the wearing course materials, which provides some leeway in terms of construction material selection. Therefore, if I put a certain material in a road, I will know the properties of that road and whether it’s sufficient for its intended purpose.”
He adds that following the development of this road construction system, mines began to enquire about the use of additives in the roads to improve their longevity and reduce maintenance.
While these additives would differ, depending on the mine site and the aggregates available, Visser explains that all these additives have similar properties and would improve the roads.
Further, he comments that it is more cost effective to use on-site aggregates, rather than have them delivered from an off-site crusher.
The additive binds the wearing coarse and gravel to reduce the dust. This, in turn, also reduces the amount of water needed for maintenance operations and dust reduction, and generally results in a low rolling resistance. Mud would also be minimised, reducing undulations and damage to vehicle components, thereby ensuring easier handling.
“We have been impressed with the benefits of applying our research. At one of the mines, we treated a ramp road with a 10% gradient with an additive. The combination of the road, additive, correct wearing course and the correct structure has resulted in the road having been operational for four years without requiring any road surface maintenance or water application. The ramp has a trolley assist system, with an electric wire overhead for the truck to use electric power. The shape of the road is vital, as undulations can cause the trucks to become disconnected from the trolley system, which reduces productivity.”
The Way Forward
Visser also stresses that this road construction approach can also be used in underground mine applications. The tunnel floor underground is uneven and mud and water add to tyre damage and high mining costs. Sometimes it takes workers more than 30 minutes travel underground to reach the face because of poor road quality. The structural design approach, with a maximum of 200 mm three dimensional bubblelock concrete filled riding surface, can be used underground.
This road construction system can remove risk of vehicle and tyre damage and provide low rolling resistance roads for vehicles operating underground.
Visser emphasises that this permanent concrete road surface could be important for mine haul trucks going forward, particularly as the potential for driverless vehicles becomes more evident. He states that such vehicles would struggle to detect and avoid undulations in the road and, as a result, road quality will become even more crucial.
“Haul roads can make money, and that is the clear message to miners. But in addition to saving money, we are providing a safer and heathier operation, which is the primary objective in the mining industry,” he concludes.
Comments
Press Office
Announcements
What's On
Subscribe to improve your user experience...
Option 1 (equivalent of R125 a month):
Receive a weekly copy of Creamer Media's Engineering News & Mining Weekly magazine
(print copy for those in South Africa and e-magazine for those outside of South Africa)
Receive daily email newsletters
Access to full search results
Access archive of magazine back copies
Access to Projects in Progress
Access to ONE Research Report of your choice in PDF format
Option 2 (equivalent of R375 a month):
All benefits from Option 1
PLUS
Access to Creamer Media's Research Channel Africa for ALL Research Reports, in PDF format, on various industrial and mining sectors
including Electricity; Water; Energy Transition; Hydrogen; Roads, Rail and Ports; Coal; Gold; Platinum; Battery Metals; etc.
Already a subscriber?
Forgotten your password?
Receive weekly copy of Creamer Media's Engineering News & Mining Weekly magazine (print copy for those in South Africa and e-magazine for those outside of South Africa)
➕
Recieve daily email newsletters
➕
Access to full search results
➕
Access archive of magazine back copies
➕
Access to Projects in Progress
➕
Access to ONE Research Report of your choice in PDF format
RESEARCH CHANNEL AFRICA
R4500 (equivalent of R375 a month)
SUBSCRIBEAll benefits from Option 1
➕
Access to Creamer Media's Research Channel Africa for ALL Research Reports on various industrial and mining sectors, in PDF format, including on:
Electricity
➕
Water
➕
Energy Transition
➕
Hydrogen
➕
Roads, Rail and Ports
➕
Coal
➕
Gold
➕
Platinum
➕
Battery Metals
➕
etc.
Receive all benefits from Option 1 or Option 2 delivered to numerous people at your company
➕
Multiple User names and Passwords for simultaneous log-ins
➕
Intranet integration access to all in your organisation