Sorting tech unlocks value from tainted material
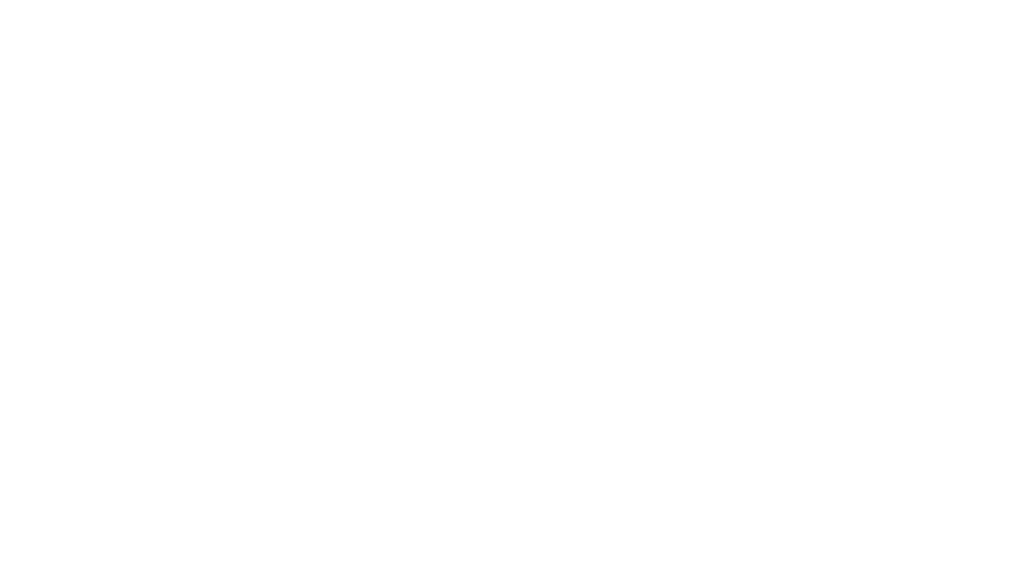
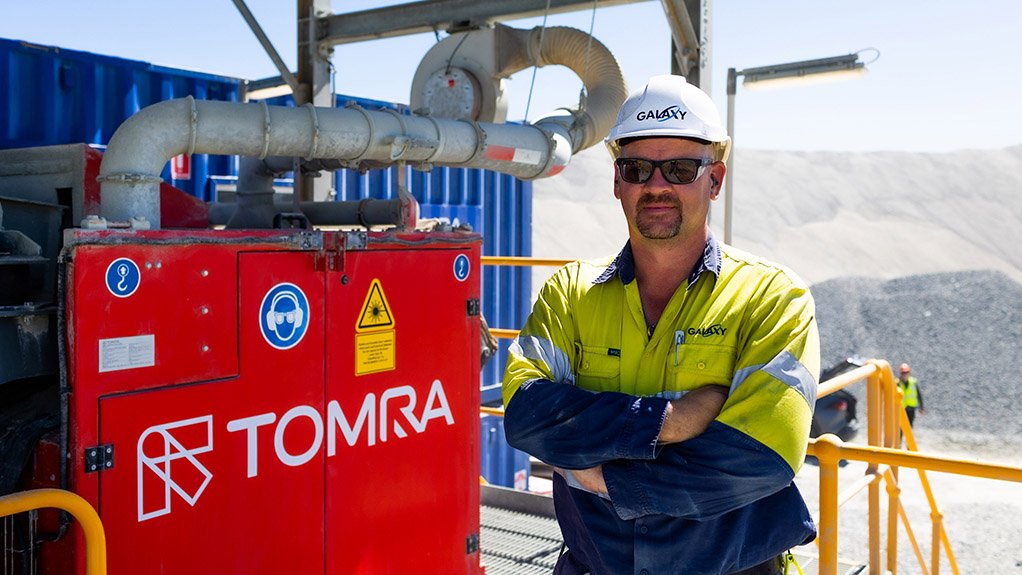
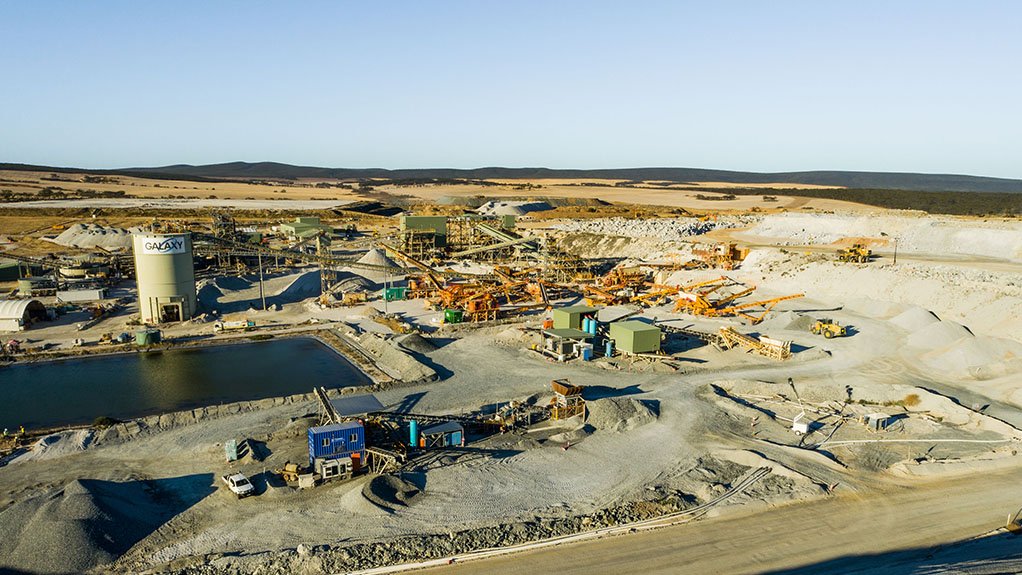
SCOTT GREEN The TOMRA PRO Secondary Laser has exceeded Galaxy Resources' expectation
MT CATTLIN LITHIUM MINE Demand for spodumene has increased owing to its use in batteries
Lithium mines often face the challenge of basalt contamination. The Mt Cattlin openpit lithium concentrate, or spodumene, mine uses a two-stage crushing system followed by dense medium separation (DMS) gravity recovery as the primary spodumene concentration process. Owing to basalt’s high density – similar to that of spodumene – the high-iron, barren material is also concentrated by the DMS, contaminating the final product.
ASX-listed company Galaxy Resources’ Mt Cattlin mine, located in the Great Southern region of Western Australia, produces high-quality spodumene concentrate for the global lithium market. The demand for this commodity is ballooning owing to the role of lithium and lithium-ion batteries in mobile devices and in electric vehicles.
While it is key to mine ore that is as clean as possible, there will always be contamination, mainly associated with contact or when there are basalt intrusions into the pegmatite, Mt Cattlin GM Keith Muller explains.
In such cases, lithium is present in what is mined; however, it is heavily contaminated with basalt. Galaxy Resources segregates that from clean ore sources, and stockpiles it to be processed at a later stage.
The Solution
Galaxy Resources has stockpiled contaminated lithium since 2016, while searching for an effective solution to treat it prior to processing to achieve a viable recovery level.
In 2019, Galaxy Resources installed optical sorters at the front-end of the plant to upgrade the low-grade ore. When it could not achieve the desired results, the company decided to explore other possible solutions with ore- processing equipment supplier TOMRA Mining.
Successful testwork at the TOMRA Test Centre revealed that the TOMRA PRO Secondary Laser sorter would be an effective solution. TOMRA’s team was confident of its performance, agreeing to the very tight performance guarantees set by Galaxy Resources.
The sorter has been operating since September 29, 2021, sorting the contaminated low-grade ore.
Muller explains that the ore is screened into two size ranges, 14 mm to 25 mm and 25 mm to 75 mm, then fed into the sorter. The sorter product is then recirculated into the crushing circuit, crushed down to a -14 mm particle size and fed into the wet plant and DMS.
Since the first day of operation, it has met and exceeded Galaxy Resources’ expectations. The mine’s target is to have 4% basalt in the product when it comes out of the TOMRA sorter; it has been consistently below this mark, says Galaxy Resources process enhancement coordinator Scott Green.
“It’s been continuous, there hasn’t been a degradation in performance. The sorter has worked well from the start and six months in, it’s still performing as well as it did with the initial acceptance testing. We have pushed the boundaries of the industry standard in particle size and feed rate, and we haven’t found the limit of the machine yet,” adds Muller.
“We have 1.2-million tonnes to treat, and we will have treated the best part of it in nine to 12 months. With the TOMRA sorter, we are using far more contaminated ore than we would previously have processed,” adds Galaxy Resources principal metallurgist Matthew Bateman.
On the back of the TOMRA PRO Secondary Laser sorter’s success, Galaxy Resources has acquired a second unit to expand secondary ore sorting capacity.
Simple and Effective
Installation was completed seamlessly despite the complication owing to the Covid-19 pandemic. TOMRA provided careful planning with effective virtual support from TOMRA’s team throughout the process.
“In terms of commissioning, I was very surprised at how quickly and easily it went, especially with the constraints on travelling. When we commissioned the TOMRA unit, we still had border closures, so everything was done remotely, and it went smoothly without any issues,” says Muller.
“It can’t be said enough how valuable it was to have the availability of TOMRA’s team whenever we needed it, especially when remotely commissioning a machine we had never dealt with before,” adds Green.
The training TOMRA provided for the Mt Cattlin operators and maintenance teams also contributed to the smooth startup.
In addition, TOMRA PRO Secondary Laser sorter is remarkably user-friendly. Operators at the mine like the simplicity of the human-machine interface of the sorter’s control panel.
Simplified maintenance is another advantage of the sorter. The mine uses the sorter on a continuous basis. When sorting is on the small size fraction, there is a significant amount of mica which then needs to be cleaned out every one to four hours, depending on how muddy it is.
“On the 75 mm fraction, we can go six to seven hours without stopping to clean. And it only takes about 20 minutes, so it’s back up and running very,” says Green.
In terms of routine maintenance, the mine uses the scheduled weekly shutdown for maintenance of the infrastructure to give it a thorough clean and check-up, he concludes.
Comments
Press Office
Announcements
What's On
Subscribe to improve your user experience...
Option 1 (equivalent of R125 a month):
Receive a weekly copy of Creamer Media's Engineering News & Mining Weekly magazine
(print copy for those in South Africa and e-magazine for those outside of South Africa)
Receive daily email newsletters
Access to full search results
Access archive of magazine back copies
Access to Projects in Progress
Access to ONE Research Report of your choice in PDF format
Option 2 (equivalent of R375 a month):
All benefits from Option 1
PLUS
Access to Creamer Media's Research Channel Africa for ALL Research Reports, in PDF format, on various industrial and mining sectors
including Electricity; Water; Energy Transition; Hydrogen; Roads, Rail and Ports; Coal; Gold; Platinum; Battery Metals; etc.
Already a subscriber?
Forgotten your password?
Receive weekly copy of Creamer Media's Engineering News & Mining Weekly magazine (print copy for those in South Africa and e-magazine for those outside of South Africa)
➕
Recieve daily email newsletters
➕
Access to full search results
➕
Access archive of magazine back copies
➕
Access to Projects in Progress
➕
Access to ONE Research Report of your choice in PDF format
RESEARCH CHANNEL AFRICA
R4500 (equivalent of R375 a month)
SUBSCRIBEAll benefits from Option 1
➕
Access to Creamer Media's Research Channel Africa for ALL Research Reports on various industrial and mining sectors, in PDF format, including on:
Electricity
➕
Water
➕
Energy Transition
➕
Hydrogen
➕
Roads, Rail and Ports
➕
Coal
➕
Gold
➕
Platinum
➕
Battery Metals
➕
etc.
Receive all benefits from Option 1 or Option 2 delivered to numerous people at your company
➕
Multiple User names and Passwords for simultaneous log-ins
➕
Intranet integration access to all in your organisation