Suppliers partner to deliver project
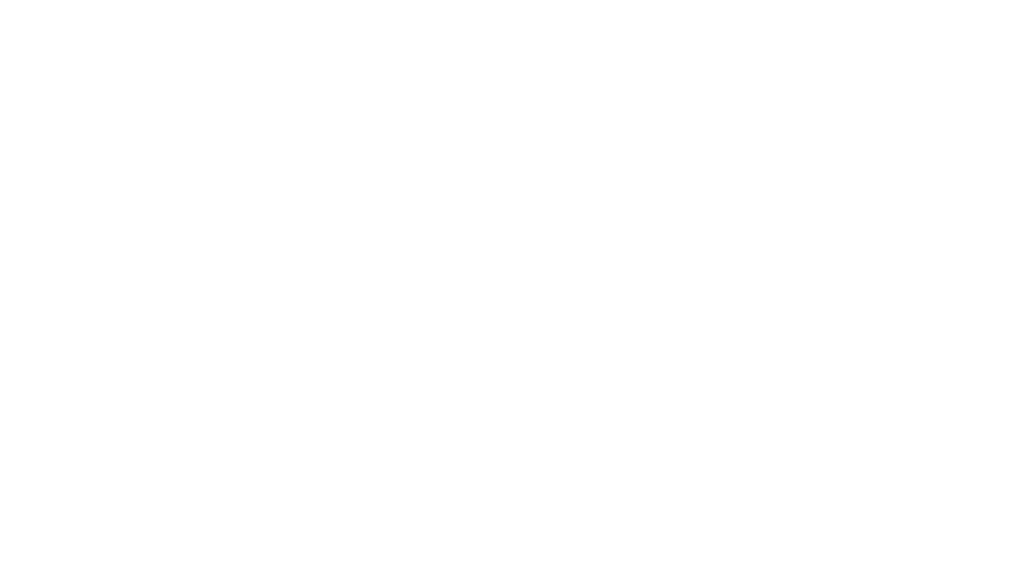
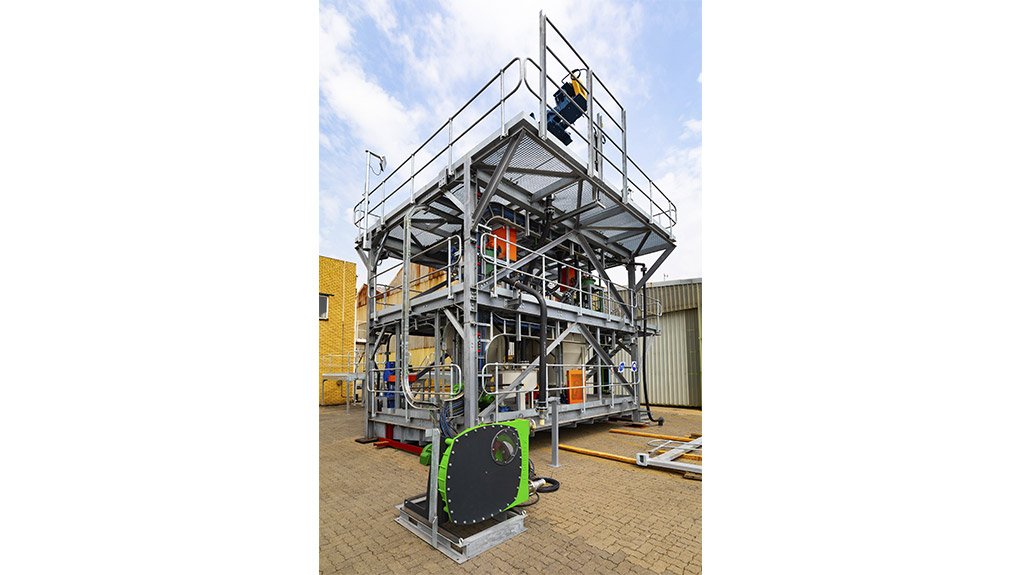
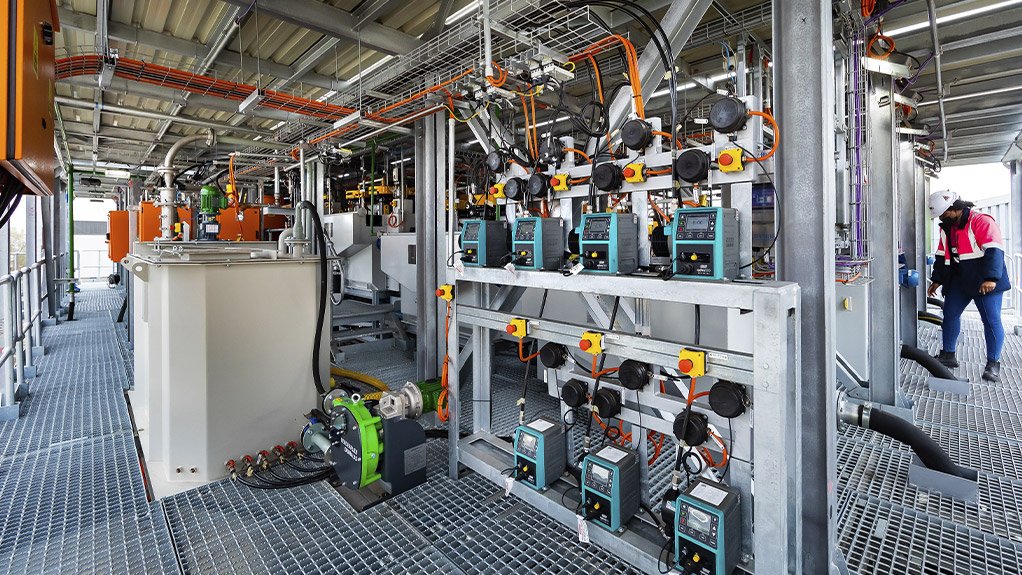
VERDERFLEX PUMPS The pumps selected for this project included the Verderflex VF65, Dura 25, Dura 35 and Dura 45
VERDERFLEX PUMPS The pumps selected for this project included the Verderflex VF65, Dura 25, Dura 35 and Dura 45
Industrial equipment supplier Verder Pumps South Africa, a “market leader in advanced industrial pumping solutions”, last month announced that it had been selected as one of the preferred pumps suppliers for platinum producer Anglo American Platinum’s (Amplats’) new modular fines flotation pilot plant and had supplied 16 pumps for various applications within the mobilised plant.
In August 2020, the modular process plant supplier ProProcess was awarded an engineering, procurement and construction contract for Amplats’ new modular fines pilot. As a preferred vendor for diversified major Anglo American, Verder supplied peristaltic pumps to ProProcess for the project.
This test facility for platinum concentrate flowsheet optimisation had to be designed with maximum road transportability in mind, as it is earmarked to be moved around various concentrator sites owned by Anglo.
To this end, the entire plant was fitted onto 16 road transportable International Organisation for Standardisation (ISO) frame skids conforming to 40 ft marine container dimensions.
The plant consists of more than 40 flotation cells (including a high-intensity flotation cell), a mill, about 30 tanks (some agitated), about 50 pumps (including centrifugal slurry, peristaltic and vertical spindle), blowers, compressors, and other items.
Verderflex peristaltic pumps are manufactured in the European Union at ISO 9001, ISO 14001 and ISO 18001 accredited facilities. The Verderflex positive displacement pumps are used with a large variety of fluids, which are totally contained within a flexible hose or tube fitted inside the pump casing.
The hose or tube is the pump’s only consumable part. This makes the Verderflex peristaltic hose and tube pumps the ideal solution for “difficult to pump” liquids or demanding applications. These range from smaller vending machine original-equipment manufacturer pumps modules and precision metering tube pumps to the world’s largest high-pressure hose pumps pumping dense, solids-laden, mining thickener slurries and highly abrasive, viscous or corrosive liquids.
The pumps selected for this project included the Verderflex VF65, Dura 25, Dura 35 and Dura 45.
“Pilot plants have much less stringent equipment requirements than production plants and this needs to be taken into consideration to avoid over designing the plant, thus unnecessarily escalating the capital outlay. This required a lot of out-of-the-box thinking and many new ideas and concepts were explored to ensure a built-for-purpose plant,” said ProProcess project manager Stefan van Dyk.
Moreover, according ProProcess mechanical lead Kean Southern, the firm applied its specialised modular approach to the design of this plant for simplified site installation and ease of transport.
“All equipment is premounted, piped up, and tested at our workshop before shipment to site. “Once testing is complete, all that is required is for flexible, interconnecting piping between the frames to be disconnected – which is made easy with the use of flanges and claw couplings,” said Southern.
“Given [that] the numerous pipe sections run between frames, each connection of the flexible hose needed to be tagged to ensure the correct hoses were reconnected during assembly. Since the plant arrives on site already partially assembled, site installation is a breeze.”
To avoid the construction of complex concrete bunded areas at each test site location, ProProcess also designed structural bunds in ISO frame format. These bunds, complete with removable sump pumps, are transported separately, and essentially form the foundation for the plant structure when placed on a flat surface.
Since they are supported at the four corners of the ISO frames, the bund foundation can tolerate a certain amount of unevenness, which is compensated for by shimming the corners to ensure a level final base for the ISO frames, making up the balance of the plant.
The Verder team not only provided fit-for-purpose pumping solutions for the plant but assisted in evaluating the pump head resulting from the impulse losses generated by peristaltic pumps. Overall, the impression of ProProcess and Verder working together on the project was a positive one.
“Over the last two decades of operating in South Africa, the Verder brand and its solutions have earned a reputation for excellence; for providing advanced, cost-effective, efficient and long-lasting pumping solutions,” Verder Pumps South Africa MD Darryl Macdougall commented.
“We were very excited to be chosen as a preferred pumps supplier for this project as the use case application is a testament to the capability of our solutions – even in some of the toughest industrial and operating environments.”
Comments
Press Office
Announcements
What's On
Subscribe to improve your user experience...
Option 1 (equivalent of R125 a month):
Receive a weekly copy of Creamer Media's Engineering News & Mining Weekly magazine
(print copy for those in South Africa and e-magazine for those outside of South Africa)
Receive daily email newsletters
Access to full search results
Access archive of magazine back copies
Access to Projects in Progress
Access to ONE Research Report of your choice in PDF format
Option 2 (equivalent of R375 a month):
All benefits from Option 1
PLUS
Access to Creamer Media's Research Channel Africa for ALL Research Reports, in PDF format, on various industrial and mining sectors
including Electricity; Water; Energy Transition; Hydrogen; Roads, Rail and Ports; Coal; Gold; Platinum; Battery Metals; etc.
Already a subscriber?
Forgotten your password?
Receive weekly copy of Creamer Media's Engineering News & Mining Weekly magazine (print copy for those in South Africa and e-magazine for those outside of South Africa)
➕
Recieve daily email newsletters
➕
Access to full search results
➕
Access archive of magazine back copies
➕
Access to Projects in Progress
➕
Access to ONE Research Report of your choice in PDF format
RESEARCH CHANNEL AFRICA
R4500 (equivalent of R375 a month)
SUBSCRIBEAll benefits from Option 1
➕
Access to Creamer Media's Research Channel Africa for ALL Research Reports on various industrial and mining sectors, in PDF format, including on:
Electricity
➕
Water
➕
Energy Transition
➕
Hydrogen
➕
Roads, Rail and Ports
➕
Coal
➕
Gold
➕
Platinum
➕
Battery Metals
➕
etc.
Receive all benefits from Option 1 or Option 2 delivered to numerous people at your company
➕
Multiple User names and Passwords for simultaneous log-ins
➕
Intranet integration access to all in your organisation