New FLS NexGen polyurethane changes the game in screen media
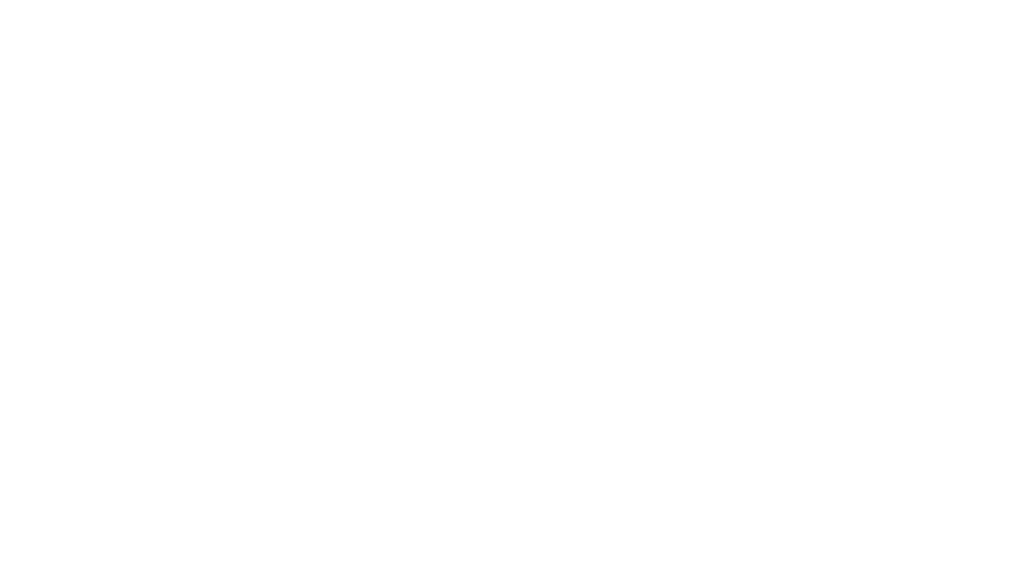
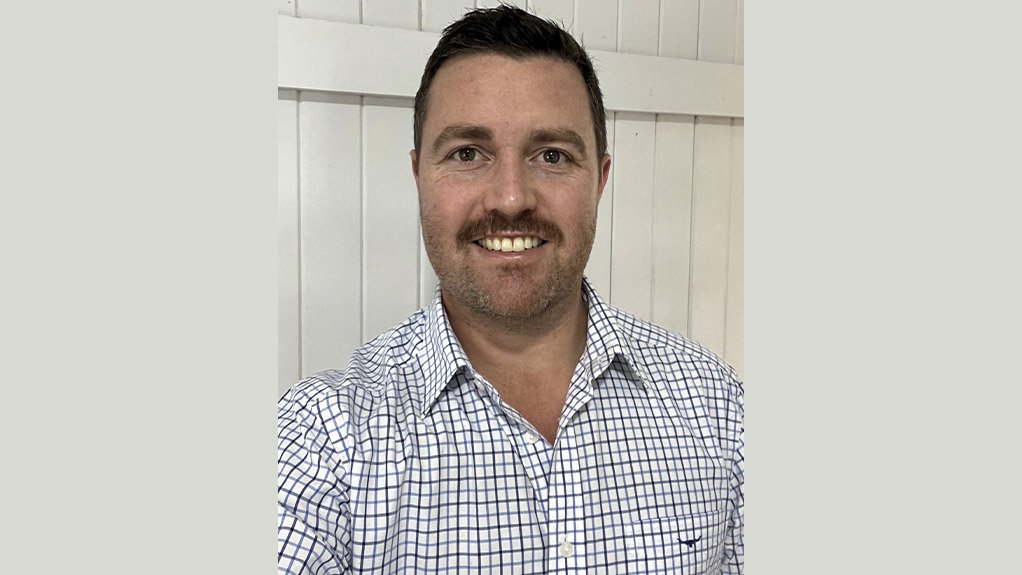
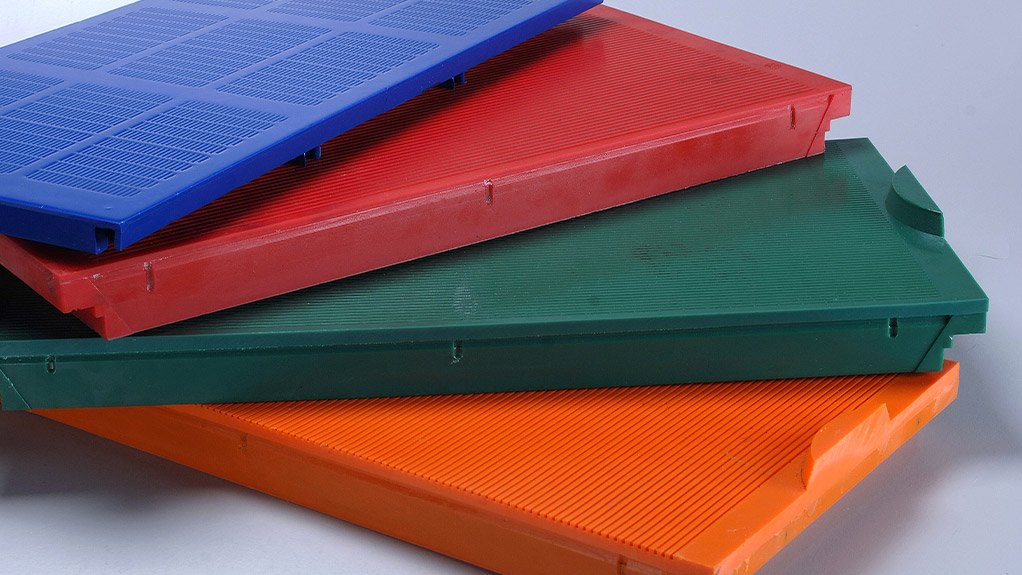
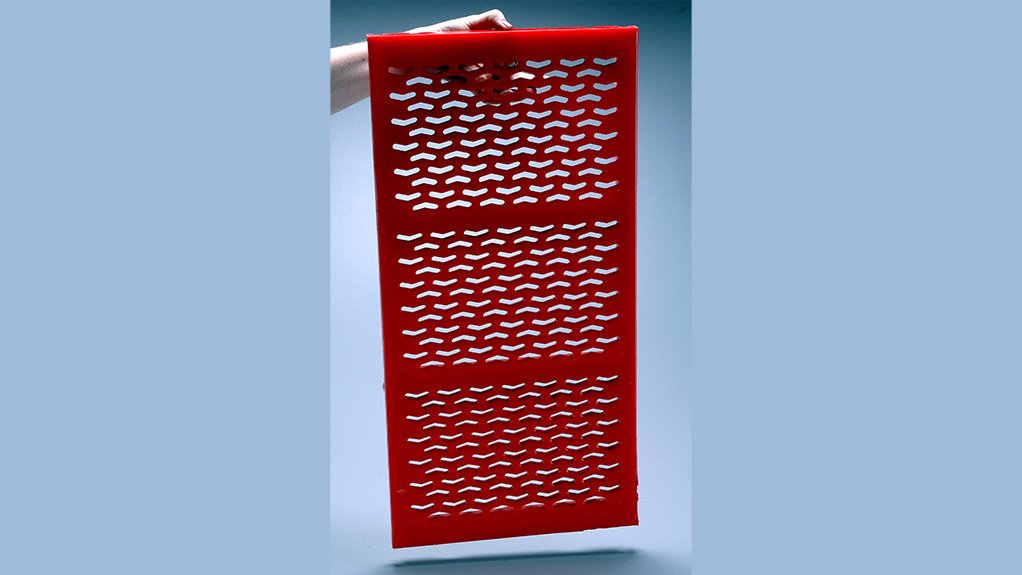
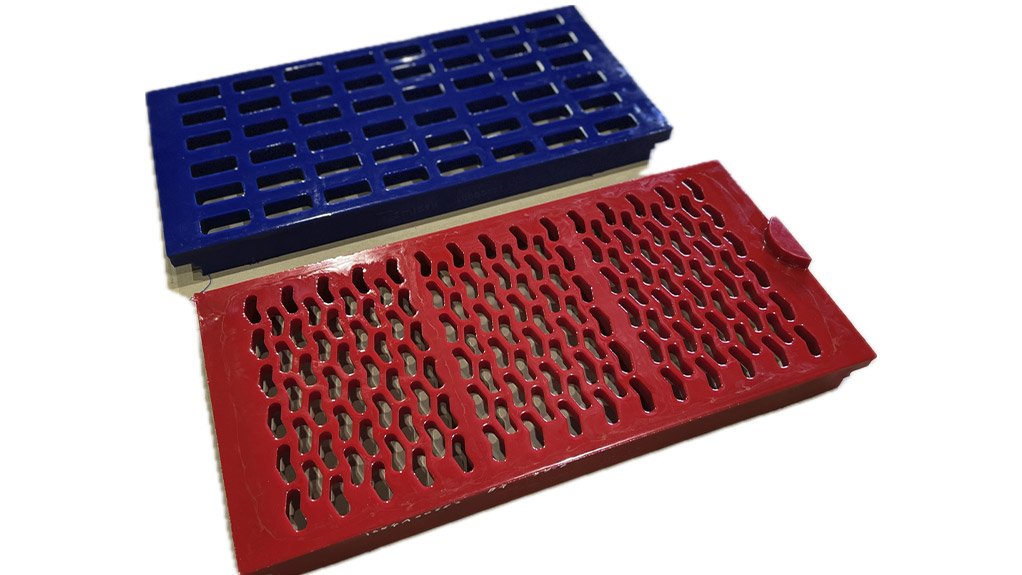
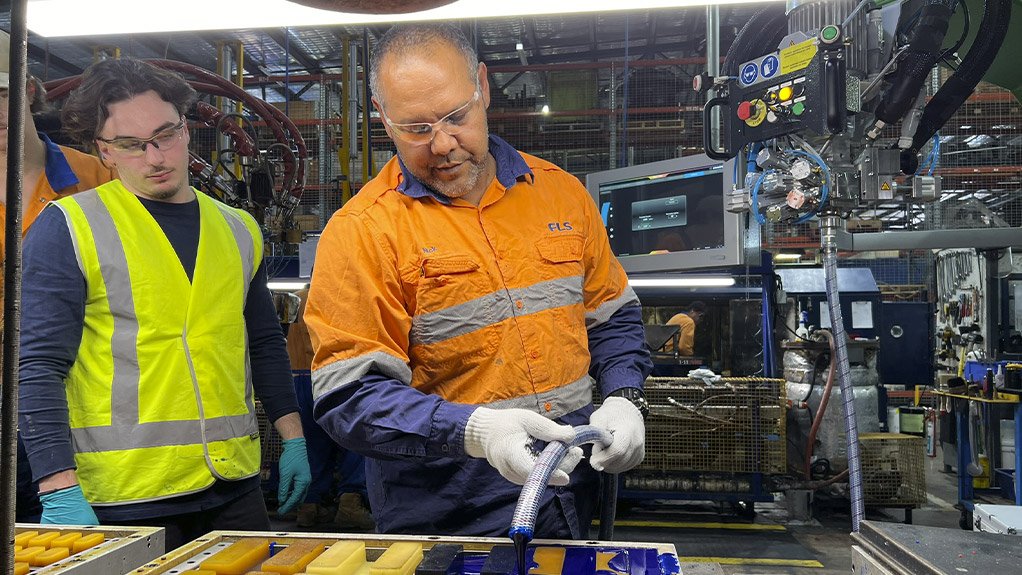
Chris Currie, Service Line Manager at FLS
FLS's NexGen polyurethane screen panel is a robust and durable solution, blending the strength of rubber with the flexibility of polyurethane elastomers
The NexGen panel delivers superior wear resistance in highly abrasive applications, outperforming traditional rubber and polyurethane panels
The NexGen panel resists abrasion without sacrificing cut resistance
The NexGen panels being poured at the FLS facility
This article has been supplied.
After a rigorous three year testing period, FLS used Electra Mining 2024 to officially launch its NexGen polyurethane, a heavy duty and hard wearing screen panel for large particle applications. Combining physical properties of rubber and polyurethane elastomers, the NexGen offers excellent wear resistance in highly abrasive applications such as early-stage screens and trommels.
As part of its dedication to providing top-tier screening media solutions tailored to meet the rigorous demands of commodity areas, FLS has brought to market its NexGen polyurethane screen media panel. Designed to offer long wear life, the NexGen polyurethane panel is ideally suited for early stage screens and trommels where high abrasion is the order of the day.
“Due to its extremely durable properties, it lasts longer than rubber or standard polyurethane in high impact applications. In some instances, it has been proven to offer double the screen panel wear life of rubber in these high-abrasion environments,” explain Chris Currie, Service Line Manager at FLS.
One of the major benefits of the long wear life is the reduction of costs. Frequent screen panel replacement leads to high maintenance and operating cost, while lowering equipment productivity at the same time. In addition, regular replacement means that screen maintenance personnel have to spend an incredible amount of time on the screen changing panels, increasing the safety risk in the process.
“With increased wear life also comes a significant reduction in waste not just in the material itself, but also in the supply chain. Less frequent panel changes mean that there is less energy used, less transport required and less stock needed, which in turn is a huge sustainability tick for our customers,” says Currie.
With screen panels, he adds, screening efficiency is a very big factor in profitable operations. Consequently, says Currie, FLS maintains at least 95% screening efficiency target in all its designs. With the premium material used in the NexGen polyurethane panels, the company is able to run a smaller ligament, that can provide more open area. A higher percentage of open area in screening panels improves screening efficiency and material throughput. This is because it gives particles more opportunities to pass through the screen.
In several trials conducted during the test period, the NexGen polyurethane proved to be in a league of its own in terms of wear life. For example, at a major iron ore mine in the Northern Cape, South Africa, the NexGen polyurethane significantly increased wear life by at least six times compared with standard thermoplastic polyurethane (TPU) injection moulded panels, injection moulded rubber and other open cast polyurethane options.
In a coal application, the NexGen polyurethane panels survived for ten weeks, compared to the five weeks that most of the standard polyurethane panels lasted. “Doubling the screen media wear life lowered maintenance time and media costs, while increasing safety and productivity,” concludes Currie.
FLSmidth
Comments
Press Office
Announcements
What's On
Subscribe to improve your user experience...
Option 1 (equivalent of R125 a month):
Receive a weekly copy of Creamer Media's Engineering News & Mining Weekly magazine
(print copy for those in South Africa and e-magazine for those outside of South Africa)
Receive daily email newsletters
Access to full search results
Access archive of magazine back copies
Access to Projects in Progress
Access to ONE Research Report of your choice in PDF format
Option 2 (equivalent of R375 a month):
All benefits from Option 1
PLUS
Access to Creamer Media's Research Channel Africa for ALL Research Reports, in PDF format, on various industrial and mining sectors
including Electricity; Water; Energy Transition; Hydrogen; Roads, Rail and Ports; Coal; Gold; Platinum; Battery Metals; etc.
Already a subscriber?
Forgotten your password?
Receive weekly copy of Creamer Media's Engineering News & Mining Weekly magazine (print copy for those in South Africa and e-magazine for those outside of South Africa)
➕
Recieve daily email newsletters
➕
Access to full search results
➕
Access archive of magazine back copies
➕
Access to Projects in Progress
➕
Access to ONE Research Report of your choice in PDF format
RESEARCH CHANNEL AFRICA
R4500 (equivalent of R375 a month)
SUBSCRIBEAll benefits from Option 1
➕
Access to Creamer Media's Research Channel Africa for ALL Research Reports on various industrial and mining sectors, in PDF format, including on:
Electricity
➕
Water
➕
Energy Transition
➕
Hydrogen
➕
Roads, Rail and Ports
➕
Coal
➕
Gold
➕
Platinum
➕
Battery Metals
➕
etc.
Receive all benefits from Option 1 or Option 2 delivered to numerous people at your company
➕
Multiple User names and Passwords for simultaneous log-ins
➕
Intranet integration access to all in your organisation