Opportunities to be had in pumps industry
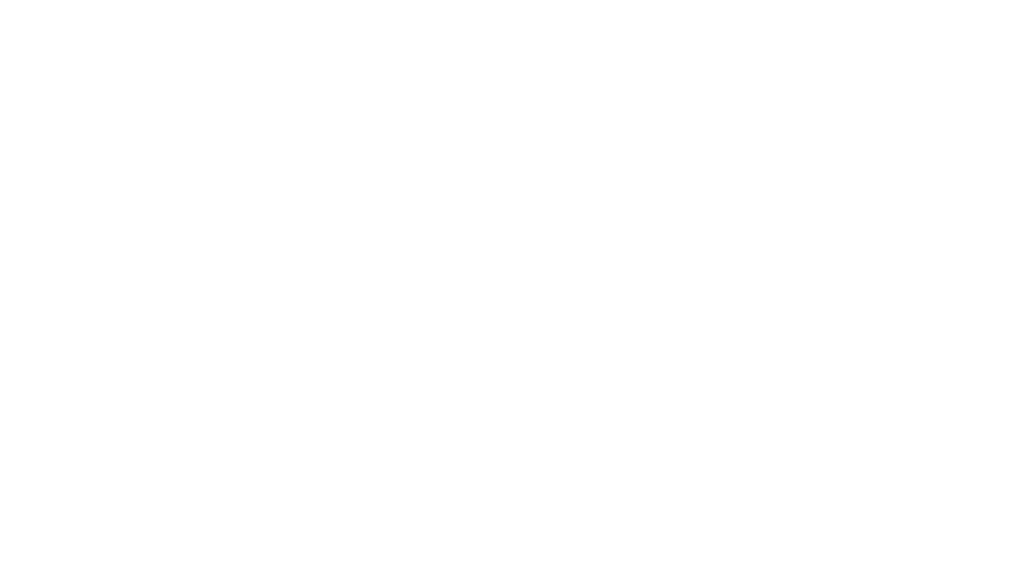
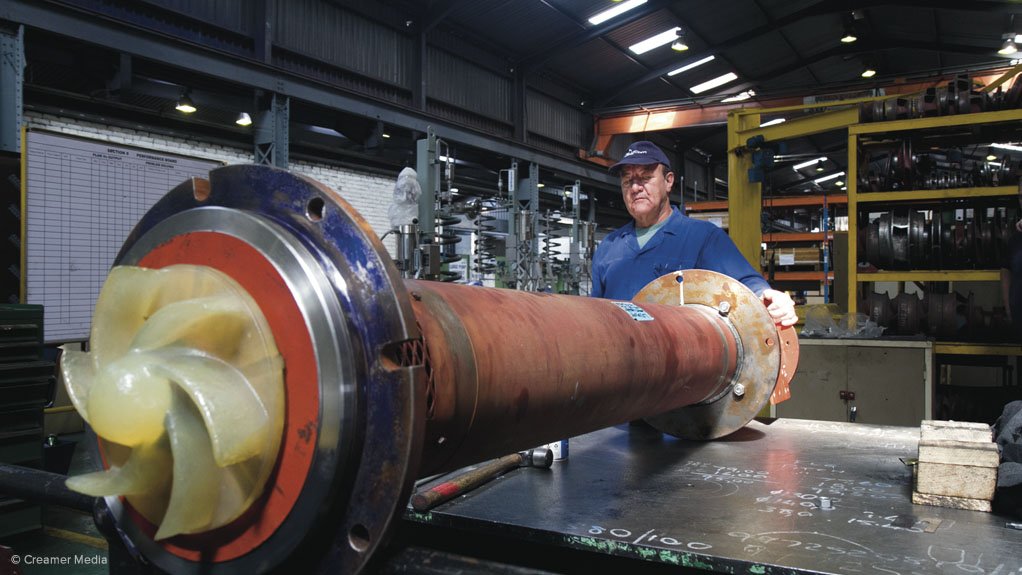
OLD HAT Pumping technology is fairly old, with an understanding of underlying engineering principles well entrenched, and is only expanded on when a need arises
There are a myriad of opportunities in the pumps industry to develop it, propel its growth and improve efficiency, avers independent process industry consultant Santosh Gunpath.
A potential area of development in the mining pumps industry lies in the better understanding and the holistic use of simulation software by clients, design houses and original-equipment manufacturers (OEMs), he adds. These entities should consider elements like the piping system in its entirety when approaching developments, rather than a myopic focus on the pump itself.
He explains that piping systems comprise elements, including pumps, flow control and piping, which need to work together harmoniously to meet specified design requirements and reduce total life cycle costs.
“Different engineering disciplines select each of these elements and incorporate them into a design, only to uncover many costly oversights during the initial start-up, which delays investment return. Better use of intelligent simulation software coupled with thorough analysis could eliminate this.”
Gunpath believes that, in the pumps industry, there exists much potential for the mining sector and OEMs to achieve cost reductions, specifically in terms of mine rehabilitation projects, and improving pumps efficiency respectively.
He notes that South African mining companies often concentrate on dewatering extinct mining operations for rehabilitation purposes, and, critically, at the lowest rand-per-ton cost, because such operations are often nonrevenue-generating activities. This focus on a frugal approach presents a challenge, which must then be managed.
A well-designed piping system encompassing piping, pumps and valves harmoniously working together will achieve this cost reduction, says Gunpath. He suggests that mining companies capitalise on their rehabilitation efforts in conjunction with OEMs (and in some cases their in-house design teams) to design at the lowest rand-per-ton cost, rather than adopting a traditional off-the-shelf design that may not necessarily be the most efficient. “This approach represents a higher design cost but, potentially, lower operational expense.”
Gunpath does not share the sentiment that all pumps have reached peak efficiency. OEMs should focus on becoming more efficient, as delivering a more efficient product will assist clients, potentially freeing up capital for further investment and, thereby, create greater demand for pumps among other processing equipment, owing to further potential project development.
“Pumping can account for up to 25% of a plant’s total motor energy usage; improving efficiency can save more than 40% of all energy costs, which will ultimately drive the sector forward.”
He believes pumps-related energy costs can be reduced through low- and high-frequency vibration monitoring. Low-frequency monitoring can be used to indicate structural, balance and alignment deficiencies, and high-frequency monitoring to detect bearing and gear train defaults. Further, he points to improving the pump power factor – the measure of how efficiently electricity is being used – to yield greater productivity for every unit of power consumed.
The development of monitoring devices and remote monitoring to address predictive maintenance is a critical component of ensuring efficient operations, Gunpath says, emphasising that further development of remote monitoring and reaction should be prioritised in line with the future trend of off-site operational control. This is evident at mines in the Pilbara region of Western Australia, which are monitored and controlled from Perth.
He suggests that all major OEMs in South Africa commit to responding to industry requirements and continue product development, noting that continuous research is being undertaken globally to identify more robust materials from which to manufacture components such as the impellor casings and seals.
Leading Innovation
Gunpath says low-grade, high-throughput copper operations in South America have been at the forefront of successful innovation in the global mining industry, with support from large OEMs. He points to the oil sands sector as another driver in “super pump” development, mentioning the Aurora Hydrotransport system, a pump that runs for 6 000 hours and only has one major outage a year, rather than three major outages a year.
“Success is driven by innovation, which, in turn, is driven by the need to solve a problem such as the cost-effective transport of large volumes.”
He further explains that, because pumping technology is fairly old, with an understanding of underlying engineering principles well entrenched, these are only expanded on when a need arises, as undertaking an academic exercise is expensive and is by no means guaranteed to generate profit.
The South African pumps industry will drive itself forward by ‘industrial natural selection’, which translates to “innovate or stagnate”, he lyricises.
However, Gunpath notes, as an example, that an alternative design solution to drive efficiency involves addressing the standard for standby pumps. While this need is acceptable for small applications, “super pumps”, employed by large mining operations, represent a significant capital cost. Using smaller standby pumps, or their total elimination from the flowsheet, at such operations, will be a major step forward in cost reduction. He cautions that this must, however, be undertaken in conjunction with the associated risks.
Comments
Announcements
What's On
Subscribe to improve your user experience...
Option 1 (equivalent of R125 a month):
Receive a weekly copy of Creamer Media's Engineering News & Mining Weekly magazine
(print copy for those in South Africa and e-magazine for those outside of South Africa)
Receive daily email newsletters
Access to full search results
Access archive of magazine back copies
Access to Projects in Progress
Access to ONE Research Report of your choice in PDF format
Option 2 (equivalent of R375 a month):
All benefits from Option 1
PLUS
Access to Creamer Media's Research Channel Africa for ALL Research Reports, in PDF format, on various industrial and mining sectors
including Electricity; Water; Energy Transition; Hydrogen; Roads, Rail and Ports; Coal; Gold; Platinum; Battery Metals; etc.
Already a subscriber?
Forgotten your password?
Receive weekly copy of Creamer Media's Engineering News & Mining Weekly magazine (print copy for those in South Africa and e-magazine for those outside of South Africa)
➕
Recieve daily email newsletters
➕
Access to full search results
➕
Access archive of magazine back copies
➕
Access to Projects in Progress
➕
Access to ONE Research Report of your choice in PDF format
RESEARCH CHANNEL AFRICA
R4500 (equivalent of R375 a month)
SUBSCRIBEAll benefits from Option 1
➕
Access to Creamer Media's Research Channel Africa for ALL Research Reports on various industrial and mining sectors, in PDF format, including on:
Electricity
➕
Water
➕
Energy Transition
➕
Hydrogen
➕
Roads, Rail and Ports
➕
Coal
➕
Gold
➕
Platinum
➕
Battery Metals
➕
etc.
Receive all benefits from Option 1 or Option 2 delivered to numerous people at your company
➕
Multiple User names and Passwords for simultaneous log-ins
➕
Intranet integration access to all in your organisation