OEM’s screens support Namibian expansion
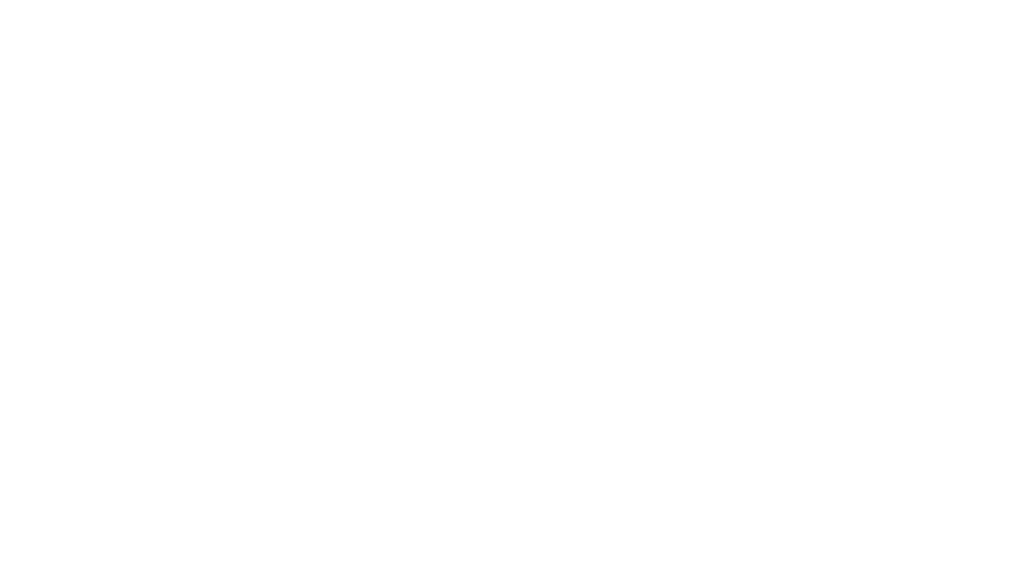
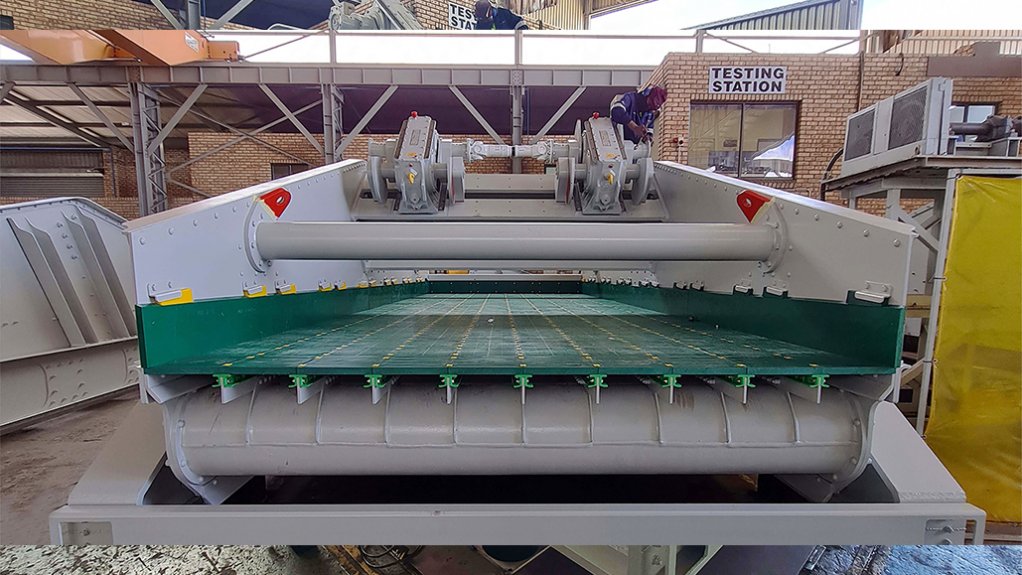
INNOVATIVE SCREENING The single deck Kwatani screen manufactured for the gold mining industry
Namibia’s bustling mining scene is witnessing exciting expansion and technological innovation with original-equipment manufacturer (OEM) Kwatani supplying five custom-designed and -manufactured mill discharge screens to a leading gold mining operation in the country.
The screens were all custom designed and manufactured at Kwatani’s Gauteng facilities.
According to Kwatani CEO Kim Schoepflin, the company has a “long history in Namibia and a strong footprint across various commodities there – including an established presence at this gold mine”.
The company, she explains, has worked with the engineering, procurement and construction contractor and the end-customer for about three years on conceptualising the optimal solution for the mine.
“The mine is gearing up to increase its production by 50%, to take advantage of the strong gold price,” says Schoepflin, adding that the company’s role was to ensure that its discharge screens met the exact process requirements, namely efficiencies of up to 95%, while delivering mechanical integrity for minimal maintenance downtime.
The expansion includes the installation of two latest-technology mills (a high-pressure grinding roll (HPGR) and a vertical mill) which will boost production while reducing energy demand.
Kwatani’s mill discharge screens, each measuring 3 m wide by 8 m long, will handle the coarse and fine material from the HPGR and the vertical mill.
The company will also supply three silo feeders of 1.2 m by 2.5 m in size, to feed material from the silo to conveyors.
“Our screen design optimises the retention time on the deck, allowing for better screening and stratification,” she says.
Owing to the volume of slurry and water sprayed onto the screens, the added retention time assists with better drainage at lower cut points, she notes.
She further explains that the coarse screens were designed at a decline, and feature a larger screening media aperture with higher amplitude and stroke.
Together with lower speed, Schoepflin adds that this achieves better screening efficiency for the coarser particles.
The fine horizontal screens, with smaller aperture screening media for the finer feed, were designed with a higher speed and lower amplitude and stroke; this will optimise the screening efficiency of the finer feed to these screens.
She also highlights the attention paid to the isolation of the vibrating screens. In this case, Kwatani engineers selected rubber buffers, which have higher dynamic loads but are more suited to wet applications and screens with a heavier mass.
“The number and type of buffers were defined according to the mass of the screens,” says Schoepflin, adding that “the selection of rubber buffers for larger screens also assists with startup and shutdown time, allowing the screens to come to rest more effectively”.
For these five screens, Kwatani designed and supplied custom counter-balance frames to minimise the dynamic load to the plant infrastructure. The company’s screen technology includes designing its exciters in-house.
This ensures that screens receive the necessary G-forces for optimal material stratification and screening, matching customers’ process requirements with the best possible efficiencies.
“To make sure our screens cope with the high capacity demands of modern processing plants, we rigorously test all units in our in-house testing facility before dispatch,” she states.
Kwatani’s screening units began their journey to Namibia at the end of November 2021, and the company will support the commissioning when the customer requires.
Comments
Press Office
Announcements
What's On
Subscribe to improve your user experience...
Option 1 (equivalent of R125 a month):
Receive a weekly copy of Creamer Media's Engineering News & Mining Weekly magazine
(print copy for those in South Africa and e-magazine for those outside of South Africa)
Receive daily email newsletters
Access to full search results
Access archive of magazine back copies
Access to Projects in Progress
Access to ONE Research Report of your choice in PDF format
Option 2 (equivalent of R375 a month):
All benefits from Option 1
PLUS
Access to Creamer Media's Research Channel Africa for ALL Research Reports, in PDF format, on various industrial and mining sectors
including Electricity; Water; Energy Transition; Hydrogen; Roads, Rail and Ports; Coal; Gold; Platinum; Battery Metals; etc.
Already a subscriber?
Forgotten your password?
Receive weekly copy of Creamer Media's Engineering News & Mining Weekly magazine (print copy for those in South Africa and e-magazine for those outside of South Africa)
➕
Recieve daily email newsletters
➕
Access to full search results
➕
Access archive of magazine back copies
➕
Access to Projects in Progress
➕
Access to ONE Research Report of your choice in PDF format
RESEARCH CHANNEL AFRICA
R4500 (equivalent of R375 a month)
SUBSCRIBEAll benefits from Option 1
➕
Access to Creamer Media's Research Channel Africa for ALL Research Reports on various industrial and mining sectors, in PDF format, including on:
Electricity
➕
Water
➕
Energy Transition
➕
Hydrogen
➕
Roads, Rail and Ports
➕
Coal
➕
Gold
➕
Platinum
➕
Battery Metals
➕
etc.
Receive all benefits from Option 1 or Option 2 delivered to numerous people at your company
➕
Multiple User names and Passwords for simultaneous log-ins
➕
Intranet integration access to all in your organisation