New factory brings component outsourcing in-house
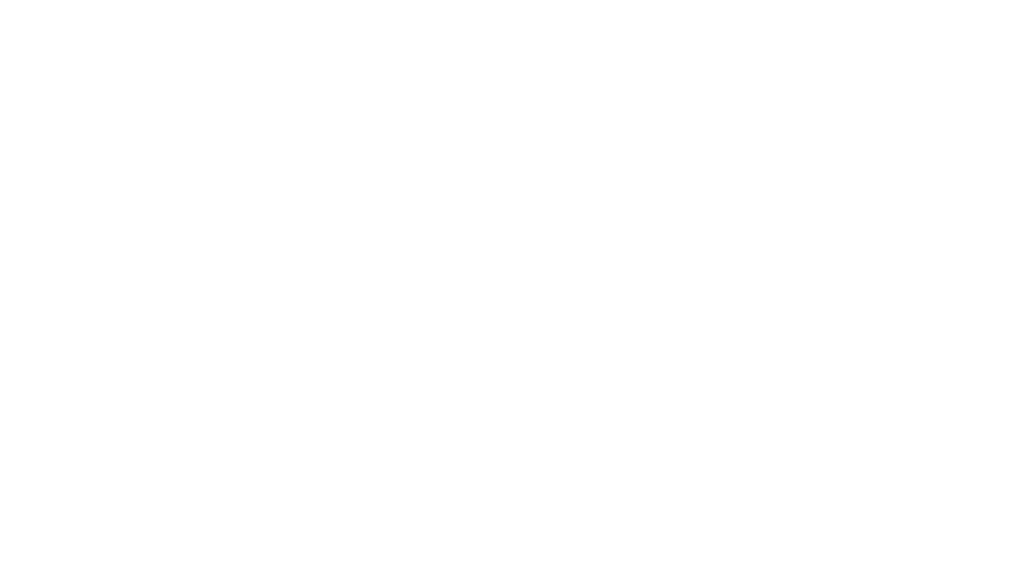
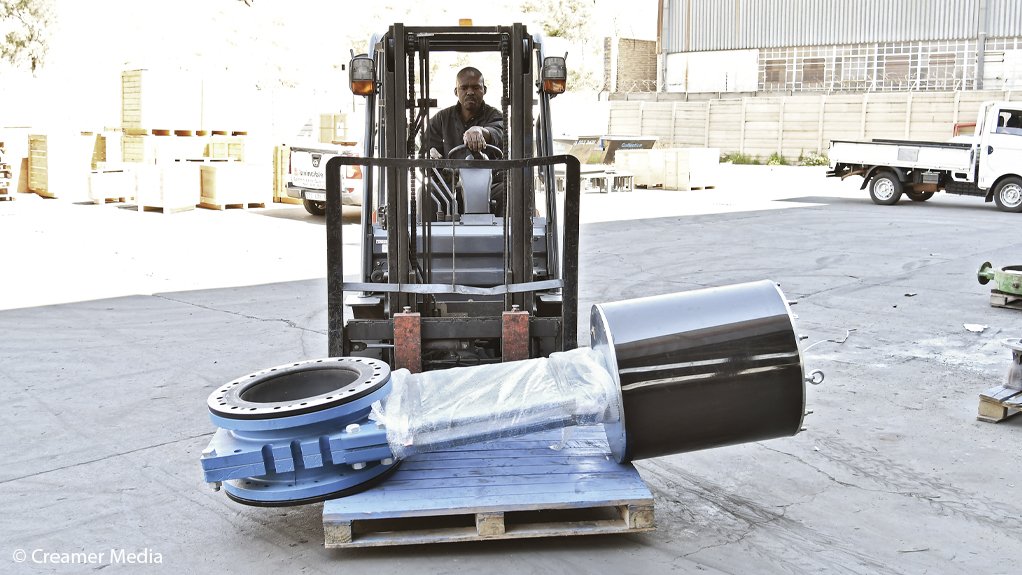
EXTENDING CAPABILITIES Invincible Valve's in-house manufacturing capability has been increased with addition of a new factory in close proximity to its existing facility in Knights, Germiston
Photo by Creamer Media's Donna Slater
Having bought a new factory in close proximity to its existing factory in Knights, Germiston, valve products and ancillary equipment manufacturer Invincible Valves has developed a new machine shop to facilitate the manufacturing of valve components that it previously sourced from third-party suppliers.
The new factory was acquired, through an auction, before the Covid-19 pandemic, and has since been renovated and developed by the company, with intentions to become fully operational by mid-month.
The new factory will house the reconditioning and rubber lining departments, and with the addition of the new machine shop, components for reconditioning and the Inval actuators will now be done in-house, making them less reliant on third-party suppliers.
“It’s quite a big step for us, because we were heavily reliant on all these things getting to us from third parties. Now we don’t have to send it out anymore, we can do it in-house,” explains Invincible Valves MD Pam du Plessis.
Invincible Valves bought an existing machine shop with which the company had a long standing relationship and incorporated it into its works.
She notes that an existing section of the machine shop was moved from Invincible Valve’s legacy factory into the new factory, to include equipment such as lathe computer numerical control machines and an autoclave.
A new 10 m autoclave for the rubber lining division has also been installed, while the original, smaller, 3 m autoclave will remain in the legacy factory.
The 10 m autoclave enables Invincible Valves to diversify its manufacturing capabilities to include the rubber lining of pipes, accommodating pipe links, while still continuing to rubber-line valves and fittings.
In addition to general renovation, Invincible Valves has added on buildings to its new factory to incorporate a full shot blasting unit, the rubber lining division and a grinding bay. The new factory also has generator backup power.
Skills Transfer
Prior to developing the new factory, Du Plessis says Invincible Valves outsourced its supply of the Inval actuator components to a company it had been in a partnership with for many years, thereby creating a degree of drawing in in-house capability.
She adds that through the purchase of the business, the machine shop operators agreed to a two-year work agreement to work in the new facility, while it will facilitate the transfer of knowledge to Invincible Valves’ personnel for the full manufacturing capabilities to be done entirely in-house by Invincible Valves.
Namibia Contract
Invincible Valves recently conducted valve reconditioning work as part of a contract for a uranium mining plant in Namibia.
Having reconditioned more than 1 200 valves, a project Invincible Valves undertook over five months, Du Plessis elaborates that the valves were brought from the mine to South Africa, arriving in containers at Invincible Valves’ facility in South Africa, in batches.
“The turnaround time was really impressive. We worked six days a week, 12 hours a day to make it happen . . . and it has been a huge thing for us in Namibia, because there are a lot of mines there looking to do the same thing,” highlights Du Plessis.
She expresses that this project “pushed the company’s boundaries . . . it’s a big thing because we have agents in the area and to show our support to them, and to be there with them, I think that was huge”.
“It’s encouraging [our agents] to go and look for more business in the area . . . we’re now well known in Namibia because of this job. I think there’s a lot more work coming . . .”, enthuses Du Plessis.
She points out that reconditioning of valves is cost effective for plants, as when the valves are reconditioned they are returned in a condition similar to when they are bought new, but at a reduced cost.
Comments
Press Office
Announcements
What's On
Subscribe to improve your user experience...
Option 1 (equivalent of R125 a month):
Receive a weekly copy of Creamer Media's Engineering News & Mining Weekly magazine
(print copy for those in South Africa and e-magazine for those outside of South Africa)
Receive daily email newsletters
Access to full search results
Access archive of magazine back copies
Access to Projects in Progress
Access to ONE Research Report of your choice in PDF format
Option 2 (equivalent of R375 a month):
All benefits from Option 1
PLUS
Access to Creamer Media's Research Channel Africa for ALL Research Reports, in PDF format, on various industrial and mining sectors
including Electricity; Water; Energy Transition; Hydrogen; Roads, Rail and Ports; Coal; Gold; Platinum; Battery Metals; etc.
Already a subscriber?
Forgotten your password?
Receive weekly copy of Creamer Media's Engineering News & Mining Weekly magazine (print copy for those in South Africa and e-magazine for those outside of South Africa)
➕
Recieve daily email newsletters
➕
Access to full search results
➕
Access archive of magazine back copies
➕
Access to Projects in Progress
➕
Access to ONE Research Report of your choice in PDF format
RESEARCH CHANNEL AFRICA
R4500 (equivalent of R375 a month)
SUBSCRIBEAll benefits from Option 1
➕
Access to Creamer Media's Research Channel Africa for ALL Research Reports on various industrial and mining sectors, in PDF format, including on:
Electricity
➕
Water
➕
Energy Transition
➕
Hydrogen
➕
Roads, Rail and Ports
➕
Coal
➕
Gold
➕
Platinum
➕
Battery Metals
➕
etc.
Receive all benefits from Option 1 or Option 2 delivered to numerous people at your company
➕
Multiple User names and Passwords for simultaneous log-ins
➕
Intranet integration access to all in your organisation