Powerful system commissioned at Chile mine
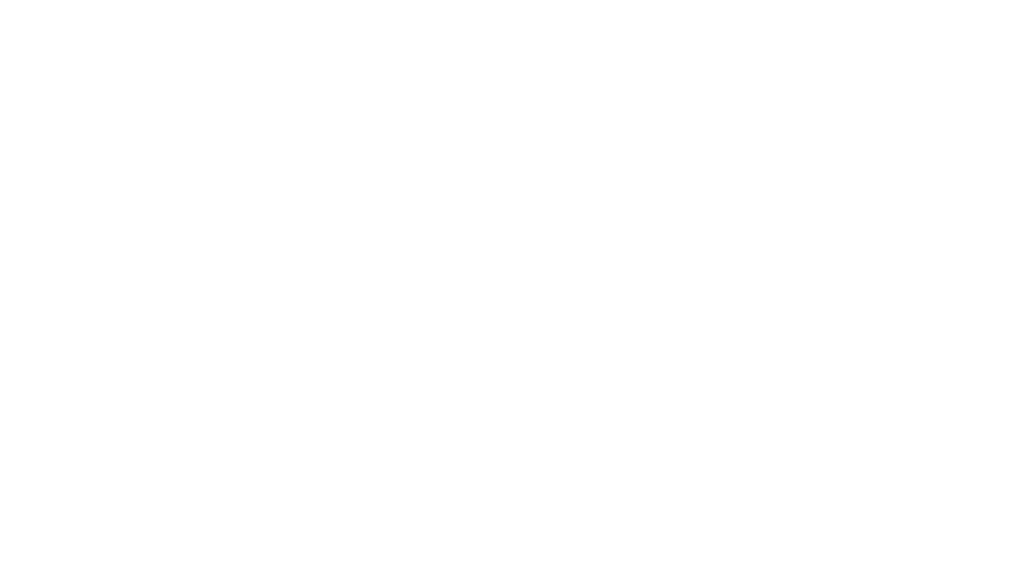
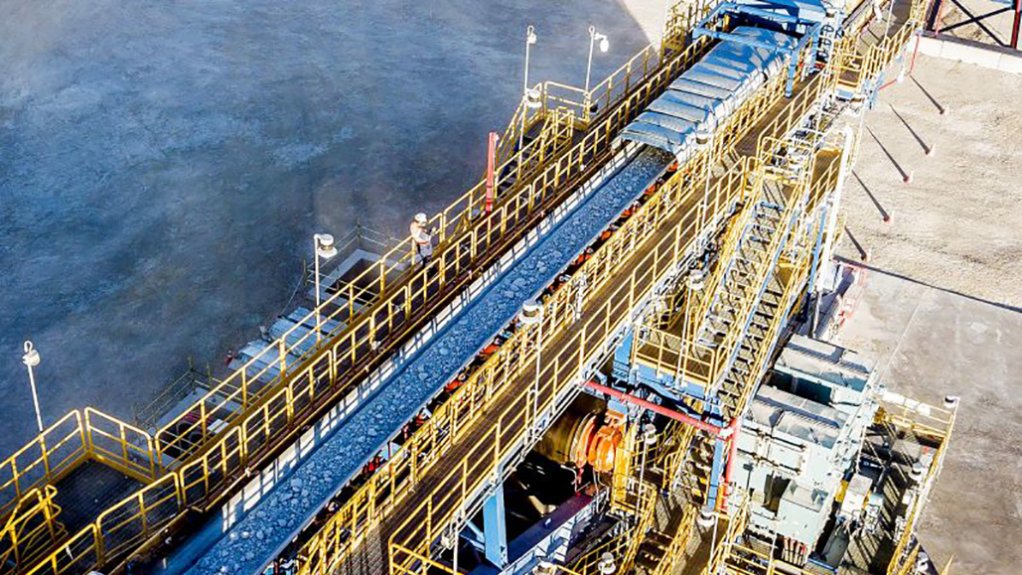
CAPABLE SYSTEM TAKRAF’s 58 MW belt conveyor system at the Chuquicamata mine in Chile transports ore along a 7 km underground tunnel that overcomes 1 km of vertical elevation change
While attending this year’s Beltcon International Materials Handling Conference in Johannesburg over August 2 and 3, mining equipment manufacturer TAKRAF showcased what it claims is the “world’s most powerful belt conveyor system” that was commissioned in Chile.
At the conference, TAKRAF delivered a paper titled ‘Chuquicamata Underground Mine Project, Powerful Conveyors with Gearless Drives in Operation’ which detailed its large belt conveyor installation for the Chuquicamata mine, owned by State-owned copper miner Codelco, and which is located in the Atacama Desert of northern Chile.
TAKRAF Germany belt conveyor systems head Dr Mario Dilefeld explained that the paper delves into TAKRAF’s design and delivery of the powerful belt conveyor system in Chile and the numerous innovations that resulted in six patents being implemented.
“This mega materials handling project, boasting a total installed drive power of 58 MW, boasts highly efficient electric drive motors, which replaced diesel truck engines, and resulted in emissions produced by transporting the material being reduced by more than two-thirds for the same copper production volume,” he said.
Total installed drive power for the entire system, including various feeder conveyors, is derived from eleven 5 MW gearless, synchronous motors.
Further to Dilefeld’s paper, the TAKRAF South Africa team was also present with a stand where event visitors were able to engage with its engineering specialists regarding development of the world’s future reserves as renewed interest, specifically around future-facing commodities, spurs investment in the mining industry.
Unique Design
TAKRAF’s innovative belt conveyor system transports crushed copper from underground storage bins to the surface along a 7 km underground tunnel that overcomes a not-insignificant 1 km of vertical elevation change.
Once on the surface, ore is then fed on to an overland conveyor that transports it the final 6 km to a distribution silo.
The underground system, comprising two conveyors of about equal length, and the overland conveyor, boast advanced gearless drive technology provided by TAKRAF’s drive technology partner, digital systems manufacturer ABB.
Gearless drives eliminate the need for a gearbox, thereby significantly reducing the number of main wear parts, which results in increased efficiency and reliability, as well as a reduced maintenance requirement.
Further advantages include a considerable reduction in the drive system’s carbon footprint and associated emissions; the emissions are reduced by 66%, when compared with diesel truck engines for the same copper production volume.
Another significant achievement for TAKRAF is the company’s installation of a newly developed steel cord belt – the ST10000 – on the uphill tunnel conveyors of the mine, thereby marking the first instance in which this new technology was deployed.
“This megaproject achieves a number of world firsts, from the system’s total installed drive power to the first global application of the ST10 000 conveyor belt,” says TAKRAF project manager Marc Hollinger.
He enthused that this project firmly entrenches TAKRAF as a capable conveyor provider capable of delivering a megaproject of this nature, incorporating advanced technologies.
“This project will go down in the record books as a defining moment for our client and we are very proud to be a part of this,” Hollinger concludes.
Comments
Announcements
What's On
Subscribe to improve your user experience...
Option 1 (equivalent of R125 a month):
Receive a weekly copy of Creamer Media's Engineering News & Mining Weekly magazine
(print copy for those in South Africa and e-magazine for those outside of South Africa)
Receive daily email newsletters
Access to full search results
Access archive of magazine back copies
Access to Projects in Progress
Access to ONE Research Report of your choice in PDF format
Option 2 (equivalent of R375 a month):
All benefits from Option 1
PLUS
Access to Creamer Media's Research Channel Africa for ALL Research Reports, in PDF format, on various industrial and mining sectors
including Electricity; Water; Energy Transition; Hydrogen; Roads, Rail and Ports; Coal; Gold; Platinum; Battery Metals; etc.
Already a subscriber?
Forgotten your password?
Receive weekly copy of Creamer Media's Engineering News & Mining Weekly magazine (print copy for those in South Africa and e-magazine for those outside of South Africa)
➕
Recieve daily email newsletters
➕
Access to full search results
➕
Access archive of magazine back copies
➕
Access to Projects in Progress
➕
Access to ONE Research Report of your choice in PDF format
RESEARCH CHANNEL AFRICA
R4500 (equivalent of R375 a month)
SUBSCRIBEAll benefits from Option 1
➕
Access to Creamer Media's Research Channel Africa for ALL Research Reports on various industrial and mining sectors, in PDF format, including on:
Electricity
➕
Water
➕
Energy Transition
➕
Hydrogen
➕
Roads, Rail and Ports
➕
Coal
➕
Gold
➕
Platinum
➕
Battery Metals
➕
etc.
Receive all benefits from Option 1 or Option 2 delivered to numerous people at your company
➕
Multiple User names and Passwords for simultaneous log-ins
➕
Intranet integration access to all in your organisation