Optimising transfer points in brownfields projects
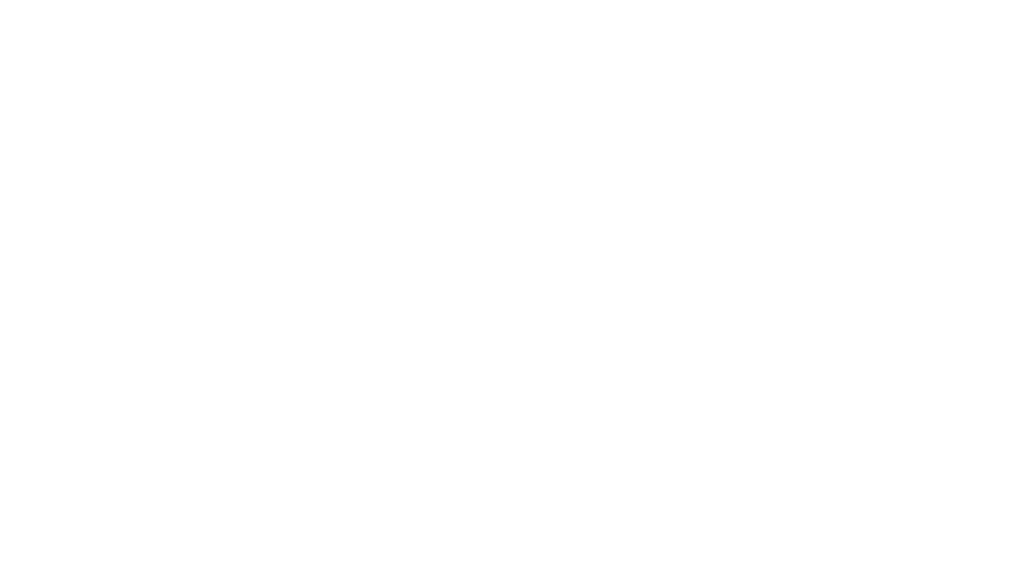
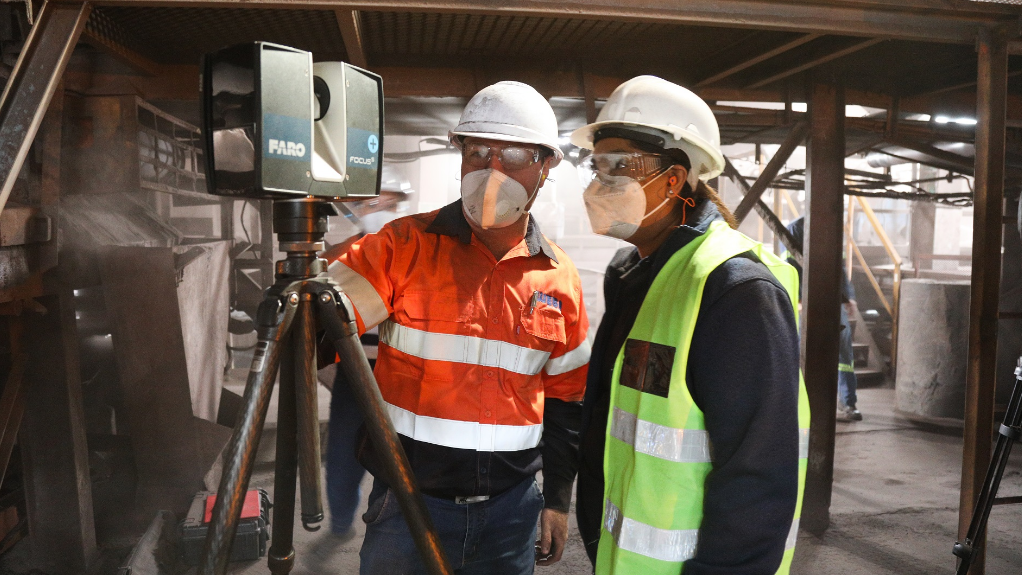
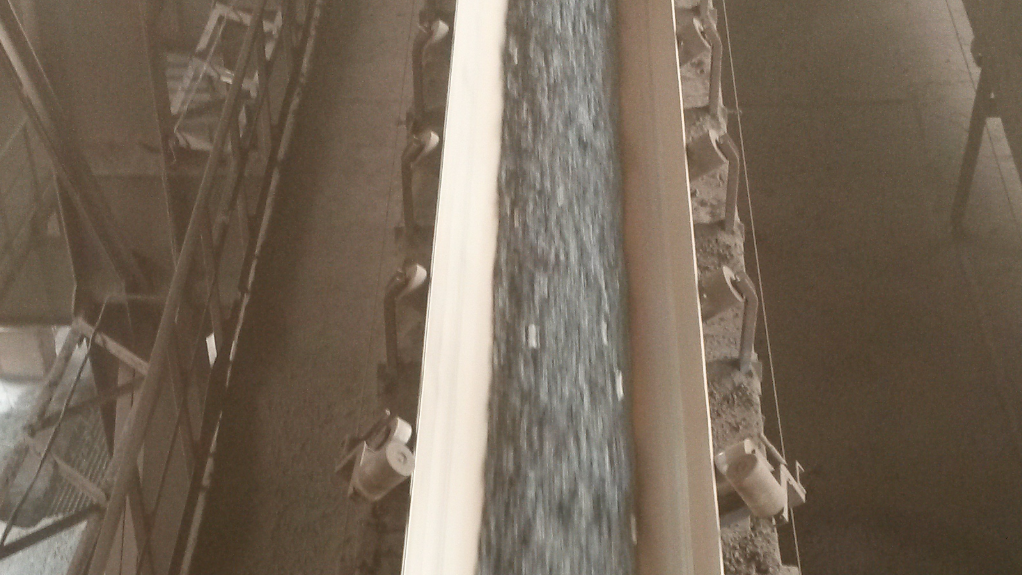
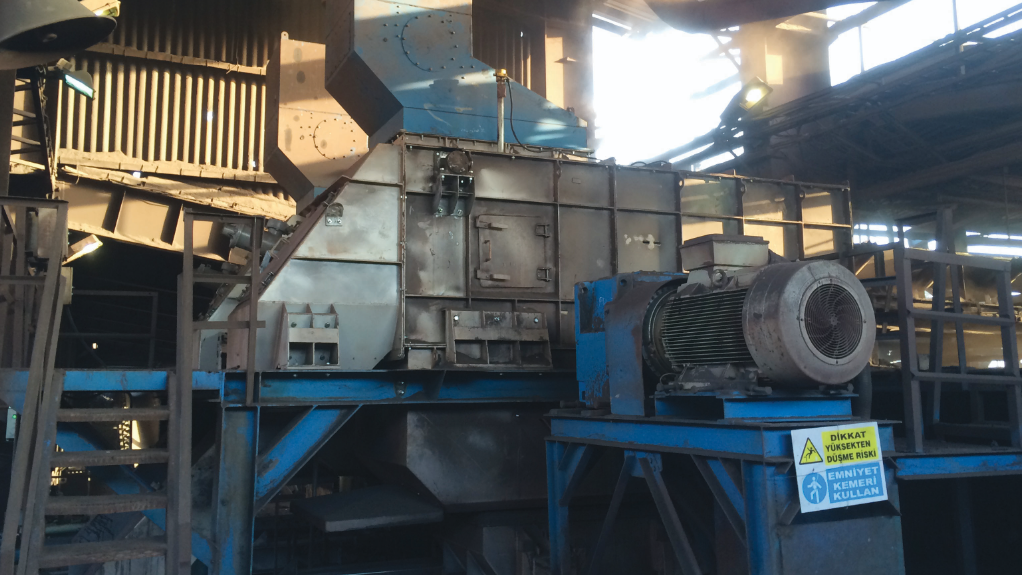
Weba Chute Systems Technical Manager, Dewald Tintinger and Director Denise Abrahams during a site survey at a steel plant
Central belt loading being discharged from a Weba chute at a steel plant in Turkey
Weba chutes, with samplers, installed at a steel plant in Turkey
This article has been supplied.
As mining companies embark on brownfields initiatives to meet rising market demand for battery and other minerals, the optimising of transfer points presents a valuable opportunity to deliver more output cost effectively.
Alwin Nienaber, Technical Director at Weba Chute Systems, says that when correctly used technology and experience provide a powerful combination when expanding production capacity. Technology can be leveraged to facilitate rapid and accurate scanning of the existing configuration of infrastructure into which the improved chutes are to be installed. Further, he says, the company brings a wealth of expertise to advise on valuable adjustments in the relationship between chutes and other equipment.
“Custom engineered chutes and transfer points have been shown to facilitate smoother flow of mined material, with greater reliability and uptime for a more streamlined and productive operation,” explains Nienaber. “The initial focus when providing transfer point solutions to a brownfields project is usually to take careful note of the physical layout so that chutes are designed with spatial constraints in mind.”
This can be most accurately and efficiently achieved using 3D laser scanning of the existing layout, to rapidly gather detailed measurements of large infrastructure on a customer’s site. Using this data, a precise 3D model can be generated on the basis of which the necessary chutes and componentry can be designed and manufactured.
“This aligns well with Weba Chute Systems’ considerable in-house expertise in chute design, as each chute we build is unique to the application it serves,” Nienaber says. “It is important to remember that every transfer point exists in a relationship to other equipment, such as a screen, crusher or conveyor belt.”
He highlights that an understanding of this relationship will underpin the productive application of transfer point design and installation. Indeed, while the 3D scanning and modelling technology provides a valuable starting point for design there is also scope for added improvements in the plant layout.
“On so many of the sites that we visit and assess, we can soon identify where changes in the relationship between the transfer points and other equipment can deliver better results,” says Nienaber. “While it is sometimes difficult – even costly – to implement some of these changes, the customer reaps many times the value in terms of uninterrupted volume flow, uptime and productivity.”
The first prize when installing transfer points, he emphasises, is always the optimal solution – which may mean reconsidering the position of the upstream and downstream equipment. In fact, this is always the starting point for Weba Chute Systems’ transfer point solutions: to achieve the most productive result for the customer.
“With our engineered design approach, we always consider the context of where our chutes are going to operate, and our decades of field experience allow us to advise the customer what will work best,” he says. “We might advise on how adjusting the position of a conveyor’s head pulley, for instance, would improve chute performance and overall plant efficiency.”
He notes that, while certain configuration changes might exceed budget constraints, the company’s intervention often allows for positive modifications to be made. A recent example of this was in a contract for a South African iron ore producer in the Northern Cape. Weba Chute Systems was asked to address the mine’s challenge where an existing competitor’s chute needed attention every two days which was severely hampering production.
“We designed and installed the optimal customised chute, but also recommended some related adjustments,” he says. “The design was a split chute, and the plant needed to speed up its conveyor quite considerably – as well as lifting the head pulley slightly – to achieve the necessary results.”
The changes recommended had financial implications, so the customer required considerable certainty that the solution would be successful. To underpin its plan, Weba Chute Systems digitally modelled the proposed design and simulated its operation using software that visualised the movement of material through the chute.
“Used by our skilled designers, this powerful software delivers more than a pretty picture,” emphasises Nienaber. “The simulation presents in video format exactly how equipment will be positioned and how material will flow through the system.”
Fundamental to these kinds of solutions, of course, is a close collaboration with the customer, built on a high level of trust in the company’s past performance. Aligned to this is Weba Chute Systems’ commitment to see through any project it embarks upon, he says.
“Our customers know we never walk away from a project – and this is an important factor in brownfields projects where one is often working within existing constraints rather than a clean slate,” he argues. “We have confidence in our people and our designs, and remain accountable for any solution we provide until it performs to levels we have promised.”
Another important factor in many projects is the level of degradation of mined material, which the company prides itself on reducing through its scientific, streamlined approach to the dynamics of bulk materials handling.
“An example of where this was important was a steel plant in Turkey where we installed a number of our chutes,” he explains. “The customer required minimal ore degradation, and even monitors the ore passing through each chute to ensure fines generation is kept to a minimum.”
Weba Chute Systems was required to incorporate samplers in its installations in this plant, and these samplers generate the data to verify the chutes are performing to expectation. The company’s custom design allows greater control over the direction, flow and velocity of material, whose volume and characteristics are specific to each application.
Comments
Press Office
Announcements
What's On
Subscribe to improve your user experience...
Option 1 (equivalent of R125 a month):
Receive a weekly copy of Creamer Media's Engineering News & Mining Weekly magazine
(print copy for those in South Africa and e-magazine for those outside of South Africa)
Receive daily email newsletters
Access to full search results
Access archive of magazine back copies
Access to Projects in Progress
Access to ONE Research Report of your choice in PDF format
Option 2 (equivalent of R375 a month):
All benefits from Option 1
PLUS
Access to Creamer Media's Research Channel Africa for ALL Research Reports, in PDF format, on various industrial and mining sectors
including Electricity; Water; Energy Transition; Hydrogen; Roads, Rail and Ports; Coal; Gold; Platinum; Battery Metals; etc.
Already a subscriber?
Forgotten your password?
Receive weekly copy of Creamer Media's Engineering News & Mining Weekly magazine (print copy for those in South Africa and e-magazine for those outside of South Africa)
➕
Recieve daily email newsletters
➕
Access to full search results
➕
Access archive of magazine back copies
➕
Access to Projects in Progress
➕
Access to ONE Research Report of your choice in PDF format
RESEARCH CHANNEL AFRICA
R4500 (equivalent of R375 a month)
SUBSCRIBEAll benefits from Option 1
➕
Access to Creamer Media's Research Channel Africa for ALL Research Reports on various industrial and mining sectors, in PDF format, including on:
Electricity
➕
Water
➕
Energy Transition
➕
Hydrogen
➕
Roads, Rail and Ports
➕
Coal
➕
Gold
➕
Platinum
➕
Battery Metals
➕
etc.
Receive all benefits from Option 1 or Option 2 delivered to numerous people at your company
➕
Multiple User names and Passwords for simultaneous log-ins
➕
Intranet integration access to all in your organisation