Sandvik Rock Processing's lifecycle strategy cuts screen costs per tonne
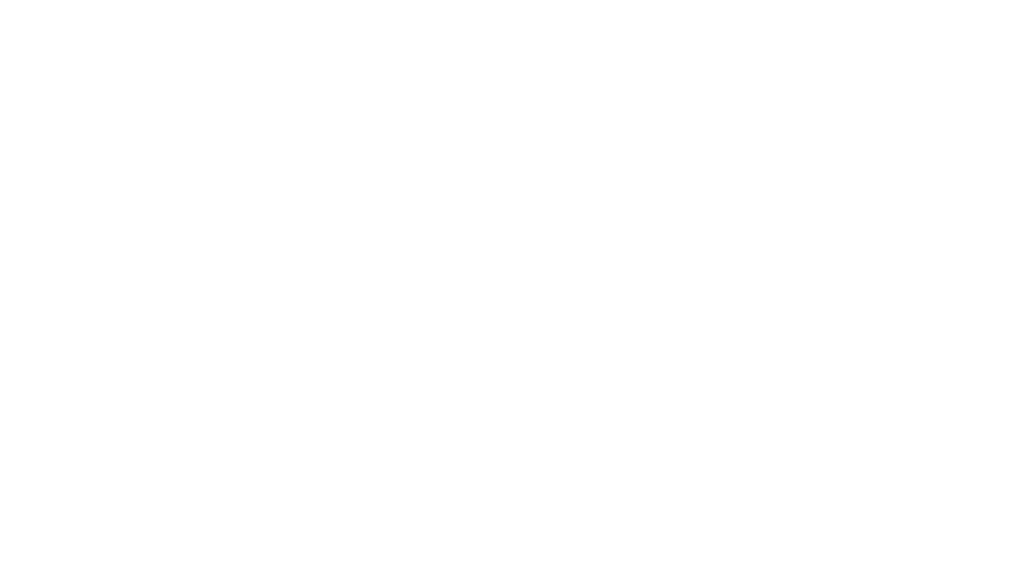
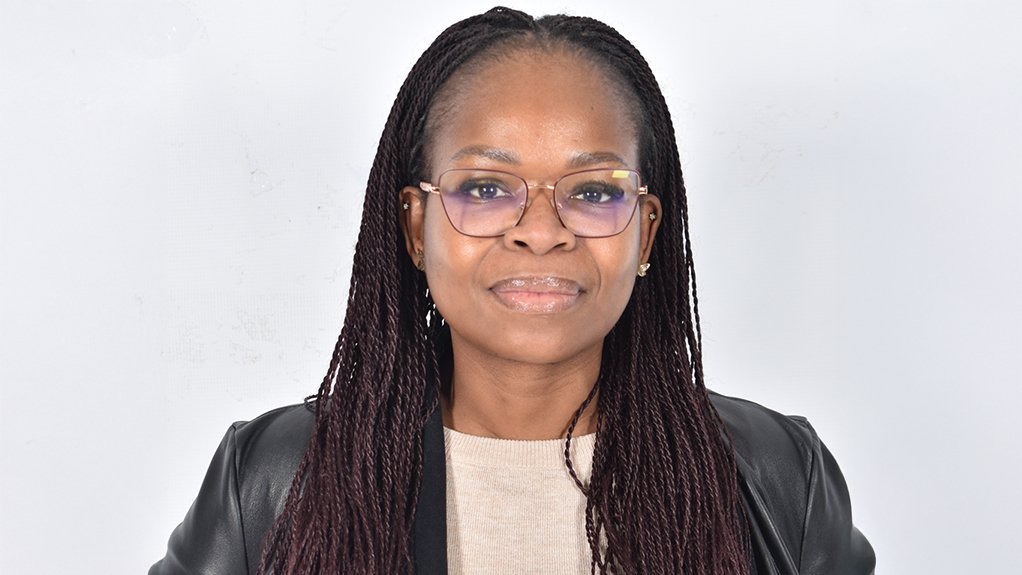
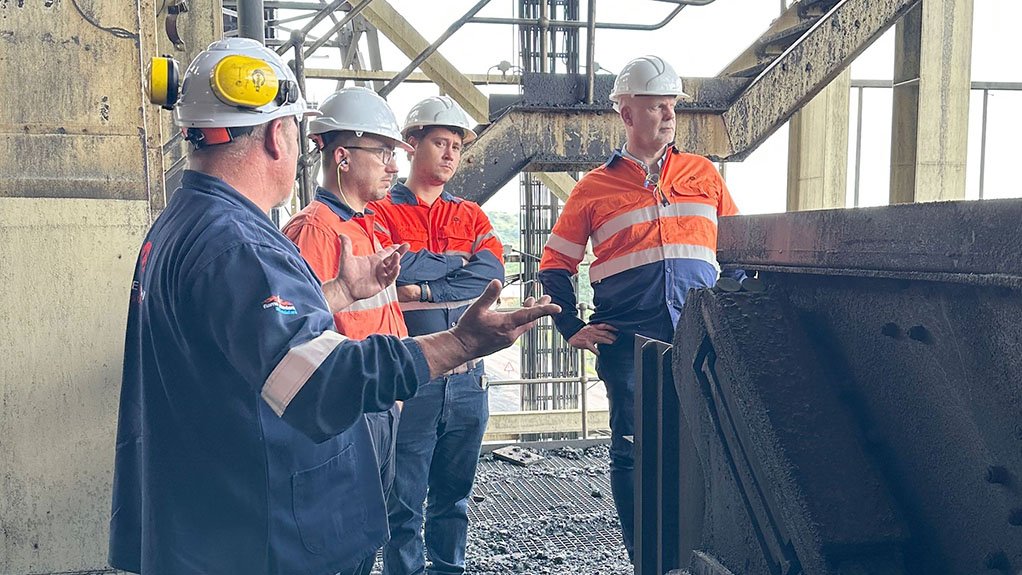
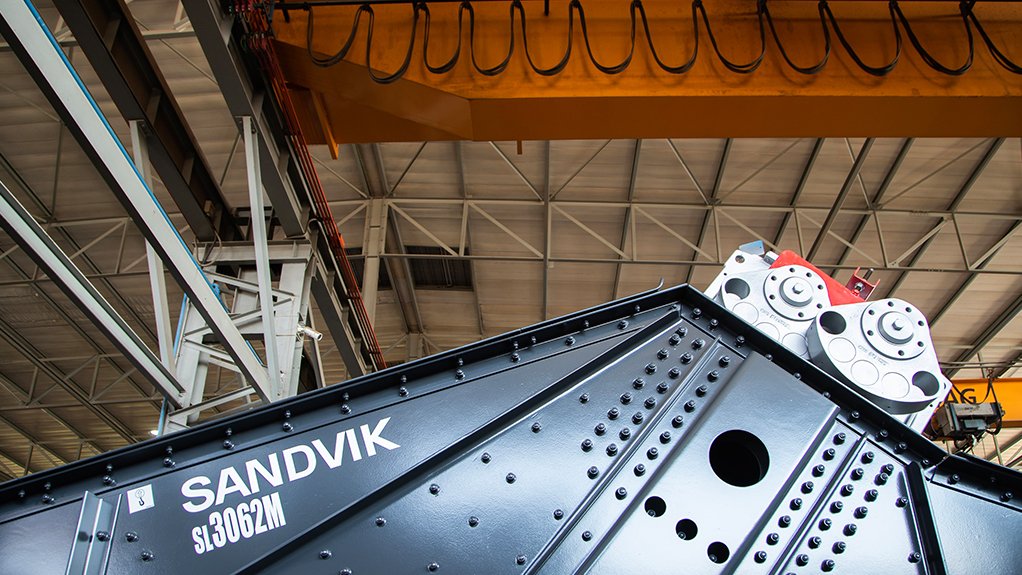
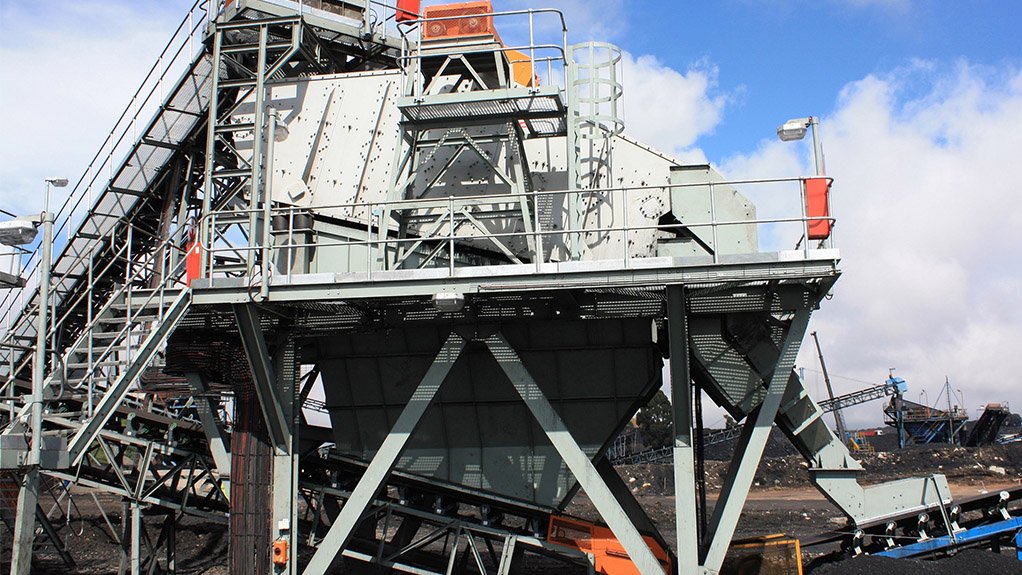
Lomave Sukati, Sandvik Rock Processing’s Business Line Manager Lifecycle Solutions
Regular inspections and proactive maintenance planning are key to reducing unplanned downtime and lowering the total cost per tonne
Sandvik Rock Processing's lifecycle management approach includes managing parts inventory to ensure availability when it is needed most
A baseline assessment conducted on site is the foundation for restoring vibrating screens to OEM standards and boosting long-term performance
This article has been supplied.
By embracing a lifecycle management approach with its customers, Sandvik Rock Processing ensures that its vibrating screens meet production targets at the lowest cost per tonne.
The most effective starting point, says Lomave Sukati, Sandvik Rock Processing’s Business Line Manager Lifecycle Solutions, is for mines to request a full assessment from their OEM partner.
“This allows for a gap analysis to identify opportunities for improvement, so the equipment can be restored to OEM standards in terms of reliability and performance,” explains Sukati. “The customer might also require that operators receive targeted on-the-job training, which helps ensure performance is maintained.”
Sandvik Rock Processing’s assessments include a visual inspection followed by dynamic testing to measure mechanical performance. Any defects or concerns are then detailed in a report to the customer for action.
“Our training empowers a customer’s team to recognise conditions that need early attention, as part of overall lifecycle management to keep equipment well maintained and productive,” she says. “The OEM can’t always be on site to conduct daily checks but operators can be trained to do this and a close working relationship with the OEM ensures there are open lines of communication to report issues.”
Regular inspections allow the remaining wear life of parts and components to be estimated and logged, enabling maintenance and part sourcing to be planned well in advance. This prevents unscheduled downtime and allows maintenance work to be done during planned plant shutdowns.
The performance of the screens is also affected by the changing nature of the ore bodies being mined, which requires constant monitoring – as changing geology could result in more abrasive material being crushed and screened.
“This may call for a different choice of wear materials in the screen panels to achieve the required output and wear life,” she says. “Screens are specified for certain conditions at the start of a project but adjustments invariably need to be made during the equipment’s lifecycle.”
Crushers and screens in the same circuit also impact one another, so mines need to work with OEM specialists who understand this relationship when conducting assessments and making adjustments over time.
“Effective lifecycle management is aimed at achieving the lowest cost per tonne over the life of the screen,” says Sukati. “By focusing on where most screen costs are incurred, mines can quickly identify areas to reduce costs as part of broader efficiency and productivity efforts.”
She emphasises that this is the most direct route to achieving low costs per tonne, especially when done in close collaboration with the OEM. She also highlights the value of formal agreements between mines and OEMs regarding responsibilities for keeping screens functioning optimally.
“These agreements provide clear roles for each party avoiding grey areas that could lead to oversights in monitoring, service delivery or parts availability,” she says. “For mining customers, these agreements are powerful tools to derisk their business by enhancing both equipment performance and reliability.”
This gives mines the confidence that they will meet production targets while gaining better control over operational costs through detailed planning and monitoring. Through its service level agreements, for instance, Sandvik Rock Processing places a team of experts on site who is responsible and accountable for the screens and must report regularly on their condition and performance.
“We can also manage inventory to ensure that necessary wear parts and components are available when required to ensure optimal uptime,” she concludes.
Comments
Announcements
What's On
Subscribe to improve your user experience...
Option 1 (equivalent of R125 a month):
Receive a weekly copy of Creamer Media's Engineering News & Mining Weekly magazine
(print copy for those in South Africa and e-magazine for those outside of South Africa)
Receive daily email newsletters
Access to full search results
Access archive of magazine back copies
Access to Projects in Progress
Access to ONE Research Report of your choice in PDF format
Option 2 (equivalent of R375 a month):
All benefits from Option 1
PLUS
Access to Creamer Media's Research Channel Africa for ALL Research Reports, in PDF format, on various industrial and mining sectors
including Electricity; Water; Energy Transition; Hydrogen; Roads, Rail and Ports; Coal; Gold; Platinum; Battery Metals; etc.
Already a subscriber?
Forgotten your password?
Receive weekly copy of Creamer Media's Engineering News & Mining Weekly magazine (print copy for those in South Africa and e-magazine for those outside of South Africa)
➕
Recieve daily email newsletters
➕
Access to full search results
➕
Access archive of magazine back copies
➕
Access to Projects in Progress
➕
Access to ONE Research Report of your choice in PDF format
RESEARCH CHANNEL AFRICA
R4500 (equivalent of R375 a month)
SUBSCRIBEAll benefits from Option 1
➕
Access to Creamer Media's Research Channel Africa for ALL Research Reports on various industrial and mining sectors, in PDF format, including on:
Electricity
➕
Water
➕
Energy Transition
➕
Hydrogen
➕
Roads, Rail and Ports
➕
Coal
➕
Gold
➕
Platinum
➕
Battery Metals
➕
etc.
Receive all benefits from Option 1 or Option 2 delivered to numerous people at your company
➕
Multiple User names and Passwords for simultaneous log-ins
➕
Intranet integration access to all in your organisation