Rapid drying oven offers faster minerals processing
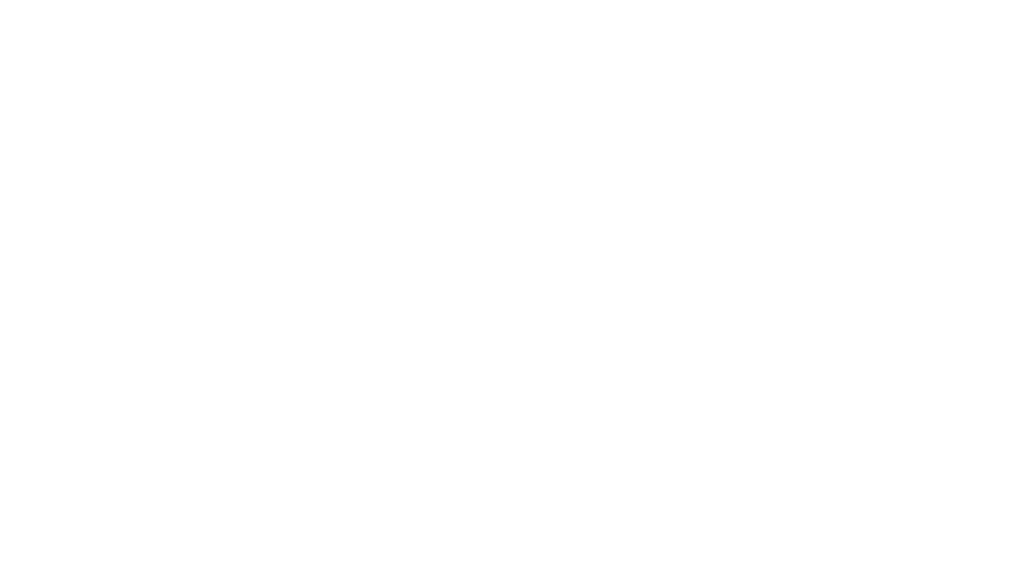
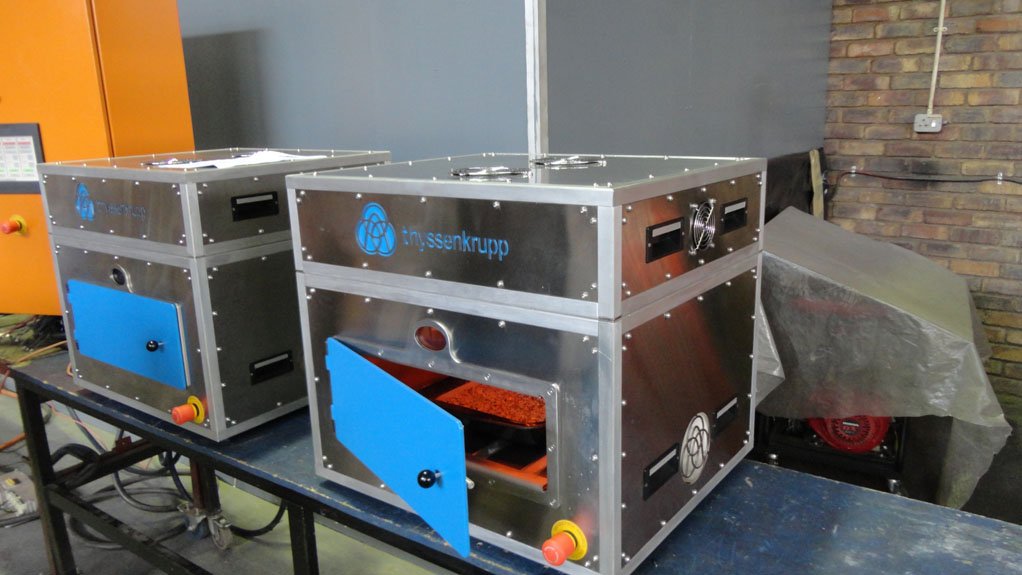
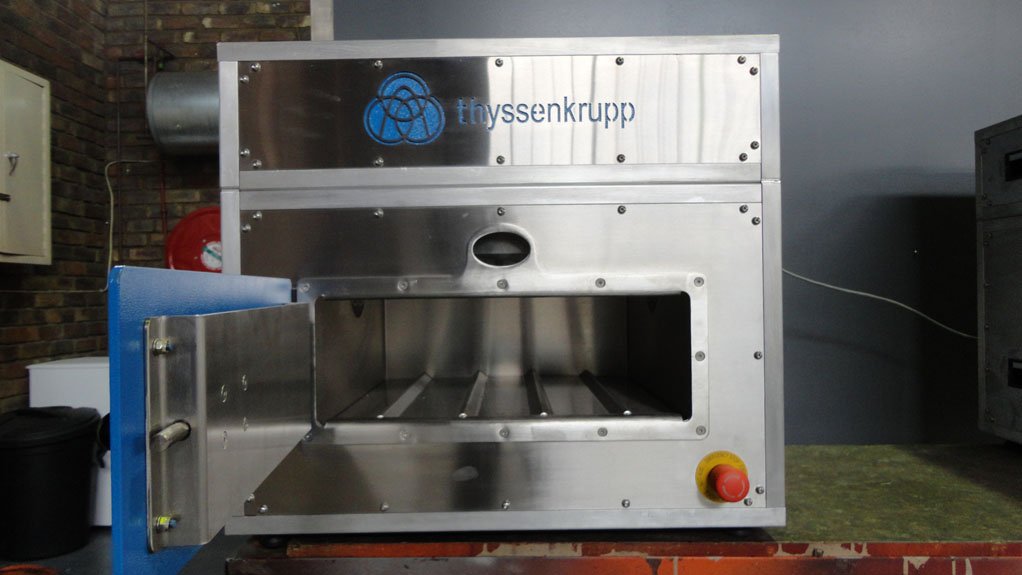
HEAT RETENTION The oven does not lose heat, even with the door open
TOP PERFORMER thyssenkrupp says its Infra-Red drying ovens have set the benchmark of oven speed and efficiency
Industrial solutions company thyssenkrupp’s Infra-Red (IR) rapid drying oven has significantly improved turnaround times for minerals processing operations specialist Minopex, owing to the oven’s fast-drying capability.
Since installation in March 2016, Minopex has reported great satisfaction with the IR oven. “We are now able to provide our customers with results on the same day, as opposed to the following day. We worked closely with thyssenkrupp over the first few months to iron out any teething problems. thyssenkrupp assists us instantly,” says Minopex minerals operations executive Elna du Toit.
The IR rapid drying oven is developed in-house by thyssenkrupp Industrial Solutions South Africa, in Johannesburg. The IR oven is capable of drying a range of mineral samples in significantly less time, compared with convection drying methods. This has set the speed and efficiency benchmark in mineral sample drying.
Minopex is a specialist in the outsourced operation and maintenance of metals and minerals processing facilities. This includes the coal, platinum, gold, iron-ore and diamond industries. Minopex is responsible for analysing samples from the different stages of a processing plant for plant process control and final product quality purposes.
Mineral samples entering the Minopex laboratory from customers in the gold mining sector are wet, containing between 2% and 60% water. This is owing to the penetrant testing process, also known as liquid penetrant testing, which is a low-cost inspection method used to locate surface-breaking defects in materials. A liquid penetrant is drawn into the surface-breaking crack by capillary action. Excess surface penetrant is then removed, after which a developer, usually in powder form, is applied to the surface, drawing out the penetrant in the crack to produce surface indications.
Du Toit explains that a convection oven is used to dry the samples because tests conducted during the penetrant testing require the material to be completely dry to prevent it from conglomerating. However, the convection drying process, she says, was proving to be extremely slow and led to poor sample turnaround, “which was impacting negatively on our customer service”.
Du Toitadds that Minopex needed assistance and, as the company had previously engaged with thyssenkrupp’s service centre and materials handling division, Minopex senior management decided to approach thyssenkrupp Industrial Solutions’ Polab division for a possible solution. The company’s Polab division is a versatile and reliable shuttle laboratory automation system that conducts sample handling by using a mobile robot, or manually, if preferred.
thyssenkrupp Industrial Solutions Polab manager Marius Combrinck says conventional drying solutions can take up to two hours before the entire sample has reached the desired drying temperature and up to 12 hours for drying process samples. Delays in reporting analytical results to process owners is, therefore, caused by extended drying times, which results in problems when owners need to perform timeous process adjustments to improve the efficiency of throughput and ensure product quality, explains Combrinck.
“To reduce drying times for processing plants, thyssenkrupp makes use of shortwave IR technology. Recognising that the customer required a quick systems approach, we did not hesitate to introduce our IR technology [to Minopex].”
The IR technology is notably faster than convection drying, owing to convection drying using “electrical heating elements that radiate longwave IR, which heats the air inside the oven. The hot air then transfers the heat to the sample tray and sample. A shortcoming of this type of heating is that all hot air is lost as soon as the oven door is opened. The heating system needs time and extra energy to recover and reach the desired cooking temperature again,” explains Combrinck.
The IR technology can be described as being similar to the light beam from a hand-held torch, he says. “Light is emitted from the torch and will shine onto the object it is pointed at. No matter how much air passes through the light beam, the light intensity will not be affected. In the same way, high-energy shortwave IR will bombard the sample material it is directed at. Cold air has no influence on this heat beam and the unit can be operated with the door open,” adds Combrinck.
Wet samples weighing between 0 kg and 10 kg are placed in containers to be placed into the IR rapid drying oven. Circulating electrical fans then extract moisture from the oven through 100 mm spigots. Shortwave IR quartz lamps heat the oven to a maximum of 200 ºC. The temperature is measured using a contactless IR pyrometer and is controlled to an accuracy of about 1 ºC by solid-state semiconductor devices. The pyrometer continuously monitors the sample surface, ensuring that the sample temperature never exceeds the laboratory-set temperature.
Only objects that are placed directly underneath the heat source will be heated to the desired temperature, resulting in a sample drying circuit that responds immediately. Shortwave IR rays provide full temperature as soon as the power is turned on. Moisture evaporation is evident seconds after the IR rays make contact with the sample surfaces. Drying ovens are only switched on when drying is required and are switched off immediately afterwards.
This method of operating a drying oven saves up to 20% on energy consumption, compared with other technology, affirms Combrinck.
thyssenkrupp will exhibit at this year’s Electra Mining Botswana exhibition, which will take place from September 12 to 14, at the Gaborone fairgrounds in Botswana. Trade show organisers Specialised Exhibitions Montgomery, in partnership with Botswana-based communcations company Soapbox Communications are organising the event.
Comments
Press Office
Announcements
What's On
Subscribe to improve your user experience...
Option 1 (equivalent of R125 a month):
Receive a weekly copy of Creamer Media's Engineering News & Mining Weekly magazine
(print copy for those in South Africa and e-magazine for those outside of South Africa)
Receive daily email newsletters
Access to full search results
Access archive of magazine back copies
Access to Projects in Progress
Access to ONE Research Report of your choice in PDF format
Option 2 (equivalent of R375 a month):
All benefits from Option 1
PLUS
Access to Creamer Media's Research Channel Africa for ALL Research Reports, in PDF format, on various industrial and mining sectors
including Electricity; Water; Energy Transition; Hydrogen; Roads, Rail and Ports; Coal; Gold; Platinum; Battery Metals; etc.
Already a subscriber?
Forgotten your password?
Receive weekly copy of Creamer Media's Engineering News & Mining Weekly magazine (print copy for those in South Africa and e-magazine for those outside of South Africa)
➕
Recieve daily email newsletters
➕
Access to full search results
➕
Access archive of magazine back copies
➕
Access to Projects in Progress
➕
Access to ONE Research Report of your choice in PDF format
RESEARCH CHANNEL AFRICA
R4500 (equivalent of R375 a month)
SUBSCRIBEAll benefits from Option 1
➕
Access to Creamer Media's Research Channel Africa for ALL Research Reports on various industrial and mining sectors, in PDF format, including on:
Electricity
➕
Water
➕
Energy Transition
➕
Hydrogen
➕
Roads, Rail and Ports
➕
Coal
➕
Gold
➕
Platinum
➕
Battery Metals
➕
etc.
Receive all benefits from Option 1 or Option 2 delivered to numerous people at your company
➕
Multiple User names and Passwords for simultaneous log-ins
➕
Intranet integration access to all in your organisation