Use of recycled copper components limits costs
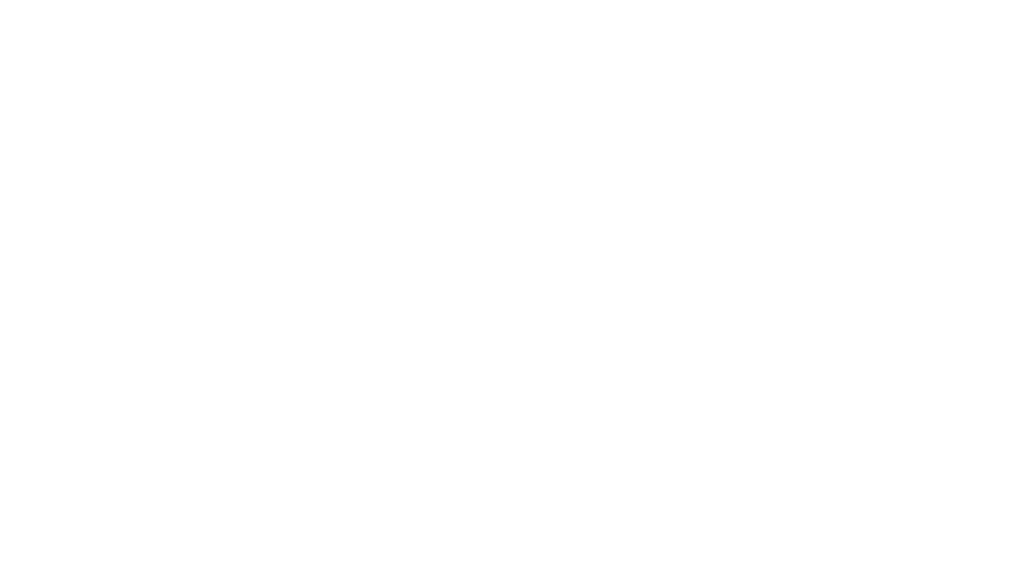
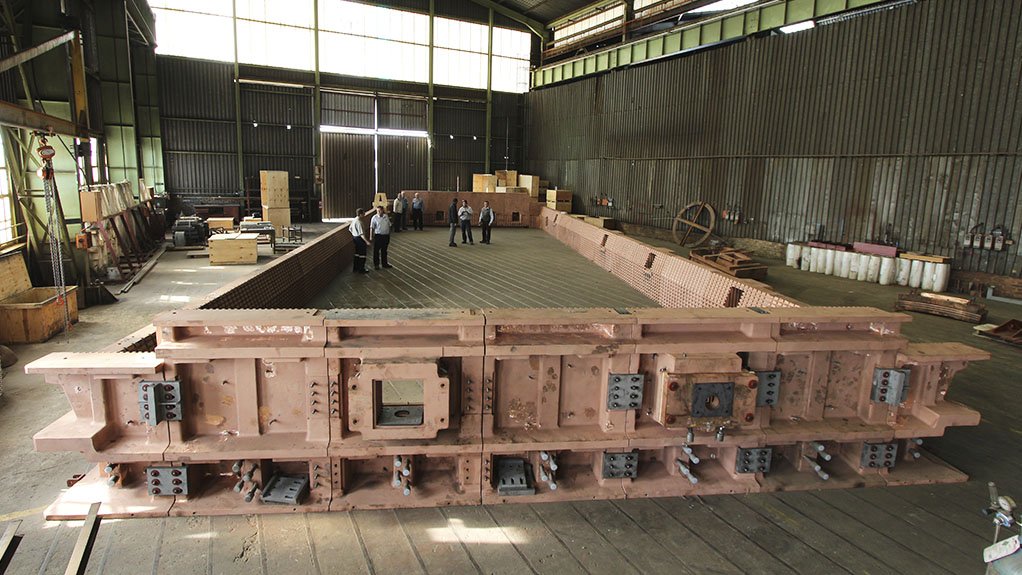
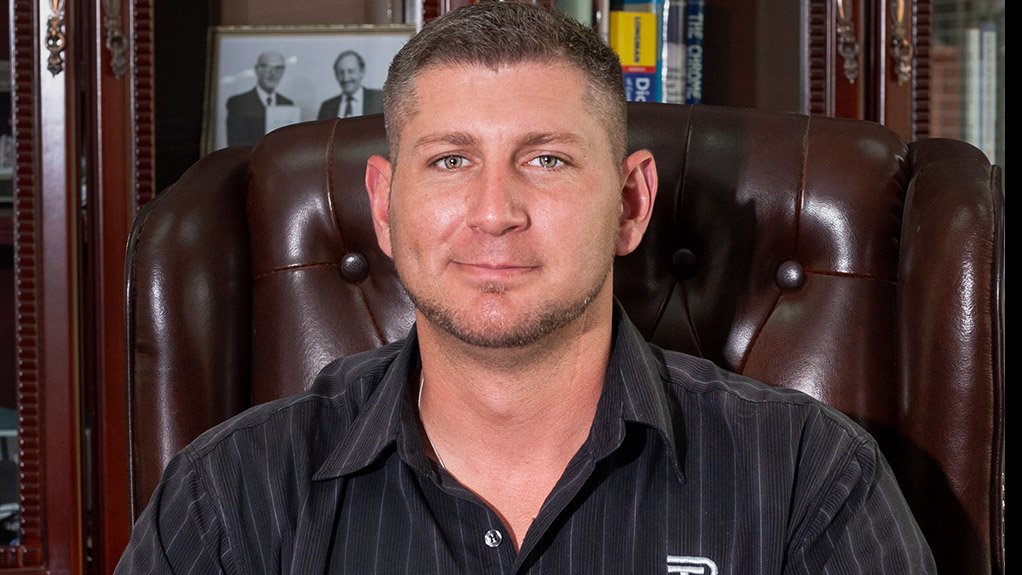
THROWING COPPER Thos Begbie has taken to recycling copper to decrease costs and increase lead times on its components
ESLI BANTJES The company has supplied 700 000 kg of copper-cooling components to the South African smelting sector since October last year
South Africa-based foundry and engineering company Thos Begbie has successfully manufactured and supplied recycled copper cast components to a platinum group metals (PGMs) smelter near Rustenburg, in the North West, over the past three months.
About 115 000 kg of raw copper and 6 500 kg of graphite were used for the project. The contract for the manufacture and supply of the components was about R50-million.
“If we look at a component for component comparison, factoring in the use of some virgin material, we successfully achieved a 90% saving on material for every component,” says Thos Begbie sales engineer Esli Bantjes.
He enthuses that, by adding the recycled copper to the virgin copper supplied by the smelter, the company has supplied 700 000 kg of copper-cooling components to the South African smelting sector since October last year.
Thos Begbie has been supplying pyrometallurgical copper components to its Rustenburg client for more than 30 years, and the client has always been very happy with the partnership, says Bantjes.
“The rebuild at the Rustenburg smelter is continuous and the startup phase, whereby the client makes sure the refractory has cured, has started; however, production is still pending.”
Bantjes adds that the company explored the option of copper recycling because of the effect of Covid-19 on raw material imports and exports, particularly in terms of severe shortages in raw materials such as copper.
“This highlighted that we needed to have a backup plan to ensure that we’d have copper available for any new rebuilds and projects.”
Why Copper?
Bantjes points out that copper is an excellent conductor of not only electricity but also heat.
“In the PGM smelter’s arc furnace, the electrical charge must be transferred through an electrode into the furnace to create an arc between the different phases.”
This electrical energy needs to be transferred from the transformers to the electrodes with the least amount of resistance. As such, the electrode columns are constructed with contact shoes – made of high-purity copper –to reduce the resistance, which, in turn, affects the amount of electrical energy input in the furnace.
The lower the electrical conductivity, the more energy is required, resulting in increased electricity consumption – often an unnecessary expense. “Fundamentally, higher utility bills equate to less profit,” Bantjes adds.
Producing recycled copper from platinum smelters is a challenge, as some of the components in the smelter’s arc furnaces had been subjected to significant erosion and corrosion, as well as monel pipes also embedded in the copper casting of the furnace.
“The monel tubing safely conveys water throughout the casting, hence it being called a cast copper cooler. For a copper cooler to perform its function, it must comply with certain criteria, of which thermal transmittance or the ability to transfer heat without affecting the energy input into the furnace, is one of the most important [factors].”
Melting the copper with the monel still embedded would lower the conductivity and, consequently, influence the thermal transmittance of the recycled material.
Thermal transmittance and electrical conductivity work in parallel and using a conductivity meter enabled Thos Begbie to measure the electrical conductivity in line with the International Association of Classification Societies standards.
“We had developed a process that enables us to successfully separate the copper and contaminants – in this case the monel – thereby providing us with ‘clean’ copper.”
This process allowed for the recovery of 99% of the scrap copper components from the different platinum smelter sites and the rebate of the copper against the cost for a new component.
Looking Forward
“We have manufactured and tested a top-secret component for one of South Africa’s platinum smelters. It was designed by one of the biggest furnace design houses in South Africa,” enthuses Bantjes.
“All the tests were to the satisfaction of the end-user. “We have been invited to tender for the manufacture and supply of the entire furnace.”
Another platinum smelter will order a furnace, as it will conduct a rebuild later this year and, as a rule, the smelter keeps an entire furnace’s components in stock.
“These two projects are worth about R100-million.”
Thos Begbie also manufactures and supplies its “running spares”
Although the company is repurposing copper from only local PGM smelters, it is promoting its being able to rebate some of the scrap copper components from its other clients to reduce material costs, Bantjes concludes.
Comments
Press Office
Announcements
What's On
Subscribe to improve your user experience...
Option 1 (equivalent of R125 a month):
Receive a weekly copy of Creamer Media's Engineering News & Mining Weekly magazine
(print copy for those in South Africa and e-magazine for those outside of South Africa)
Receive daily email newsletters
Access to full search results
Access archive of magazine back copies
Access to Projects in Progress
Access to ONE Research Report of your choice in PDF format
Option 2 (equivalent of R375 a month):
All benefits from Option 1
PLUS
Access to Creamer Media's Research Channel Africa for ALL Research Reports, in PDF format, on various industrial and mining sectors
including Electricity; Water; Energy Transition; Hydrogen; Roads, Rail and Ports; Coal; Gold; Platinum; Battery Metals; etc.
Already a subscriber?
Forgotten your password?
Receive weekly copy of Creamer Media's Engineering News & Mining Weekly magazine (print copy for those in South Africa and e-magazine for those outside of South Africa)
➕
Recieve daily email newsletters
➕
Access to full search results
➕
Access archive of magazine back copies
➕
Access to Projects in Progress
➕
Access to ONE Research Report of your choice in PDF format
RESEARCH CHANNEL AFRICA
R4500 (equivalent of R375 a month)
SUBSCRIBEAll benefits from Option 1
➕
Access to Creamer Media's Research Channel Africa for ALL Research Reports on various industrial and mining sectors, in PDF format, including on:
Electricity
➕
Water
➕
Energy Transition
➕
Hydrogen
➕
Roads, Rail and Ports
➕
Coal
➕
Gold
➕
Platinum
➕
Battery Metals
➕
etc.
Receive all benefits from Option 1 or Option 2 delivered to numerous people at your company
➕
Multiple User names and Passwords for simultaneous log-ins
➕
Intranet integration access to all in your organisation