Smelterless low-energy platinum processing concept advances further in Australia
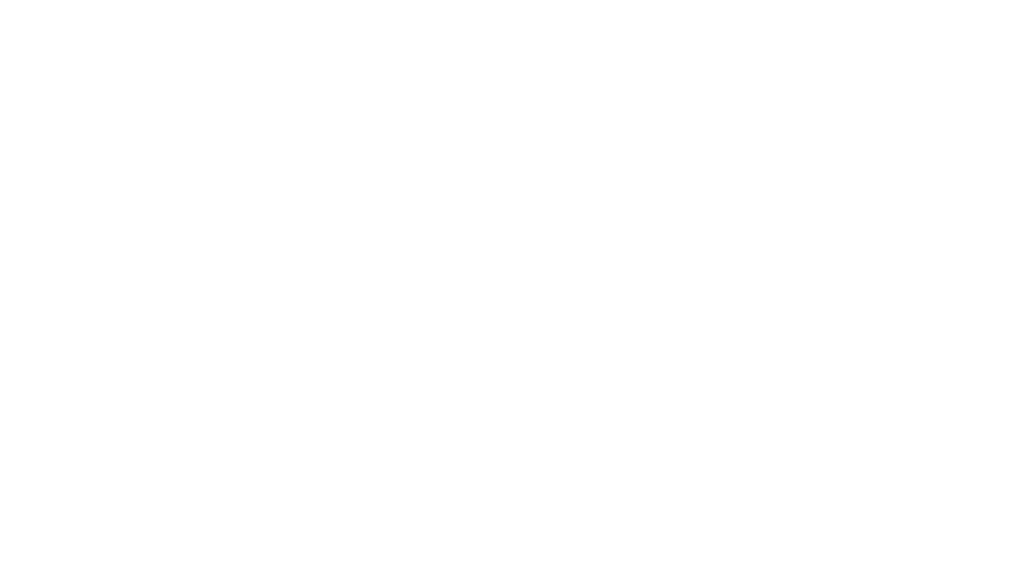
Podium Minerals CEO Sam Rodda interviewed by Mining Weekly’s Martin Creamer. Video: Darlene Creamer.
JOHANNESBURG (miningweekly.com) – A processing pathway away from high-energy pyrometallurgical smelting to low-energy hydrometallurgical platinum group metal (PGM) recoveries has been further advanced by Australian PGMs pioneer Podium Minerals.
Podium is reporting a breakthrough in platinum recoveries through a smelterless technology at its Parks Reef PGM Project in Western Australia.
The Parks Reef PGM deposit hosts platinum, palladium, rhodium, iridium, gold, copper, nickel and cobalt. A mining licence has been approved, native title granted, environmental survey completed, and scoping study advanced.
Podium is making progress on a low carbon, lower energy intensive total lifecycle of PGMs.
“For us, it's about a low energy, low carbon footprint for PGMs. It's about meeting some of the supply deficits which are forecast and looking to improve the PGMs industry overall,” Podium Minerals MD and CEO Sam Rodda told Mining Weekly in a Zoom interview. (Also watch attached Creamer Media video.)
“We're looking at an opportunity to open up a PGMs market and the PGMs commodity sector in Australia. We're really making strong advances around a technology that allows us to look at a high-grade product which is suitable for some of the major refineries in Europe,” Rodda added.
When Mining Weekly spoke to Podium in November last year, intensive hydrometallurgical testing was under way, which pointed to smelterless technology ultimately producing material suitable for refinery feed.
The ASX-listed development company has since completed 21 leach optimisation tests, which point to an unlocking of further value at laboratory scale, with continued studies being required before a mineral processing performance can be measured that represents the expected performance of a full-scale operation.
Meanwhile, processing under certain atmospheric leach conditions has achieved platinum recoveries of greater than 90%.
Platinum and iridium recoveries are under the spotlight given that these two PGMs are used in proton exchange membrane (PEM) electrolysers to produce green hydrogen, and PEM fuel cells are required to generate electricity from hydrogen for mobile and stationary offtake.
Parks Reef has an oxide zone to 45 m and a sulphide zone from 45 m to the base of the resource.
“Since November, after our really strong, heavily informed baseline, we've been able to focus on how we optimise and look to optimise value at our Parks Reef project.
“Our focus has been on how we optimise our metal recoveries through our atmospheric leach test, but also continue to consider how to minimise waste through our processing stream and reduce energy through that processing stream.
“The 21 tests focused on all three of those aspects, but particularly around what are the levers required to increase recoveries of metals such as platinum, but also around iridium and rhodium and some of the base metal products we have within our orebody,” said Rodda.
Mining Weekly: Iridium is a very scarce PGM that is needed to generate green hydrogen and catalyse hydrogen fuel cell technology. Are there indications of significant improvement when it comes to the recovery of iridium?
Rodda: We're seeing the uptake of iridium along with platinum as critical ingredients to those PEM electrolysers you speak of. It's absolutely important for us to focus on how to optimise recoveries of iridium. Through these last 21 tests, we've seen strong increases around oxide recovery of iridium, and we've seen and started to understand some of those drivers around increasing iridium recovery in our sulphide. We continue to look to extract as much metal as we can out of our orebody, iridium in particular.
Smelterless technology is very appealing in a South Africa short of electricity, but what has motivated Podium’s focus on hydrometallurgical processing in Western Australia, which has none of South Africa’s power constraints?
For us, it's twofold. Whilst we have continuity and optionality around power supply in Australia, it's important for us, particularly with a PGM metal suite, to focus on minimising our energy footprint, and the total carbon footprint of the Parks Reef project. What we’re aiming to have is one of the lowest energy PGMs in the market. That is one step.
The second step and the benefit of us looking at smelterless technology is also the opportunity to significantly add value to our Parks Reef project by removing the need for large logistical costs associated with remote operations in Australia, and looking to produce a high-grade, lower volume final product to negate the need for significant trucking, train and rail and or shipping of our final product to PGM refineries.
Who holds the intellectual property of Podium’s atmospheric leaching technology?
We're working with our preferred partner here in Australia but Podium Minerals holds the intellectual property over our atmospheric leaching and that is the basis of our project and framework. But we're also continuing to look at advances and to operationalise that technology moving forward.
In what way does it differ from the hydrometallurgical Kell technology, which is on the way to being implemented at the expanding Sedibelo PGMs mine in South Africa’s North West province?
We've had the opportunity to spend time with Kell’s Keith Liddell and his team and some of those are actually located here in Western Australia. Pleasingly, we share very similar outlooks around the potential for PGMs globally. Whilst I can't speak directly around what Keith and the team have got in place around Kell, I can talk around what we see as our differences compared to the existing market.
The attraction around smelterless technology and atmospheric leaching for us is we have the ability and we're looking to understand how we can leach either a direct ore, or a low-grade concentrate, to maximise recovery in our total product stream.
We're also looking at atmospheric leaching as a simpler operational leaching process than what could be considered in a pressurised leaching technology. Particularly in today's age, and in Australia-based processing where we have a skilled and technical shortage, it's important to consider operational aspects as well as cost and maximising metal recovery. They really are the key factors around why atmospheric leaching is our first preference for downstream processing of PGMs.
SMELTERLESS TECHNOLOGY IN SOUTH AFRICA
Kell is commissioning new smelterless technology at Sedibelo’s Pilanesberg PGMs mine, amid more than a decade of research, development and plant piloting.
Sedibelo announced its involvement with Kell at the premises of South Africa’s State-owned Industrial Development Corporation (IDC) more than ten years ago.
Sedibelo shares an interest in Kell with the IDC and founder Liddell, who conceived the smelterless concept many years ago, when working at South Africa’s State-owned mineral research organisation Mintek, on Malibongwe Drive, Randburg, in Gauteng.
Kell’s carbon dioxide emissions from concentrate to final refined metals are only 19% of the carbon dioxide emissions caused by the conventional high-energy pyrometallurgical smelting and refining route.
By allowing an operation to go from mining to finished refined metal in a week, Kell unlocks significant capital. Not only is the operating cost far cheaper, but so is the capital cost.
Comments
Press Office
Announcements
What's On
Subscribe to improve your user experience...
Option 1 (equivalent of R125 a month):
Receive a weekly copy of Creamer Media's Engineering News & Mining Weekly magazine
(print copy for those in South Africa and e-magazine for those outside of South Africa)
Receive daily email newsletters
Access to full search results
Access archive of magazine back copies
Access to Projects in Progress
Access to ONE Research Report of your choice in PDF format
Option 2 (equivalent of R375 a month):
All benefits from Option 1
PLUS
Access to Creamer Media's Research Channel Africa for ALL Research Reports, in PDF format, on various industrial and mining sectors
including Electricity; Water; Energy Transition; Hydrogen; Roads, Rail and Ports; Coal; Gold; Platinum; Battery Metals; etc.
Already a subscriber?
Forgotten your password?
Receive weekly copy of Creamer Media's Engineering News & Mining Weekly magazine (print copy for those in South Africa and e-magazine for those outside of South Africa)
➕
Recieve daily email newsletters
➕
Access to full search results
➕
Access archive of magazine back copies
➕
Access to Projects in Progress
➕
Access to ONE Research Report of your choice in PDF format
RESEARCH CHANNEL AFRICA
R4500 (equivalent of R375 a month)
SUBSCRIBEAll benefits from Option 1
➕
Access to Creamer Media's Research Channel Africa for ALL Research Reports on various industrial and mining sectors, in PDF format, including on:
Electricity
➕
Water
➕
Energy Transition
➕
Hydrogen
➕
Roads, Rail and Ports
➕
Coal
➕
Gold
➕
Platinum
➕
Battery Metals
➕
etc.
Receive all benefits from Option 1 or Option 2 delivered to numerous people at your company
➕
Multiple User names and Passwords for simultaneous log-ins
➕
Intranet integration access to all in your organisation