Mobile emulsion pumps technology goes global
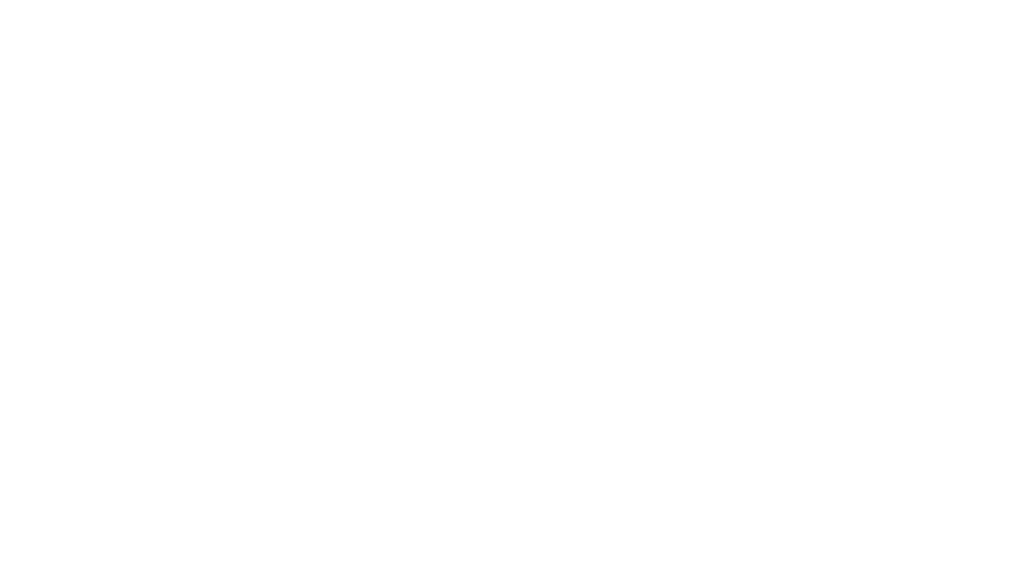
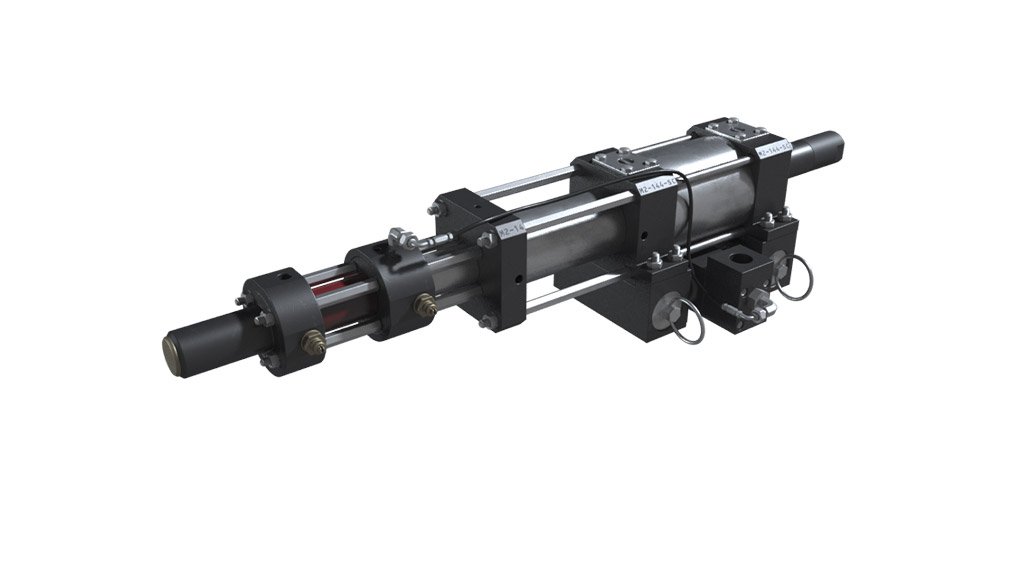
EXPLOSIVE PUMPING The MP2 emulsion pumping system is ideal for large-scale mechanised underground operations
South African explosives company BME is taking its MP2 mobile mechanised emulsion pumps technology for underground blasting applications to international markets.
BME product manager Neil Alberts tells Mining Weekly that demonstrations of the MP2 emulsion pumps technology are being planned for mining clients in Canada in the coming months, with demonstrations performed for mining clients in Australia in November last year.
“There is immense international interest in this technology. From an engineering perspective, it has value in terms of reduced labour requirements, cost and capital outlay, compared with other emulsion pumps solutions on the market.”
The 45 kg MP2 pumps system is the ‘big brother’ of BME’s 14 kg portable emulsion pump – a niche product used in narrow-reef underground blasting applications.
The MP2, however, is designed for use in open-stope, mass mining operations and is ideal for modern, mechanised mining applications, Alberts claims.
For the MP2, two mobile emulsion pumps – a primary and a backup – are fitted on all BME emulsion-charging units to prevent downtime through potential breakdowns. Should a failure occur in one shift, the design of the pumps technology allows for standard repairs to be performed by standard charging support personnel on the next shift.
Further, the MP2 system features predetermined sensitising ratios used for the operation of emulsion-charging units underground.
The pump’s electronic operating principle, which allows for exact emulsion mass dosing, means that, coupled with the MP2’s control system, user-specified masses, with accuracy of up to 10 g, can be delivered into each charged blast hole.
“All MP2 emulsion pumps are factory set to achieve optimal blasting densities and cannot be adjusted by underground personnel. Therefore, optimal densities will ensure maximum possible advance rates and eliminate the necessity for daily cup samples to be taken to ensure the correct sensitisation of emulsion,” Alberts explains.
These features reduce the support labour requirements for the emulsion-charging units on site.
The technology also enables an operator to change between two predetermined blasting densities on each pump, subsequently improving hanging wall conditions in board and pillar operations. A preset low emulsion density allows for reduced overbreak and optimal hanging wall and sidewall strata control, while the preset high-density function allows for maximum pull from the cut and optimal advance rates.
The coupled MP2 pumps can simultaneously sensitise the emulsion while pumping and lubricate the charging hose with a water jacket if required, typically for up-hole charging applications.
The pumps operate according to a simple dual-action plunger pumping principle. Emulsion and sensitiser dosing is achieved using one shaft system without any complex mechanical linkages. This ensures that constant densities are achieved without any drift, regardless of how long the pump has been in use – provided that the seals are maintained. Hose lubrication is achieved in the same way.
Alberts says the pump is designed with ease of maintenance in mind, as “the individual pumps, weighing about 20 kg each, can be swapped out in minutes, as the emulsion piping is connected to a separate pump base, which is permanently attached to the emulsion-charging unit”.
The pump connects to the pump base simply by dropping it onto locating studs and securing it down with four nuts; therefore, the pump can be separated from the unit for service or exchange simply by releasing four nuts and two hydraulic quick couplers, he elaborates.
The pump base also features cartridge nonreturn valves, which are modular units that can be pulled out and replaced without requiring any tools.
“There can often be contaminants in emulsions underground such as dirt. Therefore, maximum uptime during charging operations is achievable by quickly swapping the valves, which have been jammed open by particulate build-up,” he notes.
The MP2 also has notable safety features and s
hould something block the outlet, the hydraulic system, with pressure bypass that drives the pump, ensures that the pump cannot deadhead at unsafe pressures. Instead, it will simply stall. If the pump control system detects a stall, it will automatically deactivate the pump.
Further, the MP2 is fitted with a pair of high-precision bursting discs, which will relieve emulsion pressure, should it reach unsafe levels of about 70 bar.
The pump is intrinsically resistant to heat build-up from dry running, as the slow stroking speed and highly conductive stainless steel emulsion cylinder barrel ensure that temperatures do not reach unsafe levels, Alberts assures.
The MP2 pumps system has a low energy-requirement. Multiple power sources can be used to drive the MP2 technology, including hydraulic, pneumatic and hydropower.
BME currently has more than 200 MP2 pumps successfully operating in South Africa and West Africa.
Comments
Press Office
Announcements
What's On
Subscribe to improve your user experience...
Option 1 (equivalent of R125 a month):
Receive a weekly copy of Creamer Media's Engineering News & Mining Weekly magazine
(print copy for those in South Africa and e-magazine for those outside of South Africa)
Receive daily email newsletters
Access to full search results
Access archive of magazine back copies
Access to Projects in Progress
Access to ONE Research Report of your choice in PDF format
Option 2 (equivalent of R375 a month):
All benefits from Option 1
PLUS
Access to Creamer Media's Research Channel Africa for ALL Research Reports, in PDF format, on various industrial and mining sectors
including Electricity; Water; Energy Transition; Hydrogen; Roads, Rail and Ports; Coal; Gold; Platinum; Battery Metals; etc.
Already a subscriber?
Forgotten your password?
Receive weekly copy of Creamer Media's Engineering News & Mining Weekly magazine (print copy for those in South Africa and e-magazine for those outside of South Africa)
➕
Recieve daily email newsletters
➕
Access to full search results
➕
Access archive of magazine back copies
➕
Access to Projects in Progress
➕
Access to ONE Research Report of your choice in PDF format
RESEARCH CHANNEL AFRICA
R4500 (equivalent of R375 a month)
SUBSCRIBEAll benefits from Option 1
➕
Access to Creamer Media's Research Channel Africa for ALL Research Reports on various industrial and mining sectors, in PDF format, including on:
Electricity
➕
Water
➕
Energy Transition
➕
Hydrogen
➕
Roads, Rail and Ports
➕
Coal
➕
Gold
➕
Platinum
➕
Battery Metals
➕
etc.
Receive all benefits from Option 1 or Option 2 delivered to numerous people at your company
➕
Multiple User names and Passwords for simultaneous log-ins
➕
Intranet integration access to all in your organisation