Pump tackles acidic liquids containing solids
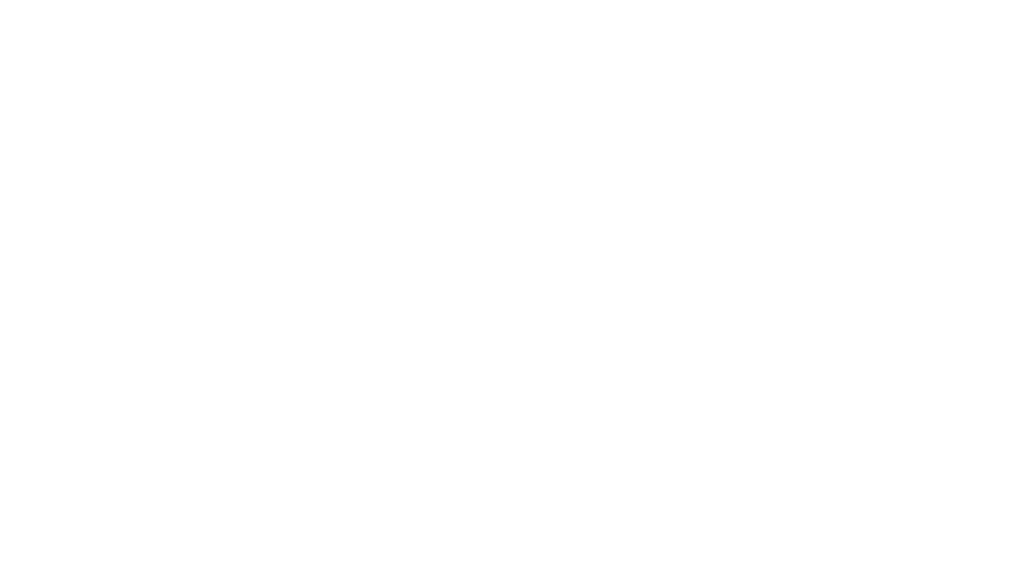
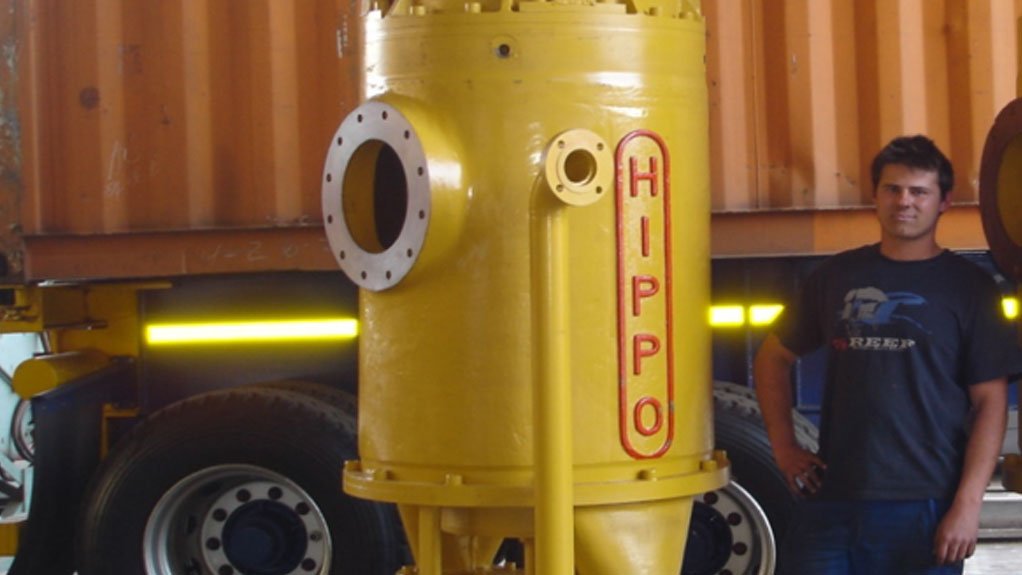
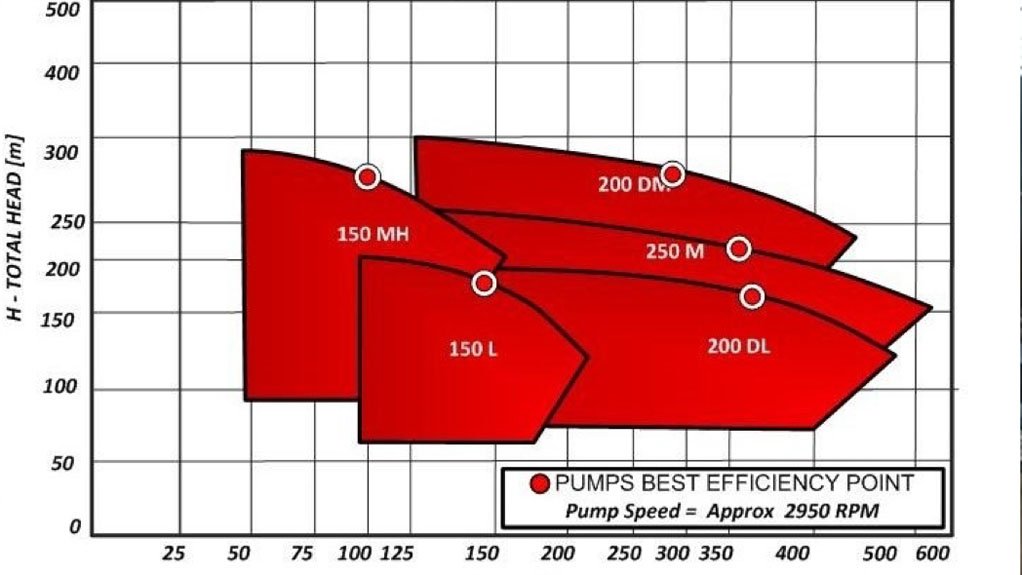
PUMP INSPIRATION The design of the high-volume, high-head, medium- and/or high-voltage Hippo pump follows the success of the submersible slurry pump developed for export to the oil sands mines at Fort McMurray, in Alberta, Canada
EFFICIENCY CURVE The high-volume, high-head Hippo pumps range consists of five models, designed to operate at 50 Hz
Centurion-based pumps manufacturer Hazleton Pumps has introduced a high-volume, high-head, medium- and/or high-voltage range of Hippo submersible slurry pumps manufactured from specialised material capable of pumping acidic liquids containing solids at high heads.
The company says the success of research and development of the high-volume, high-head, medium- and/or high-voltage Hippo slurry submersible pump has led to it being a world leader in the supply of this product – with no other pumps manufacturer having a similar product available.
Hazleton attributes the design and development of this pump to the harsh mining conditions in Southern Africa, which require submersible pumps to pump high volumes of liquid containing solids at high heads.
The range, consisting of five models, uses a single-stage impeller operating at two-pole speed (2 950 rpm) and, with an installed power of up to 2 500 kW, has been developed for both a 50 Hz as well as a 60 Hz power supply.
The design of the high- volume, high-head, medium- and/or high-voltage pump follows the success of the medium- and/or high-voltage, high-volume submersible slurry pump that was first developed in 2005 and exported to the oil sands mines at Fort McMurray, in Alberta, Canada.
Proven Design
The proven Hippo submersible slurry pump design with standard configuration has been used for the pumping of high-volume liquids containing solids with the main feature of the Hippo configuration being the twin volute discharge balanced thrust design in which all the radial forces on the impeller are balanced out, resulting in lower loading on the bearings.
The motor housing is oil filled, similar to the case of a transformer, assisting with the dissipating of heat away from the electrical windings, thus, allowing the pumps to run dry continuously. The oil also lubricates the bearings and the mechanical shaft seals. Double mechanical shaft seals are used, with the lower seal in a separate oil chamber.
Using the cantilever shaft design, the mechanical shaft seals are at submergence pressure and not at the pump discharge pressure – which is the case in most other submersible pump configurations.
The standard material of construction of the hydraulic end is 28% hard chrome with the rest of the castings being Mehanite CB3, giving the pump the ability to pump abrasive slurries, with an acid content of pH4 and above. For acidic conditions (lower than a pH4), specialised materials such as duplex stainless steel are used.
The company explains that the major application of the pumps would be for use in acid mine dewatering. The pumps can be connected in series to achieve any desired head and are specifically used in mine dewatering application at the shaft bottom.
“Underground flooding is a reality and the high- volume Hippo submersible slurry pump is well suited for these conditions. “Using the medium-voltage power of 3.3 kV or 6.6. kV, the pumps can be switched on and controlled from the surface or an alternative dry location,” says Hazleton.
The design also includes probes that have been installed close to the mechanical seals, which monitor the conductivity of the oil. Should the mechanical shaft seals wear and start to leak, the oil will become contaminated. The probe will detect the change in resistance of the oil and switch the pump off before the electrical winding fails.
The major failure of submersible pumps is due to the electrical winding of the submersible pump failing as a result of the failure of the mechanical seals, which allows the slurry being pumped to come into contact with the electrical winding. Rewinding of the stator contributes to more than 50% of the total repair cost and, if this can be avoided, the total cost of ownership is drastically reduced.
Using a stepped impeller intake sealing system (trademarked with a patent pending) with centring bush and balancing rings, the challenges are overcome. Hazleton explains that the research into the stepped impeller intake sealing system was conducted in 2015, with trials successfully completed on the smallest Hippo submersible pumps available.
The principle is that the impeller outer intake shroud is designed with a minimum of three steps, one of which is the centring bush that ensures minimal leakage from high-pressure impeller discharge to low-pressure impeller intake.
The impeller is also fitted with a minimum of one pressure balancing ring at the bottom of its shroud to limit the axial forces on the impeller. A second balancing ring is fitted to the top and bottom shroud as close to the impeller discharge as possible.
The design is based on changing the flow direction by 90º with minimum clearance as many times as possible to reduce the pressure across the steps and this principle applies to both the impeller intake as well as to the pressure balancing rings.
Comments
Press Office
Announcements
What's On
Subscribe to improve your user experience...
Option 1 (equivalent of R125 a month):
Receive a weekly copy of Creamer Media's Engineering News & Mining Weekly magazine
(print copy for those in South Africa and e-magazine for those outside of South Africa)
Receive daily email newsletters
Access to full search results
Access archive of magazine back copies
Access to Projects in Progress
Access to ONE Research Report of your choice in PDF format
Option 2 (equivalent of R375 a month):
All benefits from Option 1
PLUS
Access to Creamer Media's Research Channel Africa for ALL Research Reports, in PDF format, on various industrial and mining sectors
including Electricity; Water; Energy Transition; Hydrogen; Roads, Rail and Ports; Coal; Gold; Platinum; Battery Metals; etc.
Already a subscriber?
Forgotten your password?
Receive weekly copy of Creamer Media's Engineering News & Mining Weekly magazine (print copy for those in South Africa and e-magazine for those outside of South Africa)
➕
Recieve daily email newsletters
➕
Access to full search results
➕
Access archive of magazine back copies
➕
Access to Projects in Progress
➕
Access to ONE Research Report of your choice in PDF format
RESEARCH CHANNEL AFRICA
R4500 (equivalent of R375 a month)
SUBSCRIBEAll benefits from Option 1
➕
Access to Creamer Media's Research Channel Africa for ALL Research Reports on various industrial and mining sectors, in PDF format, including on:
Electricity
➕
Water
➕
Energy Transition
➕
Hydrogen
➕
Roads, Rail and Ports
➕
Coal
➕
Gold
➕
Platinum
➕
Battery Metals
➕
etc.
Receive all benefits from Option 1 or Option 2 delivered to numerous people at your company
➕
Multiple User names and Passwords for simultaneous log-ins
➕
Intranet integration access to all in your organisation